- 文档大小:373.8 KB
- 文档格式:pdf
- 约 6页
- 2022-03-24 发布
- 举报
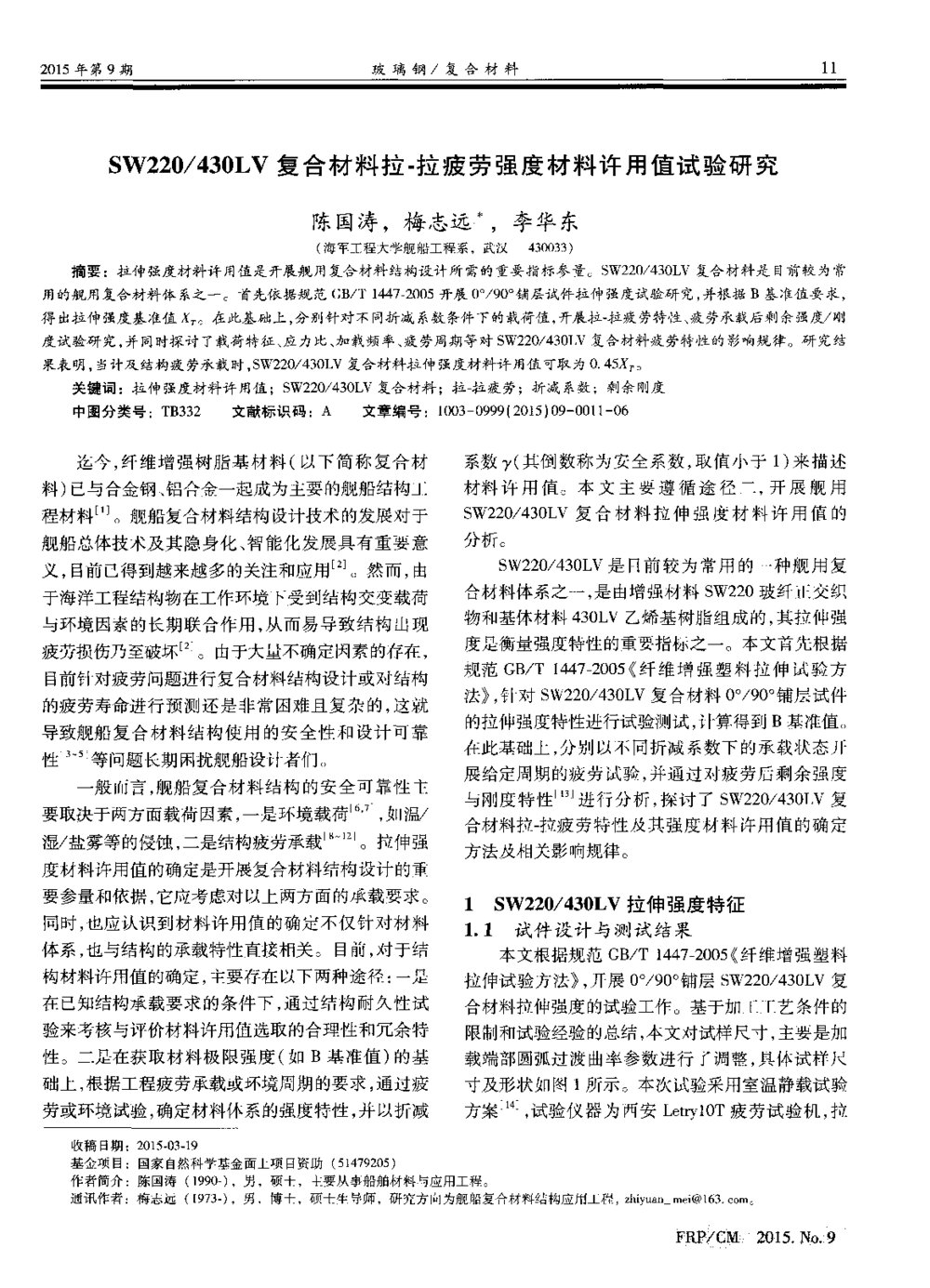
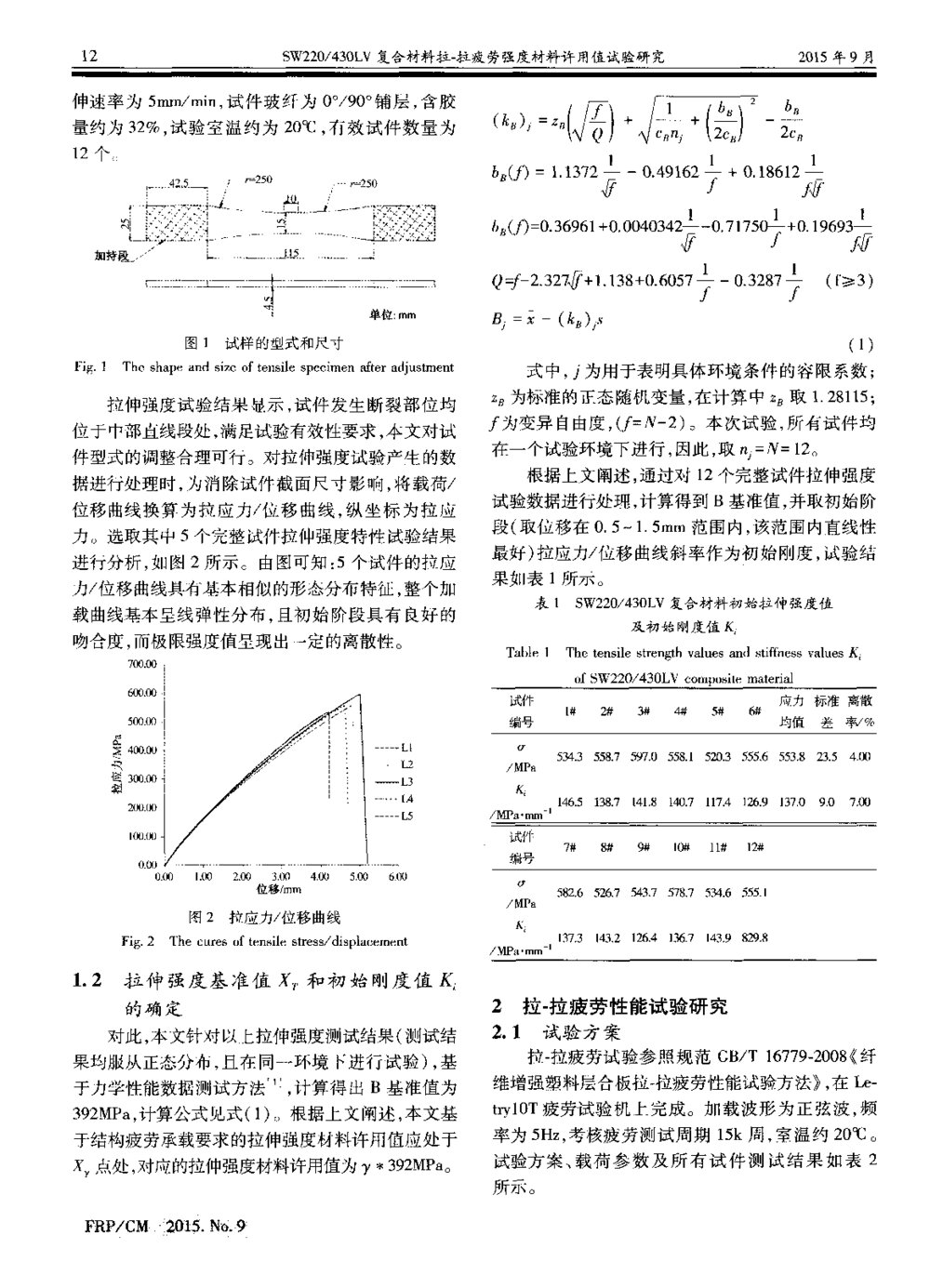
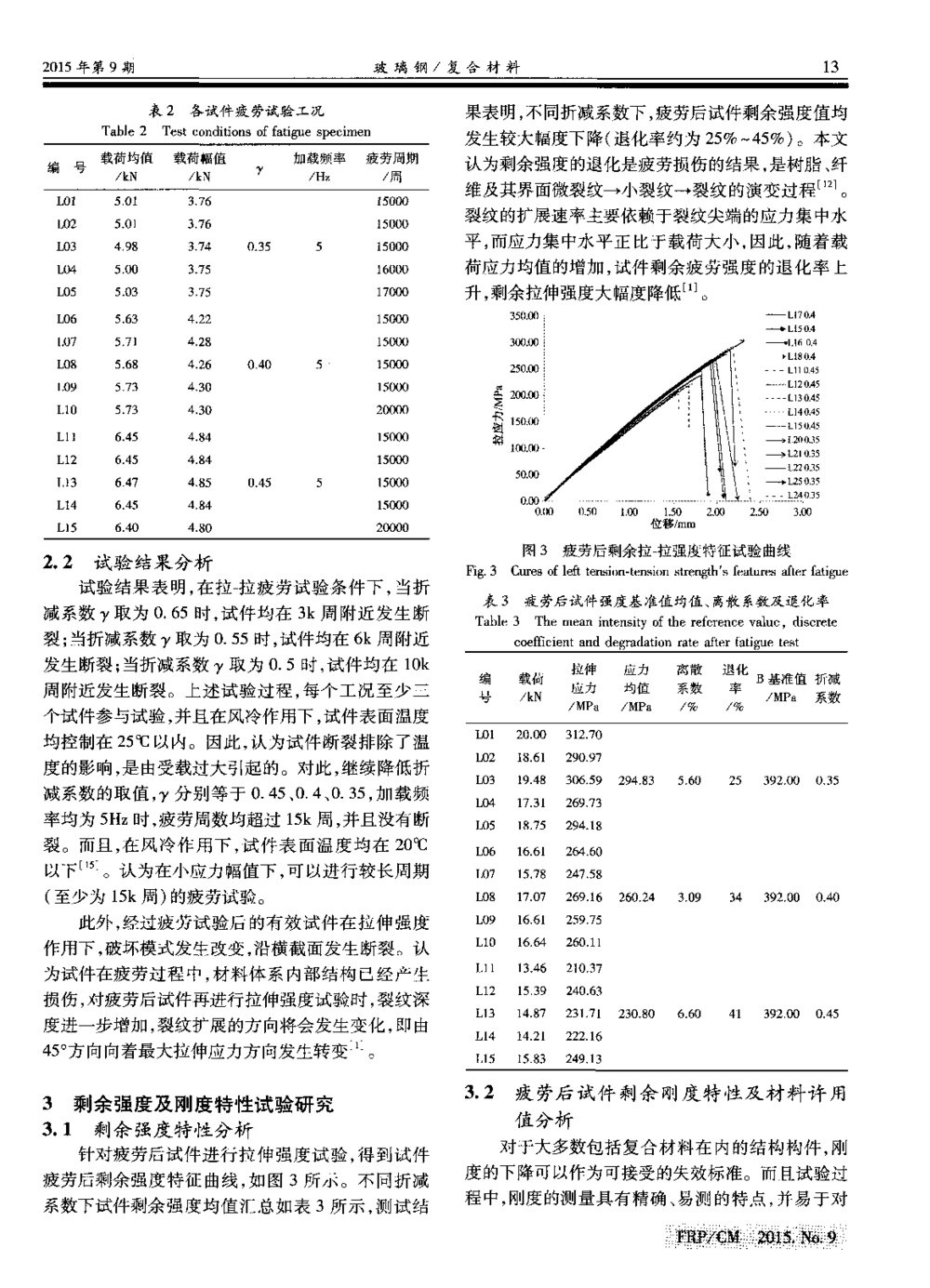
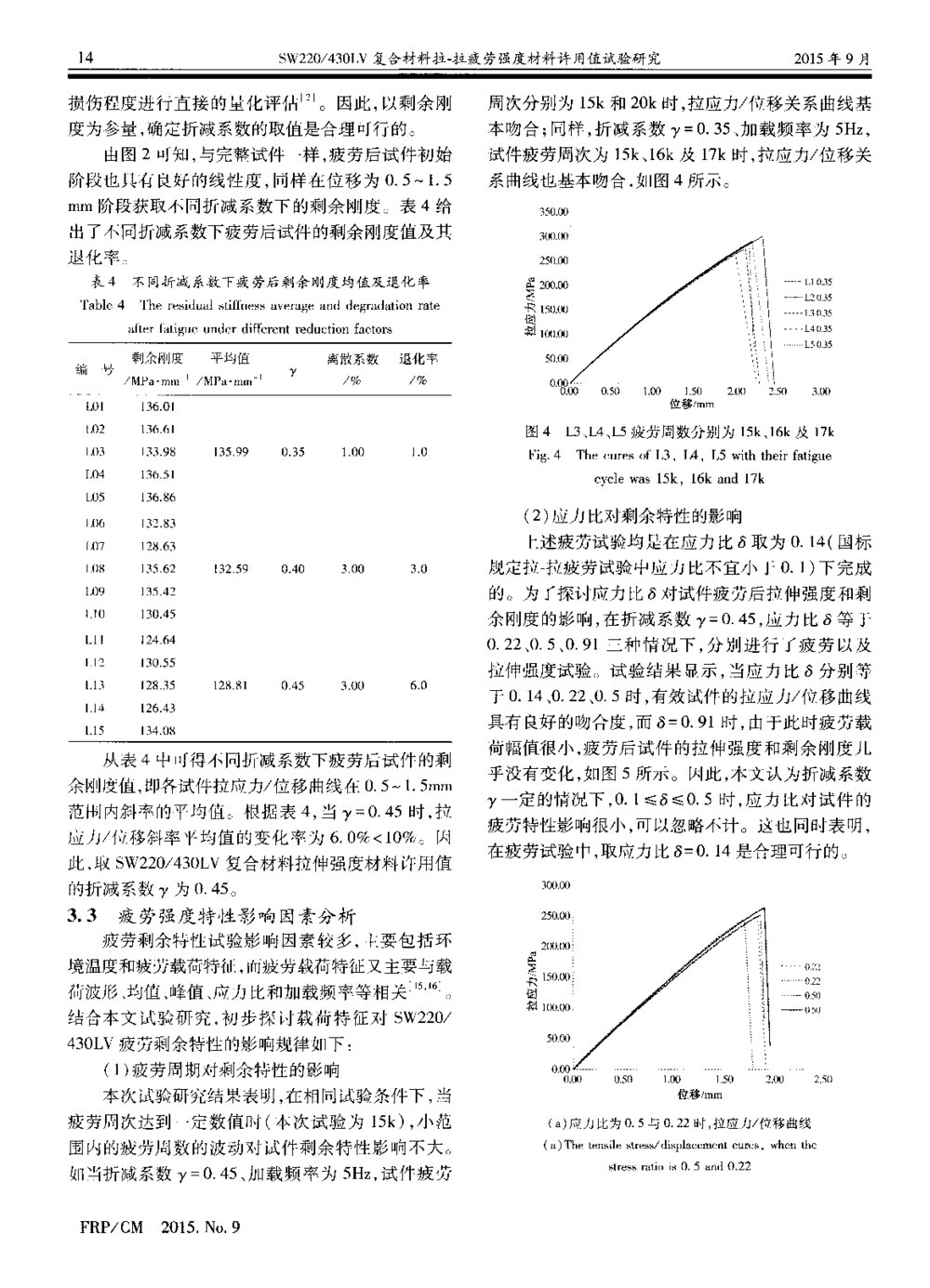
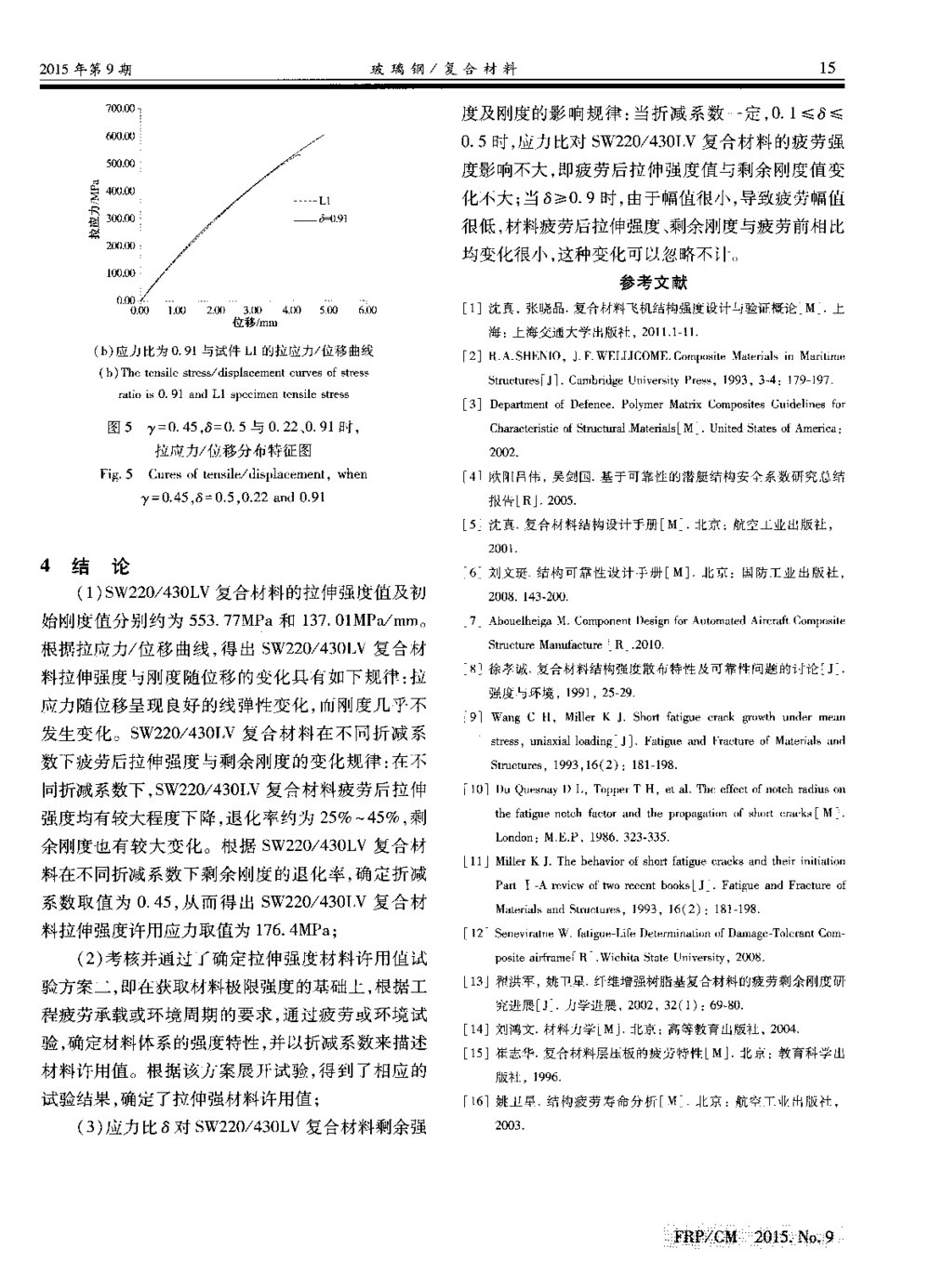
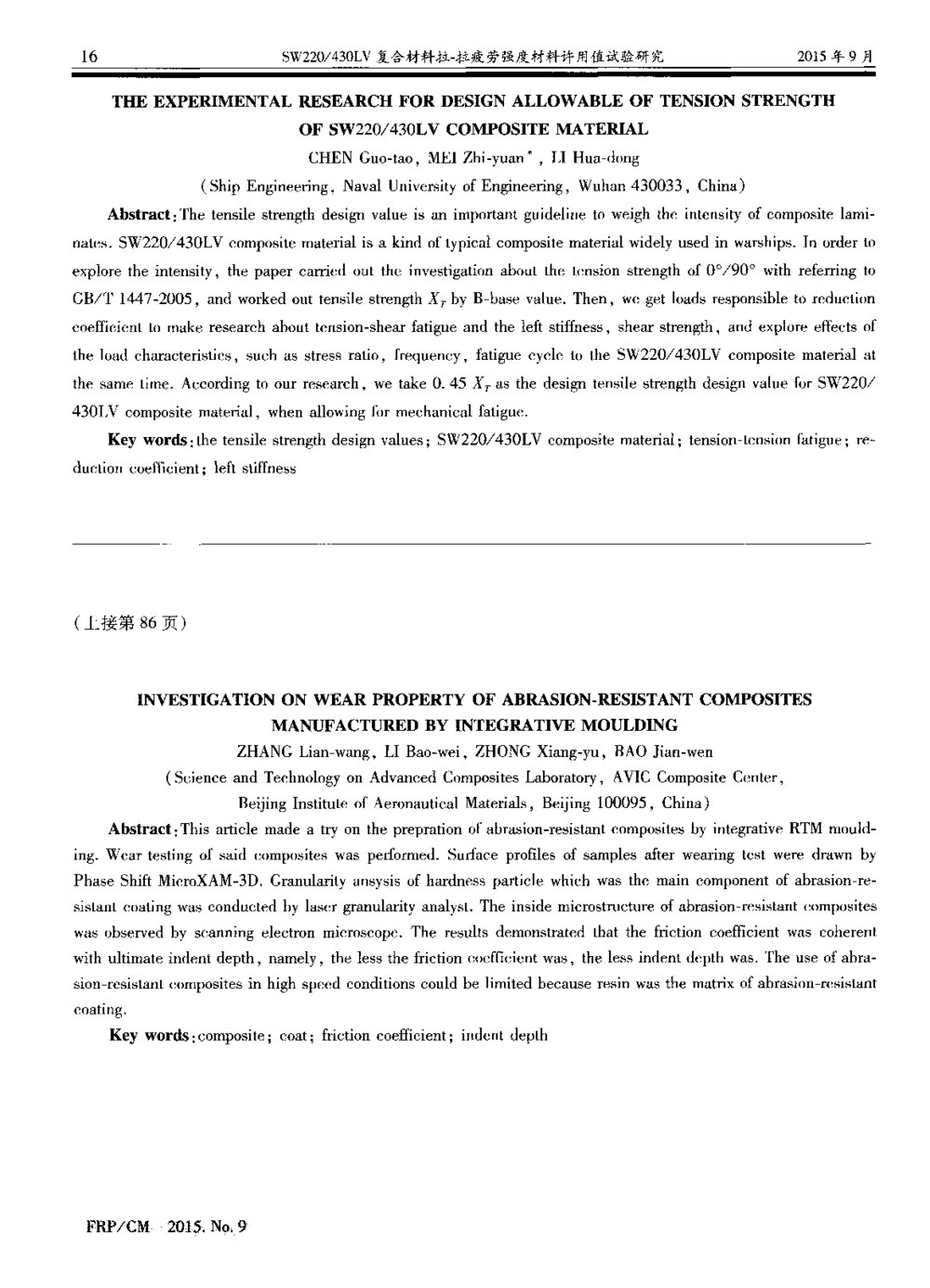
已阅读完毕,您还可以下载文档进行保存
- 1、本文档共6页,内容下载后可编辑。
- 2、本文档内容版权归属内容提供方,所产生的收益全部归内容提供方所有。如果您对本文有版权争议,可选择认领。
- 3、本文档由用户上传,本站不保证质量和数量令人满意,可能有诸多瑕疵,付费之前,请仔细先通过免费阅读内容等途径辨别内容交易风险。如存在严重挂羊头卖狗肉之情形,可联系本站下载客服投诉处理。
2015年第9期玻璃钢/复合材料SW220/430LV复合材料拉-拉疲劳强度材料许用值试验研究陈国涛,梅志远,李华东(海军工程大学舰船工程系,武汉430033)摘要:拉伸强度材料许用值是开展舰用复合材料结构设计所需的重要指标参量。SW220/430LV复合材料是目前较为常用的舰用复合材料体系之一。首先依据规范GB/T1447.2005开展0。/90。铺层试件拉伸强度试验研究,并根据B基准值要求,得出拉伸强度基准值。在此基础上,分别针对不同折减系数条件下的载荷值,开展拉一拉疲劳特性、疲劳承载后剩余强度/刚度试验研究,并同时探讨了载荷特征、应力比、加载频率、疲劳周期等对SW220/430LV复合材料疲劳特性的影响规律。研究结果表明,当计及结构疲劳承载时,SW220/430LV复合材料拉伸强度材料许用值可取为0.45X。关键词:拉伸强度材料许用值;SW220/430LV复合材料;拉一拉疲劳;折减系数;剩余刚度中图分类号:TB332文献标识码:A———文章编号:10030999(2015)09001106迄今,纤维增强树脂基材料(以下简称复合材料)已与合金钢、铝合金一起成为主要的舰船结构工程材料¨J。舰船复合材料结构设计技术的发展对于舰船总体技术及其隐身化、智能化发展具有重要意义,目前已得到越来越多的关注和应用。然而,由于海洋工程结构物在工作环境下受到结构交变载荷与环境因素的长期联合作用,从而易导致结构出现疲劳损伤乃至破坏J。由于大量不确定因素的存在,目前针对疲劳问题进行复合材料结构设计或对结构的疲劳寿命进行预测还是非常困难且复杂的,这就导致舰船复合材料结构使用的安全性和设计可靠性等问题长期困扰舰船设计者们。一般而言,舰船复合材料结构的安全可靠性主’’要取决于两方面载荷因素,一是环境载荷,如7且/湿/盐雾等的侵蚀,二是结构疲劳承载引。拉伸强度材料许用值的确定是开展复合材料结构设计的重要参量和依据,它应考虑对以上两方面的承载要求。同时,也应认识到材料许用值的确定不仅针对材料体系,也与结构的承载特性直接相关。目前,对于结构材料许用值的确定,主要存在以下两种途径:一是在已知结构承载要求的条件下,通过结构耐久性试验来考核与评价材料许用值选取的合理性和冗余特性。