- 文档大小:2.39 MB
- 文档格式:pdf
- 约 5页
- 2021-11-23 发布
- 举报
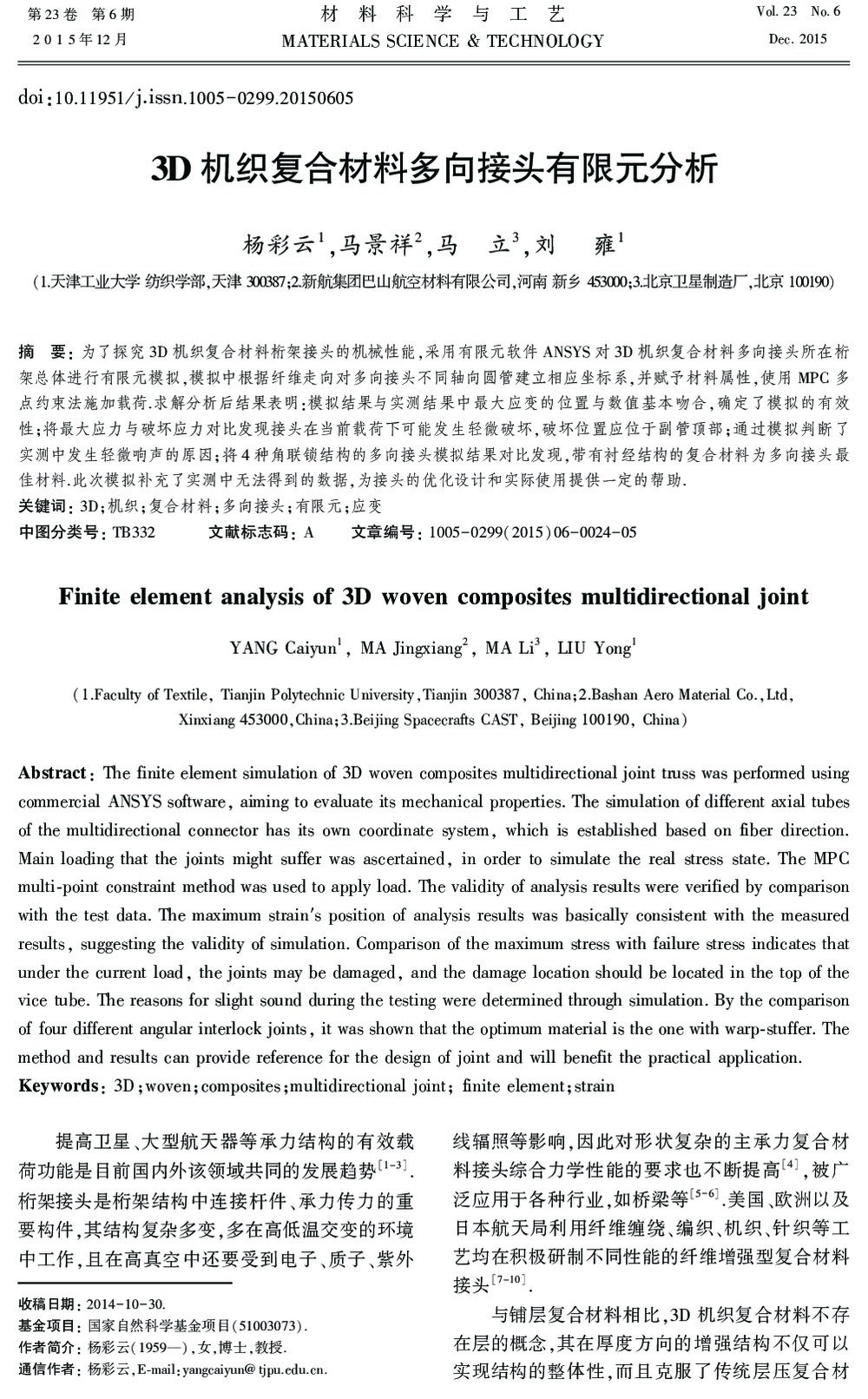
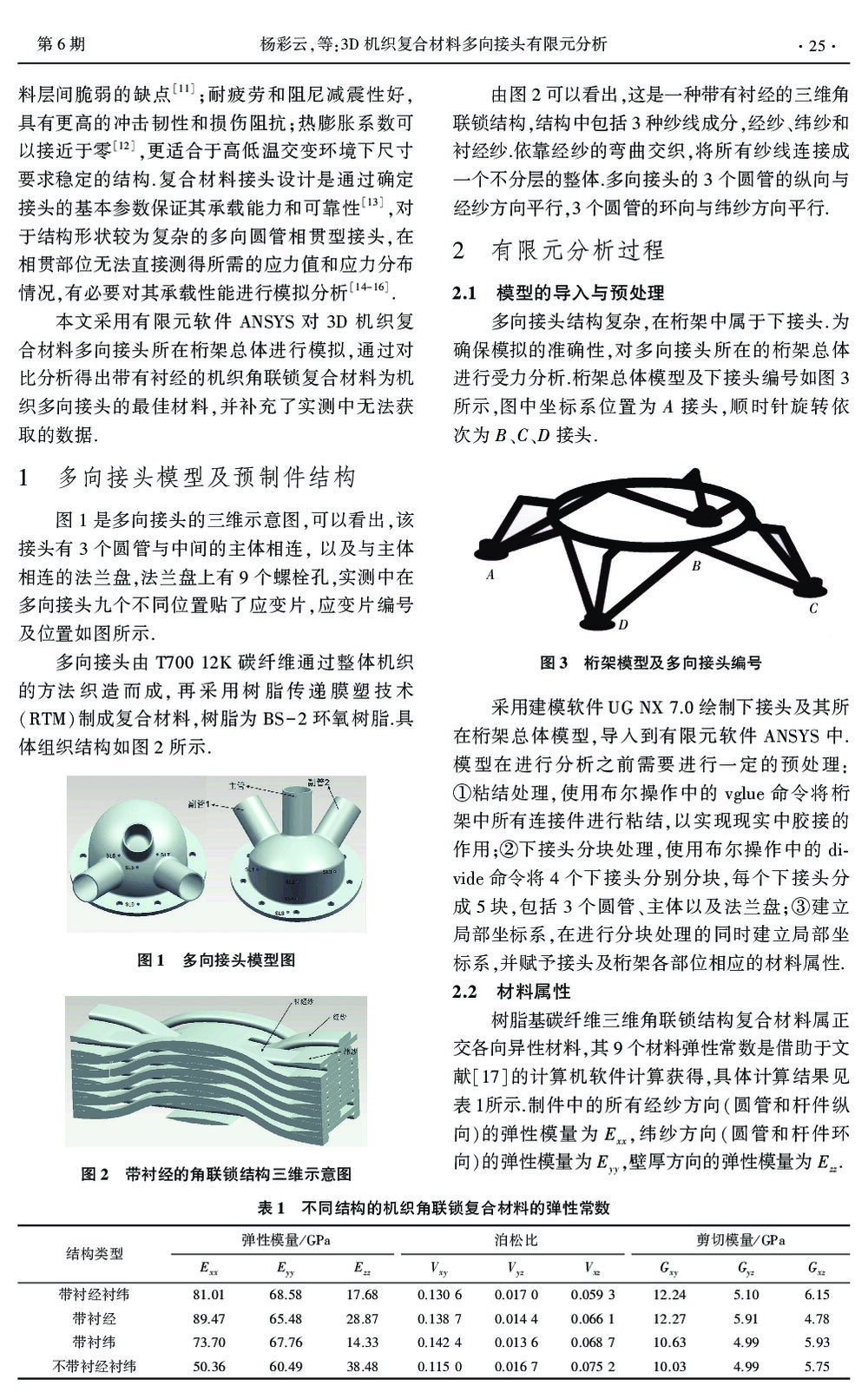
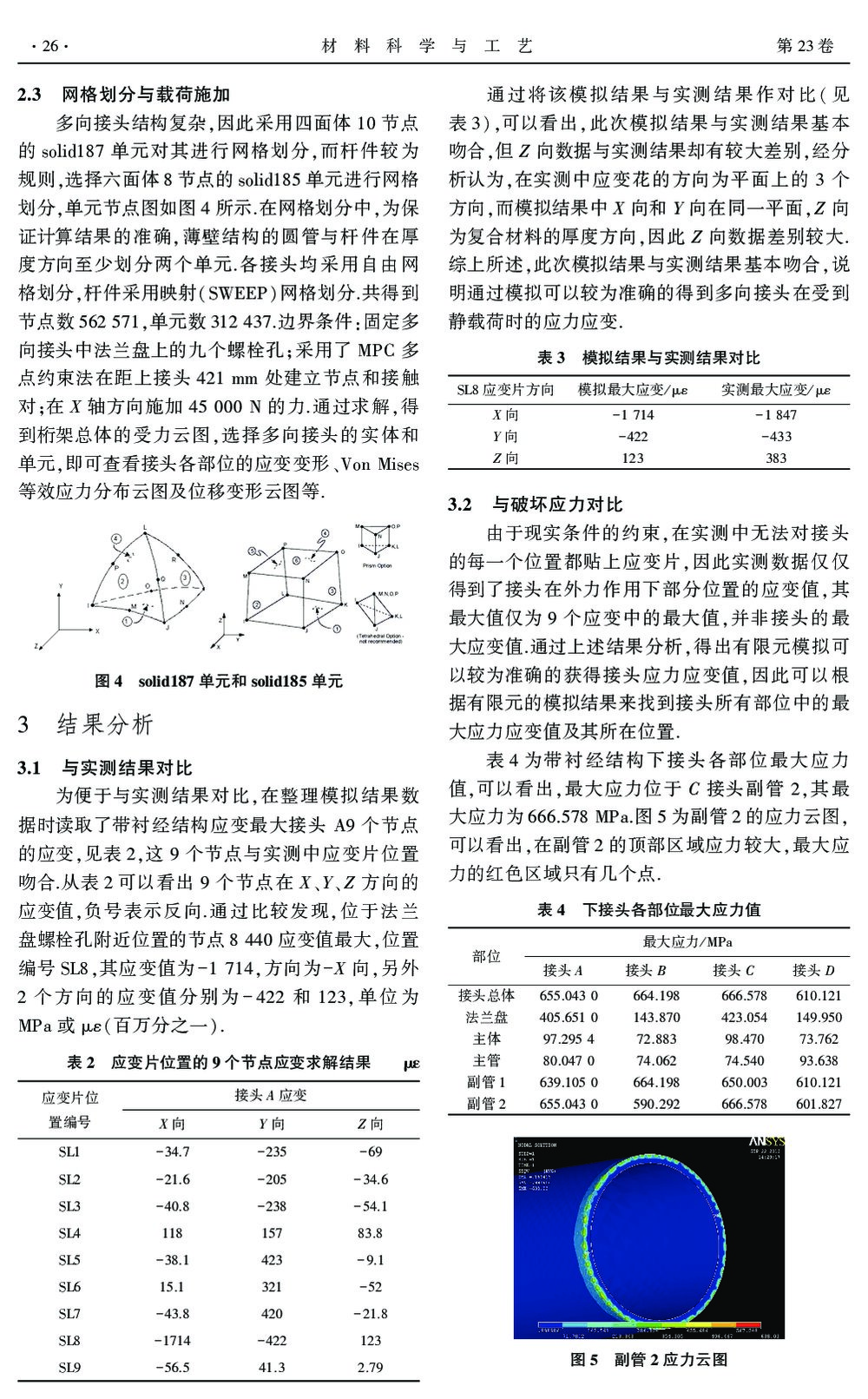
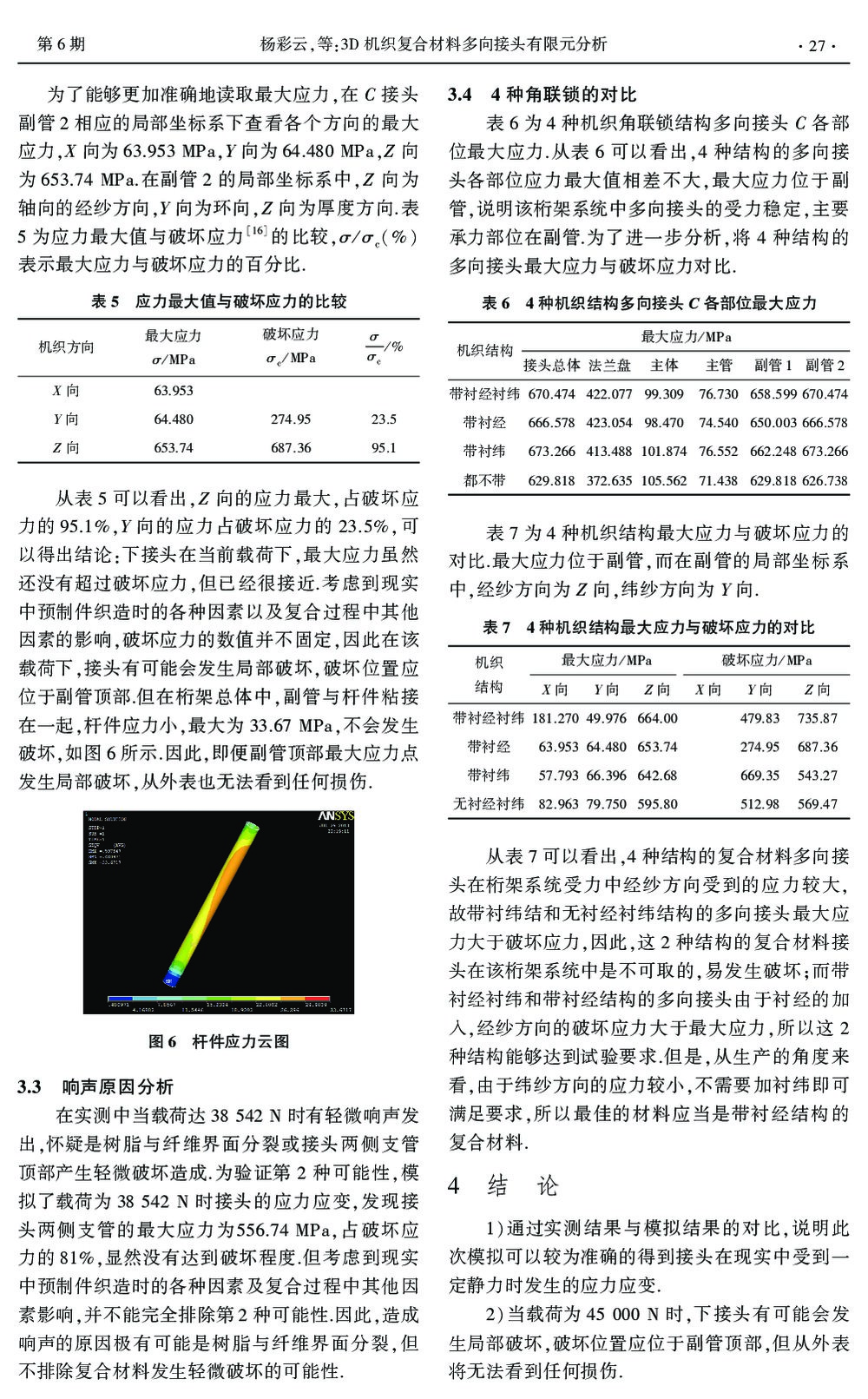
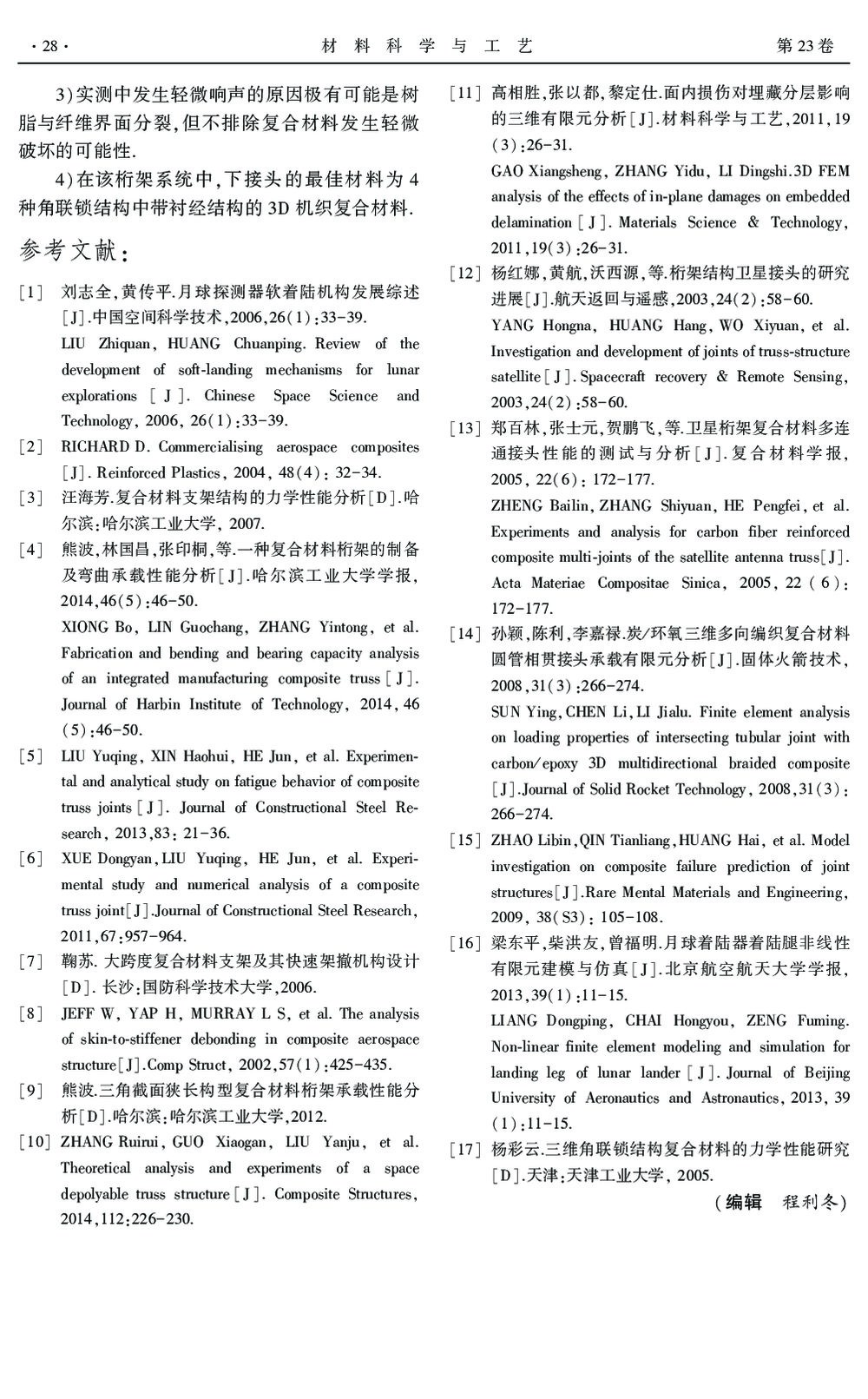
已阅读完毕,您还可以下载文档进行保存
- 1、本文档共5页,内容下载后可编辑。
- 2、本文档内容版权归属内容提供方,所产生的收益全部归内容提供方所有。如果您对本文有版权争议,可选择认领。
- 3、本文档由用户上传,本站不保证质量和数量令人满意,可能有诸多瑕疵,付费之前,请仔细先通过免费阅读内容等途径辨别内容交易风险。如存在严重挂羊头卖狗肉之情形,可联系本站下载客服投诉处理。
第23卷第6期2015年12月材料科学与工艺MATERIALSSCIENCE&TECHNOLOGYllVol23lll6Dec.2015doi:10.11951/j.issn.1005-0299.201506053D机织复合材料多向接头有限元分析杨彩云1,马景祥2,马立3,刘雍1(1.天津工业大学纺织学部,天津300387;2.新航集团巴山航空材料有限公司,河南新乡453000;3.北京卫星制造厂,北京100190)摘要:为了探究3D机织复合材料桁架接头的机械性能,采用有限元软件ANSYS对3D机织复合材料多向接头所在桁架总体进行有限元模拟,模拟中根据纤维走向对多向接头不同轴向圆管建立相应坐标系,并赋予材料属性,使用MPC多点约束法施加载荷.求解分析后结果表明:模拟结果与实测结果中最大应变的位置与数值基本吻合,确定了模拟的有效性;将最大应力与破坏应力对比发现接头在当前载荷下可能发生轻微破坏,破坏位置应位于副管顶部;通过模拟判断了实测中发生轻微响声的原因;将4种角联锁结构的多向接头模拟结果对比发现,带有衬经结构的复合材料为多向接头最佳材料.此次模拟补充了实测中无法得到的数据,为接头的优化设计和实际使用提供一定的帮助.关键词:3D;机织;复合材料;多向接头;有限元;应变中图分类号:TB332文献标志码:A文章编号:1005-0299(2015)06-0024-05Finiteelementanalysisof3DwovencompositesmultidirectionaljointYANGCaiyun1,MAJingxiang2,MALi3,LIUYong1(1.FacultyofTextile,TianjinPolytechnicUniversity,Tianjin300387,China;2.BashanAeroMaterialCo.,Ltd,Xinxiang453000,China;3.BeijingSpacecraftsCAST,Beijing100190,China)Abstract:Thefiniteelementsimulationof3DwovencompositesmultidirectionaljointtrusswasperformedusingcommercialANSYSsoftware,aimingtoevaluateitsmechanicalproperties.Thesimulationofdifferentaxialtubesofthemultidirectionalconnectorhasitsowncoordinatesystem,whichisestablishedbasedonfiberdirection.Mainloadingthatthejointsmightsufferwasascertained,inordertosimulatetherealstressstate.TheMPC⁃multipointconstraintmethodwasusedtoapplyload.Thevalidityofanalysisresultswereverifiedbycomparisonwiththetestdata.′Themaximumstrainspositionofanalysisresultswasbasicallyconsistentwiththemeasuredresults,suggestingthevalidityofsimulation.Comparisonofthemaximumstresswithfailurestressindicatesthatunderthecurrentload,thejointsmaybedamaged,andthedamagelocationshouldbelocatedinthetopofthevicetube.Thereasonsforslightsoundduringthetestingweredeterminedthroughsimulation.Bythecomparisonof⁃fourdifferentangularinterlockjoints,itwasshownthattheoptimummaterialistheonewithwarpstuffer.Themethodandresultscanprovidereferenceforthedesignofjointandwillbenefitthepracticalapplication.Keywords:3D;woven;composites;multidirectionaljoint;finiteelement;strain收稿日期:2014-10-30.基金项目:国家自然科学基金项目(51003073).作者简介:杨彩云—(1959),女,博士,教授.通信作者:杨彩云⁃,Email:yangcaiyun@tjpu.edu.cn.提高卫星、大型航天器等承力结构的有效载荷功能是目前国内外该领域共同的发展趋势[1-3].桁架接头是桁架结构中连接杆件、承力传力的重要构件,其结构复杂多变,多在高低温交变的环境中工作,且在高真空中还要受到电子、质子、紫外线辐照等影响,因此对形状复杂的主承力复合材料接头综合力学性能的要求也不断提高[4],被广泛应用于各种行业,如桥梁等[5-6].美国、欧洲以及日本航天局利用纤维缠绕、编织、机织、针织等工艺均在积极研制不同性能的纤维增强型复合材料接头[7-10].