- 文档大小:6.85 MB
- 文档格式:pdf
- 约 17页
- 2021-09-09 发布
- 举报
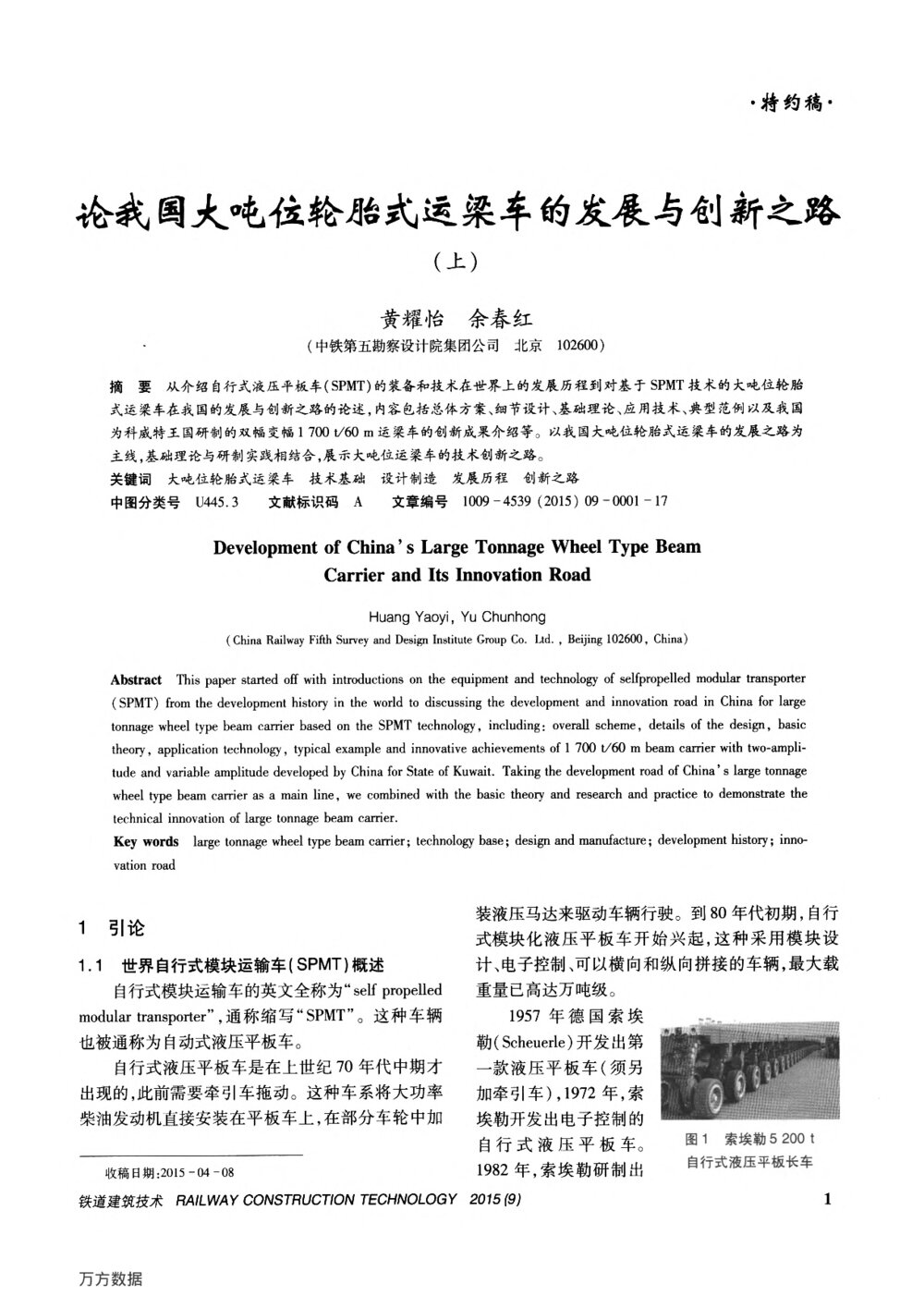
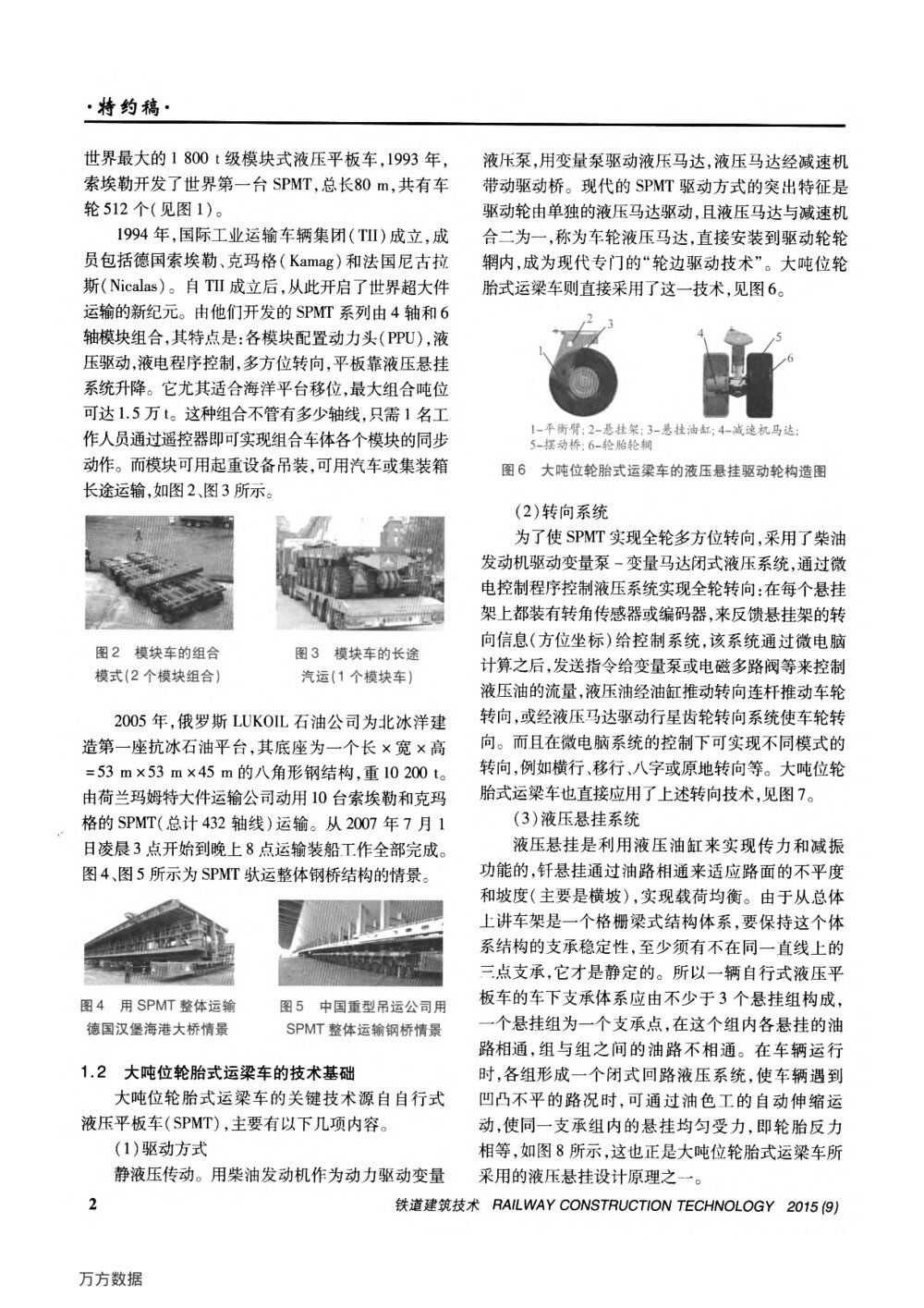
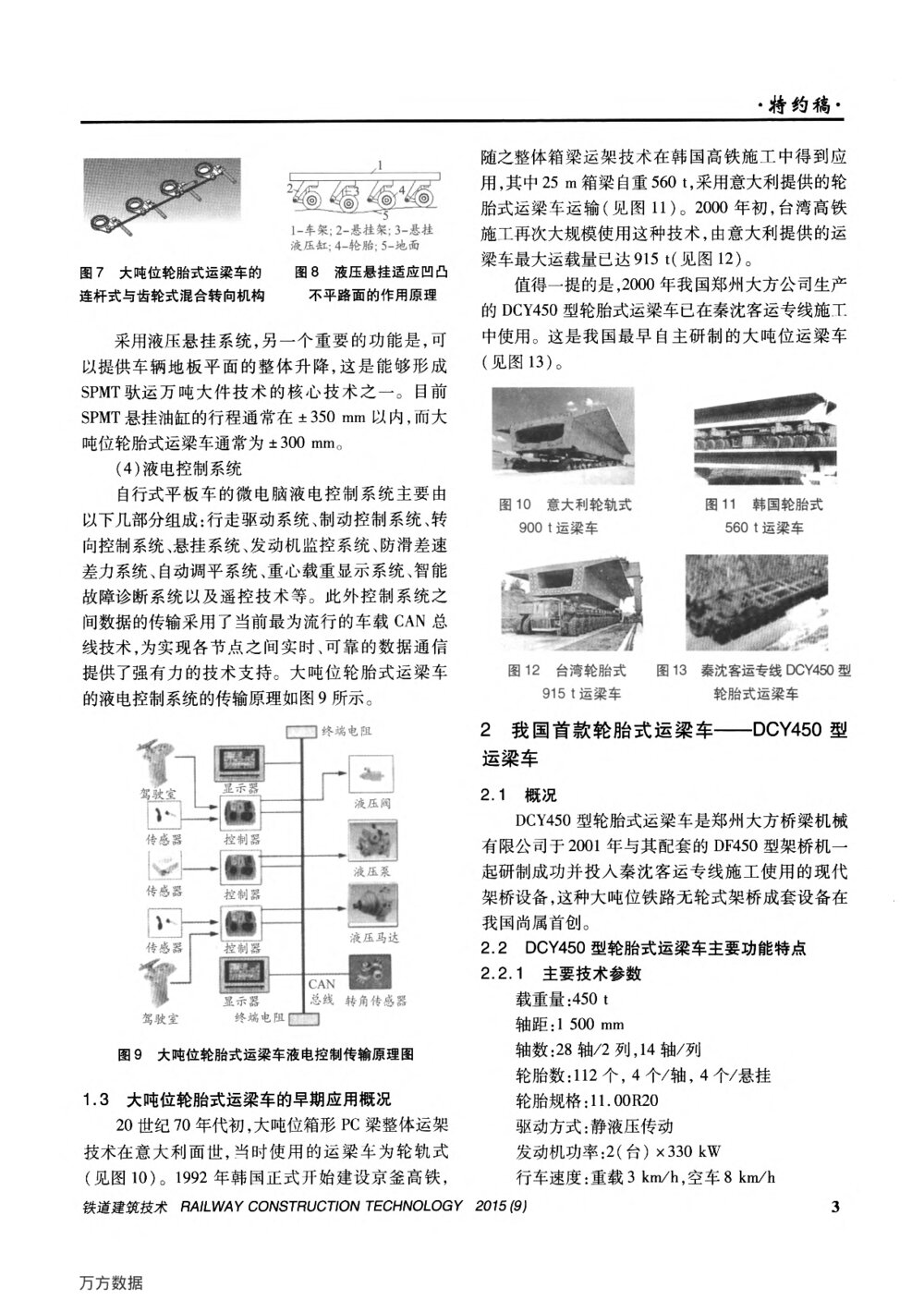
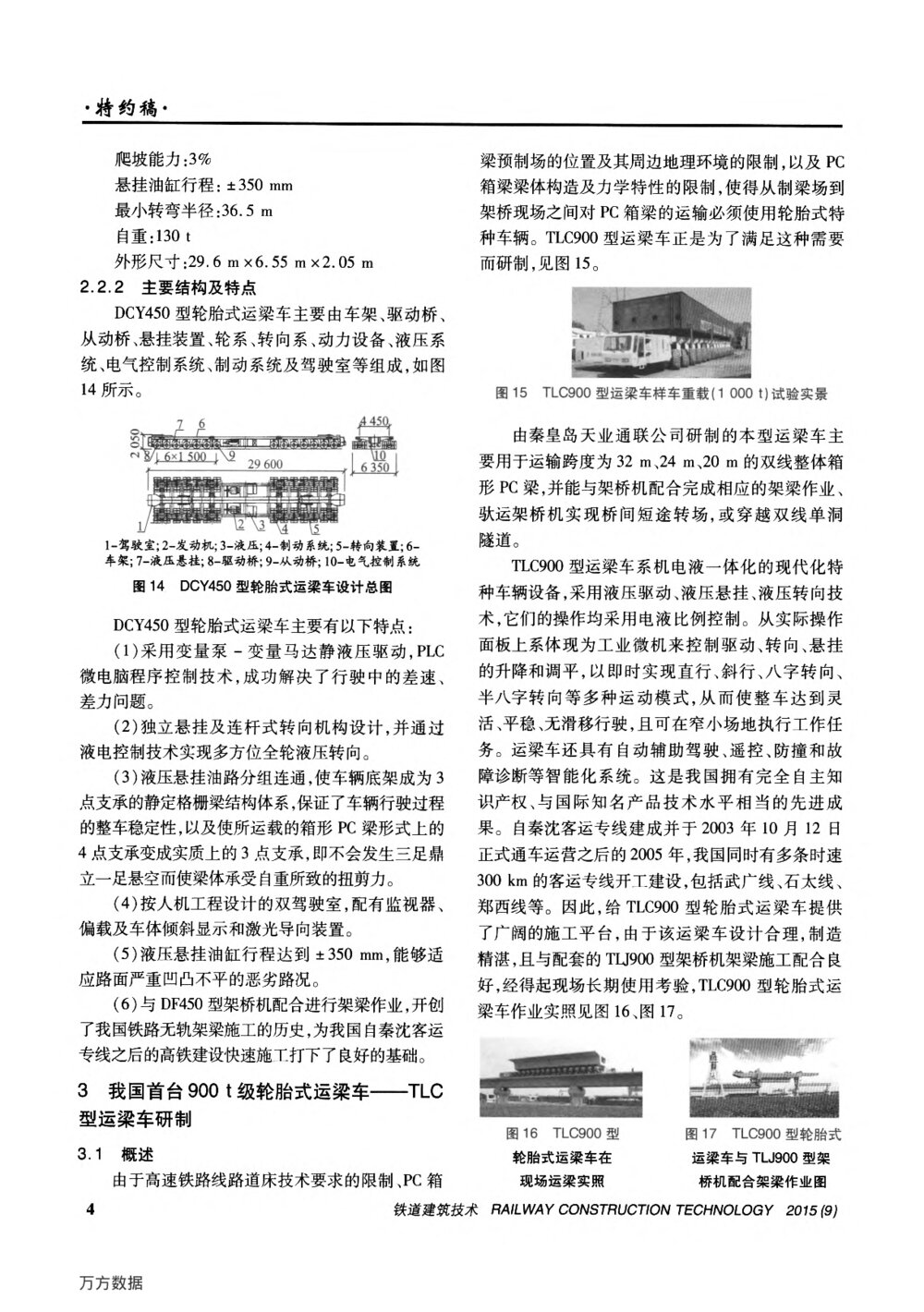
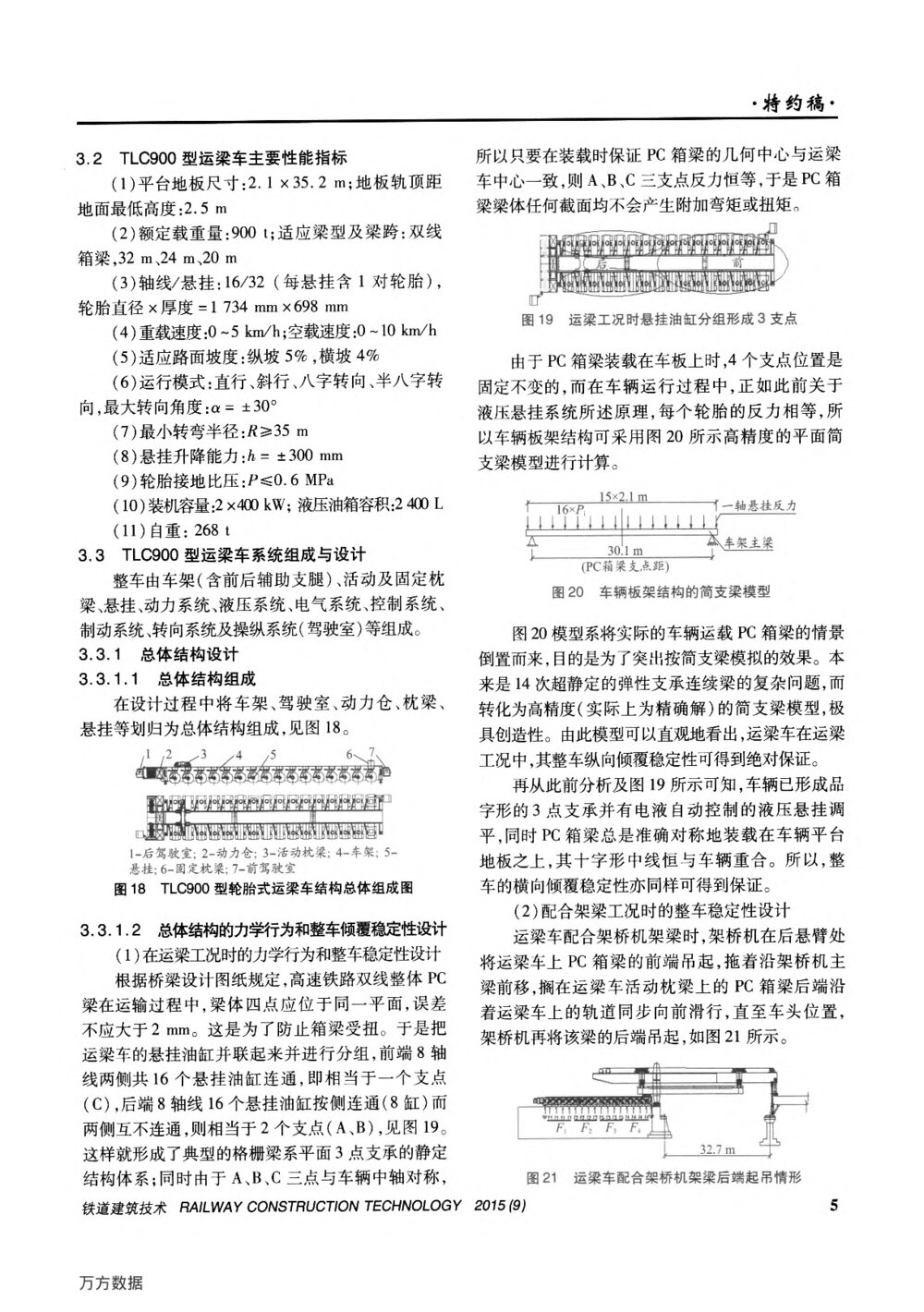
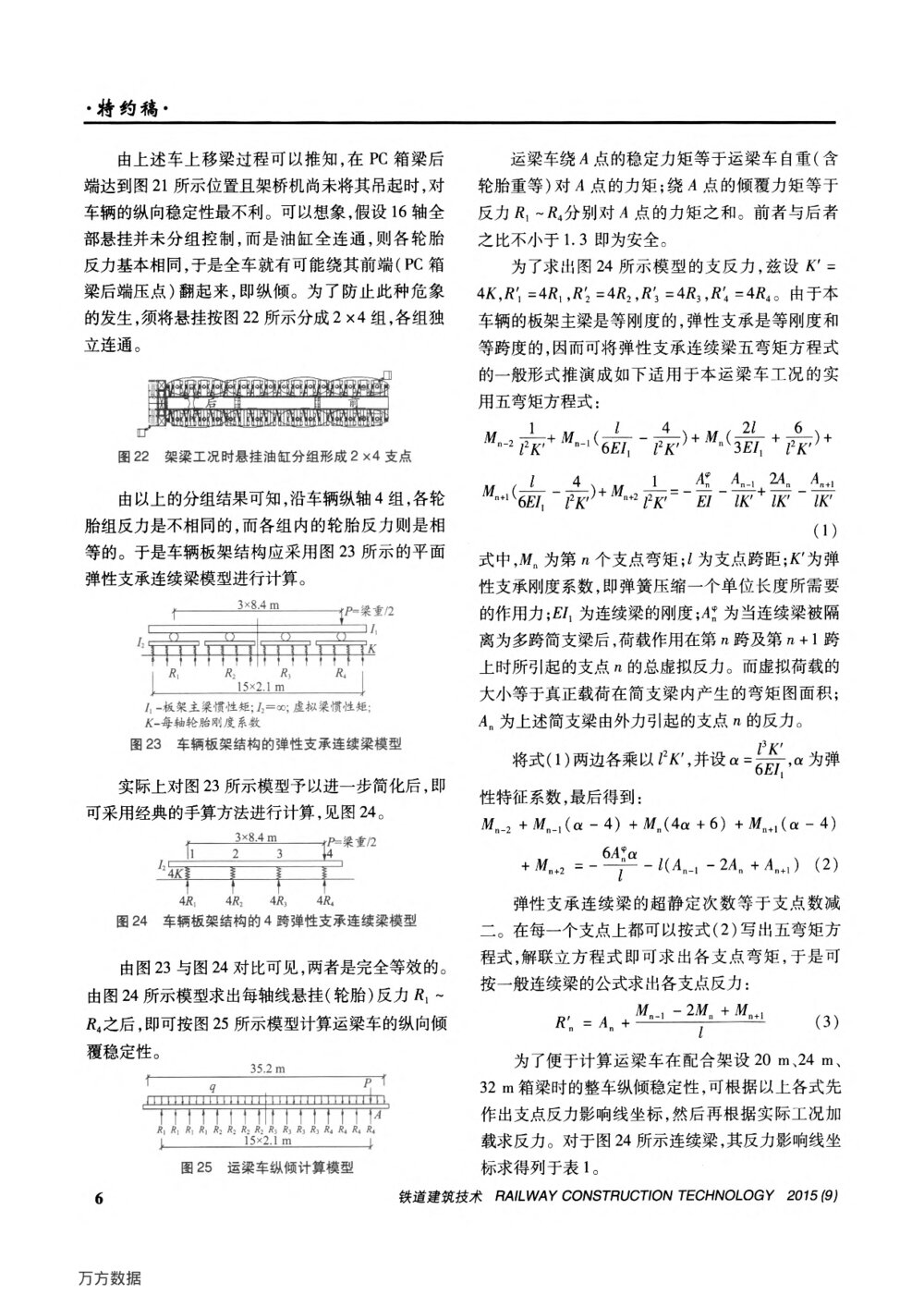
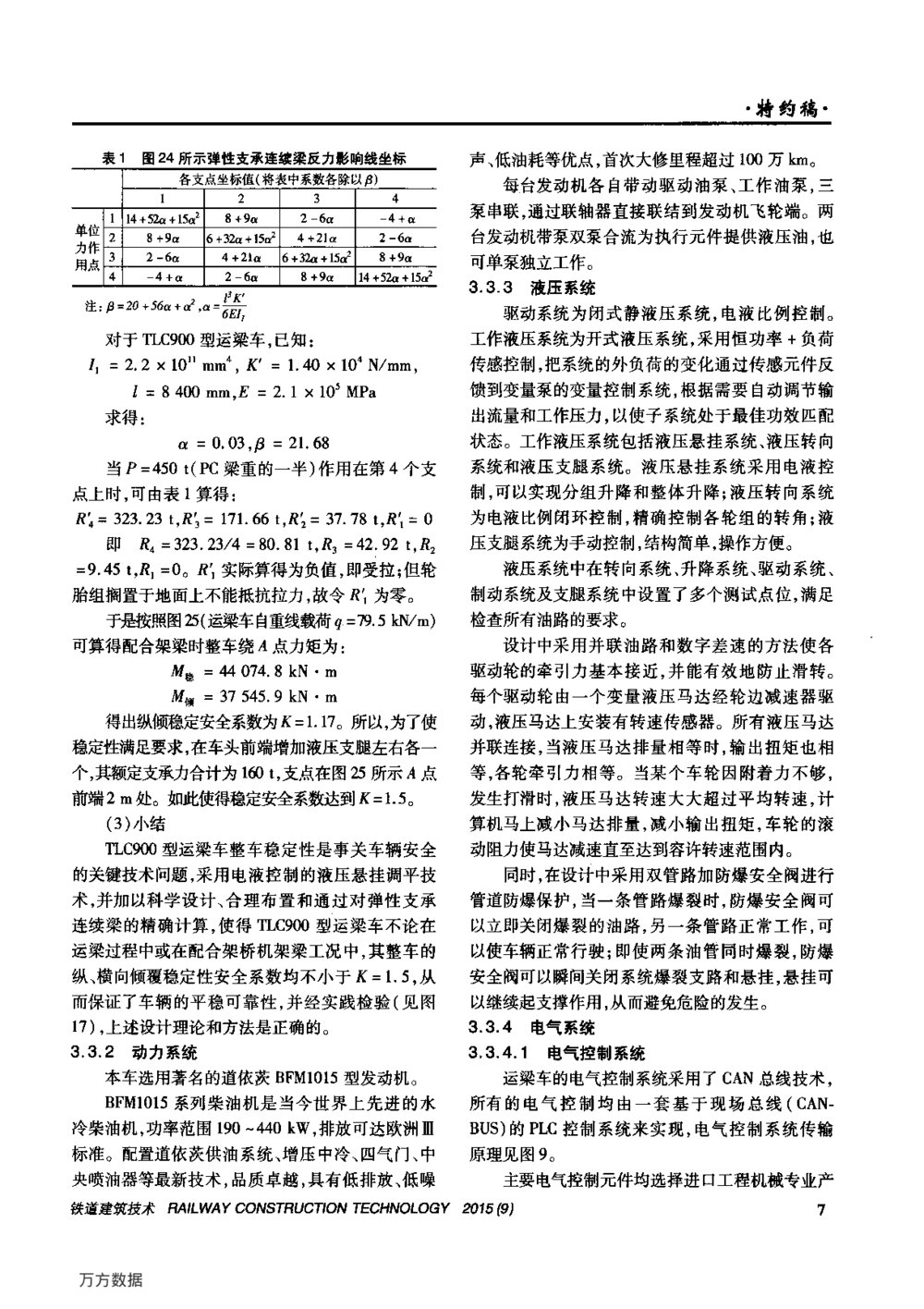
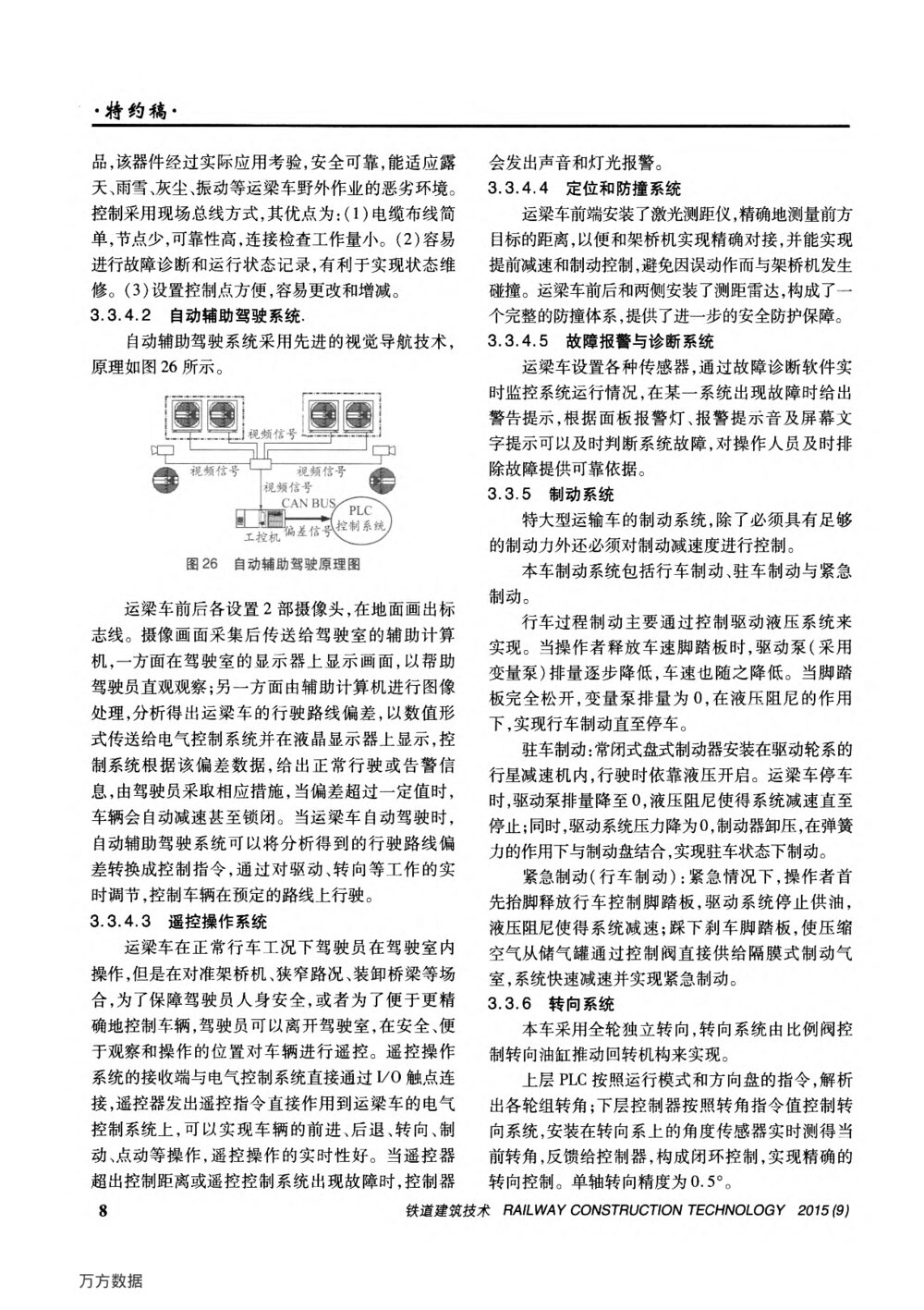
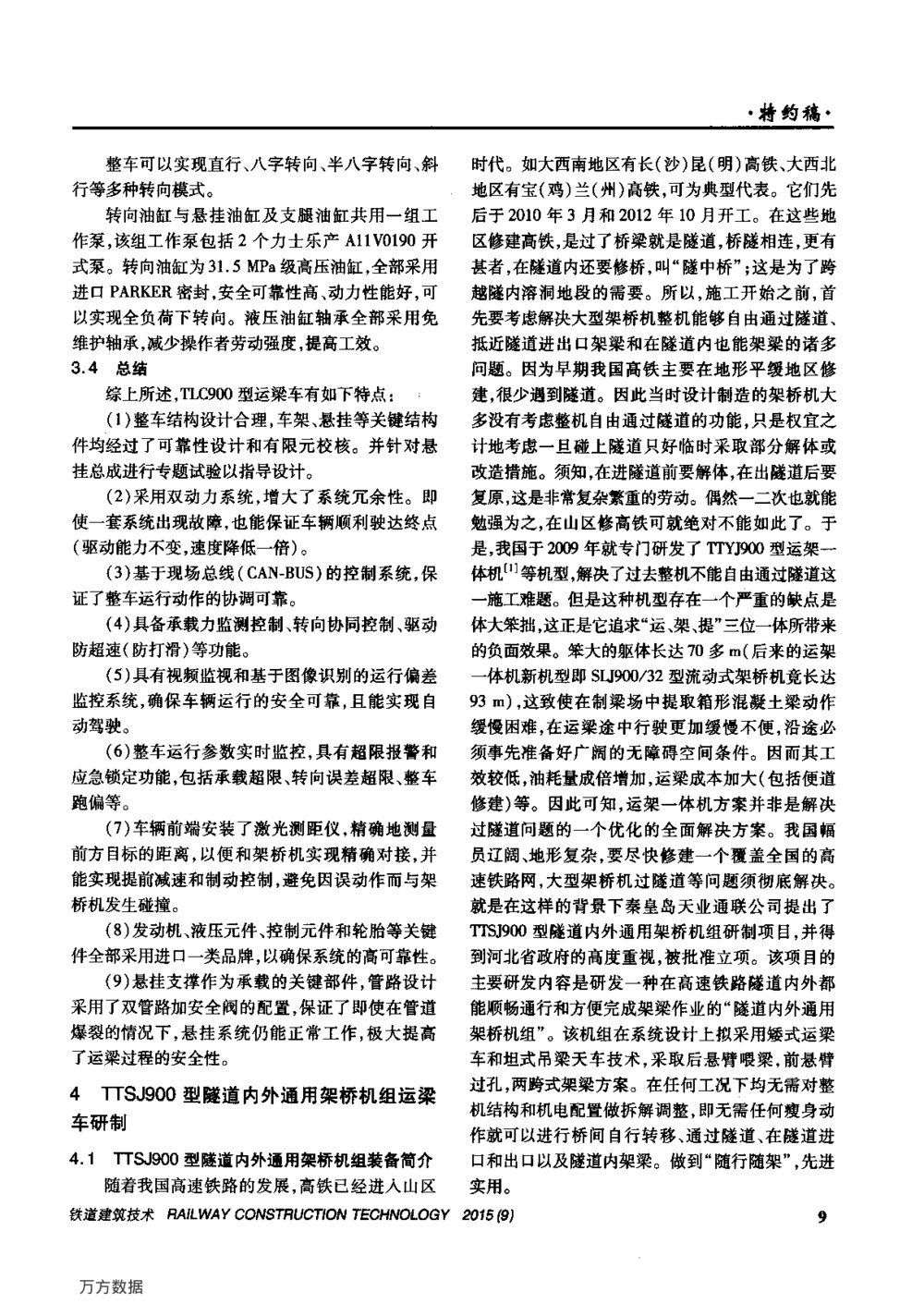
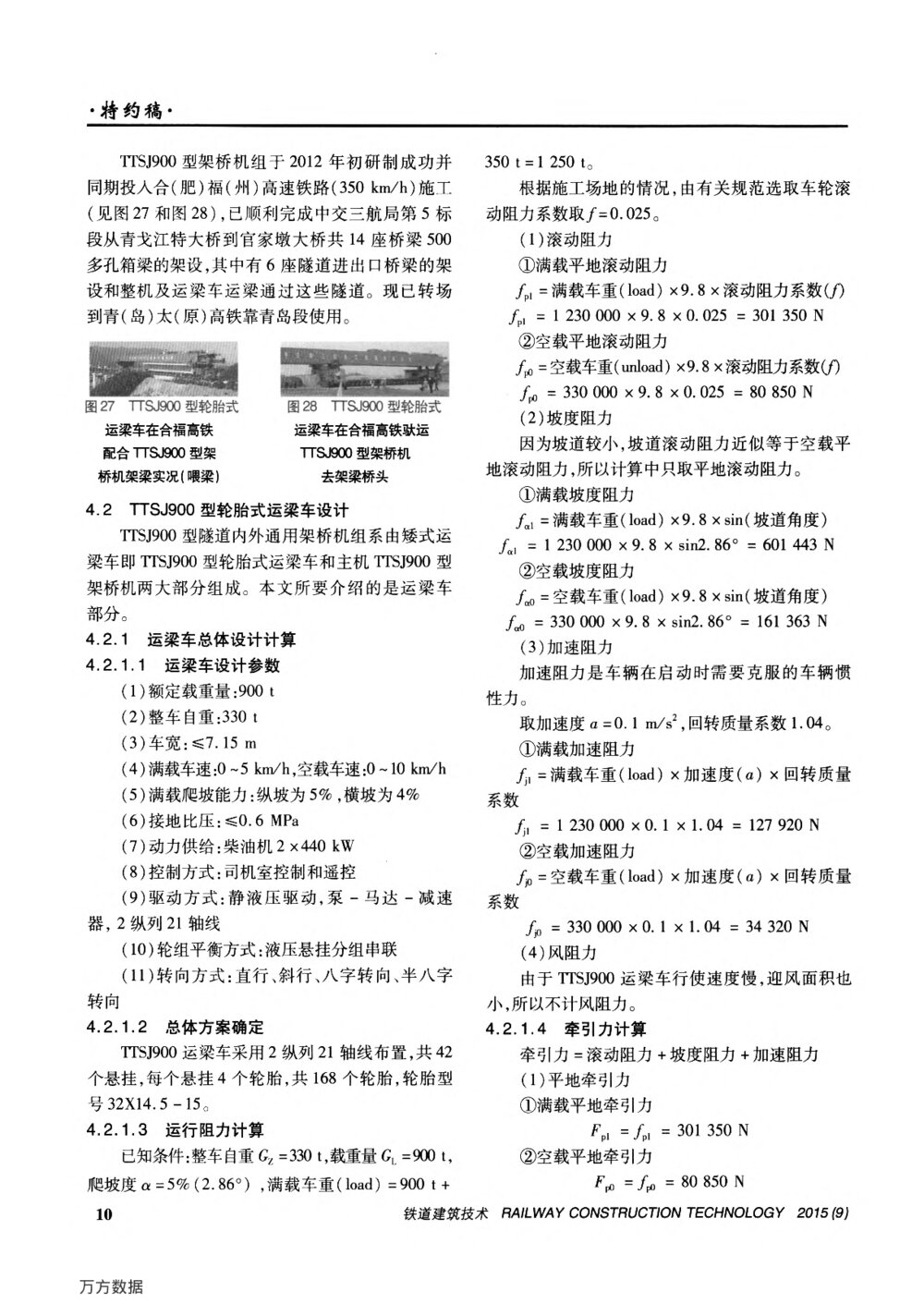
试读已结束,还剩7页未读,您可下载完整版后进行离线阅读
- 1、本文档共17页,内容下载后可编辑。
- 2、本文档内容版权归属内容提供方,所产生的收益全部归内容提供方所有。如果您对本文有版权争议,可选择认领。
- 3、本文档由用户上传,本站不保证质量和数量令人满意,可能有诸多瑕疵,付费之前,请仔细先通过免费阅读内容等途径辨别内容交易风险。如存在严重挂羊头卖狗肉之情形,可联系本站下载客服投诉处理。
・特约稿・论我国大吨位轮胎式运粱车的发展与创新之路(上)黄耀怡余春红(中铁第五勘察设计院集团公司北京102600)摘要从介绍自行式液压平板车(SPMT)的装备和技术在世界上的发展历程到对基于SPMT技术的大吨位轮胎式运梁车在我国的发展与创新之路的论述,内容包括总体方案、细节设计、基础理论、应用技术、典型范例以及我国为科威特王国研制的双幅变幅1∥70060m运梁车的创新成果介绍等。以我国大吨位轮胎式运梁车的发展之路为主线。基础理论与研制实践相结合,展示大吨位运梁车的技术创新之路。关键词大吨位轮胎式运梁车技术基础设计制造发展历程创新之路中图分类号u445.3文献标识码A——文章编号10094539(2015)09一000117DeVelopmentof’ChinasLargeTo姗ageWheelTypeBeamCarrierandItsI衄ovationRoadHuangYaoyi。YuChunhOng(ChinaRailwayFifulSuIveyandDesignInstituteGroupCo.Ltd.,Be妇ing102600,China)AbstractrI'IlispaperstartedoffwithintmductionsontIleequipmentandtechnologyofseHpropelledmodulartransporter(SPMT)f南mthedevelopmenthistoryinthewoddtodiscussingthedevelopmentandinnovationroadinChinafbrlargetonnagewheeltypebe锄ca而erbaLsedontheSPMTtechnology,including:oVeraUscheme,detailsofthedesi印,basictheory,applicationtechnology,typicalex砌pleandinnoVatiVeachieVementsof1700t/60mbe锄c枷erwith—two-锄plitudeandvariableamplitudedevelopedbyChinaforStateofKuwait.Takingthedevelopmentroadof’Chinaslargetonnagewheeltypebe帅c删erasamainline,wecombinedwitllthebasictlleoryandresearchaIIdpracticetodemoIlstratethetechnicalinnovationoflargetonnagebe砌c痂er.Key、阳rdslargetonnagewheeltypebe砌c枷er;technologybase;desigll帅dmanuf如ture;deVelopment‘history;innovatjonmad1引论1.1世界自行式模块运输车(SPMT)概述“自行式模块运输车的英文全称为selfpropeUed”“”modulartransporter,通称缩写SPMT。这种车辆也被通称为自动式液压平板车。自行式液压平板车是在上世纪70年代中期才出现的,此前需要牵引车拖动。这种车系将大功率柴油发动机直接安装在平板车上,在部分车轮中加收稿日期:2叭5一04一08铁道建篱技术RA『LMyCONS丁开UC丁『0~丁E-cH ̄0LOGy装液压马达来驱动车辆行驶。到80年代初期,自行式模块化液压平板车开始兴起,这种采用模块设计、电子控制、可以横向和纵向拼接的车辆,最大载重量已高达万吨级。1957年德国索埃勒(Scheuede)开发出第一款液压平板车(须另加牵引车),1972年,索埃勒开发出电子控制的自行式液压平板车。1982年,索埃勒研制出2015(91图1索埃勒5200t自行式液压平板长车1万方数据・特约稿・世界最大的l800t级模块式液压平板车,1993年,索埃勒开发了世界第一台sPMT,总长80m,共有车轮512个(见图1)。1994年,国际工业运输车辆集团(TII)成立,成员包括德国索埃勒、克玛格(Kamag)和法国尼古拉斯(Nicalas)。自1rII成立后,从此开启了世界超大件运输的新纪元。由他们开发的SPMT系列由4轴和6轴模块组合,其特点是:各模块配置动力头(PPu),液压驱动,液电程序控制,多方位转向,平板靠液压悬挂系统升降。它尤其适合海洋平台移位,最大组合吨位可达1.5万t。这种组合不管有多少轴线,只需1名工作人员通过遥控器即可实现组合车体各个模块的同步动作。而模块可用起重设备吊装,可用汽车或集装箱长途运输,如图2、图3所示。图2模块车的组合图3模块车的长途模式(2个模块组合)汽运(1个模块车)2005年,俄罗斯LUKOIL石油公司为北冰洋建造第一座抗冰石油平台,其底座为一个长×宽×高=53m×53m×45m的八角形钢结构,重10200t。由荷兰玛姆特大件运输公司动用10台索埃勒和克玛格的SPMT(总计432轴线)运输。从2007年7月1日凌晨3点开始到晚上8点运输装船工作全部完成。图4、图5所示为SPMT驮运整体钢桥结构的情景。液压泵,用变量泵驱动液压马达,液压马达经减速机带动驱动桥。现代的SPMT驱动方式的突出特征是驱动轮由单独的液压马达驱动,且液压马达与减速机合二为一,称为车轮液压马达,直接安装到驱动轮轮“”辋内,成为现代专门的轮边驱动技术。大吨位轮胎式运梁车则直接采用了这一技术,见图6。