二是在获取材料极限强度(如B基准值)的基础上,根据工程疲劳承载或环境周期的要求,通过疲劳或环境试验,确定材料体系的强度特性,并以折减收稿日期:基金项目:作者简介:通讯作者:系数(其倒数称为安全系数,取值小于1)来描述材料许用值。本文主要遵循途径二,开展舰用SW220/430LV复合材料拉伸强度材料许用值的分析。SW220/430LV是目前较为常用的一种舰用复合材料体系之一,是由增强材料SW220玻纤正交织物和基体材料430LV乙烯基树脂组成的,其拉伸强度是衡量强度特性的重要指标之一。本文首先根据—规范GB/T14472005《纤维增强塑料拉伸试验方法》,针对SW220/430LV复合材料0 ̄/90。铺层试件的拉伸强度特性进行试验测试,计算得到B基准值。在此基础上,分别以不同折减系数下的承载状态开展给定周期的疲劳试验,并通过对疲劳后剩余强度与刚度特性进行分析,探讨了SW220/430LV复合材料拉.拉疲劳特性及其强度材料许用值的确定方法及相关影响规律。1SW220/430LV拉伸强度特征1.1试件设计与测试结果—本文根据规范GB/T14472005《纤维增强塑料拉伸试验方法》,开展0 ̄/90。铺层SW220/430LV复合材料拉伸强度的试验工作。基于加工工艺条件的限制和试验经验的总结,本文对试样尺寸,主要是加载端部圆弧过渡曲率参数进行了调整,具体试样尺寸及形状如图1所示。本次试验采用室温静载试验方案,试验仪器为西安LetrylOT疲劳试验机,拉2015..03..19国家自然科学基金面上项目资助(51479205)陈国涛(1990一),男,硕士,主要从事船舶材料与应用工程。—梅志远(1973-),男,博士,硕士生导师,研究方向为舰船复合材料结构应用工程,zhiyuanmei@163.tom。FRP/CM-20l5.No,912SW220/430LV复合材料拉一拉疲劳强度材料许用值试验研究2015年9月仲速率为5mm/min,试件玻纤为0 ̄/90。铺层,含胶量约为32%,试验室温约为20 ̄C,有效试件数量为12个。加持图1试样的型式和尺寸Fig.1Theshapeandsizeoftensilespecimenafteradjustment拉伸强度试验结果显示,试件发生断裂部位均位于中部直线段处,满足试验有效性要求,本文对试件型式的调整合理可行。对拉伸强度试验产生的数据进行处理时,为消除试件截面尺寸影响,将载荷/位移曲线换算为拉应力/位移曲线,纵坐标为拉应力。选取其中5个完整试件拉伸强度特性试验结果进行分析,如图2所示。由图可知:5个试件的拉应力/位移曲线具有基本相似的形态分布特征,整个加载曲线基本呈线弹性分布,且初始阶段具有良好的吻合度,而极限强度值呈现出一定的离散性。蔓。R氆捌图2拉应力/位移曲线Fig.2Thecuresoftensilestress/displacement1-2拉伸强度基准值和初始刚度值K的确定对此,本文针对以上拉伸强度测试结果(测试结果均服从正态分布,且在同一环境下进行试验),基于力学性能数据测试方法j,计算得出B基准值为392MPa,计算公式见式(1)。根据上文阐述,本文基于结构疲劳承载要求的拉伸强度材料许用值应处于点处,对应的拉伸强度材料许用值为392MPa。