与铺层复合材料相比,3D机织复合材料不存在层的概念,其在厚度方向的增强结构不仅可以实现结构的整体性,而且克服了传统层压复合材料层间脆弱的缺点[11];耐疲劳和阻尼减震性好,具有更高的冲击韧性和损伤阻抗;热膨胀系数可以接近于零[12],更适合于高低温交变环境下尺寸要求稳定的结构.复合材料接头设计是通过确定接头的基本参数保证其承载能力和可靠性[13],对于结构形状较为复杂的多向圆管相贯型接头,在相贯部位无法直接测得所需的应力值和应力分布情况,有必要对其承载性能进行模拟分析[14-16].本文采用有限元软件ANSYS对3D机织复合材料多向接头所在桁架总体进行模拟,通过对比分析得出带有衬经的机织角联锁复合材料为机织多向接头的最佳材料,并补充了实测中无法获取的数据.1多向接头模型及预制件结构图1是多向接头的三维示意图,可以看出,该接头有3个圆管与中间的主体相连,以及与主体相连的法兰盘,法兰盘上有9个螺栓孔,实测中在多向接头九个不同位置贴了应变片,应变片编号及位置如图所示.多向接头由T70012K碳纤维通过整体机织的方法织造而成,再采用树脂传递膜塑技术(RTM)制成复合材料,树脂为BS-2环氧树脂.具体组织结构如图2所示.图1多向接头模型图图2带衬经的角联锁结构三维示意图由图2可以看出,这是一种带有衬经的三维角联锁结构,结构中包括3种纱线成分,经纱、纬纱和衬经纱.依靠经纱的弯曲交织,将所有纱线连接成一个不分层的整体.多向接头的3个圆管的纵向与经纱方向平行,3个圆管的环向与纬纱方向平行.2有限元分析过程2.1模型的导入与预处理多向接头结构复杂,在桁架中属于下接头.为确保模拟的准确性,对多向接头所在的桁架总体进行受力分析.桁架总体模型及下接头编号如图3所示,图中坐标系位置为A接头,顺时针旋转依次为B、C、D接头.ABCD图3桁架模型及多向接头编号采用建模软件UGNX7.0绘制下接头及其所在桁架总体模型,导入到有限元软件ANSYS中.模型在进行分析之前需要进行一定的预处理:①粘结处理,使用布尔操作中的vglue命令将桁架中所有连接件进行粘结,以实现现实中胶接的作用②;下接头分块处理,使用布尔操作中的⁃divide命令将4个下接头分别分块,每个下接头分成5块,包括3个圆管、主体以及法兰盘③;建立局部坐标系,在进行分块处理的同时建立局部坐标系,并赋予接头及桁架各部位相应的材料属性.2.2材料属性树脂基碳纤维三维角联锁结构复合材料属正交各向异性材料,其9个材料弹性常数是借助于文献[17]的计算机软件计算获得,具体计算结果见表1所示.制件中的所有经纱方向(圆管和杆件纵向)的弹性模量为Exx,纬纱方向(圆管和杆件环向)的弹性模量为Eyy,壁厚方向的弹性模量为Ezz.表1不同结构的机织角联锁复合材料的弹性常数结构类型弹性模量/GPa泊松比剪切模量/GPaExxEyyEzzVxyVyzVxzGxyGyzGxz带衬经衬纬81.0168.5817.680.13060.01700.059312.245.106.15带衬经89.4765.4828.870.13870.01440.066112.275.914.78带衬纬73.7067.7614.330.14240.01360.068710.634.995.93不带衬经衬纬50.3660.4938.480.11500.01670.075210.034.995.75·52·第6期杨彩云,等:3D机织复合材料多向接头有限元分析2.3网格划分与载荷施加多向接头结构复杂,因此采用四面体10节点的solid187单元对其进行网格划分,而杆件较为规则,选择六面体8节点的solid185单元进行网格划分,单元节点图如图4所示.