誊嘶l一平衡臂:2一悬挂架;3一悬挂油缸;4一减速机马达:5一摆动桥:6一轮胎轮辋图6大吨位轮胎式运梁车的液压悬挂驱动轮构造图(2)转向系统为了使SPMT实现全轮多方位转向,采用了柴油发动机驱动变量泵一变量马达闭式液压系统,通过微电控制程序控制液压系统实现全轮转向:在每个悬挂架上都装有转角传感器或编码器,来反馈悬挂架的转向信息(方位坐标)给控制系统,该系统通过微电脑计算之后,发送指令给变量泵或电磁多路阀等来控制液压油的流量,液压油经油缸推动转向连杆推动车轮转向,或经液压马达驱动行星齿轮转向系统使车轮转向。而且在微电脑系统的控制下可实现不同模式的转向,例如横行、移行、八字或原地转向等。大吨位轮胎式运梁车也直接应用了上述转向技术,见图7。(3)液压悬挂系统液压悬挂是利用液压油缸来实现传力和减振功能的,钎悬挂通过油路相通来适应路面的不平度万方数据・特约稿・一一≮’1一车架;2一悬挂未;3一悬挂采用液压悬挂系统,另一个重要的功能是,可以提供车辆地板平面的整体升降,这是能够形成SPMT驮运万吨大件技术的核心技术之一。目前SPMT悬挂油缸的行程通常在±350mm以内,而大吨位轮胎式运梁车通常为±300mm。(4)液电控制系统自行式平板车的微电脑液电控制系统主要由以下几部分组成:行走驱动系统、制动控制系统、转向控制系统、悬挂系统、发动机监控系统、防滑差速差力系统、自动调平系统、重心载重显示系统、智能故障诊断系统以及遥控技术等。此外控制系统之间数据的传输采用了当前最为流行的车载cAN总线技术,为实现各节点之间实时、可靠的数据通信提供了强有力的技术支持。大吨位轮胎式运梁车的液电控制系统的传输原理如图9所示。√■I一I1|:铲}一I-|传感器‘覆葡戛驾驶室■l控制器显示器终端电阻终端电阻——厂]广.1-1I————L一‘液压阀液压马达|总线转角传感器图9大吨位轮胎式运梁车液电控制传输原理图1.3大吨位轮胎式运梁车的早期应用概况20世纪70年代初,大吨位箱形Pc梁整体运架技术在意大利面世,当时使用的运梁车为轮轨式(见图10)。1992年韩国正式开始建设京釜高铁,铁道建筑技术RA『LMyCO~S丁尺UC丁『0~丁E-cHNOLOGy随之整体箱梁运架技术在韩国高铁施工中得到应用,其中25m箱梁自重560t,采用意大利提供的轮胎式运梁车运输(见图11)。2000年初,台湾高铁施工再次大规模使用这种技术,由意大利提供的运梁车最大运载量已达915t(见图12)。值得一提的是,2000年我国郑州大方公司生产的DCY450型轮胎式运梁车已在秦沈客运专线施工中使用。这是我国最早自主研制的大吨位运梁车(见图13)。图10意大利轮轨式900t运梁车图11韩国轮胎式560t运梁车图12台湾轮胎式‘图13秦沈客运专线DcY450型915t运梁车轮胎式运梁车——2我国首款轮胎式运梁车DCY450型运梁车2.1概况DCY450型轮胎式运梁车是郑州大方桥梁机械有限公司于2001年与其配套的DF450型架桥机一起研制成功并投入秦沈客运专线施工使用的现代架桥设备,这种大吨位铁路无轮式架桥成套设备在我国尚属首创。2.2DCY450型轮胎式运梁车主要功能特点2.2.1主要技术参数载重量:450t轴距:1500mm轴数:28轴/2列,14轴/列轮胎数:112个,4个/轴,4个/悬挂轮胎规格:11.00R20驱动方式:静液压传动发动机功率:2(台)×330kw行车速度:重载3km/h,空车8Ⅱ∥kh20T5r9J3万方数据・特约稿・爬坡能力:3%悬挂油缸行程:±350mm最小转弯半径:36.5m自重:130t外形尺寸:29.6m×6.55m×2.05m2.2.2主要结构及特点DCY450型轮胎式运梁车主要由车架、驱动桥、从动桥、悬挂装置、轮系、转向系、动力设备、液压系统、电气控制系统、制动系统及驾驶室等组成,如图14所示。l一驾驶室;2一发动机;3一液压;4一制动系统;5一转向装置:6一车架;7一液压悬挂;8一驱动桥;9一从动桥;lO一电气控制系统图14DCY450型轮胎式运梁车设计总图DCY450型轮胎式运梁车主要有以下特点:(1)采用变量泵一变量马达静液压驱动,PLc微电脑程序控制技术,成功解决了行驶中的差速、差力问题。(2)独立悬挂及连杆式转向机构设计,并通过液电控制技术实现多方位全轮液压转向。(3)液压悬挂油路分组连通,使车辆底架成为3点支承的静定格栅梁结构体系,保证了车辆行驶过程的整车稳定性,以及使所运载的箱形Pc梁形式上的4点支承变成实质上的3点支承,即不会发生三足鼎立一足悬空而使梁体承受自重所致的扭剪力。(4)按人机工程设计的双驾驶室,配有监视器、偏载及车体倾斜显示和激光导向装置。(5)液压悬挂油缸行程达到±350mm,能够适应路面严重凹凸不平的恶劣路况。(6)与DF450型架桥机配合进行架梁作业,开创了我国铁路无轨架梁施工的历史,为我国自秦沈客运专线之后的高铁建设陕速施工打下了良好的基础。3我国首台900t级轮胎式运梁车_TLC型运梁车研制3.1概述梁预制场的位置及其周边地理环境的限制,以及PC箱梁梁体构造及力学特性的限制,使得从制梁场到架桥现场之间对PC箱梁的运输必须使用轮胎式特种车辆。TLc900型运梁车正是为了满足这种需要而研制,见图15。图15TLC900型运梁车样车重载(1000t)试验实景由秦皇岛天业通联公司研制的本型运梁车主要用于运输跨度为32m、24m、20m的双线整体箱形PC梁,并能与架桥机配合完成相应的架梁作业、驮运架桥机实现桥问短途转场,或穿越双线单洞隧道。TLC900型运梁车系机电液一体化的现代化特种车辆设备,采用液压驱动、液压悬挂、液压转向技术,它们的操作均采用电液比例控制。从实际操作面板上系体现为工业微机来控制驱动、转向、悬挂的升降和调平,以即时实现直行、斜行、八字转向、半八字转向等多种运动模式,从而使整车达到灵活、平稳、无滑移行驶,且可在窄小场地执行工作任务。运梁车还具有自动辅助驾驶、遥控、防撞和故障诊断等智能化系统。这是我国拥有完全自主知识产权、与国际知名产品技术水平相当的先进成果。自秦沈客运专线建成并于2003年10月12日正式通车运营之后的2005年,我国同时有多条时速300km的客运专线开工建设,包括武广线、石太线、郑西线等。因此,给TLc900型轮胎式运梁车提供了广阔的施工平台,由于该运梁车设计合理,制造精湛,且与配套的TLl900型架桥机架梁施工配合良好,经得起现场长期使用考验,TLC900型轮胎式运梁车作业实照见图16、图17。由于高速铁路线路道床技术要求的限制、Pc箱4铁道建筑技术毒刍互图16TLC900型轮胎式运梁车在现场运梁实照图17TLC900型轮胎式运梁车与TU900型架桥机配合架梁作业图RAf正-MyCO~S丁开UC丁『O~丁EClHN0£-0Gy2075俐爵万方数据・特约稿・3.2TLC900型运梁车主要性能指标(1)平台地板尺寸:2.1×35.2m;地板轨顶距地面最低高度:2.5m(2)额定载重量:900t;适应梁型及梁跨:双线箱梁,32m、24m、20m(3)轴线/悬挂:16/32(每悬挂含1对轮胎),轮胎直径x厚度=1734mmx698mm(4)重载速度:0~5—Wh;空载速度:010km/h(5)适应路面坡度:纵坡5%,横坡4%(6)运行模式:直行、斜行、八字转向、半八字转向,最大转向角度:d=±30。