- 文档大小:2.16 MB
- 文档格式:pdf
- 约 6页
- 2022-03-25 发布
- 举报
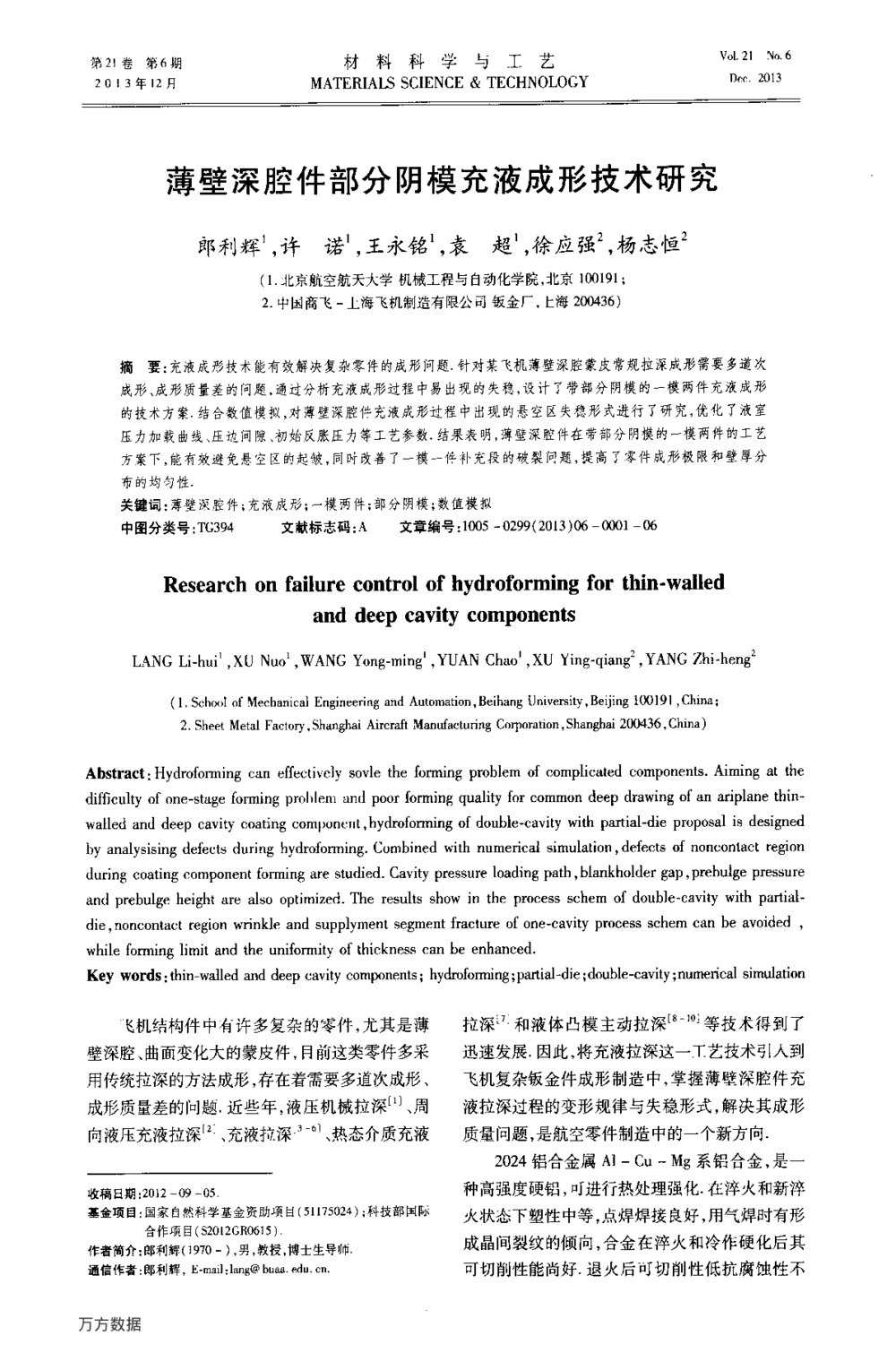
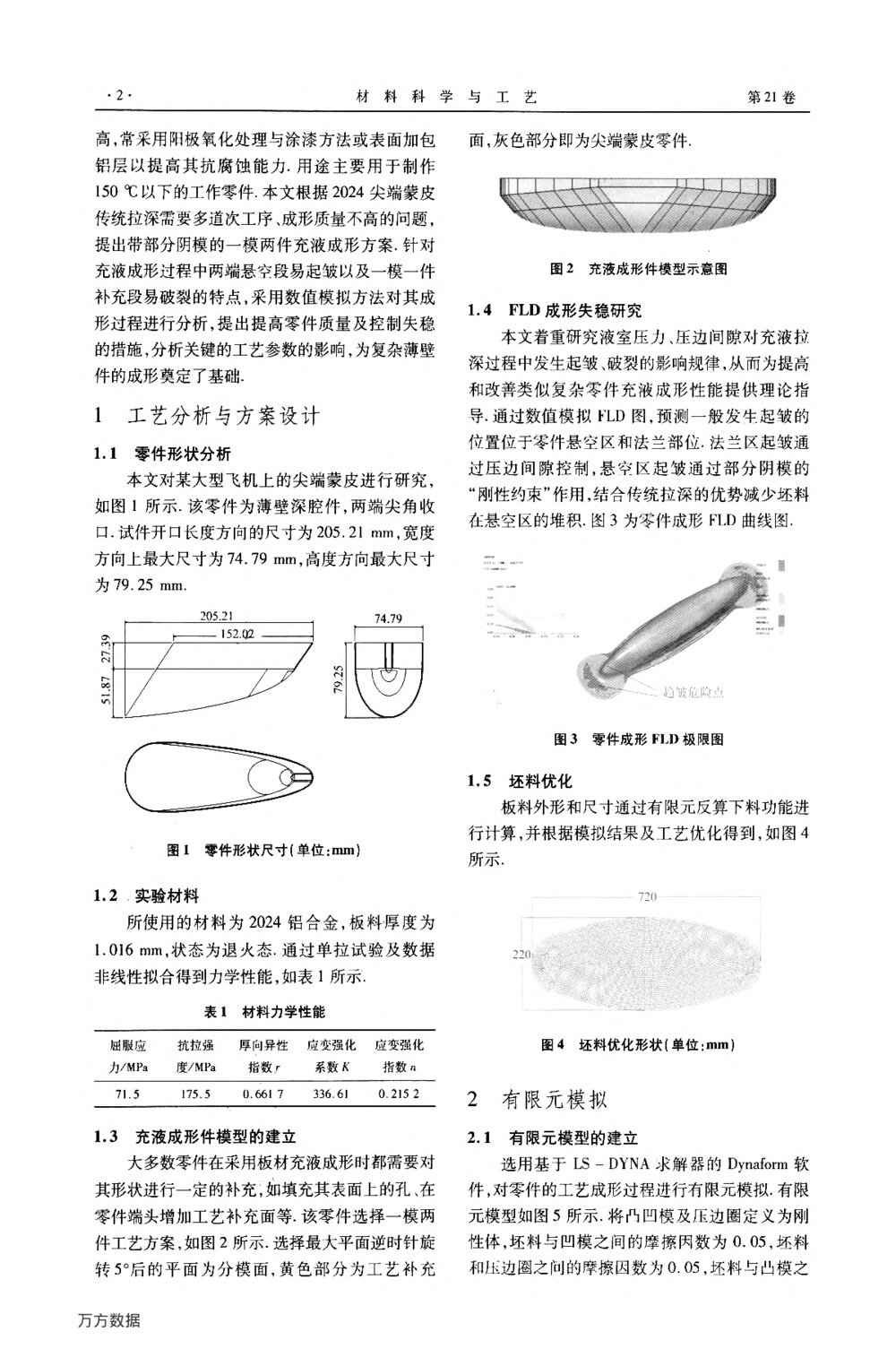
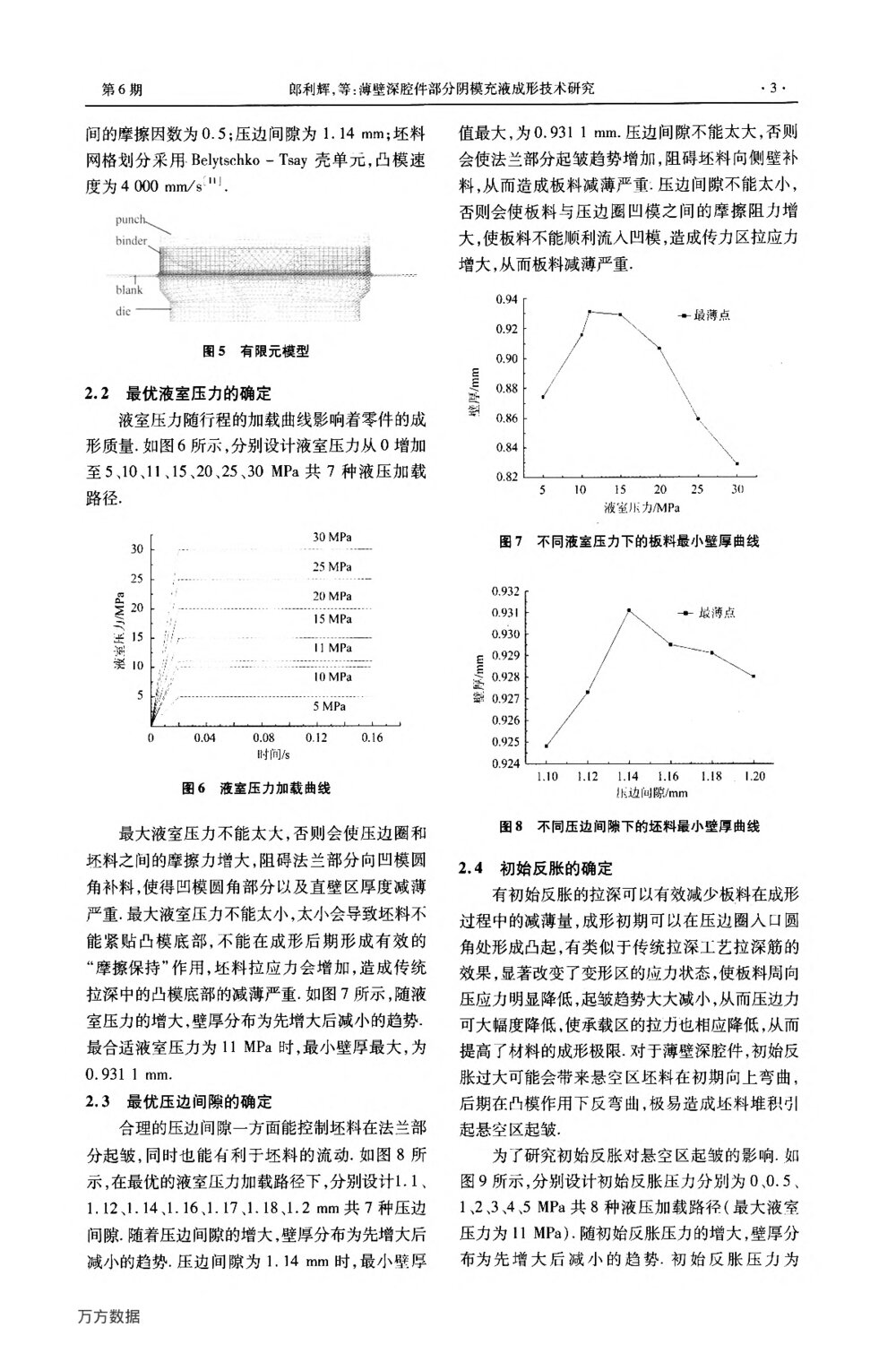
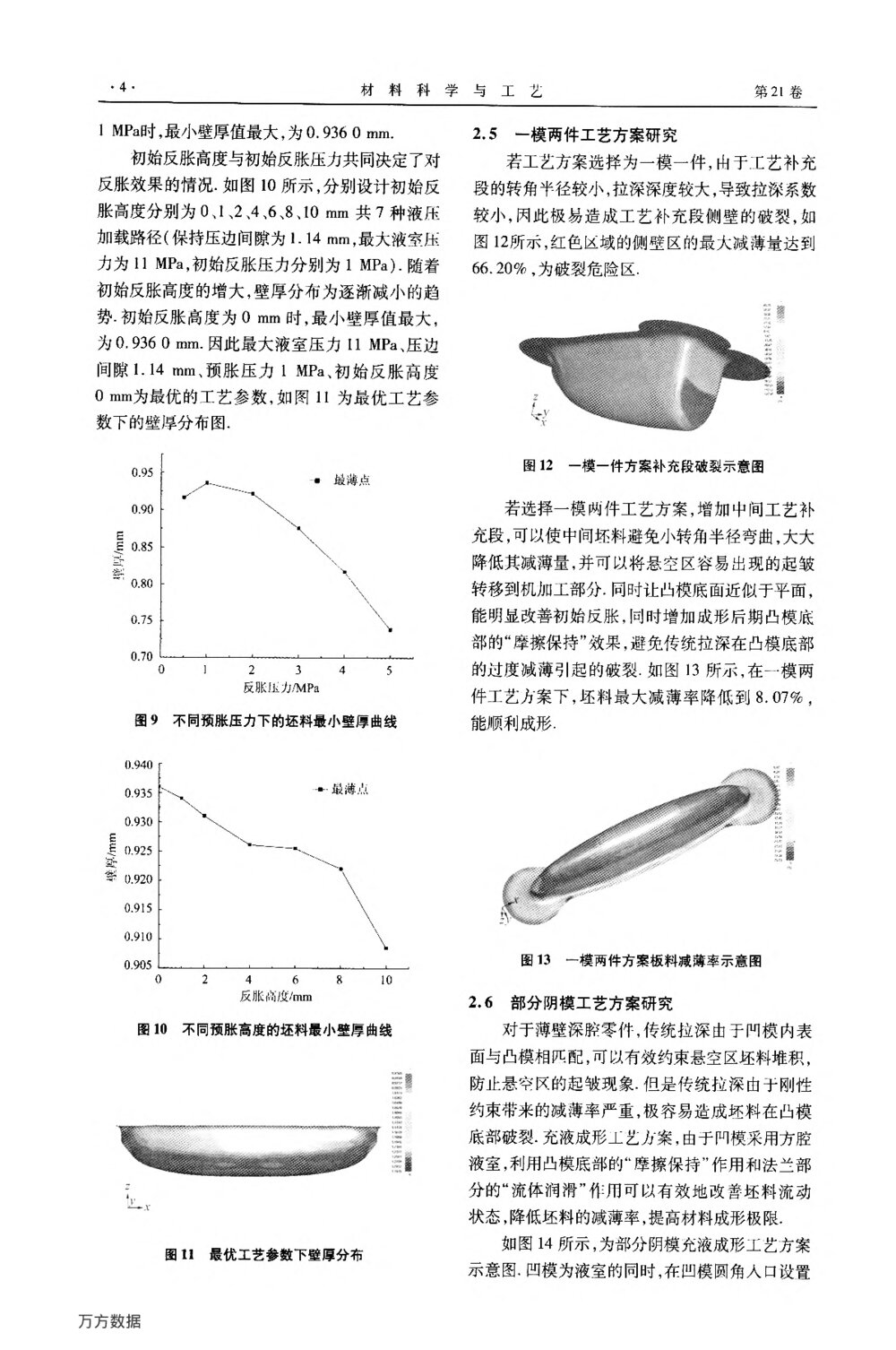
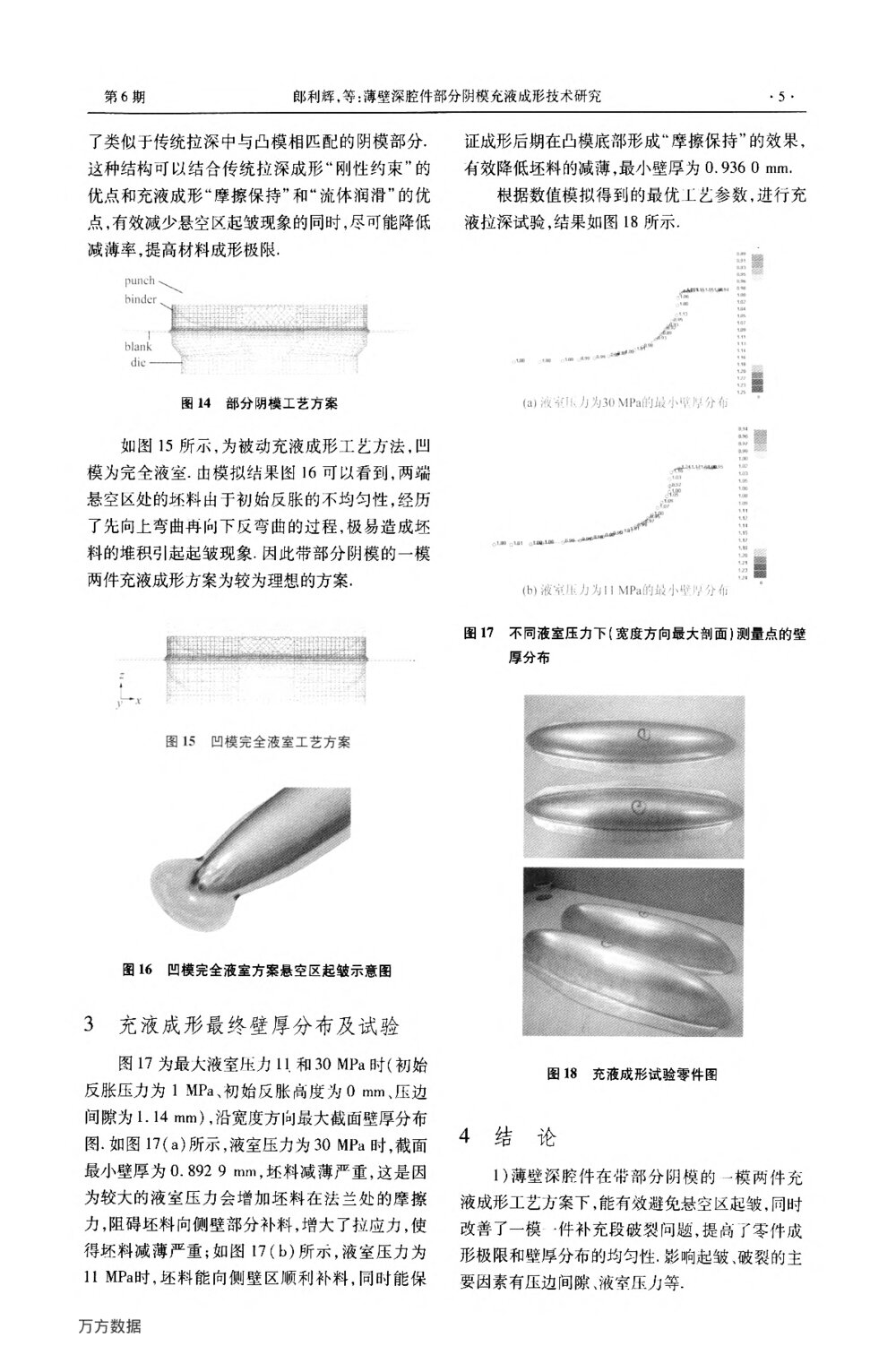

已阅读完毕,您还可以下载文档进行保存
- 1、本文档共6页,内容下载后可编辑。
- 2、本文档内容版权归属内容提供方,所产生的收益全部归内容提供方所有。如果您对本文有版权争议,可选择认领。
- 3、本文档由用户上传,本站不保证质量和数量令人满意,可能有诸多瑕疵,付费之前,请仔细先通过免费阅读内容等途径辨别内容交易风险。如存在严重挂羊头卖狗肉之情形,可联系本站下载客服投诉处理。
第21卷第6期2013年12月材料科学与工艺MATERIALSSCIENCE&TECHNOLOGYV01.2lNo.6Dee.2013薄壁深腔件部分阴模充液成形技术研究郎利辉1,许诺1,王永铭1,袁超1,徐应强2,杨志恒2(1.北京航空航天大学机械工程与自动化学院,北京100191;2.中国商飞一上海飞机制造有限公司钣金厂,上海200436)摘要:充液成形技术能有效解决复杂零件的成形问题.针对某飞机薄壁深腔蒙皮常规拉深成形需要多道次成形、成形质量差的问题,通过分析充液成形过程中易出现的失稳,设计了带部分阴模的一模两件充液成形的技术方案.结合数值模拟,对薄壁深腔件充液成形过程中出现的悬空区失稳形式进行了研究,优化了液室压力加载曲线、压边间隙、初始反胀压力等工艺参数.结果表明,薄壁深腔件在带部分阴模的一模两件的工艺方案下,能有效避免悬空区的起皱,同时改善了一模一件补充段的破裂问题,提高了零件成形极限和壁厚分布的均匀性.关键词:薄壁深腔件;充液成形;一模两件;部分阴模;数值模拟中图分类号:TG394文献标志码:A———文章编号:10050299(2013)06000106Researchonfailurecontrolofhydroformingforthin-walledanddeepcavitycomponentsLANG—Lihui1,XUNu01,WANGYong.min91,YUANCha01,XUYing.qian92,YANGZhi.hen92(1.SchoolofMechanicalEngineeringandAutomation,BeihangUniversity,Beijing100191,China;2.SheetMetalFactory,ShanghaiAircraftManufacturingCorporation,Shanghai200436,China)Abstract:Hydroformingcaneffectivelysovletheformingproblemofcomplicatedcomponents.Aimingatthedifficultyofone--stageformingproblemandpoorformingqualityforcommondeepdrawingofanariplanethin・-walledanddeepcavitycoatingcomponent,hydroformingofdouble-cavitywith—partialdieproposalisdesignedbyanalysisingdefectsduringhydroforming.Combinedwithnumericalsimulation,defectsofnoncontactregionduringcoatingcomponentformingarestudied.Cavitypressureloadingpath,blankholdergap,prebulgepressureandprebulgeheightarealsooptimized.Theresultsshowintheprocessschemofdouble-cavitywithpartial-die,noncontactregionwrinkleandsupplymentsegmentfractureofone-cavityprocesssehemcanbeavoided,whileforminglimitandtheuniformityofthicknesscanbeenhanced.Key—words:thinwalledanddeepcavity—components;hydroforming;partialdie;double-cavity;numericalsimulation飞机结构件中有许多复杂的零件,尤其是薄壁深腔、曲面变化大的蒙皮件,目前这类零件多采用传统拉深的方法成形,存在着需要多道次成形、…成形质量差的问题.