在网格划分中,为保证计算结果的准确,薄壁结构的圆管与杆件在厚度方向至少划分两个单元.各接头均采用自由网格划分,杆件采用映射(SWEEP)网格划分.共得到节点数562571,单元数312437.边界条件:固定多向接头中法兰盘上的九个螺栓孔;采用了MPC多点约束法在距上接头421mm处建立节点和接触对;在X轴方向施加45000N的力.通过求解,得到桁架总体的受力云图,选择多向接头的实体和单元,即可查看接头各部位的应变变形、VonMises等效应力分布云图及位移变形云图等.图4solid187单元和solid185单元3结果分析3.1与实测结果对比为便于与实测结果对比,在整理模拟结果数据时读取了带衬经结构应变最大接头A9个节点的应变,见表2,这9个节点与实测中应变片位置吻合.从表2可以看出9个节点在X、Y、Z方向的应变值,负号表示反向.通过比较发现,位于法兰盘螺栓孔附近位置的节点8440应变值最大,位置编号SL8,其应变值为-1714,方向为-X向,另外2个方向的应变值分别为-422和123,单位为MPa或με(百万分之一).表2应变片位置的9个节点应变求解结果με应变片位置编号接头A应变X向Y向Z向SL1-34.7-235-69SL2-21.6-205-34.6SL3-40.8-238-54.1SL411815783.8SL5-38.1423-9.1SL615.1321-52SL7-43.8420-21.8SL8-1714-422123SL9-56.541.32.79通过将该模拟结果与实测结果作对比(见表3),可以看出,此次模拟结果与实测结果基本吻合,但Z向数据与实测结果却有较大差别,经分析认为,在实测中应变花的方向为平面上的3个方向,而模拟结果中X向和Y向在同一平面,Z向为复合材料的厚度方向,因此Z向数据差别较大.综上所述,此次模拟结果与实测结果基本吻合,说明通过模拟可以较为准确的得到多向接头在受到静载荷时的应力应变.表3模拟结果与实测结果对比SL8应变片方向模拟最大应变/με实测最大应变/μεX向-1714-1847Y向-422-433Z向1233833.2与破坏应力对比由于现实条件的约束,在实测中无法对接头的每一个位置都贴上应变片,因此实测数据仅仅得到了接头在外力作用下部分位置的应变值,其最大值仅为9个应变中的最大值,并非接头的最大应变值.通过上述结果分析,得出有限元模拟可以较为准确的获得接头应力应变值,因此可以根据有限元的模拟结果来找到接头所有部位中的最大应力应变值及其所在位置.表4为带衬经结构下接头各部位最大应力值,可以看出,最大应力位于C接头副管2,其最大应力为666.578MPa.图5为副管2的应力云图,可以看出,在副管2的顶部区域应力较大,最大应力的红色区域只有几个点.