≥(7)最小转弯半径:R35m(8)悬挂升降能力:^=±300mm≤(9)轮胎接地比压:P0.6MPa(10)装机容量:2×400kw;液压油箱容积:2400L(11)自重:268t3.3TLC900型运梁车系统组成与设计整车由车架(含前后辅助支腿)、活动及固定枕梁、悬挂、动力系统、液压系统、电气系统、控制系统、制动系统、转向系统及操纵系统(驾驶室)等组成。3.3.1总体结构设计3.3.1.1总体结构组成在设计过程中将车架、驾驶室、动力仓、枕梁、悬挂等划归为总体结构组成,见图18。l一后驾驶室;2一动力仓:3一活动枕梁:4一车架:5一悬挂;6一固定枕梁;7一前驾驶室图18TLC900型轮胎式运梁车结构总体组成图3.3.1.2总体结构的力学行为和整车倾覆稳定性设计(1)在运梁工况时的力学行为和整车稳定I生设计根据桥梁设计图纸规定,高速铁路双线整体PC梁在运输过程中,梁体四点应位于同一平面,误差不应大于2mm。这是为了防止箱梁受扭。于是把运梁车的悬挂油缸并联起来并进行分组,前端8轴线两侧共16个悬挂油缸连通,即相当于一个支点(C),后端8轴线16个悬挂油缸按侧连通(8缸)而两侧互不连通,则相当于2个支点(A、B),见图19。这样就形成了典型的格栅梁系平面3点支承的静定结构体系;同时由于A、B、C三点与车辆中轴对称,所以只要在装载时保证Pc箱梁的几何中心与运梁车中心一致,则A、B、C三支点反力恒等,于是PC箱梁梁体任何截面均不会产生附加弯矩或扭矩。图19运梁工况时悬挂油缸分组形成3支点由于PC箱梁装载在车板上时,4个支点位置是固定不变的,而在车辆运行过程中,正如此前关于液压悬挂系统所述原理,每个轮胎的反力相等,所以车辆板架结构可采用图20所示高精度的平面简支梁模型进行计算。图20车辆板架结构的简支梁模型图20模型系将实际的车辆运载PC箱梁的情景倒置而来,目的是为了突出按简支梁模拟的效果。本来是14次超静定的弹性支承连续梁的复杂问题,而转化为高精度(实际上为精确解)的简支梁模型,极具创造性。由此模型可以直观地看出,运梁车在运梁工况中,其整车纵向倾覆稳定性可得到绝对保证。再从此前分析及图19所示可知,车辆已形成品字形的3点支承并有电液自动控制的液压悬挂调平,同时PC箱梁总是准确对称地装载在车辆平台地板之上,其十字形中线恒与车辆重合。所以,整车的横向倾覆稳定性亦同样可得到保证。(2)配合架梁工况时的整车稳定性设计运梁车配合架桥机架梁时,架桥机在后悬臂处将运梁车上PC箱梁的前端吊起,拖着沿架桥机主梁前移,搁在运梁车活动枕梁上的Pc箱梁后端沿着运梁车上的轨道同步向前滑行,直至车头位置,架桥机再将该梁的后端吊起,如图21所示。铁道建筑技术RA『LWAyCONS丁开UC丁『0~硅_Cf_f ̄0LOGy20T5r9J图21运梁车配合架桥机架梁后端起吊情形5万方数据・特约稿・由上述车上移梁过程可以推知,在PC箱梁后端达到图21所示位置且架桥机尚未将其吊起时,对车辆的纵向稳定性最不利。可以想象,假设16轴全部悬挂并未分组控制,而是油缸全连通,则各轮胎反力基本相同,于是全车就有可能绕其前端(Pc箱梁后端压点)翻起来,即纵倾。为了防止此种危象的发生,须将悬挂按图22所示分成2×4组,各组独立连通。图22架梁工况时悬挂油缸分组形成2×4支点由以上的分组结果可知,沿车辆纵轴4组,各轮胎组反力是不相同的,而各组内的轮胎反力则是相等的。于是车辆板架结构应采用图23所示的平面弹性支承连续梁模型进行计算。JRIR2尺3尺。l1511:!盟』∞,.一板架主梁惯性矩;厶=;虚拟梁惯性矩;K一每轴轮胎刚度系数图23车辆板架结构的弹性支承连续梁模型实际上对图23所示模型予以进一步简化后,即可采用经典的手算方法进行计算,见图24。重/2被,彻:姐34见图24车辆板架结构的4跨弹性支承连续梁模型由图23与图24对比可见,两者是完全等效的。由图24所示模型求出每轴线悬挂(轮胎)反力R。一尺。之后,即可按图25所示模型计算运梁车的纵向倾覆稳定性。35.2mⅡⅡⅡⅡⅡⅡⅡⅡⅡⅡⅡ.工卫工啐工卫工j田.RlR1R1Rl尺!只!R:尺:R3R3尺3月3R4詹4詹4R{l!i!!:!里J图25运梁车纵倾计算模型运梁车绕A点的稳定力矩等于运梁车自重(含轮胎重等)对A点的力矩;绕A点的倾覆力矩等于反力尺,~R。分别对A点的力矩之和。前者与后者之比不小于1.3即为安全。’为了求出图24所示模型的支反力,兹设K=4K,尺j=4尺l,尺:=4尺2,R:=4尺3,R:=4尺。。由于本车辆的板架主梁是等刚度的,弹性支承是等刚度和等跨度的,因而可将弹性支承连续梁五弯矩方程式的一般形式推演成如下适用于本运梁车工况的实用五弯矩方程式:咋:南+%。(击一寿)+州盖+景)+‰c击一南,+帆轭南=一篙一豢+凳一等(1)’式中,肘。为第n个支点弯矩;z为支点跨距;K为弹性支承刚度系数,即弹簧压缩一个单位长度所需要的作用力;肼。为连续梁的刚度;A:为当连续梁被隔离为多跨简支梁后,荷载作用在第n跨及第n+1跨上时所引起的支点n的总虚拟反力。而虚拟荷载的大小等于真正载荷在简支梁内产生的弯矩图面积;A。为上述简支梁由外力引起的支点n的反力。’将式(1)两边各乘以z2K,并设a=器,仅为弹性特征系数,最后得到:M。一2+M。一l(a一4)+M。(4a+6)+肘。+l(d一4)Ⅲ+M:一半一f(A¨一2A。+A川)(2)弹性支承连续梁的超静定次数等于支点数减二。在每一个支点上都可以按式(2)写出五弯矩方程式,解联立方程式即可求出各支点弯矩,于是可按一般连续梁的公式求出各支点反力:R::A。+坠_掣(3)为了便于计算运梁车在配合架设20m、24m、32m箱梁时的整车纵倾稳定性,可根据以上各式先作出支点反力影响线坐标,然后再根据实际工况加载求反力。对于图24所示连续梁,其反力影响线坐标求得列于表1。6铁道建篱技术闩饵fLMyCO~S丁RUC丁JO~丁ECH~OLOGy2075俐万方数据・特约稿・表1图24所示弹性支承连续梁反力影响线坐标声、低油耗等优点,首次大修里程超过100万km。——L』堕掣些堕垡毕量壁堕堕挚堕一每台发动机各自带动驱动油泵、工作油泵,三—■——]T伍ii五ir百石1rif_石泵串联,通过联轴器直接联结到发动机飞轮端。两苎曩I28+9a‰16++15fl4+2la—26a台发动机带泵双泵合流为执行元件提供液压油,也甬羔B}!二塑l!±!!!.1鱼±婴±!鲨l!±!竺一可单泵独立工作。——‘——匕L二兰兰r_上笔竽上j生堕止生巡3.3.3液压系统戳卢纠¨∞∽时旷面驱动系统为闭式静液压系统,电液比例控制。对于TLC900型运梁车,已知:工作液压系统为开式液压系统,采用恒功率+负荷,.=2.2×1011mm4,F=1.40×104N/mm,传感控制,把系统的外负荷的变化通过传感元件反Z=8400mm.E:2.1×105MPa馈到变量泵的变量控制系统,根据需要自动调节输求得:出流量和工作压力,以使子系统处于最佳功效匹配a:0.03,8:21.68状态。工作液压系统包括液压悬挂系统、液压转向当P=450t(PC梁重的一半)作用在第4个支系统和液压支腿系统。