- 文档大小:729.82 KB
- 文档格式:pdf
- 约 7页
- 2022-03-26 发布
- 举报
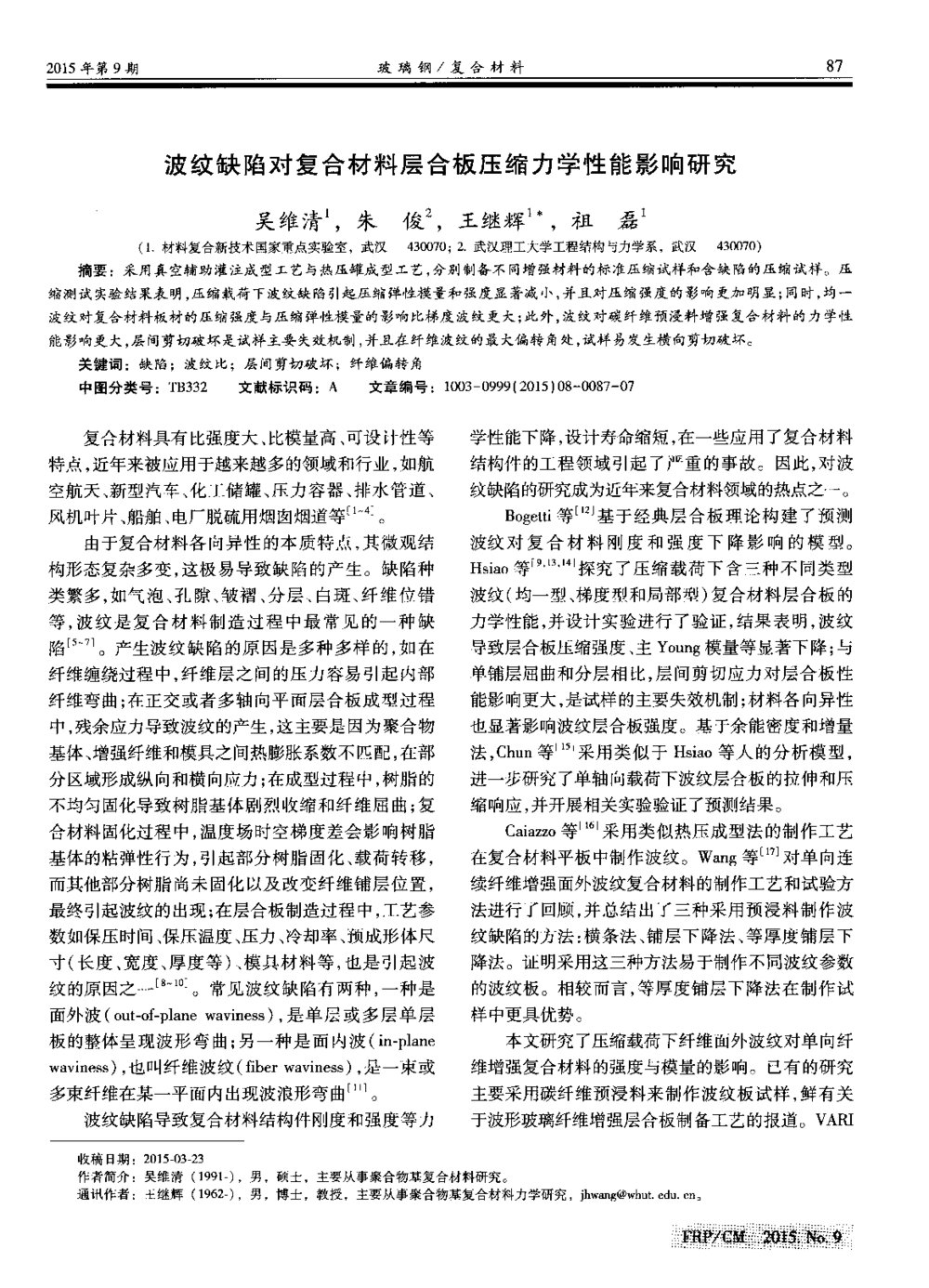