表4下接头各部位最大应力值部位最大应力/MPa接头A接头B接头C接头D接头总体655.0430664.198666.578610.121法兰盘405.6510143.870423.054149.950主体97.295472.88398.47073.762主管80.047074.06274.54093.638副管1639.1050664.198650.003610.121副管2655.0430590.292666.578601.827图5副管2应力云图·62·材料科学与工艺第23卷为了能够更加准确地读取最大应力,在C接头副管2相应的局部坐标系下查看各个方向的最大应力,X向为63.953MPa,Y向为64.480MPa,Z向为653.74MPa.在副管2的局部坐标系中,Z向为轴向的经纱方向,Y向为环向,Z向为厚度方向.表5为应力最大值与破坏应力[16]的比较,σ/σc(%)表示最大应力与破坏应力的百分比.表5应力最大值与破坏应力的比较机织方向最大应力σ/MPa破坏应力σc/MPaσσc/%X向63.953Y向64.480274.9523.5Z向653.74687.3695.1从表5可以看出,Z向的应力最大,占破坏应力的95.1%,Y向的应力占破坏应力的23.5%,可以得出结论:下接头在当前载荷下,最大应力虽然还没有超过破坏应力,但已经很接近.考虑到现实中预制件织造时的各种因素以及复合过程中其他因素的影响,破坏应力的数值并不固定,因此在该载荷下,接头有可能会发生局部破坏,破坏位置应位于副管顶部.但在桁架总体中,副管与杆件粘接在一起,杆件应力小,最大为33.67MPa,不会发生破坏,如图6所示.因此,即便副管顶部最大应力点发生局部破坏,从外表也无法看到任何损伤.图6杆件应力云图3.3响声原因分析在实测中当载荷达38542N时有轻微响声发出,怀疑是树脂与纤维界面分裂或接头两侧支管顶部产生轻微破坏造成.为验证第2种可能性,模拟了载荷为38542N时接头的应力应变,发现接头两侧支管的最大应力为556.74MPa,占破坏应力的81%,显然没有达到破坏程度.但考虑到现实中预制件织造时的各种因素及复合过程中其他因素影响,并不能完全排除第2种可能性.因此,造成响声的原因极有可能是树脂与纤维界面分裂,但不排除复合材料发生轻微破坏的可能性.3.44种角联锁的对比表6为4种机织角联锁结构多向接头C各部位最大应力.从表6可以看出,4种结构的多向接头各部位应力最大值相差不大,最大应力位于副管,说明该桁架系统中多向接头的受力稳定,主要承力部位在副管.为了进一步分析,将4种结构的多向接头最大应力与破坏应力对比.表64种机织结构多向接头C各部位最大应力机织结构最大应力/MPa接头总体法兰盘主体主管副管1副管2带衬经衬纬670.474422.07799.30976.730658.599670.474带衬经666.578423.05498.47074.540650.003666.578带衬纬673.266413.488101.87476.552662.248673.266都不带629.818372.635105.56271.438629.818626.738表7为4种机织结构最大应力与破坏应力的对比.最大应力位于副管,而在副管的局部坐标系中,经纱方向为Z向,纬纱方向为Y向.