液压悬挂系统采用电液控点上时,可由表1算得:制,可以实现分组升降和整体升降;液压转向系统R:=323.23t,R:=171.66t,尺:=37.78t,R:=0为电液比例闭环控制,精确控制各轮组的转角;液即R。=323.23/4=80.81t,尺,=42.92t,R,压支腿系统为手动控制,结构简单,操作方便。=9.45t,R,=O。R:实际算得为负值,即受拉;但轮液压系统中在转向系统、升降系统、驱动系统、胎组搁置于地面上不能抵抗拉力,故令尺:为零。制动系统及支腿系统中设置了多个测试点位,满足于是按照图25(运梁车自重线载荷g=79.5Wm)检查所有油路的要求。可算得配合架梁时整车绕A点力矩为:设计中采用并联油路和数字差速的方法使各M穗=44074.8kN・m驱动轮的牵引力基本接近,并能有效地防止滑转。‰=37545.9kN・m每个驱动轮由一个变量液压马达经轮边减速器驱得出纵倾稳定安全系数为K=1.17。所以,为了使动,液压马达上安装有转速传感器。所有液压马达稳定性满足要求,在车头前端增加液压支腿左右各一并联连接,当液压马达排量相等时,输出扭矩也相个,其额定支承力合计为160t,支点在图25所示A点等,各轮牵引力相等。当某个车轮因附着力不够,前端2m处。如此使得稳定安全系数达到K=1.5。发生打滑时,液压马达转速大大超过平均转速,计(3)小结算机马上减小马达排量,减小输出扭矩,车轮的滚11Lc900型运梁车整车稳定性是事关车辆安全动阻力使马达减速直至达到容许转速范围内。的关键技术问题,采用电液控制的液压悬挂调平技同时,在设计中采用双管路加防爆安全阀进行术,并加以科学设计、合理布置和通过对弹性支承管道防爆保护,当一条管路爆裂时,防爆安全阀可连续梁的精确计算,使得TLC900型运梁车不论在以立即关闭爆裂的油路,另一条管路正常工作,可运梁过程中或在配合架桥机架梁工况中,其整车的以使车辆正常行驶;即使两条油管同时爆裂,防爆纵、横向倾覆稳定性安全系数均不小于K=1.5,从安全阀可以瞬间关闭系统爆裂支路和悬挂,悬挂可而保证了车辆的平稳可靠性,并经实践检验(见图以继续起支撑作用,从而避免危险的发生。17),上述设计理论和方法是正确的。3.3.4电气系统3.3.2动力系统3.3.4.1电气控制系统本车选用著名的道依茨BFMlol5型发动机。运梁车的电气控制系统采用了cAN总线技术,BFMlol5系列柴油机是当今世界上先进的水所有的电气控制均由一套基于现场总线(cAN一冷柴油机,功率范围190一440ⅢkW,排放可达欧洲BUS)的PLC控制系统来实现,电气控制系统传输标准。配置道依茨供油系统、增压中冷、四气门、中原理见图9。央喷油器等最新技术,品质卓越,具有低排放、低噪主要电气控制元件均选择进口工程机械专业产钐}道建筑技|术RA,LwAyc0NS丁RUC丁『oN丁ECHN0loGy’2D5r9J7万方数据・特约稿・品,该器件经过实际应用考验,安全可靠,能适应露天、雨雪、灰尘、振动等运梁车野外作业的恶劣环境。控制采用现场总线方式,其优点为:(1)电缆布线简单,节点少,可靠性高,连接检查工作量小。(2)容易进行故障诊断和运行状态记录,有利于实现状态维修。(3)设置控制点方便,容易更改和增减。3.3.4.2自动辅助驾驶系统.自动辅助驾驶系统采用先进的视觉导航技术,原理如图26所示。||固||圄||{I固|J固||L::意.:::i,j视频信号二兰:三#三军.j@视频错t频。茅信号e嘲窝’工控机啪左旧\\//图26自动辅助驾驶原理图运梁车前后各设置2部摄像头,在地面画出标志线。摄像画面采集后传送给驾驶室的辅助计算机,一方面在驾驶室的显示器上显示画面,以帮助驾驶员直观观察;另一方面由辅助计算机进行图像处理,分析得出运梁车的行驶路线偏差,以数值形式传送给电气控制系统并在液晶显示器上显示,控制系统根据该偏差数据,给出正常行驶或告警信息,由驾驶员采取相应措施,当偏差超过一定值时,车辆会自动减速甚至锁闭。当运梁车自动驾驶时,自动辅助驾驶系统可以将分析得到的行驶路线偏差转换成控制指令,通过对驱动、转向等工作的实时调节,控制车辆在预定的路线上行驶。3.3.4.3遥控操作系统运梁车在正常行车工况下驾驶员在驾驶室内操作,但是在对准架桥机、狭窄路况、装卸桥梁等场合,为了保障驾驶员人身安全,或者为了便于更精确地控制车辆,驾驶员可以离开驾驶室,在安全、便于观察和操作的位置对车辆进行遥控。遥控操作系统的接收端与电气控制系统直接通过L/O触点连接,遥控器发出遥控指令直接作用到运梁车的电气控制系统上,可以实现车辆的前进、后退、转向、制动、点动等操作,遥控操作的实时性好。当遥控器超出控制距离或遥控控制系统出现故障时,控制器会发出声音和灯光报警。3.3。4.4定位和防撞系统运梁车前端安装了激光测距仪,精确地测量前方目标的距离,以便和架桥机实现精确对接,并能实现提前减速和制动控制,避免因误动作而与架桥机发生碰撞。运梁车前后和两侧安装了测距雷达,构成了一个完整的防撞体系,提供了进一步的安全防护保障。3.3.4.5故障报警与诊断系统运梁车设置各种传感器,通过故障诊断软件实时监控系统运行情况,在某一系统出现故障时给出警告提示,根据面板报警灯、报警提示音及屏幕文字提示可以及时判断系统故障,对操作人员及时排除故障提供可靠依据。3.3.5制动系统特大型运输车的制动系统,除了必须具有足够的制动力外还必须对制动减速度进行控制。本车制动系统包括行车制动、驻车制动与紧急制动。行车过程制动主要通过控制驱动液压系统来实现。当操作者释放车速脚踏板时,驱动泵(采用变量泵)排量逐步降低,车速也随之降低。当脚踏板完全松开,变量泵排量为0,在液压阻尼的作用下,实现行车制动直至停车。驻车制动:常闭式盘式制动器安装在驱动轮系的行星减速机内,行驶时依靠液压开启。运梁车停车时,驱动泵排量降至0,液压阻尼使得系统减速直至停止;同时,驱动系统压力降为0,制动器卸压,在弹簧力的作用下与制动盘结合,实现驻车状态下制动。紧急制动(行车制动):紧急情况下,操作者首先抬脚释放行车控制脚踏板,驱动系统停止供油,液压阻尼使得系统减速;踩下刹车脚踏板,使压缩空气从储气罐通过控制阀直接供给隔膜式制动气室,系统快速减速并实现紧急制动。3.3.6转向系统本车采用全轮独立转向,转向系统由比例阀控制转向油缸推动回转机构来实现。上层PLC按照运行模式和方向盘的指令,解析出各轮组转角;下层控制器按照转角指令值控制转向系统,安装在转向系上的角度传感器实时测得当前转角,反馈给控制器,构成闭环控制,实现精确的转向控制。单轴转向精度为0.5。。8铁道建筑技术RAILWAYcONsTRUCTIONTEcHNOLOGY2015(9)万方数据・特约稿・整车可以实现直行、八字转向、半八字转向、斜时代。如大西南地区有长(沙)昆(明)高铁、大西北行等多种转向模式。地区有宝(鸡)兰(州)高铁,可为典型代表。它们先转向油缸与悬挂油缸及支腿油缸共用一组工后于2010年3月和2012年10月开工。在这些地作泵,该组工作泵包括2个力士乐产A11vol90开区修建高铁,是过了桥梁就是隧道,桥隧相连,更有式泵。