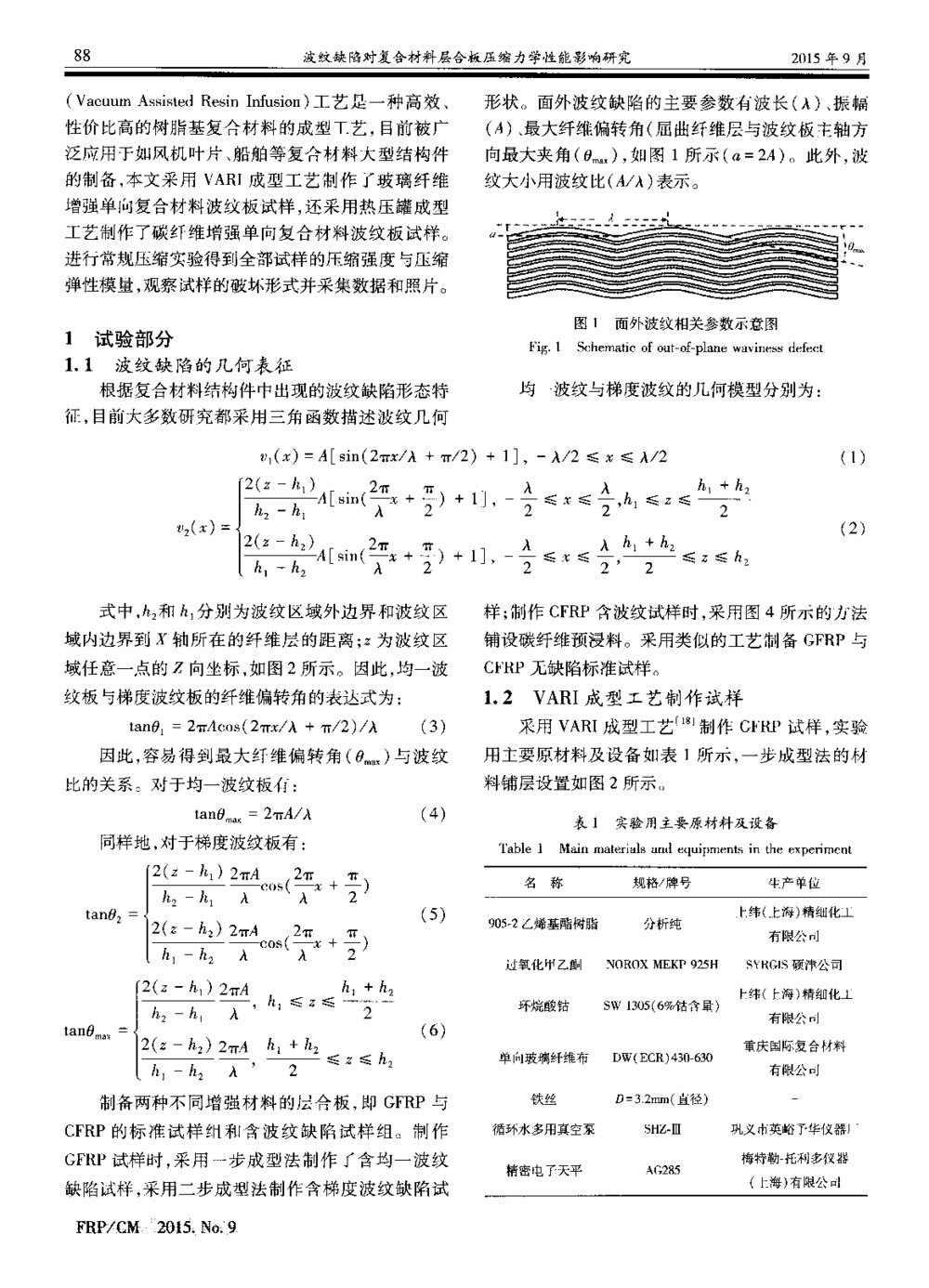