表74种机织结构最大应力与破坏应力的对比机织结构最大应力/MPa破坏应力/MPaX向Y向Z向X向Y向Z向带衬经衬纬181.27049.976664.00479.83735.87带衬经63.95364.480653.74274.95687.36带衬纬57.79366.396642.68669.35543.27无衬经衬纬82.96379.750595.80512.98569.47从表7可以看出,4种结构的复合材料多向接头在桁架系统受力中经纱方向受到的应力较大,故带衬纬结和无衬经衬纬结构的多向接头最大应力大于破坏应力,因此,这2种结构的复合材料接头在该桁架系统中是不可取的,易发生破坏;而带衬经衬纬和带衬经结构的多向接头由于衬经的加入,经纱方向的破坏应力大于最大应力,所以这2种结构能够达到试验要求.但是,从生产的角度来看,由于纬纱方向的应力较小,不需要加衬纬即可满足要求,所以最佳的材料应当是带衬经结构的复合材料.4结论1)通过实测结果与模拟结果的对比,说明此次模拟可以较为准确的得到接头在现实中受到一定静力时发生的应力应变.2)当载荷为45000N时,下接头有可能会发生局部破坏,破坏位置应位于副管顶部,但从外表将无法看到任何损伤.·72·第6期杨彩云,等:3D机织复合材料多向接头有限元分析3)实测中发生轻微响声的原因极有可能是树脂与纤维界面分裂,但不排除复合材料发生轻微破坏的可能性.4)在该桁架系统中,下接头的最佳材料为4种角联锁结构中带衬经结构的3D机织复合材料.参考文献:[1]刘志全,黄传平.月球探测器软着陆机构发展综述[J].中国空间科学技术,2006,26(1):33-39.LIUZhiquan,HUANGChuanping.Reviewofthedevelopmentof⁃softlandingmechanismsforlunarexplorations[J].ChineseSpaceScienceandTechnology,2006,26(1):33-39.[2]RICHARDD.Commercialisingaerospacecomposites[J].ReinforcedPlastics,2004,48(4):32-34.[3]汪海芳.复合材料支架结构的力学性能分析[D].哈尔滨:哈尔滨工业大学,2007.[4]熊波,林国昌,张印桐,等.一种复合材料桁架的制备及弯曲承载性能分析[J].哈尔滨工业大学学报,2014,46(5):46-50.XIONGBo,LINGuochang,ZHANGYintong,etal.Fabricationandbendingandbearingcapacityanalysisofanintegratedmanufacturingcompositetruss[J].JournalofHarbinInstituteofTechnology,2014,46(5):46-50.[5]LIUYuqing,XINHaohui,HEJun,etal.⁃Experimentalandanalyticalstudyonfatiguebehaviorofcompositetrussjoints[J].JournalofConstructionalSteel⁃Research,2013,83:21-36.[6]XUEDongyan,LIUYuqing,HEJun,etal.⁃Experimentalstudyandnumericalanalysisofacompositetrussjoint[J].JournalofConstructionalSteelResearch,2011,67:957-964.