近些年,液压机械拉深、周‘向液压充液拉深2。、充液拉深卜6『、热态介质充液——收稿日期:20120905.基金项目:国家自然科学基金资助项目(51175024);科技部国际合作项目(¥2012GR0615).作者简介:郎利辉(1970一),男,教授,博士生导师.通信作者:郎利辉,E-mail:lang@buaa.edu.cn.’’拉深"o和液体凸模主动拉深81叫等技术得到了迅速发展.因此,将充液拉深这一工艺技术引入到飞机复杂钣金件成形制造中,掌握薄壁深腔件充液拉深过程的变形规律与失稳形式,解决其成形质量问题,是航空零件制造中的一个新方向.——2024铝合金属AlCuMg系铝合金,是一种高强度硬铝,可进行热处理强化.在淬火和新淬火状态下塑性中等,点焊焊接良好,用气焊时有形成晶间裂纹的倾向,合金在淬火和冷作硬化后其可切削性能尚好.退火后可切削性低抗腐蚀性不万方数据・2・材料科学与工艺第21卷高,常采用阳极氧化处理与涂漆方法或表面加包铝层以提高其抗腐蚀能力.用途主要用于制作℃150以下的工作零件.本文根据2024尖端蒙皮传统拉深需要多道次工序、成形质量不高的问题,提出带部分阴模的一模两件充液成形方案.针对充液成形过程中两端悬空段易起皱以及一模一件补充段易破裂的特点,采用数值模拟方法对其成形过程进行分析,提出提高零件质量及控制失稳的措施,分析关键的工艺参数的影响,为复杂薄壁件的成形奠定了基础.1工艺分析与方案设计1.1零件形状分析本文对某大型飞机上的尖端蒙皮进行研究,如图1所示.该零件为薄壁深腔件,两端尖角收口.试件开口长度方向的尺寸为205.2lmm,宽度方向上最大尺寸为74.79mm,高度方向最大尺寸为79.25mm.74.79———————————P1图1零件形状尺寸(单位_"nlln)1.2.实验材料所使用的材料为2024铝合金,板料厚度为1.016mm,状态为退火态.通过单拉试验及数据非线性拟合得到力学性能,如表1所示.表1材料力学性能1.3充液成形件模型的建立大多数零件在采用板材充液成形时都需要对其形状进行一定的补充,如填充其表面上的孑L、在零件端头增加工艺补充面等.该零件选择一模两件工艺方案,如图2所示.选择最大平面逆时针旋转5。后的平面为分模面,黄色部分为工艺补充面,灰色部分即为尖端蒙皮零件图2充液成形件模型示意图1.4FLD成形失稳研究本文着重研究液室压力、压边间隙对充液拉深过程中发生起皱、破裂的影响规律,从而为提高和改善类似复杂零件充液成形性能提供理论指导.通过数值模拟FLD图,预测一般发生起皱的位置位于零件悬空区和法兰部位.