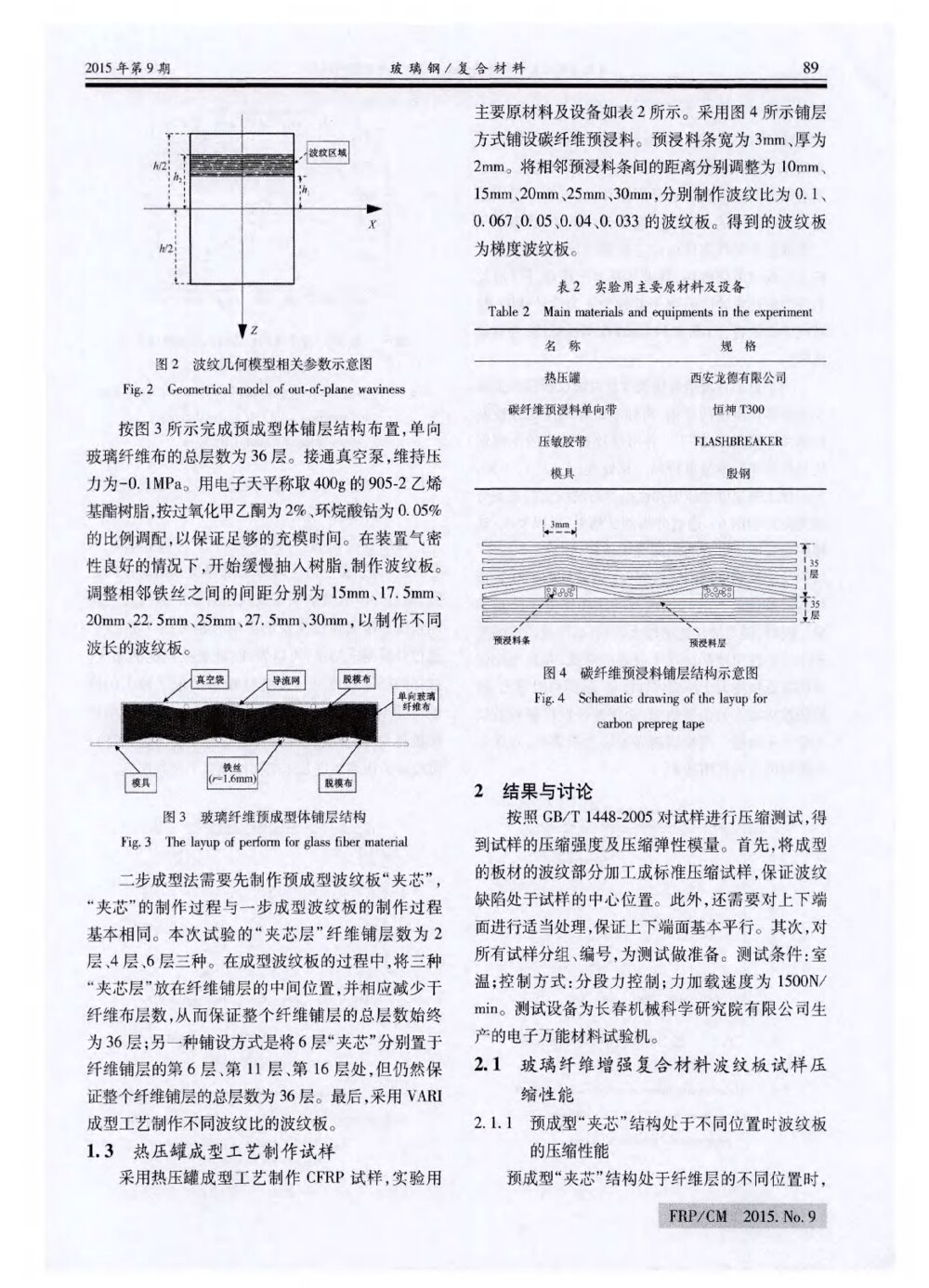
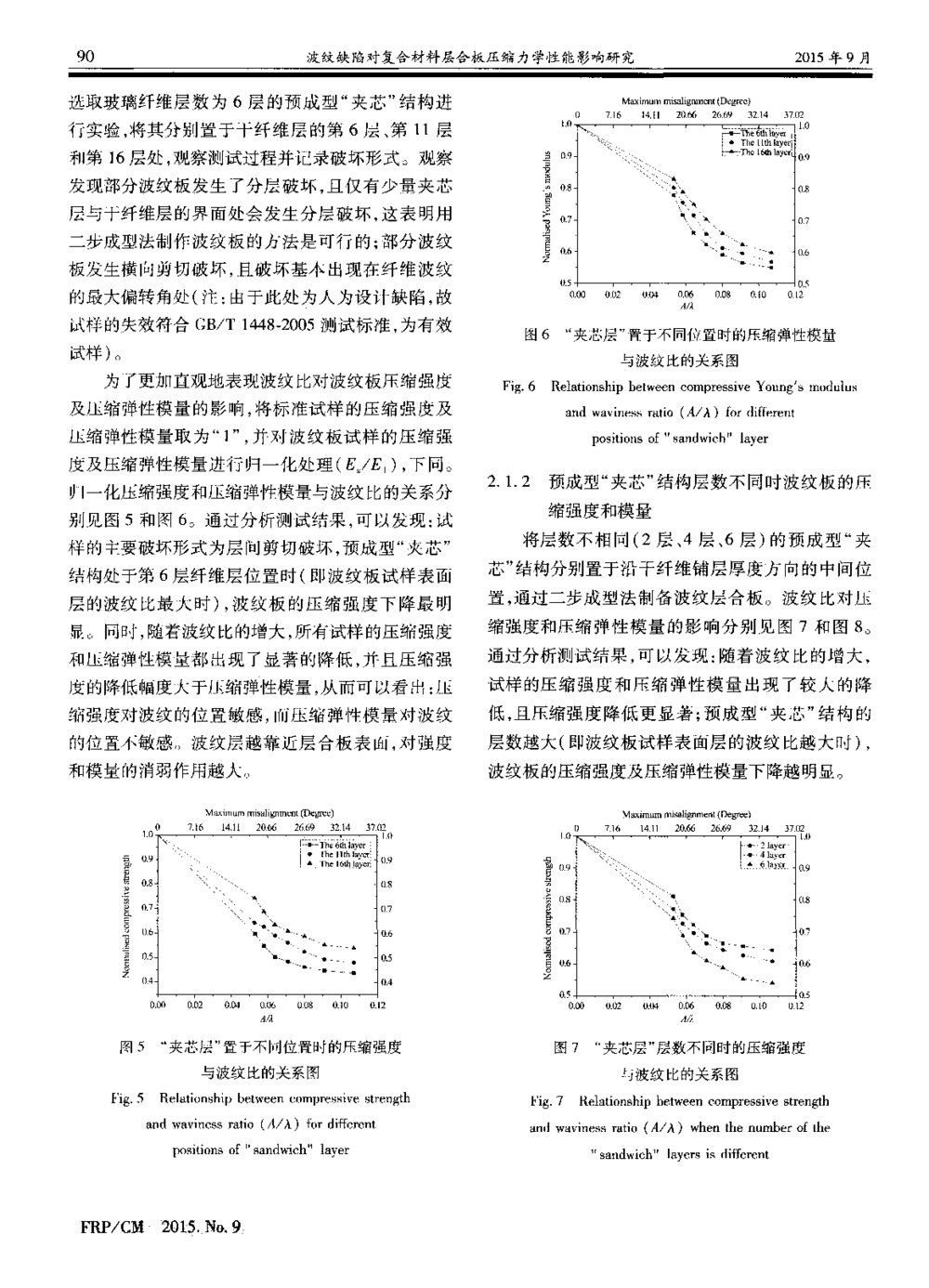
