- 文档大小:2.29 MB
- 文档格式:pdf
- 约 6页
- 2022-03-25 发布
- 举报
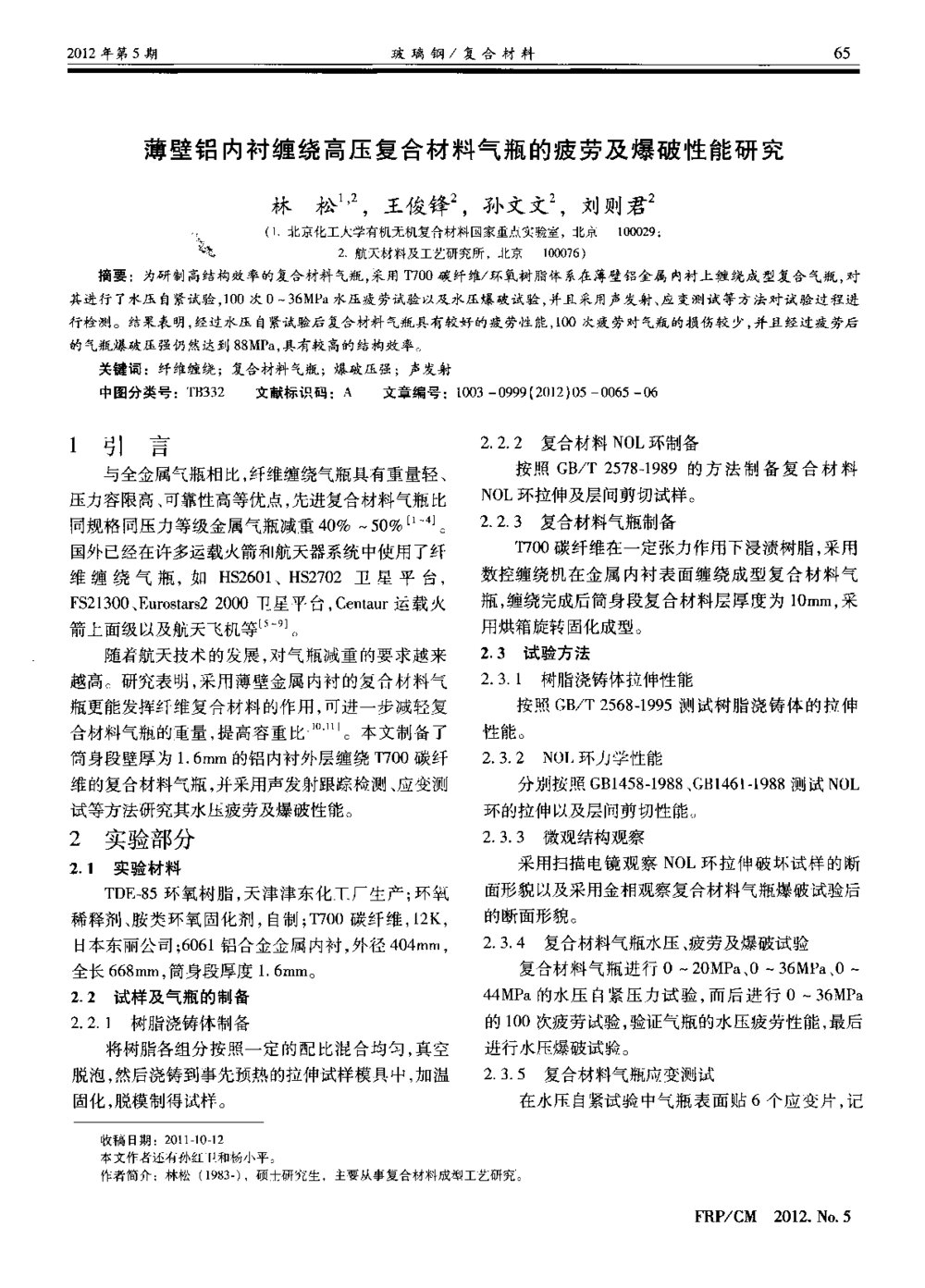
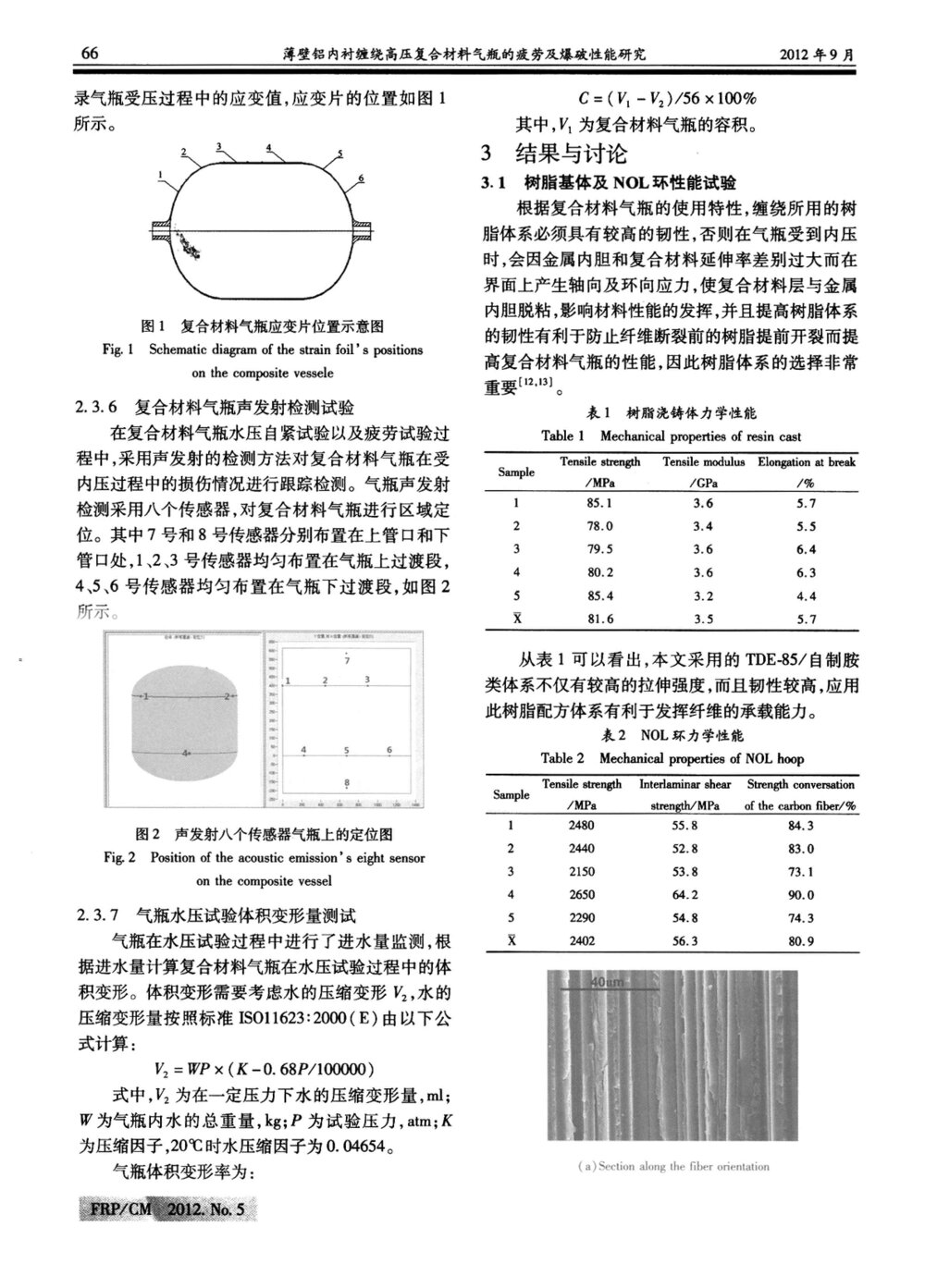
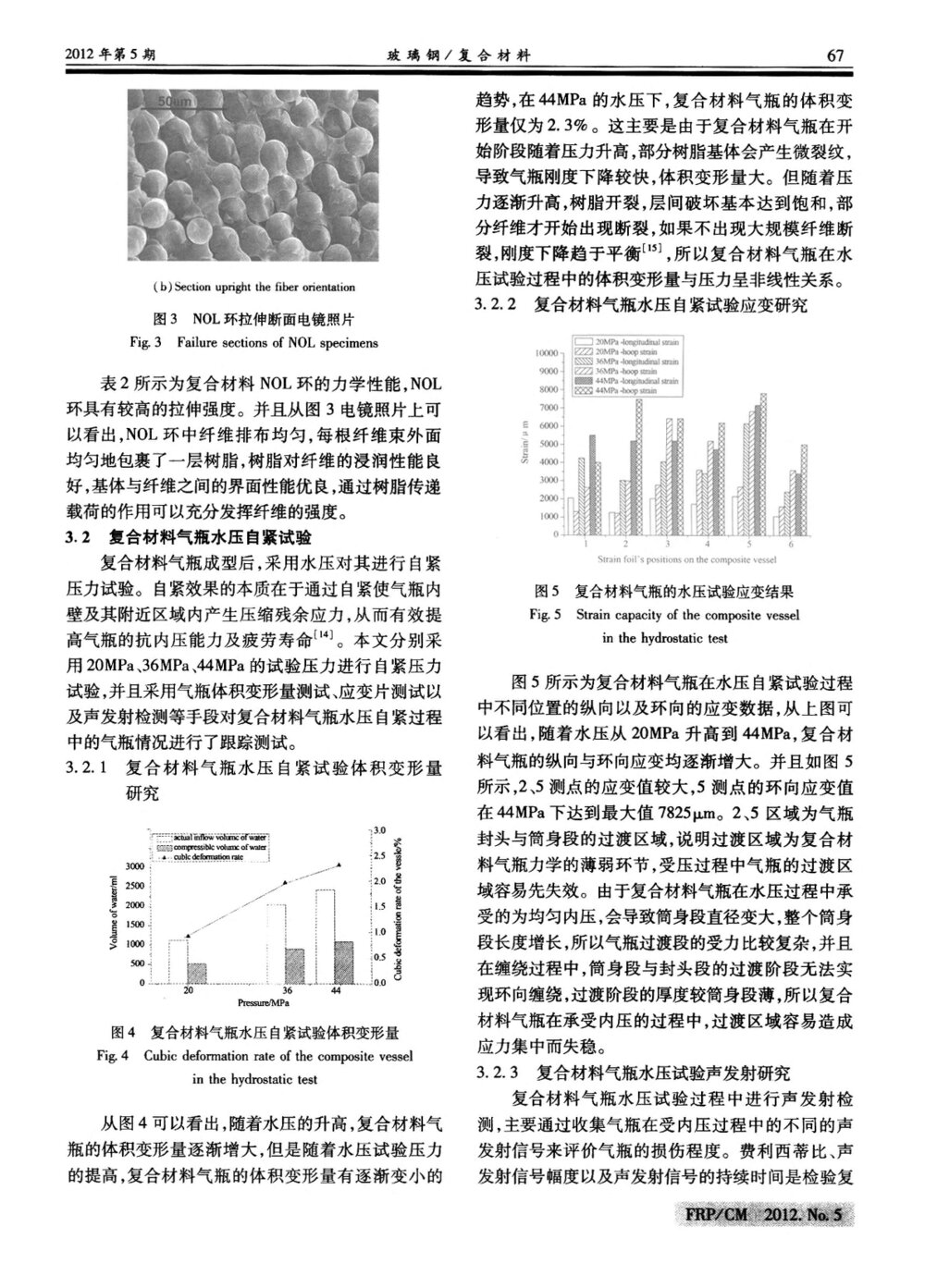
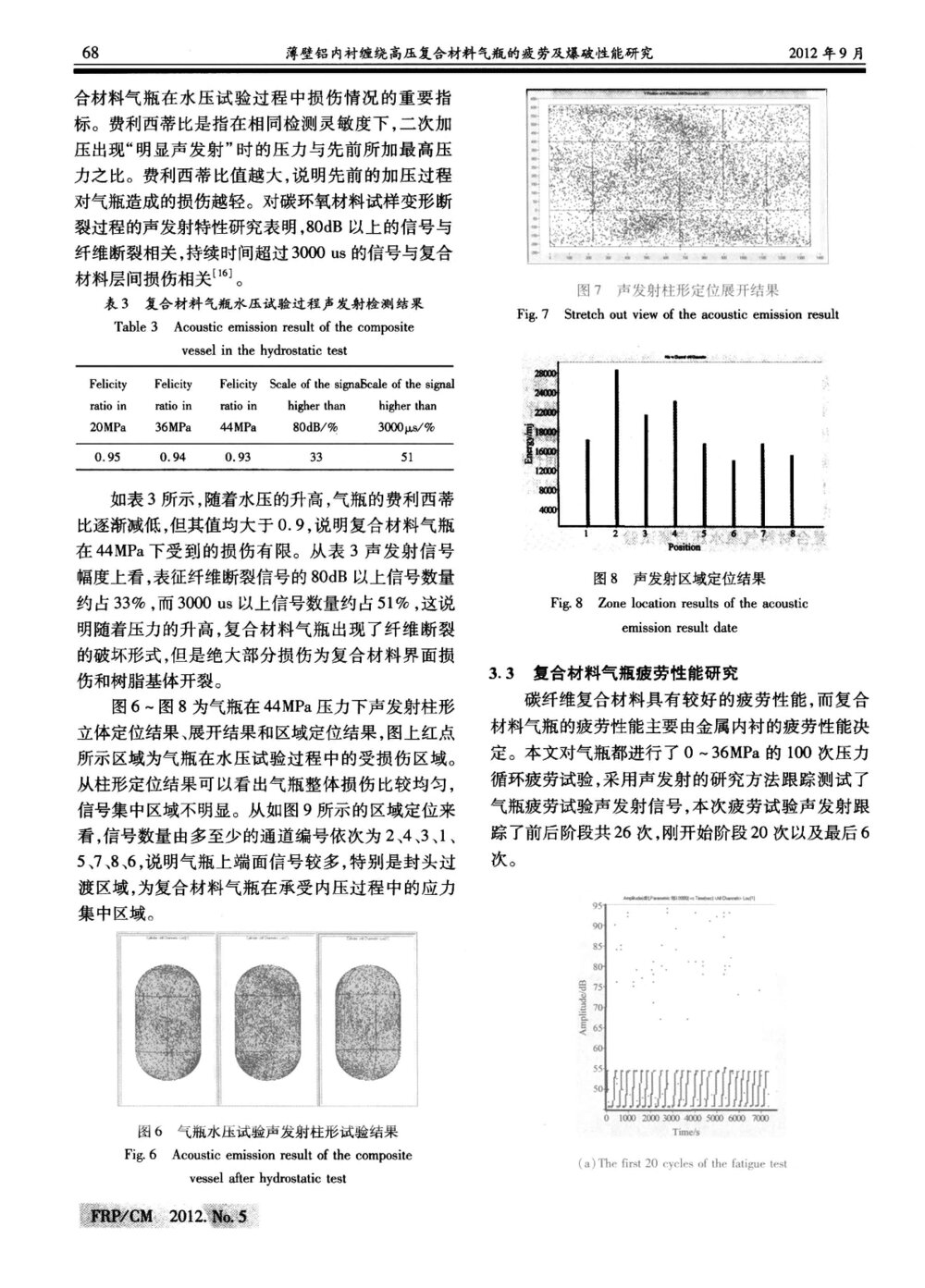
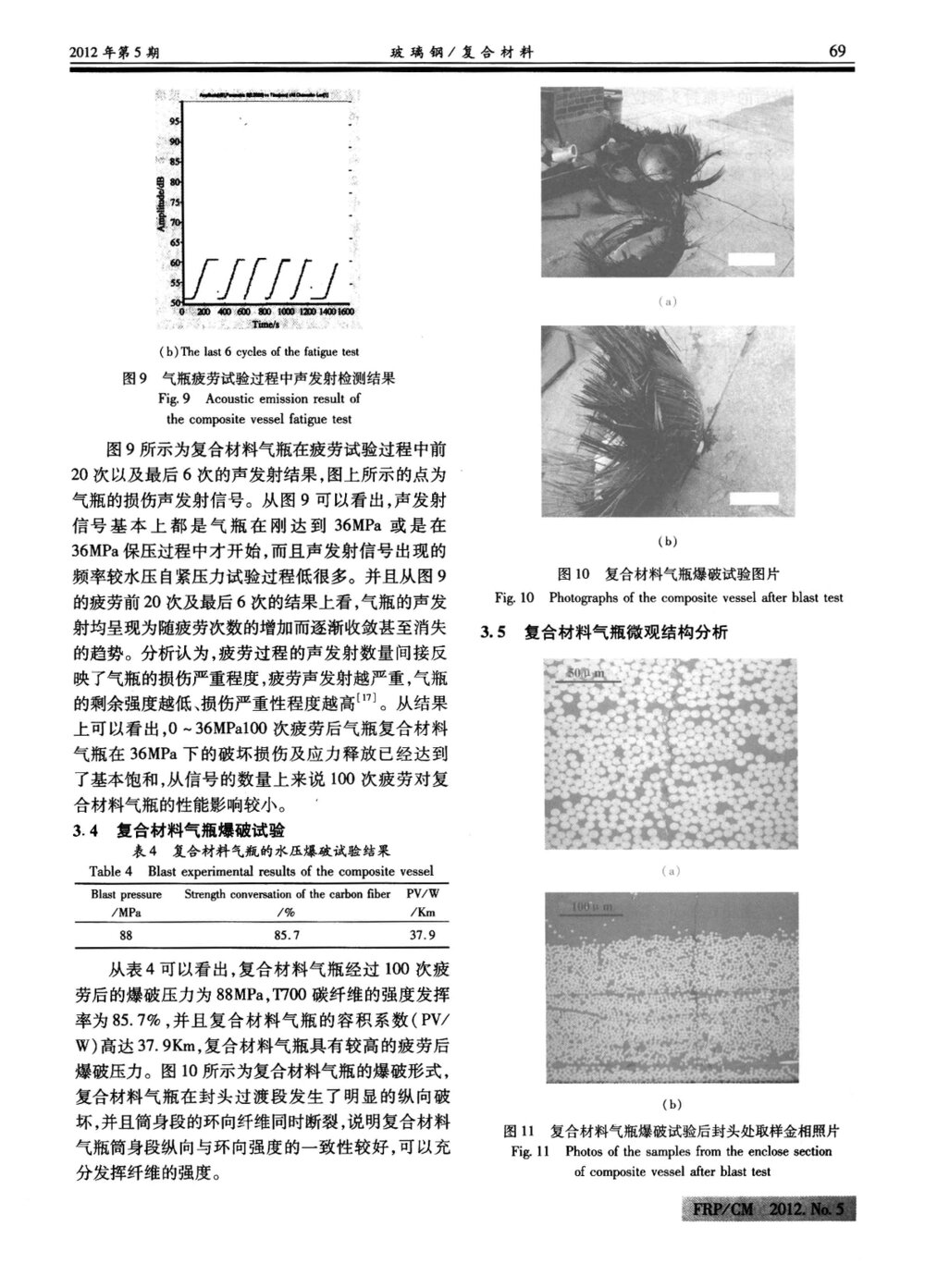
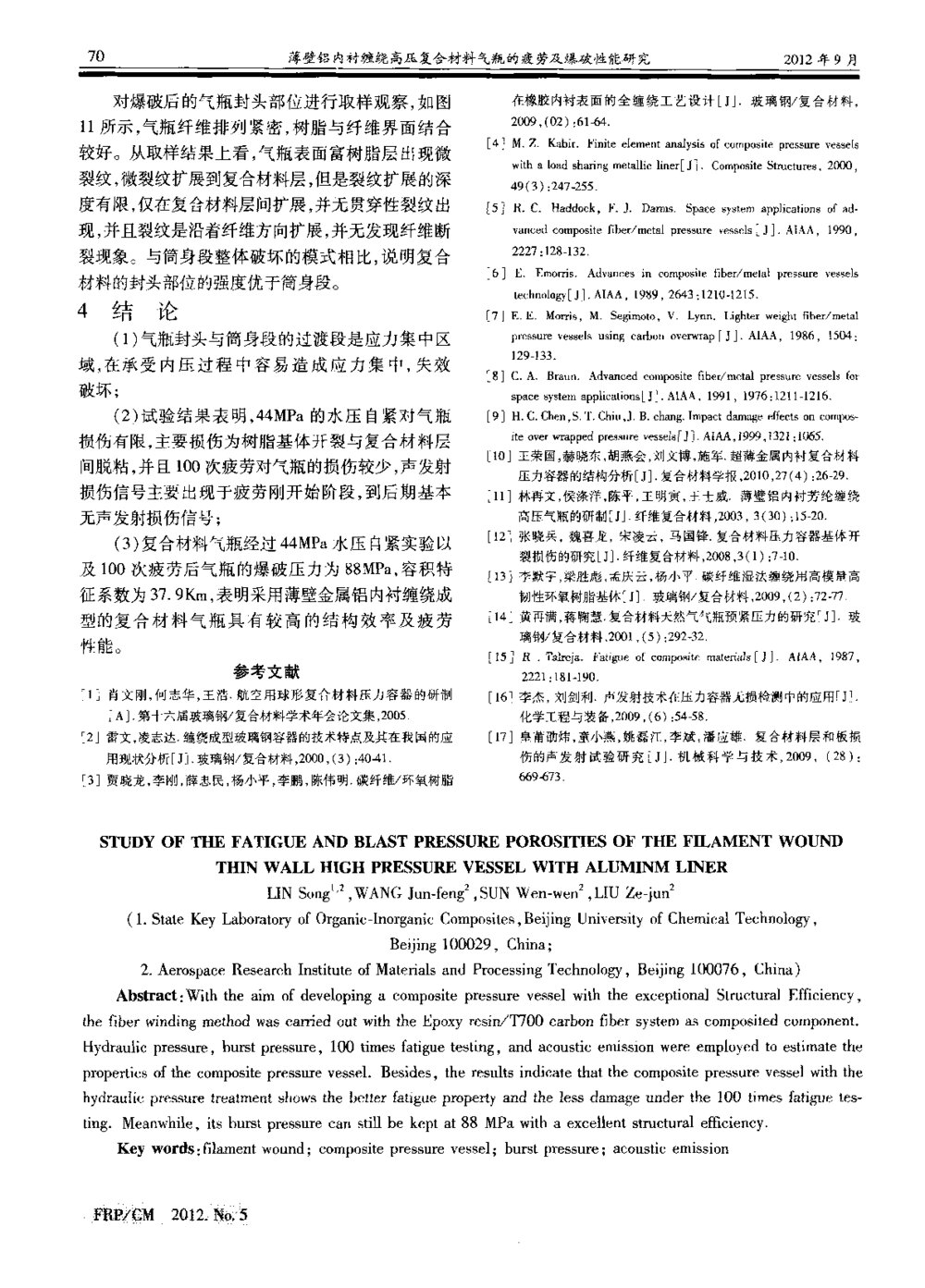
已阅读完毕,您还可以下载文档进行保存
- 1、本文档共6页,内容下载后可编辑。
- 2、本文档内容版权归属内容提供方,所产生的收益全部归内容提供方所有。如果您对本文有版权争议,可选择认领。
- 3、本文档由用户上传,本站不保证质量和数量令人满意,可能有诸多瑕疵,付费之前,请仔细先通过免费阅读内容等途径辨别内容交易风险。如存在严重挂羊头卖狗肉之情形,可联系本站下载客服投诉处理。
2012年第5期玻璃钢/复合材料65薄壁铝内衬缠绕高压复合材料气瓶的疲劳及爆破性能研究林松1’2,王俊锋2,孙文文2,刘则君2。(1.北京化工大学有机无机复合材料国家重点实验室,北京100029;毪2.航天材料及工艺研究所,北京100076)摘要:为研制高结构效率的复合材料气瓶,采用r1700碳纤维/环氧树脂体系在薄壁铝金属内衬上缠绕成型复合气瓶,对其进行了水压自紧试验,100次0~36MPa水压疲劳试验以及水压爆破试验.并且采用声发射、应变测试等方法对试验过程进行检测。结果表明,经过水压自紧试验后复合材料气瓶具有较好的疲劳性能,100次疲劳对气瓶的损伤较少,并且经过疲劳后的气瓶爆破压强仍然达到88MPa,具有较高的结构效率。关键词:纤维缠绕;复合材料气瓶;爆破压强;声发射中图分类号:TB332文献标识码:A文章编号:1003—0999(2012)05—0065—061引言与全金属气瓶相比,纤维缠绕气瓶具有重量轻、压力容限高、可靠性高等优点,先进复合材料气瓶比同规格同压力等级金属气瓶减重40%~50%¨“J。国外已经在许多运载火箭和航天器系统中使用了纤维缠绕气瓶,如HS2601、HS2702卫星平台,FS21300、Eurostars22000卫星平台,Centaur运载火箭上面级以及航天飞机等¨曲J。随着航天技术的发展,对气瓶减重的要求越来越高。研究表明,采用薄壁金属内衬的复合材料气瓶更能发挥纤维复合材料的作用,可进一步减轻复合材料气瓶的重量,提高容重比¨0’11o。本文制备了筒身段壁厚为1.6ram的铝内衬外层缠绕T700碳纤维的复合材料气瓶,并采用声发射跟踪检测、应变测试等方法研究其水压疲劳及爆破性能。2实验部分2.1实验材料TDE.85环氧树脂,天津津东化工厂生产;环氧稀释剂、胺类环氧固化剂,自制;T700碳纤维,12K,日本东丽公司;6061铝合金金属内衬,外径404ram,全长668mm,筒身段厚度1.6mm。