F】P/CM2015No,9)+霜b2c日6口(:1.1372一0.491621+o.1861213—bB(:0.36961+0.0040342一.71750+.19693F ̄-001j内≥Q--f-2.32+1.138+0.6057 ̄-一o.3287(f3)J,=一(B),(1)式中,为用于表明具体环境条件的容限系数;z为标准的正态随机变量,在计算中z取1.28115;为变异自由度,(-厂=N一2)。本次试验,所有试件均Ⅳ在一个试验环境下进行,因此,取n==12。根据上文阐述,通过对12个完整试件拉伸强度试验数据进行处理,计算得到B基准值,并取初始阶—段(取位移在0.51.5mm范围内,该范围内直线性最好)拉应力/位移曲线斜率作为初始刚度,试验结果如表1所示。表1SW220/430LV复合材料初始拉伸强度值及初始刚度值KTable1ThetensilestrengthvaluesandstiffnessvaluesK.ofSW220/430LVcompositematerial试件...,应力标准离散1#3#4#5#6栉编号均值差率/%2拉-拉疲劳性能试验研究2.1试验方案拉.拉疲劳试验参照规范GB/T16779-2008《纤—维增强塑料层合板拉.拉疲劳性能试验方法》,在LetrylOT疲劳试验机上完成。加载波形为正弦波,频率为5Hz,考核疲劳测试周期15k周,室温约20%。试验方案、载荷参数及所有试件测试结果如表2所示一~2015年第9期玻璃钢/复合材料13表2各试件疲劳试验工况Table2Testconditionsoffatiguespecimen编号载值载值7加率疲期2.2试验结果分析试验结果表明,在拉一拉疲劳试验条件下,当折减系数取为0.65时,试件均在3k周附近发生断裂;当折减系数取为0.55时,试件均在6k周附近发生断裂;当折减系数取为0.5时,试件均在10k周附近发生断裂。上述试验过程,每个工况至少三个试件参与试验,并且在风冷作用下,试件表面温度均控制在25 ̄C以内。因此,认为试件断裂排除了温度的影响,是由受载过大引起的。对此,继续降低折减系数的取值,y分别等于0.45、0.4、0.35,加载频率均为5Hz时,疲劳周数均超过15k周,并且没有断℃裂。而且,在风冷作用下,试件表面温度均在2O以下¨。认为在小应力幅值下,可以进行较长周期(至少为15k周)的疲劳试验。此外,经过疲劳试验后的有效试件在拉伸强度作用下,破坏模式发生改变,沿横截面发生断裂。认为试件在疲劳过程中,材料体系内部结构已经产生损伤,对疲劳后试件再进行拉伸强度试验时,裂纹深度进一步增加,裂纹扩展的方向将会发生变化,即由45。方向向着最大拉伸应力方向发生转变J。3剩余强度及刚度特性试验研究3.1剩余强度特性分析针对疲劳后试件进行拉伸强度试验,得到试件疲劳后剩余强度特征曲线,如图3所示。不同折减系数下试件剩余强度均值汇总如表3所示,测试结果表明,不同折减系数下,疲劳后试件剩余强度值均发生较大幅度下降(退化率约为25%~45%)。本文认为剩余强度的退化是疲劳损伤的结果,是树脂、纤维及其界面微裂纹一小裂纹一裂纹的演变过程。裂纹的扩展速率主要依赖于裂纹尖端的应力集中水平,而应力集中水平正比于载荷大小,因此,随着载荷应力均值的增加,试件剩余疲劳强度的退化率上升,剩余拉伸强度大幅度降低¨J。室稿一Ll704——+L1504—一L160.4’Ll804一一Lll045一L12045一一一.LI3045-LI4045一L15045——÷L200.35—L21035——L22o35——'L2535一一一L240352.5O3.oo图3疲劳后剩余拉一拉强度特征试验曲线Fig.3Curesoflef—ttensiontensionstrengthSfeaturesafterfatigue表3疲劳后试件强度基准值均值、离散系数及退化率Table3Themeanintensityofthereferencevalue,discretecoefficientanddegradationrateafterfatiguetest霉载/k荷N/MPa/笔MPa……饕/MPa ̄(’,%,%312.70290.97306.59269.73294.18264.6O247.58269.16259.75260.11210.37240.63231.71222.16249.13294-835.6O25392.000.35260.243.0934392.OO0.40230.806.6041392.000.453.2疲劳后试件剩余刚度特性及材料许用值分析对于大多数包括复合材料在内的结构构件,刚度的下降可以作为可接受的失效标准。而且试验过’程中网0度的测量具有精确、易测的特点,并易于对磐,c'o.9咖咖咖咖咖咖咖咖咖咖"加加勰如如舳333334444444444叭叭∞∞∞醯卯∞554555555566666123456789012345mm∞muuuuuu01815l87140643767066O897865766123456789O12345mmuuuuuul4SW220/430LV复合材料拉一拉疲劳强度材料许用值试验研究损伤程度进行直接的量化评估j。因此,以剩余刚度为参量,确定折减系数的取值是合理可行的。由图2可知,与完整试件一样,疲劳后试件初始阶段也具有良好的线性度,同样在位移为0.5~1.5mm阶段获取不同折减系数下的剩余刚度。表4给出了不同折减系数下疲劳后试件的剩余刚度值及其退化率。表4不同折减系数下疲劳后剩余刚度均值及退化率Fable4Theresidualstiffnessaverageanddegradationrateafterfatigueunderdift ̄rentreductionfactors..剩余刚度平均值离散系数退化率珈丁/MPa.n】m。/Mmm一1/%/%l36.Oll36.6l133.98136.5l136培6132馏3128.63135.62135.42l3O45l24.64l30.55l28.35l26.43l34.08从表4中可得不同折减系数下疲劳后试件的剩—余刚度值,即各试件拉应力/位移曲线在0.51.5mm范围内斜率的平均值。根据表4,当=0.45时,拉应力/位移斜率平均值的变化率为6.0%<10%。因此,取SW220/430LV复合材料拉伸强度材料许用值的折减系数为0.45。3.3疲劳强度特性影响因素分析疲劳剩余特性试验影响因素较多,主要包括环境温度和疲劳载荷特征,而疲劳载荷特征又主要与载荷波形、均值、峰值、应力比和加载频率等相关¨J。结合本文试验研究,初步探讨载荷特征对SW220/430LV疲劳剩余特性的影响规律如下:(1)疲劳周期对剩余特性的影响本次试验研究结果表明,在相同试验条件下,当疲劳周次达到一定数值时(本次试验为15k),小范围内的疲劳周数的波动对试件剩余特性影响不大。如当折减系数=0.45、加载频率为5Hz,试件疲劳FRP/CM2015.No.9周次分别为15k和20k时,拉应力/位移关系曲线基本吻合;同样,折减系数=0.35、加载频率为5Hz,试件疲劳周次为15k、16k及17k时,拉应力/位移关系曲线也基本吻合,如图4所示。