转向油缸为31.5MPa级高压油缸,全部采用“”甚者,在隧道内还要修桥,叫隧中桥;这是为了跨进口PARKER密封,安全可靠性高、动力性能好,可越隧内溶洞地段的需要。所以,施工开始之前,首以实现全负荷下转向。液压油缸轴承全部采用免先要考虑解决大型架桥机整机能够自由通过隧道、维护轴承,减少操作者劳动强度,提高工效。抵近隧道进出口架梁和在隧道内也能架梁的诸多3.4总结问题。因为早期我国高铁主要在地形平缓地区修综上所述,TLC900型运梁车有如下特点:建,很少遇到隧道。因此当时设计制造的架桥机大(1)整车结构设计合理,车架、悬挂等关键结构多没有考虑整机自由通过隧道的功能,只是权宜之件均经过了可靠性设计和有限元校核。并针对悬计地考虑一旦碰上隧道只好临时采取部分解体或挂总成进行专题试验以指导设计。改造措施。须知,在进隧道前要解体,在出隧道后要(2)采用双动力系统,增大了系统冗余性。即复原,这是非常复杂繁重的劳动。偶然一二次也就能使一套系统出现故障,也能保证车辆顺利驶达终点勉强为之,在山区修高铁可就绝对不能如此了。于(驱动能力不变,速度降低一倍)。是,我国于2009年就专门研发了TrY舢型运架一…(3)基于现场总线(CAN.BuS)的控制系统,保体机等机型,解决了过去整机不能自由通过隧道这证了整车运行动作的协调可靠。一施工难题。但是这种机型存在一个严重的缺点是(4)具备承载力监测控制、转向协同控制、驱动“”体大笨拙,这正是它追求运、架、提三位一体所带来防超速(防打滑)等功能。的负面效果。笨大的躯体长达70多m(后来的运架(5)具有视频监视和基于图像识别的运行偏差一体机新机型即SLJ900/32型流动式架桥机竞长达监控系统,确保车辆运行的安全可靠,且能实现自93m),这致使在制梁场中提取箱形混凝土梁动作动驾驶。缓慢困难,在运梁途中行驶更加缓慢不便,沿途必(6)整车运行参数实时监控,具有超限报警和须事先准备好广阔的无障碍空间条件。因而其工应急锁定功能,包括承载超限、转向误差超限、整车效较低,油耗量成倍增加,运梁成本加大(包括便道跑偏等。修建)等。因此可知,运架一体机方案并非是解决(7)车辆前端安装了激光测距仪,精确地测量过隧道问题的一个优化的全面解决方案。我国幅前方目标的距离,以便和架桥机实现精确对接,并员辽阔、地形复杂,要尽快修建一个覆盖全国的高能实现提前减速和制动控制,避免因误动作而与架速铁路网,大型架桥机过隧道等问题须彻底解决。桥机发生碰撞。就是在这样的背景下秦皇岛天业通联公司提出了(8)发动机、液压元件、控制元件和轮胎等关键卿00型隧道内外通用架桥机组研制项目,并得件全部采用进口一类品牌,以确保系统的高可靠性。到河北省政府的高度重视,被批准立项。该项目的(9)悬挂支撑作为承载的关键部件,管路设计主要研发内容是研发一种在高速铁路隧道内外都采用了双管路加安全阀的配置,保证了即使在管道“能顺畅通行和方便完成架梁作业的隧道内外通用爆裂的情况下,悬挂系统仍能正常工作,极大提高”架桥机组。该机组在系统设计上拟采用矮式运梁了运梁过程的安全性。车和坦式吊梁天车技术,采取后悬臂喂梁,前悬臂:o啪。型隧道内外通用架桥机组运梁蓑黎嚣淼裟蒜茬需囊萎蓑…十甲。作就可以进行桥间自行转移、通过隧道、在隧道进4.1TTSJ900型隧道内外通用架桥机组装备简介“”口和出口以及隧道内架梁。做到随行随架,先进随着我国高速铁路的发展,高铁已经进入山区实用。铁道建筑技术只AJL¨伪yC0 ̄S丁开UCT-『0N"-C删0fOGy’2D5r9J9万方数据・特约稿・’,ITISJ900型架桥机组于2012年初研制成功并同期投入合(肥)福(州)高速铁路(350km/h)施工(见图27和图28),已顺利完成中交三航局第5标段从青戈江特大桥到官家墩大桥共14座桥梁500多孔箱梁的架设,其中有6座隧道进出口桥梁的架设和整机及运梁车运梁通过这些隧道。现已转场到青(岛)太(原)高铁靠青岛段使用。图27TTsJ900型轮胎式运梁车在合福高铁配合T1_s目)0型架桥机架梁实况(喂梁)图28TTsJ900型轮胎式运梁车在合福高铁驮运T1_S1900型架桥机去架梁桥头4.2。rTSJ900型轮胎式运梁车设计’rrISJ900型隧道内外通用架桥机组系由矮式运’梁车即1TISJ900型轮胎式运梁车和主机TTSJ900型架桥机两大部分组成。本文所要介绍的是运梁车部分。4.2.1运梁车总体设计计算4.2.1.1运梁车设计参数(1)额定载重量:900t(2)整车自重:330t≤(3)车宽:7.15m(4)满载车速:0~5∥∽kh,空载车速:0~10h(5)满载爬坡能力:纵坡为5%,横坡为4%≤(6)接地比压:0.6MPa(7)动力供给:柴油机2×440kW(8)控制方式:司机室控制和遥控(9)驱动方式:静液压驱动,泵一马达一减速器,2纵列2l轴线(10)轮组平衡方式:液压悬挂分组串联(11)转向方式:直行、斜行、八字转向、半八字转向4.2.1.2总体方案确定rITI'SJ900运梁车采用2纵列21轴线布置,共42个悬挂,每个悬挂4个轮胎,共168个轮胎,轮胎型—号32X14.515。4.2.1.3运行阻力计算已知条件:整车自重G:=330t,载重量G。.=900t,350t=l250t。根据施工场地的情况,由有关规范选取车轮滚动阻力系数取.厂=0.025。(1)滚动阻力①满载平地滚动阻力工。=满载车重(10ad)×9.8×滚动阻力系数(力丘l=1230000×9.8×0.025=301350N②空载平地滚动阻力厶=空载车重(u11load)×9.8×∽滚动阻力系数厶=330000×9.8×0.025=80850N(2)坡度阻力因为坡道较小,坡道滚动阻力近似等于空载平地滚动阻力,所以计算中只取平地滚动阻力。①满载坡度阻力丘。=满载车重(10ad)×9.8×sin(坡道角度)六1=1230000×9.8×sin2.86。=60l443N②空载坡度阻力厶=空载车重(10ad)×9.8×sin(坡道角度)厶=330000×9.8×sin2.86。=161363N(3)加速阻力加速阻力是车辆在启动时需要克服的车辆惯性力。取加速度口=0.1∥ns2,回转质量系数1.04。①满载加速阻力,。=满载车重(10ad)×加速度(o)×回转质量系数Zl=l230ooo×o.1×1.04=127920N②空载加速阻力厶=空载车重(10ad)×加速度(o)×回转质量系数厶=330000×0.1×1.04=34320N(4)风阻力由于TTSJ900运梁车行使速度慢,迎风面积也小,所以不计风阻力。4.2.1.4牵引力计算牵引力=滚动阻力+坡度阻力+加速阻力(1)平地牵引力①满载平地牵引力‘F,l=l=301350N②空载平地牵引力爬坡度d=5%(2.86。),满载车重(10ad)=900t+10钐}道建筑技术‰=厶=80850NFM』LWAyCONS丁开UC丁fO~丁E_Cf_f ̄0£-0Gy2D75r9J万方数据・特约稿・(2)坡道牵引力①满载坡道牵引力‘F。l=l+五1F。