2.2试样及气瓶的制备2.2.1树脂浇铸体制备将树脂各组分按照一定的配比混合均匀,真空脱泡,然后浇铸到事先预热的拉伸试样模具中,加温固化,脱模制得试样。2.2.2复合材料NOL环制备按照GB/T2578.1989的方法制备复合材料NOL环拉伸及层间剪切试样。2.2.3复合材料气瓶制备\"1700碳纤维在一定张力作用下浸渍树脂,采用数控缠绕机在金属内衬表面缠绕成型复合材料气瓶,缠绕完成后筒身段复合材料层厚度为10mm,采用烘箱旋转固化成型。2.3试验方法2.3.1树脂浇铸体拉伸性能按照GB/T2568.1995测试树脂浇铸体的拉伸性能。2.3.2NOL环力学性能分别按照GBl458.1988、GBl461.1988测试NOL环的拉伸以及层问剪切性能。2.3.3微观结构观察采用扫描电镜观察NOL环拉伸破坏试样的断面形貌以及采用金相观察复合材料气瓶爆破试验后的断面形貌。2.3.4复合材料气瓶水压、疲劳及爆破试验复合材料气瓶进行0~20MPa、0~36MPa、0~44MPa的水压自紧压力试验,而后进行0~36MPa的100次疲劳试验,验证气瓶的水压疲劳性能,最后进行水压爆破试验。2.3.5复合材料气瓶应变测试在水压自紧试验中气瓶表面贴6个应变片,记收稿日期:2011.10—12本文作者还有孙红卫和杨小平。作者简介:林松(1983-),硕士研究生,主要从事复合材料成型工艺研究。FRP/CM2012.No.5薄壁铝内村缠绕高压复合材料气瓶的疲劳及爆破性能研究2012年9月录气瓶受压过程中的应变值,应变片的位置如图1所示。图1复合材料气瓶应变片位置示意图Fig.1Schematicdiagramofthestrainfoil’8positionsonthecompositevessele2.3.6复合材料气瓶声发射检测试验在复合材料气瓶水压自紧试验以及疲劳试验过程中,采用声发射的检测方法对复合材料气瓶在受内压过程中的损伤情况进行跟踪检测。气瓶声发射检测采用八个传感器,对复合材料气瓶进行区域定位。其中7号和8号传感器分别布置在上管口和下管口处,1、2、3号传感器均匀布置在气瓶上过渡段,4、5、6号传感器均匀布置在气瓶下过渡段,如图2所汞图2声发射八个传感器气瓶上的定位图Fig.2Positionoftheacousticemission’seightsensoronthecompositevessel2.3.7气瓶水压试验体积变形量测试气瓶在水压试验过程中进行了进水量监测,根据进水量计算复合材料气瓶在水压试验过程中的体积变形。体积变形需要考虑水的压缩变形K,水的压缩变形量按照标准IS011623:2000(E)由以下公式计算:v2=即×(K-0.68P/100000)式中,K为在一定压力下水的压缩变形量,nd;形为气瓶内水的总重量,kg;P为试验压力,arm;K为压缩因子,20℃时水压缩因子为0.04654。气瓶体积变形率为:C=(Vl—v2)/56×100%其中,K为复合材料气瓶的容积。