法兰区起皱通过压边间隙控制,悬空区起皱通过部分阴模的“”刚性约束作用,结合传统拉深的优势减少坯料在悬空区的堆积.图3为零件成形FLD曲线图.图3零件成形FLD极限图1.5坯料优化板料外形和尺寸通过有限元反算下料功能进行计算,并根据模拟结果及工艺优化得到,如图4所示.图4坯料优化形状(单位:mill)2有限元模拟2.1有限元模型的建立—选用基于LSDYNA求解器的Dynaform软件,对零件的工艺成形过程进行有限元模拟.有限元模型如图5所示.将凸凹模及压边圈定义为刚性体,坯料与凹模之间的摩擦因数为0.05,坯料和压边圈之间的摩擦因数为0.05,坯料与凸模之万方数据第6期郎利辉,等:薄壁深腔件部分阴模充液成形技术研究间的摩擦因数为0.5;压边间隙为1.14mm;坯料—网格划分采甩BelytschkoTsay壳单元,凸模速度为4000mm/s【11].叫眦1\binder图5有限元模型2.2最优液室压力的确定液室压力随行程的加载曲线影响着零件的成形质量.如图6所示,分别设计液室压力从0增加至5、10、11、15、20、25、30MPa共7种液压加载路径.图6液室压力加载曲线最大液室压力不能太大,否则会使压边圈和坯料之间的摩擦力增大,阻碍法兰部分向凹模圆角补料,使得凹模圆角部分以及直壁区厚度减薄严重.最大液室压力不能太小,太小会导致坯料不能紧贴凸模底部,不能在成形后期形成有效的“”摩擦保持作用,坯料拉应力会增加,造成传统拉深中的凸模底部的减薄严重.如图7所示,随液室压力的增大,壁厚分布为先增大后减小的趋势.最合适液室压力为11MPa时,最小壁厚最大,为0.9311mm.2.3最优压边间隙的确定合理的压边间隙一方面能控制坯料在法兰部分起皱,同时也能有利于坯料的流动.如图8所示,在最优的液室压力加载路径下,分别设计1.1、1.12、1.14、1.16、1.17、1.18、1.2mm共7种压边间隙.随着压边间隙的增大,壁厚分布为先增大后减小的趋势.压边间隙为1.14mm时,最小壁厚值最大,为0.9311mm.压边间隙不能太大,否则会使法兰部分起皱趋势增加,阻碍坯料向侧壁补料,从而造成板料减薄严重.压边间隙不能太小,否则会使板料与压边圈凹模之间的摩擦阻力增大,使板料不能顺利流入凹模,造成传力区拉应力增大,从而板料减薄严重.E£蛩剖图7不同液室压力下的板料最小壁厚曲线图8不同压边间隙下的坯料最小壁厚曲线2.4初始反胀的确定有初始反胀的拉深可以有效减少板料在成形过程中的减薄量,成形初期可以在压边圈入口圆角处形成凸起,有类似于传统拉深工艺拉深筋的效果,显著改变了变形区的应力状态,使板料周向压应力明显降低,起皱趋势大大减小,从而压边力可大幅度降低,使承载区的拉力也相应降低,从而提高了材料的成形极限.