[7]鞠苏.大跨度复合材料支架及其快速架撤机构设计[D].长沙:国防科学技术大学,2006.[8]JEFFW,YAPH,MURRAYLS,etal.Theanalysisof⁃⁃skintostiffenerdebondingincompositeaerospacestructure[J].CompStruct,2002,57(1):425-435.[9]熊波.三角截面狭长构型复合材料桁架承载性能分析[D].哈尔滨:哈尔滨工业大学,2012.[10]ZHANGRuirui,GUOXiaogan,LIUYanju,etal.Theoreticalanalysisandexperimentsofaspacedepolyabletrussstructure[J].CompositeStructures,2014,112:226-230.[11]高相胜,张以都,黎定仕.面内损伤对埋藏分层影响的三维有限元分析[J].材料科学与工艺,2011,19(3):26-31.GAOXiangsheng,ZHANGYidu,LIDingshi.3DFEM⁃analysisoftheeffectsofinplanedamagesonembeddeddelamination[J].MaterialsScience&Technology,2011,19(3):26-31.[12]杨红娜,黄航,沃西源,等.桁架结构卫星接头的研究进展[J].航天返回与遥感,2003,24(2):58-60.YANGHongna,HUANGHang,WOXiyuan,etal.⁃Investigationanddevelopmentofjointsoftrussstructuresatellite[J].Spacecraftrecovery&RemoteSensing,2003,24(2):58-60.[13]郑百林,张士元,贺鹏飞,等.卫星桁架复合材料多连通接头性能的测试与分析[J].复合材料学报,2005,22(6):172-177.ZHENGBailin,ZHANGShiyuan,HEPengfei,etal.Experimentsandanalysisforcarbonfiberreinforced⁃compositemultijointsofthesatelliteantennatruss[J].ActaMateriaeCompositaeSinica,2005,22(6):172-177.[14]孙颖,陈利,李嘉禄.炭/环氧三维多向编织复合材料圆管相贯接头承载有限元分析[J].固体火箭技术,2008,31(3):266-274.SUNYing,CHENLi,LIJialu.Finiteelementanalysisonloadingpropertiesofintersectingtubularjointwithcarbon/epoxy3Dmultidirectionalbraidedcomposite[J].JournalofSolidRocketTechnology,2008,31(3):266-274.