1=301350+601443=902793N②空载坡道牵引力}j俚0=j曲+j曲F棚=80850+161363=242213N(3)平地启动牵引力①满载平地启动牵引力‘Fpjl=l+Zl=301350+127920=429270N②空载平地启动牵引力Fpio=厶+厶=80850+34320=115170N(4)坡道启动时牵引力①满载坡道启动牵引力F1=厶l+正l+,1FI=301350+601443+127920=1030713N②空载坡道启动牵引力F、={曲七{由七{o凡=80850+16l363+34320=276533N4.2.1.5发动机选型计算发动机功率:P=n”其中,F为牵引力,为在此牵引力下的速度。(1)平地运行最大功率计算由运梁车设计参数可知:满载平地最大行驶速度为".=5∥knh=1.389rn/s,空载平地最大行驶速度为%=10kIn/h=2.778∥ns。由平地牵引力计算可知:运粱车平地满载运行所需牵引力比空载运行所需牵引力大得多,所以只需计算满载平地运行功率即可。满载平地运行功率:P。=F。。秽,,则P,=301350×1.389=418575W一419kW(2)发动机功率计算’取机械液压总效率7=0.65,则:所需发动机功率P=满载坡道运行功率P。/机械液压总效率卵,即P=419/0.65=645kW考虑1.2倍的驱动动力储备系数和估算转向系统功率90kw,则发动机功率为:P=1.2×645+90=864kW采用双发动机驱动,每台发动机功率P0=P/2=864/2=432W(3)发动机选型选用道依茨发动机BF8M1015cP,功率为440kw,转速2100r/IIlin,最大扭矩2350∥N・n1250I/Hlin。4.2.1.6轮胎的选定Ⅱ耐900运梁车轮胎数量为168,根据满载重量初步计算单胎承载力:t=(900+330)/168=7.32t,选—用轮胎型号为32x14.515轮胎。4.2.1.7总图设计根据上述内容和相关计算结果,可作出该矮式运梁车的总图设计,如图29所示。由图29可见,TTSJ900运梁车由主梁、横梁、液压悬挂轮组、动力系统、液压系统、电气系统、控制系统、制动系统、转向系统、支腿及驾驶室等部件组成。1TrSJ900运梁车发动机后置,主梁中置,2纵列21轴线;每轮轴8车轮,共168轮;13轴线驱动,共—104轮。轮胎采用泰凯英32x14.515无内胎充气轮胎;采用液压悬挂、液压驱动、液压制动、电液转向;控制系统采用现场总线控制模式,前后端设置相同配置的驾驶室。≤燕=磊磊i霭图29TTSJ900运梁车总图4.2.1.8驱动轮计算(1)驱动轮布置:13轴驱动,每个驱动轮为双Ⅳ胎,总驱动轮数=13×2×2=52。最大牵引力时单胎驱动轮牵引力:FI:争:掣:20149N‘1^,<,,’’‘’一一一(2)地面附着力对于碎石路面,附着系数西=0.60。平均每轮载荷:≥P=!乏F:9.8=王里!堕旦铲×9.8=7・750N单轮胎附着力:E=P×0.6=71750×O.6=43咖N单轮胎附着力疋>最大牵引力时单胎驱动轮牵引力F.,行走时轮胎不会打滑。4.2.1.9减速机计算减速机实际最大驱动力矩:钐}道建笳技术RAfL蝴yC0~S丁RL,C丁『0~丁E_cHNOLOGy2D,5例1l万方数据・特约稿・…戴爬懋t奎磐:“空载平地妄达转速:二2置2冀篓篓…咿;。:熏赫晒.4划in’.,。堡塑妻彗竖i唆于鼍,挚蝥蝥曼马挚:萨奥H1m≥≤¥袅平地薹嘉量:…060,是跫曼竺。兰裂?篓}、:娑:智’∞如声私君:荔i赢・7舰:・嘶V商n竺.要登竖篓三苎,液压马达工作压差计算Z2.j.i;~鑫矗;#;液压马萼三仨压差:(1)液磊孬圣竺熏睡%鬻登登帕拙口、+小:嚣勰励脯勘观~嘲。重载爬坡工况,车速2k-ll/h,重载爬坡马达“’州慨刁一叫"里重蓑_地单个苎登竺驱动扭矩:Z三.I儿_;2车架结构设计计算≯瓦:!重载:塑与竽×o.38:2202N.m车架结福主孬并算毫括羞已知各种工况条件万方数据・特约稿・腿对运梁车作用力R=100t,运梁车自重G=330t,运梁车21轴线悬挂沿纵向分成2组(前10后11),形成简支的两点支撑,简化后的模型如图30b所示。a.运梁车驮运架桥机桥间转移IF=100tIG=330tIF,=500t88065594lll5257975b.运梁车驮运架桥机桥间转移纵稳性计算模型图30运梁车驮运架桥机桥间转移及纵稳性计算模型倾覆点为A点,计算倾覆力矩M倾和稳定力矩M稳。有:肘倾=500×7975=3987500‘tmmM稳=330×11525+100×25925=6395750‘tmm运梁车纵倾稳定性系数:皓急=勰-1.6>1.5(观稳定性满腰求)4.2.3运梁车驮运架桥机进行桥间转移之步骤对照图31来说明rrI踟900型运梁车驮运1TIsJ900型架桥机进行桥间转移之步骤。(1)末孔梁架设完毕,前后天车后退至主梁后端。(2)辅支腿顶升支撑,收起前支腿。(3)前支腿自行退回至运梁车前端踏座上支立,并把前支腿与运梁车锚固好,解除运梁车前端与已架梁吊孔之锚栓,稍稍收起辅支腿,运梁车即可驮运架桥机整体前行。…—叠!===1——————J_-・・一一J¨’雾;:=喜E!了●—……_--_l___青~一目,图31TTSJ900型运梁车驮运TTSJ900型架桥机进行桥间转移之步骤图动均衡系统,以及架首孔梁之后各孔梁的底车抗后倾技术,是此研制项目所必须解决的关键技术和重大创新技术之一,它能够保证架桥机组在整个架梁过程,底车系统的纵向稳定性自始至终都能得到保证。至于架梁过程底车系统存在纵向失稳问题,后文将会予以叙述。4.3.1TTSJ900型隧道内外通用架桥机组首孔梁架设步骤TTSJ900型架桥机组系作业时,主机与底车要相互配合使用,其架设一座桥首孔梁的步骤如图32所示。第l步:架桥机主机主梁成后悬臂喂梁状态,后端行走支腿向后翘起,承重后支腿缩起,底车系统把混凝土梁从后方运来并送进主机腹内即后悬臂“”下方,此过程称为喂梁。第2步:运梁车喂梁到位后,主机承重后支腿落下,支立于底车系统后部横垫梁并与之连接。第3步:原支立在中间桥墩上的移动式支腿前移到前方墩支立,使架桥机成为两跨式架梁状态,两台天车将混凝土梁从底车上吊起。第4步:主机上两台吊梁天车吊运混凝土梁到桥孑L位置落梁就位。第5步:落梁到位后,移动式支腿从前方墩退回到桥台胸墙顶上支立,拆除主机承重后支腿与底车系统后部承重横垫梁之间的连接,承重后支腿缩起;此时,底车可退出到后方去运梁。图32丌SJ900型架桥机架首孔粱步骤图4.3架梁过程底车系统(兼运梁车)的纵向稳定性由上述可见,第3步存在问题:当前、后吊梁天控制车同时从运梁车上起吊混凝土梁时,底车后部横垫在n踟900型架桥机组研制项目中,提出了用梁上的承载重量将达到最大值,而位于底车前端的于架首孔梁工况的底车(亦即配套运梁车)承重自横垫梁,作为所装载混凝土梁的前支点,其上的承铁道建筑技术F矾『LWAyc0NSmUC丁『0N了ECH~0£.OGy’205佃J13万方数据・特约稿・’需如此,十分繁琐。为此,在1TISJ900型架桥机组的l、2、3一£盖式支腿:4一液电程序主端系统:5一底车研制项目中,提出了一种可在架首孑L梁的工况中,曼鼗蔫蠢;蠢童麟盈壹躲蠢谚嬲自始至终都能自动得到保证底车系统纵向稳定性图33丌sJ900型架桥机组底车承重自动均衡系统构成图——的方法底车承重自动均衡系统。