对于薄壁深腔件,初始反胀过大可能会带来悬空区坯料在初期向上弯曲,后期在凸模作用下反弯曲,极易造成坯料堆积引起悬空区起皱.为了研究初始反胀对悬空区起皱的影响.如图9所示,分别设计初始反胀压力分别为0、0.5、1、2、3、4、5MPa共8种液压加载路径(最大液室压力为11MPa).随初始反胀压力的增大,壁厚分布为先增大后减小的趋势.初始反胀压力为万方数据材料科学与工艺第21卷1MPa时,最小壁厚值最大,为0.9360mm.初始反胀高度与初始反胀压力共同决定了对反胀效果的情况.如图10所示,分别设计初始反胀高度分别为0、1、2、4、6、8、10mm共7种液压加载路径(保持压边间隙为1.14mm,最大液室压力为1lMPa,初始反胀压力分别为1MPa).随着初始反胀高度的增大,壁厚分布为逐渐减小的趋势.初始反胀高度为0mm时,最小壁厚值最大,为0.9360mm.因此最大液室压力11MPa、压边间隙1.14mm、预胀压力1MPa、初始反胀高度0mm为最优的工艺参数,如图1I为最优工艺参数下的壁厚分布图.图9不同预胀压力下的坯料最小壁厚曲线图10不同预胀高度的坯料最小壁厚曲线图1l最优工艺参数下壁厚分布薹囊墓拳羞薹i2.5一模两件工艺方案研究若工艺方案选择为一模一件,由于工艺补充段的转角半径较小,拉深深度较大,导致拉深系数较小,因此极易造成工艺补充段侧壁的破裂,如图12所示,红色区域的侧壁区的最大减薄量达到66.20%,为破裂危险区.雾饕图12一模一件方案补充段破裂示意图若选择一模两件工艺方案,增加中间工艺补充段,可以使中间坯料避免小转角半径弯曲,大大降低其减薄量,并可以将悬空区容易出现的起皱转移到机加工部分.同时让凸模底面近似于平面,能明显改善初始反胀,同时增加成形后期凸模底“”部的摩擦保持效果,避免传统拉深在凸模底部的过度减薄引起的破裂.如图13所示,在一模两件工艺方案下,坯料最大减薄率降低到8.07%,能顺利成形.图13一模两件方案板料减薄率示意图2.6部分阴模工艺方案研究对于薄壁深腔零件,传统拉深由于凹模内表面与凸模相匹配,可以有效约束悬空区坯料堆积,防止悬空区的起皱现象.但是传统拉深由于刚性约束带来的减薄率严重,极容易造成坯料在凸模底部破裂.充液成形工艺方案,由于凹模采用方腔“”液室,利用凸模底部的摩擦保持作用和法兰部“”分的流体润滑作用可以有效地改善坯料流动状态,降低坯料的减薄率,提高材料成形极限.