3结果与讨论3.1树脂基体及NOL环性能试验根据复合材料气瓶的使用特性,缠绕所用的树脂体系必须具有较高的韧性,否则在气瓶受到内压时,会因金属内胆和复合材料延伸率差别过大而在界面上产生轴向及环向应力,使复合材料层与金属内胆脱粘,影响材料性能的发挥,并且提高树脂体系的韧性有利于防止纤维断裂前的树脂提前开裂而提高复合材料气瓶的性能,因此树脂体系的选择非常重要012.13]o表1树脂浇铸体力学性能Table1Mechanicalpropertiesofresincast从表1可以看出,本文采用的TDE-85/自制胺类体系不仅有较高的拉伸强度,而且韧性较高,应用此树脂配方体系有利于发挥纤维的承载能力。表2NOL环力学性能Table2MechanicalpropertiesofNOLhoopTensile8t地n_ctlIInterlaminarshearStrengthconverfstionSample/MPa蚰ngth/MPaofthecarbonfiber/%l248055.884.32440215026502290240252.853.864.254.856.383.O73.190.074.380.92012年第5期玻璃钢/复合材料67Lb)Sectionuptighttheiiberofienbtion图3NOL环拉伸断面电镜照片Fig.3FailuresectionsofNOLspecimens表2所示为复合材料NOL环的力学性能,NOL环具有较高的拉伸强度。并且从图3电镜照片上可以看出,NOL环中纤维排布均匀,每根纤维束外面均匀地包裹了一层树脂,树脂对纤维的浸润性能良好,基体与纤维之间的界面性能优良,通过树脂传递载荷的作用可以充分发挥纤维的强度。3.2复合材料气瓶水压自紧试验复合材料气瓶成型后,采用水压对其进行自紧压力试验。自紧效果的本质在于通过自紧使气瓶内壁及其附近区域内产生压缩残余应力,从而有效提高气瓶的抗内压能力及疲劳寿命¨41。本文分别采用20MPa、36MPa、44MPa的试验压力进行自紧压力试验,并且采用气瓶体积变形量测试、应变片测试以及声发射检测等手段对复合材料气瓶水压自紧过程中的气瓶情况进行了跟踪测试。3.2.1复合材料气瓶水压自紧试验体积变形量研究姗0j…i…隐一一ijg{…%20图4复合材料气瓶水压自紧试验体积变形量Fig.4Cubicdeformationrateofthecompositevesselinthehydrostatictest从图4可以看出,随着水压的升高,复合材料气瓶的体积变形量逐渐增大,但是随着水压试验压力的提高,复合材料气瓶的体积变形量有逐渐变小的趋势,在44MPa的水压下,复合材料气瓶的体积变形量仅为2.3%。这主要是由于复合材料气瓶在开始阶段随着压力升高,部分树脂基体会产生微裂纹,导致气瓶刚度下降较快,体积变形量大。但随着压力逐渐升高,树脂开裂,层间破坏基本达到饱和,部分纤维才开始出现断裂,如果不出现大规模纤维断裂,刚度下降趋于平衡【I5】,所以复合材料气瓶在水压试验过程中的体积变形量与压力呈非线性关系。