4.3.2底车承重自动均衡系统4.3.2.2底车承重自动均衡系统的控制原理4.3.2.1设计思路及结构组成底车系统各轮胎组的悬挂液压缸(见图34)设底车承重自动均衡系统的设计思路是:将天车起计为前后两组。各组内又由若干单元悬挂液压缸吊混凝土梁时,经由主机承重后支腿传给底车系统后组成,组内各单元悬挂液压缸是相互连通的,即在部承重横垫梁的巨大压力所造成的底车系统向后倾同一动作中,组内各液压缸的压力相等。但前组和翻的力矩,由所述承重自动均衡系统所产生的抗后倾后组悬挂液压缸之间压力一般是不相等的,因而底力矩(亦即稳定力矩)来抵消并留有安全盈余,而无车系统的液压悬挂体系实际上分为2个液压悬挂中需从外部以强迫锚固方式予以达成。具体为:心:前悬挂中心及后悬挂中心。(1)在底车系统车架主梁后部、承重横垫梁后假设前悬挂组包含的单元悬挂数量为n,后悬侧安装3对液压缸式支腿,如图33所示,各液压缸挂组包含的单元悬挂数量为,n,则前悬挂组各液压所容许的最大支撑力经设计计算确定。缸压力之和为n×p,(1P,为前悬挂组单元液压缸压(2)在底车系统配置一套液电程序控制系统力,包含自重和吊重,下同),其合力中心即为前悬(PLc系统),统一控制3对液压缸式支腿的液压缸挂组的几何中心;同理可定义出后悬挂组各液压缸压力和动作(缩起或伸出)。控制各支腿液压缸的压力之和(m×p,,P,为后悬挂组单元液压缸压力)压力随主机系统承重后支腿传给底车系统后部承及其几何中心。重横垫梁的压力的增大(减小)而增大(减小);当前前、后悬挂中心和3对液压缸式支腿共同构成后吊梁天车抬吊混凝土箱梁沿主机主梁向前方桥了对底车系统本身及支立在底车系统后部承重横孔方向前移时,则后部承重横垫梁的压力就线性地垫梁之上的主机承重后支腿的承重体系。如图34减小,此时支腿液压缸的油压也就会自动地随之相所示,Q;为主机系统承重后支腿传给底车系统后部应减小。否则,从理论上讲,底车反而会发生向前承重横垫梁的主机部分自重与天车吊重的合力;Dn端倾翻的趋势。只有后倾和前倾都不会发生,底车为Q;作用点与后悬挂中心之间的距离;d;为前悬挂车体才能达到真正的纵向稳定性。中心各单元液压缸压力与后悬挂中心的距离;pi(i底车承重自助均衡系统的结构组成如图33所=l,2,3)为3对支腿液压缸的压力;D.为pi与后悬示,主要包括:液压缸式支腿1、2、3,液电程序控制挂中心之间的距离。14铁道建筒技术RA『LMy”CO ̄S丁开UCO~丁£.Cf_f ̄0£-OGy2D75r9J万方数据・特约稿・后悬挂中心是底车系统向后倾翻的理论倾翻点,绕该点的倾覆力矩M。=Q。・仇,绕该点的稳定∑力矩』I钆=(pf×∑di)+(pi+Di)。若要保证机组在作业过程中不向后发生倾翻,≥则必须保证:M。/肘。K(K为大于1的安全系数),∑即在架梁作业全过程都必须有(P,×∑di)+(Pi×Di)>Q。×Do成立。根据前面所述,架首孔梁时的作业步骤第2步至第3步的动作都会引起以上所述各力:Q。、p,、p,、p.一p,等数值的变化。因此,通过调整液压缸式支腿的液压缸压力p。~p,的大小,可以保证在架梁作≥业全过程M。/M。K公式总是成立。缸式支腿\一困口r混凝土粱■■■■UIII■■^III■■U-II-IIIIIryljp-iIp.Jjl肛UmlD.门-,㈩(,妒,)(,妒。)图34架桥机架梁受力体系示意图根据以上逻辑编写的控制程序流程图如图35所示。液电程序控制系统的构成及工作流程如图36所示。将编制完成的程序输入微电控制箱(基于智—能化的总线控制系统CANBuS),由微电控制箱执行架梁过程的控制程序,并将实时指令传输给液压变量泵站。变量泵站按微电控制箱的指令打开比例电磁阀,将液压油按指定的流量送人各支腿液压缸中。安装在液压缸阀块上的压力传感元件会将实时压力信息传回微电控制箱,通过控制程序计算之后再将新的指令传输给液压变量泵站,变量泵站再根据微电控制箱的实时指令调整比例电磁阀送……人各支腿液压缸中的液压油流量如此周而复始,直到架梁作业结束。图35控制程序框图架梁过程I.1微电控制箱(带可编程1.1变量泵站1.1各油缸式支腿之油缸’’计算机程序I。l逻辑控制器、放大器等)ll(带比例电磁阀)ll(带传感器)图36液电程序控制系统的构成及工作流程图4.3.2.3承重自动均衡系统的实施方法根据前面所述架首孑L梁的第2步,如图32和图33所示,底车系统喂梁到位后,在主机承重后支腿落下,并支撑在底车系统后部横垫梁上但尚未受力之前,启动液电程序控制系统4,即在司机室内操作台“”上,先后按下该控制系统4的总按钮和开始按钮,系统4的程序启动,直至首孑L混凝土梁落下在桥孑L上,之后,解除主机后支腿与底车横垫梁之间的连接,后支腿缩起,架桥机组成为后悬臂状态。确认架桥机组已成为后悬臂状态后,按下液电程序控制系统4的“”结束按钮,则各液压缸式支腿1~3自动缩回;待到液压缸完全缩回后,将控制系统4的总开关关闭。这时底车系统即可退出,回后方准备运梁。在架梁全过程中,控制系统4一直保持运行状态,其时程跨度包括:(1)主机承重后支腿支立在底车系统后部承重横垫梁上并施行连接。(2)主机的中间移动式支腿由桥台上前移到前方墩上支立,前后天车从运梁车上起吊混凝土梁。(3)前后天车抬吊着混凝土梁由后向前移动全过程。(4)混凝土梁吊运到位,在首孑L桥跨上落梁到铁道建筑技术RA『LWAyC0~S丁只UC丁『0~丁E-cH~0LDGy’205r9J15万方数据・特约稿・位全过程。(5)落梁到位后,移动式支腿又从前方墩退回到桥台胸墙顶部支立,主机承重后,拆除支腿与底车系统后部承重横梁之间的连接,承重后支腿缩起。综上所述可见,整个架首孔梁过程中,在本系统所—配置的3对液压缸式支腿及一套基于现场总线(CANBUS)的液电控制系统的作用下,底车系统能够自动保持其承重的均衡性,保证了底车系统的纵向稳定性。但应指出,本系统所采用的底车系统后部的3对液压缸式支腿的安全作用条件是其支撑地面应是坚实的路基,而不可支在已架混凝土梁桥面上,否则会有压裂已架混凝土梁的危险。当首孔梁架设完毕进入第二孔梁的架设程序时,就无需再使用这个自动均衡系统,而是利用已架梁前端的吊梁孑L(预制箱梁的额定吊点)用专用锚具将底车前端锚固在已架混凝土梁头上。从而避免造成液压缸支腿压裂已架梁面的危险。4.3.3架第2孔及前方各孔梁时底车的抗后倾技术4.3.3.1技术背景当首孔梁架设完毕,架桥机向前纵移过孔去架第2孔、第3孑L-.・直至末孔梁时,各孔梁的作业工艺相同,如图37所示。‘¨垒善茎蓄1—————鱼量k,_!。Jr图37TTsJ900型架桥机架第2孔及前方各孔梁步骤图将图37与图32对比可知,1TSJ900型架桥机架第2孔及前方各孔梁与架首孔梁两者架梁作业工艺大体相同,所不同的是架首孔梁时运梁车喂梁停靠位置是在桥头路堤之上,架第2孑L及前方各孔梁时运梁车喂梁位置是在已架混凝土梁之上。