如图14所示,为部分阴模充液成形工艺方案示意图.凹模为液室的同时,在凹模圆角入口设置万方数据第6期郎利辉,等:薄壁深腔件部分阴模充液成形技术研究了类似于传统拉深中与凸模相匹配的阴模部分.“”这种结构可以结合传统拉深成形刚性约束的“”“”优点和充液成形摩擦保持和流体润滑的优点,有效减少悬空区起皱现象的同时,尽可能降低减薄率,提高材料成形极限.““p。h\binder,鼍蠹蠢篱鏊鞠blank氅◆1。?穸——’die零二’。蔓图14部分阴模工艺方案如图15所示,为被动充液成形工艺方法,凹模为完全液室.由模拟结果图16可以看到,两端悬空区处的坯料由于初始反胀的不均匀性,经历了先向上弯曲再向下反弯曲的过程,极易造成坯料的堆积引起起皱现象.因此带部分阴模的一模两件充液成形方案为较为理想的方案.图15凹模完全液室工艺方案图16凹模完全液室方案悬空区起皱示意图3充液成形最终壁厚分布及试验图17为最大液室压力11.和30MPa时(初始反胀压力为1MPa、初始反胀高度为0mm、压边间隙为1.14mm),沿宽度方向最大截面壁厚分布图.如图17(a)所示,液室压力为30MPa时,截面最小壁厚为0.8929mm,坯料减薄严重,这是因为较大的液室压力会增加坯料在法兰处的摩擦力,阻碍坯料向侧壁部分补料,增大了拉应力,使得坯料减薄严重;如图17(b)所示,液室压力为1lMPaB寸,坯料能向侧壁区顺利补料,同时能保“”证成形后期在凸模底部形成摩擦保持的效果,有效降低坯料的减薄,最小壁厚为0.9360mm.根据数值模拟得到的最优工艺参数,进行充液拉深试验,结果如图18所示.■“…””“n:1】:"”∥。㈨……”“…。。。。I。。。一t!!』¨』纛嚣_-蛊(:¨,,o.1∥“f㈣1\呲h、-.,??7””f俨B1m-搿曼翼油图17不同液室压力下(宽度方向最大剖面)测量点的壁厚分布图18充液成形试验零件图4结论1)薄壁深腔件在带部分阴模的一模两件充液成形工艺方案下,能有效避免悬空区起皱,同时改善了一模一件补充段破裂问题,提高了零件成形极限和壁厚分布的均匀性.影响起皱、破裂的主要因素有压边间隙、液室压力等.万方数据・6・材料科学与工艺第21卷2)适当的压边间隙除了能抑制法兰起皱,也能防止太小造成侧壁区减薄破裂,优化的压边间隙为1.14mm.通过对薄壁深腔件充液成形模拟,得到的最优液室压力为11MPa,坯料能够顺利成形且壁厚均匀;最优初始反胀压力为1MPa,初始反胀高度为0mm.在数值模拟优化的参数下,进行了充液成形试验,得到了悬空区表面质量高的零件.