3.2.2复合材料气瓶水压自紧试验应变研究L—J20Mh-Io帅1…姗臣盈20慨-romp∞h圆%MPa堋utltmlstraitⅧ囫舟栅swain1“m-!ongltudmlm¨“№鼬-hoop$自nun图5复合材料气瓶的水压试验应变结果Fig.5Straincapacityofthecompositevesselinthehydrostatictest图5所示为复合材料气瓶在水压自紧试验过程中不同位置的纵向以及环向的应变数据,从上图可以看出,随着水压从20MPa升高到44MPa,复合材料气瓶的纵向与环向应变均逐渐增大。并且如图5所示,2、5测点的应变值较大,5测点的环向应变值在44MPa下达到最大值7825岬。2、5区域为气瓶封头与筒身段的过渡区域,说明过渡区域为复合材料气瓶力学的薄弱环节,受压过程中气瓶的过渡区域容易先失效。由于复合材料气瓶在水压过程中承受的为均匀内压,会导致筒身段直径变大,整个筒身段长度增长,所以气瓶过渡段的受力比较复杂,并且在缠绕过程中,筒身段与封头段的过渡阶段无法实现环向缠绕,过渡阶段的厚度较筒身段薄,所以复合材料气瓶在承受内压的过程中,过渡区域容易造成应力集中而失稳。3+2.3复合材料气瓶水压试验声发射研究复合材料气瓶水压试验过程中进行声发射检测,主要通过收集气瓶在受内压过程中的不同的声发射信号来评价气瓶的损伤程度。费利西蒂比、声发射信号幅度以及声发射信号的持续时间是检验复弼氇鐾孵鲢《溜目瞰豁蕾《馥蠢繁。.匠睫渥沿滢灌蓬啪蜘咖铷啪322l●一E亲iJ0Q莹o>68薄壁铝内衬缠绕高压复合材料气瓶的疲劳及爆破性能研究2012年9月合材料气瓶在水压试验过程中损伤情况的重要指标。费利西蒂比是指在相同检测灵敏度下,二次加“”压出现明显声发射时的压力与先前所加最高压力之比。费利西蒂比值越大,说明先前的加压过程对气瓶造成的损伤越轻。对碳环氧材料试样变形断裂过程的声发射特性研究表明,80dB以上的信号与纤维断裂相关,持续时间超过3000US的信号与复合材料层间损伤相关¨6|。表3复合材料气瓶水压试验过程声发射检测结果Table3Acousticemissionresultofthecompositevesselinthehydrostatictest如表3所示,随着水压的升高,气瓶的费利西蒂比逐渐减低,但其值均大于0.9,说明复合材料气瓶在44MPa下受到的损伤有限。从表3声发射信号幅度上看,表征纤维断裂信号的80dB以上信号数量约占33%,而3000US以上信号数量约占5l%,这说明随着压力的升高,复合材料气瓶出现了纤维断裂的破坏形式,但是绝大部分损伤为复合材料界面损伤和树脂基体开裂。图6~图8为气瓶在44MPa压力下声发射柱形立体定位结果、展开结果和区域定位结果,图上红点所示区域为气瓶在水压试验过程中的受损伤区域。从柱形定位结果可以看出气瓶整体损伤比较均匀,信号集中区域不明显。从如图9所示的区域定位来看,信号数量由多至少的通道编号依次为2、4、3、1、5、7、8、6,说明气瓶上端面信号较多,特别是封头过渡区域,为复合材料气瓶在承受内压过程中的应力集中区域。