现在的问题同样是发生在图37所示之步骤3,当前、后吊梁天车同时从运梁车上起吊混凝土梁时,运梁车后部横垫梁上的承载重量达到最大值,而运梁车前端作为所装载混凝土梁的前支点的横垫梁上的承压力却被前吊梁小车传递到桥机主梁上了,此时运梁车前端横垫梁变为零载荷。于是,蜈蚣形轮胎式运梁车即时的荷重状态是前轻后重,极不平衡,车16辆将会发生绕后端向后倾翻的状况,此即为此前所述之车辆失去了纵向稳定性。且前又述及,底车承重自动均衡系统所采用的底车后部3对油缸式支腿是不可以支承在已架梁梁面上的,以避免有压裂梁面的危险。所以就研究采用了将底车前端锚固在已架箱梁的吊梁孔中,达到抵抗底车后倾的目的。4.3.3.2底车抗后倾技术的工作原理所述架桥机组轮胎式底车亦即运梁车喂架时的抗后倾技术,是用以解决,r11SJ900型架桥机组在架梁过程中底车系统将会发生向后倾翻的问题和保证下车系统的绝对纵稳性。为达到上述目的,所采用的技术方案是将轮胎式底车车体前端与已架混凝土梁梁头之间用特制的装拆式锚栓机构联结起来,使喂梁开始时发生在车体上的后倾力让已架混凝土梁的自重来抵抗。也即是将轮胎式运梁车的车体前端锚固在已架混凝土梁梁头上。锚固机构系科学地利用已架梁原有的吊梁孔达到装拆式锚固的目的。具体技术措施是设计制造2套装拆式锚栓机构分别铰接于运梁车车体主梁前端两侧,使装拆式锚栓机构与车体主梁铰接的所在位置能够在运梁车喂梁对位停车后正好与已架混凝土梁头上原有的吊梁孑L对齐,然后将锚杆穿入吊梁孑L,拧上锚杆螺母即可。锚栓机构主要由锚链、锚杆、上卸扣、下卸扣、托座、凸面和凹面垫圈及锚杆螺母组成,其总体上仍属于柔性锚链体系,并非刚性锚杆构造,因此其只会产生拉力,不会产生弯矩,力学行为良好而安全。4.3.3.3底车抗后倾技术的实施方法该下车系统的抗后倾技术的具体实施方式包括以下几个步骤。首先设业已设计、制造、安装轮胎式底车车体前端的拆装式锚栓机构如图38所示。铁道建篱技术99.M放大A向图38底车前端锚固机构组成图∞RAlUAYcoNSTRucTloNTEcHNoLoGY2015191万方数据・特约稿・图38主视图所示为架桥机组处于喂梁到位的状态。由运梁车前端的M放大图及其A向视图可见底车车体前端两侧的拆装式锚栓机构主要组成包括:锚链1、锚杆2、托座3、凹面垫圈4、凸面垫圈—5、锚杆螺母6、锚链上卸扣1一l、锚链下卸扣12。锚杆2上端锻制成蛇头眼板,以通过下卸扣1—2与锚链l的下端连接起来;锚杆2下端带螺纹,将托座3套进锚杆2,加上凹面垫圈4和凸面垫圈5之后拧紧锚杆螺母6,就组成了一个特制的拆装式锚栓机构。在底车车架主梁9前端两侧各焊接一块带孔耳——板91,以通过上卸扣11把锚链1上端连接起来。则拆装式锚栓机构就如此安装在车架主梁9前端两侧。关系到该研制项目所提出的新型架梁工艺的成败。所采用的底车纵向稳定性的保证技术,即架首孔梁时所采用的底车承重自动均衡技术来代替过去的对底车施行土工强迫锚固的落后方法;架第2孔及前方各孔梁时所采用的底车抗后倾技术,体现了用简单方便的方法解决重大复杂问题的良好效果。实践证明它们所产生的社会经济效益明显,技术方案和技术措施正确和精确,它们能够大幅度提高高速铁路和海湾大桥等的架梁施工技术水平,其安全性、先进性、实用性和经济性优越,具有良好的推广应用价值。(未完待续)参考文献接着实施轮胎式底车车架主梁9前端与已架混[1]黄耀怡,余春红・略沦我国大吨位架桥机从创始到世界……凝土竺置竺固然。…,Ⅲ淼搿1k嚣虢k赫首先,根据前面所述架梁步骤之第2步,如图“’‘。。;芜三兹:;)[J]:磊毳筑蒜:磊j;::):::。1;_38主视图所示,当运梁车喂梁对位时,应使运梁车[3]黄耀怡,余春红.纵论我国大吨位提梁机从世界首创到(也是架桥机组的底车)前端的主梁9两侧安装拆—持续领先之路[J].铁道建筑技术,2015(6):117.装式锚栓机构的位置正好与已架梁8的前头两侧吊[4]王金祥,黄耀怡,董秀林,等高速铁路桥梁运架设备梁孔7对齐,如图38中M放大图及其A向视图—嘲型运梁车硎[J].锔颤燃,嬲(6):610.所示。[5]黄耀怡,王金祥,董秀林,等.7I脚型轮胎式运梁车接着,将拆装式锚栓机构的锚杆2穿进已架梁整车稳定性设计[J].铁道标准设计,200r7(9):12一14・8的两侧吊梁孑L—7,用下卸扣12将锚杆2上端与[6]黄耀怡,李彬,刘培勇,等・11Lc660型轮胎式运梁车架已安装好在车架主梁9前端两侧的锚链l下端连接竺竺登壬况刚、弹譬混合支承连续梁的弯矩计算[1]・’起来再把已穿进吊梁孑L7内的锚杆2下端套进托…裟关篓甚裂:毛1600型跨双幅轮胎式座3、凹面垫圈4、凸面垫圈5及锚杆螺母6,即完成运梁车技术研究[J].今日工程机械,2008(6):1僻一113.了整个锚固作业。这样,当主机系统的吊梁天车从[8]张志华.DF450型架桥机及DcY型运梁车[J].工程运梁车上起吊混凝土梁时,就不会发生运梁车向后—机械,2001(4):68.倾翻的现象,且确保了运梁车亦即架桥机组底车的[9]刘培勇,江创华,刘刚,等.900t隧道型运梁车[J].工纵向稳定性。—程机械,2011(11):46.4.3.3.4小结[10]黄耀怡・铁路客运专线桥梁铺架技术研究与成套设备TTSJ900型隧道内外通用架桥机组的研制与应—研制[J].铁道标准设计,2005(5):3235・要墨翌竺婴2竺苎套苎查竺翌计型项隳苎n¨嚣芋篓瓣要怒篙警雄惴赫满获得成功,该机组在合福高铁施工中已胜利完成[12];磊石』刘菇;:;坤,;.妻于我国高铁运架一体机第5标段14座桥梁总共500多孔箱梁的架设任务。的设计与应用[J].铁道建筑技术,2014(2):6一19.而本文所介绍的该机组架梁过程底车的纵向稳定[13]黄耀怡.-I璐J900型隧道内外通用架桥机组底车承重性控制是该研制项目的一个重大关键技术问题,它—自动均衡系统[J].工程机械,2015(5):16.万方数据
您可能关注的文档
- 阿尔及利亚175铁路项目深路堑边坡研究.pdf
- 按法国规范的泥灰岩鉴别及其在路基工程中应用.pdf
- 暗挖车站洞桩法下穿桥梁关键措施研究.pdf
- 阿尔及利亚东西高速公路M3标段边坡系统防护研究.pdf
- 饱水粉砂地层盾构穿越既有建筑群施工技术探讨.pdf
- 贝雷片联合三角悬挑支架在软基处悬臂梁施工中的应用.pdf
- 边坡加筋技术在十堰北站场坪高填方边坡工程中的应用.pdf
- 薄壁筒桩复合地基在铁路深厚软基加固中的试验研究.pdf
- 滨北线松花江公铁两用桥改建工程总体设计.pdf
- 波形钢腹板体外预应力箱梁在新密溱水路大桥中的应用.pdf
- 步履式顶推钢箱梁高位落梁技术研究.pdf
- 藏区高速复杂地质条件下古堰塞湖沉积物特征研究.pdf
- 草原地区铁路建设对环境的影响探析.pdf
- 敞开式 TBM 厚板窄间隙 MAG 焊工艺研究.pdf
- 敞开式钢管-混凝土桁架组合梁施工技术.pdf
- 敞开式TBM在软弱围岩中掘进反力保障措施.pdf
- 超大板式转换层分层施工技术.pdf
- 超大截面劲性砼结构施工技术.pdf
- 超大超重地下连续墙钢筋笼吊装设计与验算.pdf
- 超大直径泥水盾构机始发技术.pdf

- 村长
- 该用户很懒,什么也没介绍