参考文献:[1]BECKERHJ,BENSMANG.Furtherdevelopmentinhydromechanicaldeepdrawing[C3//DevelopmentsintheDrawingsofMetalsonMetalSocietyofLondon.—[S.1.]:[S.n.],1983:272278.[2]NAKAMURAK,NAKAGAWAT.SheetmetalformingwithhydrauliccounterpressureinJapan[J].Annal—CIRP,1987,36:191194.[3]LANG—Lihui,ZHANG—Shutong,LITao,et—a1.Investigationintotheformingofcomplicatedpartswithpoorformabilitymaterialsincold/warmsheethydroforming[J].TubeHydroformingTechnology,Minemachi:—[S.n.],2007:171180.[4]LANG—Lihui,DANCKERTJ,NIEISENKB.Studyonhydromechanicaldeepdrawingwithuniformpressureontotheblank[J].InternationalJournalofMachine—Tools&Maufacture,2004,44:495502.[5]AMINOH,NAKAMURAK,NAKAGAWAT.Counter・pressuredeepdrwinganditsapplicationintheformingofautomobileparts[J].JournalofMaterialsProcessing—Technology,1990,23:243265.[6]LARSENB.Hydromechanicalformingofsheetmetal[J].SheetMetal—Industries,1997:162168.[7]李涛,郎利辉,安冬洋.复杂薄壁零件板多级充液成形及过程数值模拟[J].北京航空航天大学学报,—2007,33(7):830832.[8]郎利辉,王永铭.复杂薄壁微小截面环形件的充液—成形技术研究[J].锻压技术,2011,36(2):3438.[9]刘合军,郎利辉.高强度铝合金板材的温热介质充液成形研究[J].塑性工程学报,2009,16(1):—3236.[10]杨踊,孙淑铎,刘慧茹.航空发动机复杂型面罩子钣充液成形技术[J].航空制造技术,2010,1(1):9l一99.[11]项辉宇,冷崇杰,张媛.覆盖件成形缺陷的数值仿真实例分析[J].计算机仿真,2009,26(12):—226229.(编辑程利冬)万方数据