酬围图6气瓶水压试验声发射柱彤试验结果Fig.6AcousticemissionresultofthecompositevesselafterhydrostatictestI冬|1,t‘”,戈射j}=三:t””慢£?。{i墩Fig.7Stretchoutviewoftheacousticemissionresult图8声发射区域定位结果Fig.8Zonelocationresultsoftheacousticemissionresultdate3.3复合材料气瓶疲劳性能研究碳纤维复合材料具有较好的疲劳性能,而复合材料气瓶的疲劳性能主要由金属内衬的疲劳性能决定。本文对气瓶都进行了0—36MPa的100次压力循环疲劳试验,采用声发射的研究方法跟踪测试了气瓶疲劳试验声发射信号,本次疲劳试验声发射跟踪了前后阶段共26次,刚开始阶段20次以及最后6次。2012年第5期玻璃钢/复合材料(b)Thelast6cyclesofthefatiguetest图9气瓶疲劳试验过程中声发射检测结果Fig.9Acousticemissionresultofthecompositevesselfatiguetest图9所示为复合材料气瓶在疲劳试验过程中前20次以及最后6次的声发射结果,图上所示的点为气瓶的损伤声发射信号。从图9可以看出,声发射信号基本上都是气瓶在刚达到36MPa或是在36MPa保压过程中才开始,而且声发射信号出现的频率较水压自紧压力试验过程低很多。并且从图9的疲劳前20次及最后6次的结果上看,气瓶的声发射均呈现为随疲劳次数的增加而逐渐收敛甚至消失的趋势。分析认为,疲劳过程的声发射数量间接反映了气瓶的损伤严重程度,疲劳声发射越严重,气瓶的剩余强度越低、损伤严重性程度越高¨¨。从结果上可以看出,0—36MPal00次疲劳后气瓶复合材料气瓶在36MPa下的破坏损伤及应力释放已经达到了基本饱和,从信号的数量上来说100次疲劳对复合材料气瓶的性能影响较小。3.4复合材料气瓶爆破试验表4复合材料气瓶的水压爆破试验结果Table4Blastexperimentalresultsofthecompositevessel从表4可以看出,复合材料气瓶经过100次疲劳后的爆破压力为88MPa,r1700碳纤维的强度发挥率为85.7%,并且复合材料气瓶的容积系数(PV/w)高达37.9Km,复合材料气瓶具有较高的疲劳后爆破压力。图10所示为复合材料气瓶的爆破形式,复合材料气瓶在封头过渡段发生了明显的纵向破坏,并且筒身段的环向纤维同时断裂,说明复合材料气瓶筒身段纵向与环向强度的一致性较好,可以充分发挥纤维的强度。。。\【b)图10复合材料气瓶爆破试验图片Fig.10Photographsofthecompositevesselafterblasttest3.5复合材料气瓶微观结构分析(b)图ll复合材料气瓶爆破试验后封头处取样金相照片Fig.11Photosofthesamplesfromtheenclosesectionofcompositevesselafterblasttest70薄壁铝内衬缠绕高压复合材料气瓶的疲劳及爆破性能研究2012年9月对爆破后的气瓶封头部位进行取样观察,如图11所示,气瓶纤维排列紧密,树脂与纤维界面结合较好。