位移/mm图4L3、l4、L5疲劳周数分别为15k、16k及17kFig.4ThecuresofL3,IA,L5withtheirfatiguecyclewas15k,16kand17k(2)应力比对剩余特性的影响上述疲劳试验均是在应力比6取为0.14(国标规定拉一拉疲劳试验中应力比不宜小于0.1)下完成的。为了探讨应力比6对试件疲劳后拉伸强度和剩余刚度的影响,在折减系数=0.45,应力比6等于0.22、0.5、0.91三种情况下,分别进行了疲劳以及拉伸强度试验。试验结果显示,当应力比6分别等于0.14、0.22、0.5时,有效试件的拉应力/位移曲线具有良好的吻合度,而=0.91时,由于此时疲劳载荷幅值很小,疲劳后试件的拉伸强度和剩余刚度几乎没有变化,如图5所示。因此,本文认为折减系数一≤≤定的情况下,0.160.5时,应力比对试件的疲劳特性影响很小,可以忽略不计。这也同时表明,在疲劳试验中,取应力比6=0.14是合理可行的。(a)应力比为0.5与0.22时,拉应力/位移曲线(a)Thetensilestress/displacementeures,whenthestressratiois0.5and0.22叭∞∞∞m¨他2015年第9期玻璃钢/复合材料翻7o0.0o6.oo(b)应力比为0.91与试件L1的拉应力/位移曲线(b)Thetensilestress/displacementcurvesofstressratiois0.91andL1specimentensilestress图5=0.45,6=0.5与0.22、0.91时,拉应力/位移分布特征图Fig.5Curesoftensile/displacement,when=0.45,6=0.5,0.22and0.914结论(1)SW220/430LV复合材料的拉伸强度值及初始刚度值分别约为553.77MPa和137.01MPa/mm。根据拉应力/位移曲线,得出SW220/430LV复合材料拉伸强度与刚度随位移的变化具有如下规律:拉应力随位移呈现良好的线弹性变化,而刚度几乎不发生变化。SW220/430LV复合材料在不同折减系数下疲劳后拉伸强度与剩余刚度的变化规律:在不同折减系数下,SW220/430LV复合材料疲劳后拉伸强度均有较大程度下降,退化率约为25%~45%,剩余刚度也有较大变化。根据SW220/430LV复合材料在不同折减系数下剩余刚度的退化率,确定折减系数取值为0.45,从而得出SW220/430LV复合材料拉伸强度许用应力取值为176.4MPa;(2)考核并通过了确定拉伸强度材料许用值试验方案二,即在获取材料极限强度的基础上,根据工程疲劳承载或环境周期的要求,通过疲劳或环境试验,确定材料体系的强度特性,并以折减系数来描述材料许用值。根据该方案展开试验,得到了相应的试验结果,确定了拉伸强材料许用值;(3)应力比对SW220/430LV复合材料剩余强≤≤度及刚度的影响规律:当折减系数一定,0.160.5时,应力比对SW220/430LV复合材料的疲劳强度影响不大,即疲劳后拉伸强度值与剩余刚度值变≥化不大;当60.9时,由于幅值很小,导致疲劳幅值很低,材料疲劳后拉伸强度、剩余刚度与疲劳前相比均变化很小,这种变化可以忽略不计。参考文献[1]沈真,张晓晶.复合材料飞机结构强度设计与验证概论[M].