您可能关注的文档
- “离位”增韧复合材料准静态压入损伤特性研究.pdf
- “神舟七号”飞船舱外航天服防护头盔组件的研制.pdf
- “十二五”复合材料发展重点和方向解读.pdf
- “珠串”堆叠超结构的介孔铁酸锌的制备与表征.pdf
- (001)应变对正交相Ca2 P0.25 Si0.75能带结构及光学性质的影响.pdf
- 0.8设计系数用X80管线钢在近中性pH溶液中的应力腐蚀开裂行为.pdf
- 0.20mm CGO硅钢高温退火Goss晶粒起源及异常长大行为研究.pdf
- 0Cr16Ni5Mo低碳马氏体不锈钢的热变形行为及其热加工图.pdf
- 0Cr17Ni4Cu4Nb钢制螺钉断裂原因分析.pdf
- 1.5MW风机叶片模具加热工艺研究与技术创新.pdf
- 1.5MW风机叶片VARI工艺模拟分析及验证.pdf
- 2.5维机织复合材料低速冲击性能研究.pdf
- 2.25Cr-1Mo钢后续热处理中的磷偏聚行为.pdf
- 2A50锻铝三点弯曲试验与高分辨率CT成像分析.pdf
- 2A12与2A11铝合金超声波焊接工艺与组织研究.pdf
- 2MW风机复合材料叶片材料及工艺研究.pdf
- 3Cr2W8V模具钢激光表面相变硬化层性能的研究.pdf
- 3D打印技术及先进应用研究进展.pdf
- 3D打印技术研究现状和关键技术.pdf
- 5%鱼藤酮悬浮剂的研制.pdf

- 一夕落阳
- 该用户很懒,什么也没介绍
相关文档
- “离位”增韧复合材料准静态压入损伤特性研究.pdf2021-11-235页
- “神舟七号”飞船舱外航天服防护头盔组件的研制.pdf2021-11-233页
- “十二五”复合材料发展重点和方向解读.pdf2021-11-232页
- “珠串”堆叠超结构的介孔铁酸锌的制备与表征.pdf2021-11-235页
- (001)应变对正交相Ca2 P0.25 Si0.75能带结构及光学性质的影响.pdf2021-11-236页
- 0.8设计系数用X80管线钢在近中性pH溶液中的应力腐蚀开裂行为.pdf2021-11-237页
- 0.20mm CGO硅钢高温退火Goss晶粒起源及异常长大行为研究.pdf2021-11-237页