[15]ZHAOLibin,QINTianliang,HUANGHai,etal.Modelinvestigationoncompositefailurepredictionofjointstructures[J].RareMentalMaterialsandEngineering,2009,38(S3):105-108.[16]梁东平,柴洪友,曾福明.月球着陆器着陆腿非线性有限元建模与仿真[J].北京航空航天大学学报,2013,39(1):11-15.LIANGDongping,CHAIHongyou,ZENGFuming.⁃Nonlinearfiniteelementmodelingandsimulationforlandinglegoflunarlander[J].JournalofBeijingUniversityofAeronauticsandAstronautics,2013,39(1):11-15.[17]杨彩云.三维角联锁结构复合材料的力学性能研究[D].天津:天津工业大学,2005.(编辑程利冬)·82·材料科学与工艺第23卷
您可能关注的文档
- “离位”增韧复合材料准静态压入损伤特性研究.pdf
- “神舟七号”飞船舱外航天服防护头盔组件的研制.pdf
- “十二五”复合材料发展重点和方向解读.pdf
- “珠串”堆叠超结构的介孔铁酸锌的制备与表征.pdf
- (001)应变对正交相Ca2 P0.25 Si0.75能带结构及光学性质的影响.pdf
- 0.8设计系数用X80管线钢在近中性pH溶液中的应力腐蚀开裂行为.pdf
- 0.20mm CGO硅钢高温退火Goss晶粒起源及异常长大行为研究.pdf
- 0Cr16Ni5Mo低碳马氏体不锈钢的热变形行为及其热加工图.pdf
- 0Cr17Ni4Cu4Nb钢制螺钉断裂原因分析.pdf
- 1.5MW风机叶片模具加热工艺研究与技术创新.pdf
- 1.5MW风机叶片VARI工艺模拟分析及验证.pdf
- 2.5维机织复合材料低速冲击性能研究.pdf
- 2.25Cr-1Mo钢后续热处理中的磷偏聚行为.pdf
- 2A50锻铝三点弯曲试验与高分辨率CT成像分析.pdf
- 2A12与2A11铝合金超声波焊接工艺与组织研究.pdf
- 2MW风机复合材料叶片材料及工艺研究.pdf
- 3Cr2W8V模具钢激光表面相变硬化层性能的研究.pdf
- 3D打印技术及先进应用研究进展.pdf
- 3D打印技术研究现状和关键技术.pdf
- 5%鱼藤酮悬浮剂的研制.pdf

- 陌南尘
- 该用户很懒,什么也没介绍
相关文档
- “离位”增韧复合材料准静态压入损伤特性研究.pdf2021-11-235页
- “神舟七号”飞船舱外航天服防护头盔组件的研制.pdf2021-11-233页
- “十二五”复合材料发展重点和方向解读.pdf2021-11-232页
- “珠串”堆叠超结构的介孔铁酸锌的制备与表征.pdf2021-11-235页
- (001)应变对正交相Ca2 P0.25 Si0.75能带结构及光学性质的影响.pdf2021-11-236页
- 0.8设计系数用X80管线钢在近中性pH溶液中的应力腐蚀开裂行为.pdf2021-11-237页
- 0.20mm CGO硅钢高温退火Goss晶粒起源及异常长大行为研究.pdf2021-11-237页