从取样结果上看,气瓶表面富树脂层出现微裂纹,微裂纹扩展到复合材料层,但是裂纹扩展的深度有限,仅在复合材料层间扩展,并无贯穿性裂纹出现,并且裂纹是沿着纤维方向扩展,并无发现纤维断裂现象。与筒身段整体破坏的模式相比,说明复合材料的封头部位的强度优于筒身段。4结论(1)气瓶封头与筒身段的过渡段是应力集中区域,在承受内压过程中容易造成应力集中,失效破坏;(2)试验结果表明,44MPa的水压自紧对气瓶损伤有限,主要损伤为树脂基体开裂与复合材料层间脱粘,并且100次疲劳对气瓶的损伤较少,声发射损伤信号主要出现于疲劳刚开始阶段,到后期基本无声发射损伤信号;(3)复合材料气瓶经过44MPa水压自紧实验以及100次疲劳后气瓶的爆破压力为88MPa,容积特征系数为37.9Km,表明采用薄壁金属铝内衬缠绕成型的复合材料气瓶具有较高的结构效率及疲劳性能。参考文献[1]肖文刚,何志华,王浩.航空用球形复合材料压力容器的研制[A].第十六届玻璃钢/复合材料学术年会论文集,2005[2]雷文,凌志达.缠绕成型玻璃钢容器的技术特点及其在我国的应用现状分析[J].玻璃钢/复合材料,2000,(3):4041.『3]贾晓龙,李刚。薛忠民,杨小平.李鹏,陈伟明.碳纤维/环氧树脂在橡胶内衬表面的全缠绕工艺设计[J].玻璃钢/复合材料,2009,(02):61-64.[4]M.z.Kabir,Finiteelementanalysisofcompositepressurevesselswithaloadsharingmetallicliner[J].CompositeStructures,2000,49(3):247-255.[5]R.c.Haddock,F.J.Danns.Spacesystemapplicationsofad—vancedcompositefiber/metalpressurevessels[J].AIAA,1990,2227:128.132.[6]E.Emorris,Advancesincompositefiber/metalpressurevesselstechnology[J].AIAA,1989,2643:1210—1215.[7]E.E.Morris,M.Segimoto,V.Lynil.Lighterweightfiber/metalpressurevesselsusingcarbonoverwrap[J].AIAA,1986,1504:129.】33.[8]c.A.Braun.Advancedcompositefiber/metalpressurevesselsforspacesystemapplications[J].AIAA,1991,1976:1211-1216.