上海:上海交通大学出版社,2011.1-l1.[2]R.A.SHENIO,J.F.WELLICOME.CompositeMaterialsinMaritime—Structures[J].CambridgeUniversityPress,1993,3-4:179197.[3]DepartmentofDefence.PolymerMatrixCompositesGuidelinesforCharacteristicofStructuralMaterials『M].UnitedStatesofAmerica:2002.[4]欧阳吕伟,吴剑国.基于可靠性的潜艇结构安全系数研究总结报告[R].2005.[5]沈真.复合材料结构设计手册[M].北京:航空工业出版社,2001.[6]刘文埏.结构可靠性设计手册[M].北京:国防工业出版社,2008.143.200.[7]AbouelheigaM.ComponentDesignforAutomatedAircraftCompositeStructureManufacture[R].2010.[8]徐孝诚.复合材料结构强度散布特性及可靠性问题的讨论[J].—强度与环境,1991,2529.[9]WangCH,MillerKJ.Shoafatiguecrackgrowthundermeanstress,uniaxialloading[J].FatigueandFractureofMaterialsand—Structures,1993,16(2):181198.[1O]DuQuesnayDL,TopperTH,eta1.Theeffectofnotchradiusonthefatiguenotchfactorandthepropagationofshortcracks[M].London:M.E.P,1986.323-335.[11]MillerKJ.ThebehaviorofshortfatiguecracksandtheirinitiationPartI-Areviewoftworecentbooks[J].FatigueandFractureofMaterialsandStructures,1993,16(2):181-198.——[12]SeneviratneW.fatigueLifeDeterminationofDamage-TolerantCornpositeairframe[R].WichitaStateUniversity,2008.[13]翟洪军,姚卫星.纤维增强树脂基复合材料的疲劳剩余刚度研—究进展[J].力学进展,2002,32(1):6980.[14]刘鸿文.材料力学[M].北京:高等教育出版社,2004.[15]崔志华.复合材料层压板的疲劳特性[M].北京:教育科学出版社,1996.[16]姚卫星.结构疲劳寿命分析[M].北京:航空工业出版社,2003.FRP/CM2015 ̄No,9SW220/430LV复合材料拉一拉疲劳强度材料许用值试验研究2015年9月THEEXPERIMENTALRESEARCHFoRDESIGALL0WABLE0~IENS10STRENGTHoFSW220/430LVCOMPoSITEMATERIAL——CHENGuotao,MEIZhi-yuan,LIHuadong(ShipEngineering,NavalUniversityofEngineering,Wuhan430033,China)—Abstract:Thetensilestrengthdesignvalueisanimportantguidelinetoweightheintensityofcompositelaminates.SW220/430LVcompositematerialisakindoftypicalcompositematerialwidelyusedinwarships.Inordertoexploretheintensity,thepapercarriedouttheinvestigationaboutthetensionstrengthofo/90。withreferringto—GB/T1447-2005,andworkedouttensilestrengthXrbyBbasevalue.Then,wegetloadsresponsibletoreduction—coefficienttomakeresearchabouttensionshearfatigueandtheleftstiffness,shearstrength,andexploreeffectsoftheloadcharacteristics,suchasstressratio,frequency,fatiguecycletotheSW220/430LVcompositematerialatthesametime.Accordingtoourresearch,wetake0.45XrasthedesigntensilestrengthdesignvalueforSW220/430LVcompositematerial,whenallowingformechanicalfatigue.——Keywords:thetensilestrengthdesignvalues;SW220/430LVcompositematerial;tensiontensionfatigue;reductioncoemcient:leftstiffness(上接第86页)’’’‘—’’’INVESIlGAI100NWEARPR0PERTYU量IABRASl_,RESISllA1CUMPUSlIESMANUFACTUREDBYINTEGRATIVEMoULDING————ZHANGLianwang,LIBaowei,ZHONGXiangyu,BAOJianwen(ScienceandTechnologyonAdvancedCompositesLaboratory,AVICCompositeCenter,BeijingInstituteofAeronauticalMaterials,Beijing100095,China)——Abstract:ThisarticlemadeatryonthepreprationofabrasionresistantcompositesbyintegrativeRTMmoulding.Weartestingofsaidcompositeswasperformed.Surfaceprofilesofsamplesafterwearingtestweredrawnby——PhaseShiftMicroXAM一3D.Granularityansysisofhardnessparticlewhichwasthemaincomponentofabrasionre—sistantcoatingwasconductedbylasergranularityanalyst.Theinsidemicrostructureofabrasionresistantcompositeswasobservedbyscanningelectronmicroscope.Theresultsdemonstratedthatthefrictioncoefficientwascoherentwithultimateindentdepth,namely,thelessthefrictioncoefficientwas,thelessindentdepthwas.Theuseofabra-sion--resistantcompositesinhighspeedconditionscouldbelimitedbecauseresinwasthematrixofabrasion--resistantcoating.Keywords:composite;coat;frictioncoefficient;indentdepthCM2015.No,9
您可能关注的文档
- “离位”增韧复合材料准静态压入损伤特性研究.pdf
- “神舟七号”飞船舱外航天服防护头盔组件的研制.pdf
- “十二五”复合材料发展重点和方向解读.pdf
- “珠串”堆叠超结构的介孔铁酸锌的制备与表征.pdf
- (001)应变对正交相Ca2 P0.25 Si0.75能带结构及光学性质的影响.pdf
- 0.8设计系数用X80管线钢在近中性pH溶液中的应力腐蚀开裂行为.pdf
- 0.20mm CGO硅钢高温退火Goss晶粒起源及异常长大行为研究.pdf
- 0Cr16Ni5Mo低碳马氏体不锈钢的热变形行为及其热加工图.pdf
- 0Cr17Ni4Cu4Nb钢制螺钉断裂原因分析.pdf
- 1.5MW风机叶片模具加热工艺研究与技术创新.pdf
- 1.5MW风机叶片VARI工艺模拟分析及验证.pdf
- 2.5维机织复合材料低速冲击性能研究.pdf
- 2.25Cr-1Mo钢后续热处理中的磷偏聚行为.pdf
- 2A50锻铝三点弯曲试验与高分辨率CT成像分析.pdf
- 2A12与2A11铝合金超声波焊接工艺与组织研究.pdf
- 2MW风机复合材料叶片材料及工艺研究.pdf
- 3Cr2W8V模具钢激光表面相变硬化层性能的研究.pdf
- 3D打印技术及先进应用研究进展.pdf
- 3D打印技术研究现状和关键技术.pdf
- 5%鱼藤酮悬浮剂的研制.pdf

- 周大爷
- 该用户很懒,什么也没介绍
相关文档
- “离位”增韧复合材料准静态压入损伤特性研究.pdf2021-11-235页
- “神舟七号”飞船舱外航天服防护头盔组件的研制.pdf2021-11-233页
- “十二五”复合材料发展重点和方向解读.pdf2021-11-232页
- “珠串”堆叠超结构的介孔铁酸锌的制备与表征.pdf2021-11-235页
- (001)应变对正交相Ca2 P0.25 Si0.75能带结构及光学性质的影响.pdf2021-11-236页
- 0.8设计系数用X80管线钢在近中性pH溶液中的应力腐蚀开裂行为.pdf2021-11-237页
- 0.20mm CGO硅钢高温退火Goss晶粒起源及异常长大行为研究.pdf2021-11-237页