[9]H.C.Chen,S.T.Chiu\'JB,chang.Impactdamageeffectsoncompos—iteoverwrappedpressurevessels[J]AtAA,1999,{321:1065.[10]王荣国,赫晓东,胡燕会,刘文博,施军.超薄金属内衬复合材料压力容器的结构分析[J].复合材料学报,2010,27(4):26-29.[11]林再文,侯涤洋,陈平,王明寅,王士威.薄璧铝内衬芳纶缠绕高压气瓶的研制[J].纤维复合材料,2003,3(30):15—20.[12]张晓兵,魏喜龙,宋凌云,马国锋.复合材料压力容器基体开裂损伤的研究[J].纤维复合材料,2008,3(1):7—10.[13]李默字,梁胜彪,盂庆云,杨小平.碳纤维湿法缠绕用高模量高韧性环氧树脂基体[J].玻璃钢/复合材料,2009,(2):72-77.[14]黄再满,蒋鞠慧.复合材料天然气气瓶预紧压力的研究[J].玻璃钢/复合材料,2001,(5):292—32.[15]R.Yalreja,Fatigueofcompositemater/als[J],AIAA,1987,2221:181—190.[16]李杰,刘剑利.声发射技术在压力容器无损检测中的应用[J].化学工程与装备,2009,(6):54-58.[17]皇莆劭炜,童小燕,姚磊江,李斌,潘应雄.复合材料层和板损伤的声发射试验研究[J].机械科学与技术,2009,(28):669-673STUDYoFTHEFATIGUEANDBLAS’I’PRESSUREPoRoSITIESOFTHEFILAMEN’I’WoUNDTHINWALLHIGHPRESSUREVESSELWlTHALUMINMLINERLINSong‘12,WANGJun—fen92,SUNWen—wen2,LIUZe-jun2(1.StateKeyLaboratoryofOrganic—InorganicComposites,BeijingUniversityofChemicalTechnology,Beijing100029,China;2.AerospaceResearchInstituteofMaterialsandProcessingTechnology,Beijing100076,China)Abstract:WiththeaimofdevelopingacompositepressurevesselwiththeexceptionalStructuralEfficiency,thefiberwindingmethodwascarriedoutwiththeEpoxyresin/T700carbonfibersystemascompositedcomponent.Hydraulicpressure,burstpressure,100timesfatiguetesting,andacousticemissionwereemployedtoestimatethepropertiesofthecompositepressurevessel.Besides,theresultsindicatethatthecompositepressurevesselwiththehydraulicpressuretreatmentSHOWSthebetterfatiguepropertyandthelessdamageunderthe100timesfatiguetes—ting.Meanwhile,itsburstpressurecanstillbekeptat88MPawithaexcellentstructuralefficiency.Keywords:filamentwound;compositepressurevessel;burstpressure;acousticemissionFRP/CM2012.No,5
您可能关注的文档
- “离位”增韧复合材料准静态压入损伤特性研究.pdf
- “神舟七号”飞船舱外航天服防护头盔组件的研制.pdf
- “十二五”复合材料发展重点和方向解读.pdf
- “珠串”堆叠超结构的介孔铁酸锌的制备与表征.pdf
- (001)应变对正交相Ca2 P0.25 Si0.75能带结构及光学性质的影响.pdf
- 0.8设计系数用X80管线钢在近中性pH溶液中的应力腐蚀开裂行为.pdf
- 0.20mm CGO硅钢高温退火Goss晶粒起源及异常长大行为研究.pdf
- 0Cr16Ni5Mo低碳马氏体不锈钢的热变形行为及其热加工图.pdf
- 0Cr17Ni4Cu4Nb钢制螺钉断裂原因分析.pdf
- 1.5MW风机叶片模具加热工艺研究与技术创新.pdf
- 1.5MW风机叶片VARI工艺模拟分析及验证.pdf
- 2.5维机织复合材料低速冲击性能研究.pdf
- 2.25Cr-1Mo钢后续热处理中的磷偏聚行为.pdf
- 2A50锻铝三点弯曲试验与高分辨率CT成像分析.pdf
- 2A12与2A11铝合金超声波焊接工艺与组织研究.pdf
- 2MW风机复合材料叶片材料及工艺研究.pdf
- 3Cr2W8V模具钢激光表面相变硬化层性能的研究.pdf
- 3D打印技术及先进应用研究进展.pdf
- 3D打印技术研究现状和关键技术.pdf
- 5%鱼藤酮悬浮剂的研制.pdf

- 庸梦人
- 该用户很懒,什么也没介绍
相关文档
- “离位”增韧复合材料准静态压入损伤特性研究.pdf2021-11-235页
- “神舟七号”飞船舱外航天服防护头盔组件的研制.pdf2021-11-233页
- “十二五”复合材料发展重点和方向解读.pdf2021-11-232页
- “珠串”堆叠超结构的介孔铁酸锌的制备与表征.pdf2021-11-235页
- (001)应变对正交相Ca2 P0.25 Si0.75能带结构及光学性质的影响.pdf2021-11-236页
- 0.8设计系数用X80管线钢在近中性pH溶液中的应力腐蚀开裂行为.pdf2021-11-237页
- 0.20mm CGO硅钢高温退火Goss晶粒起源及异常长大行为研究.pdf2021-11-237页