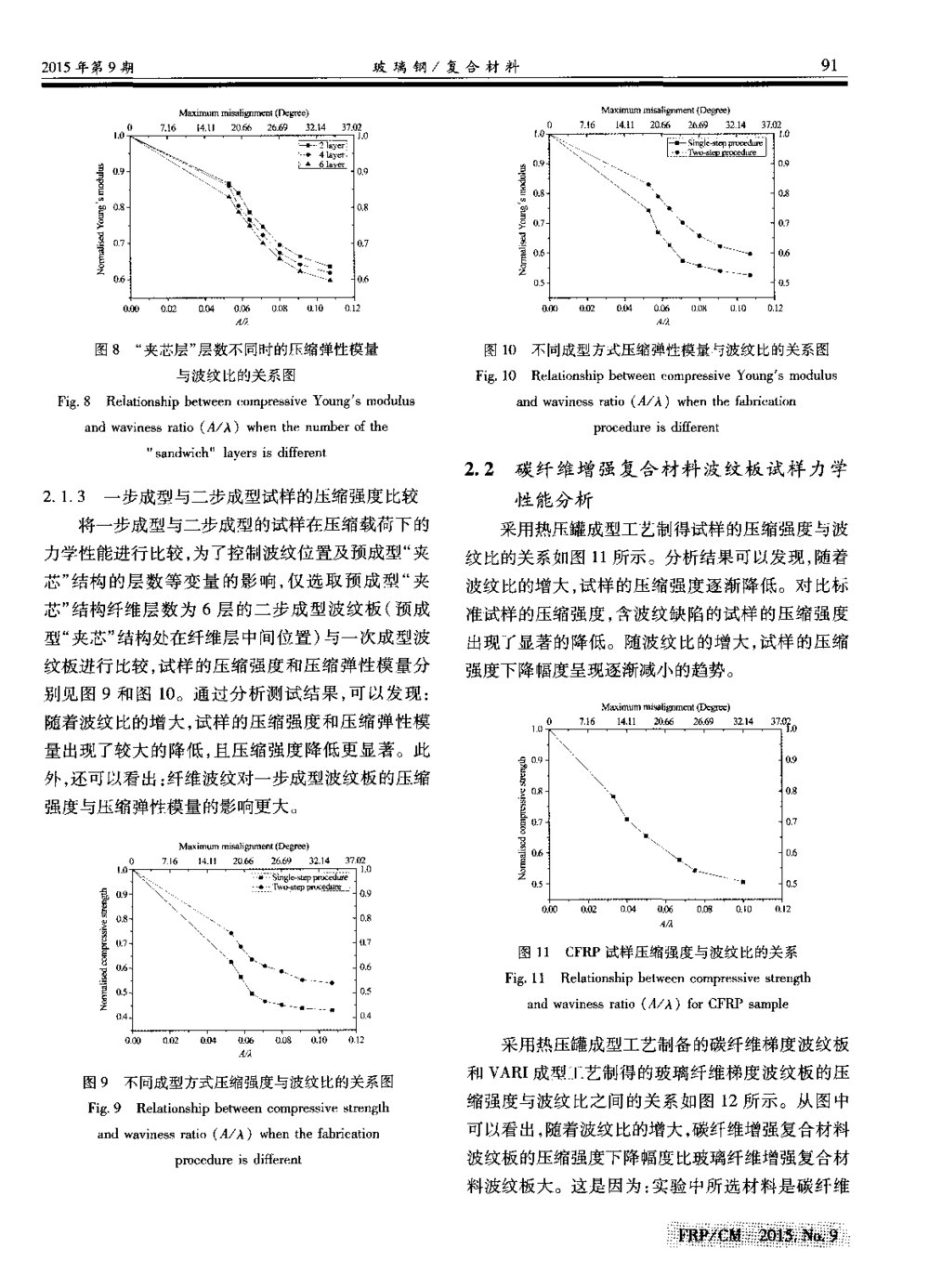
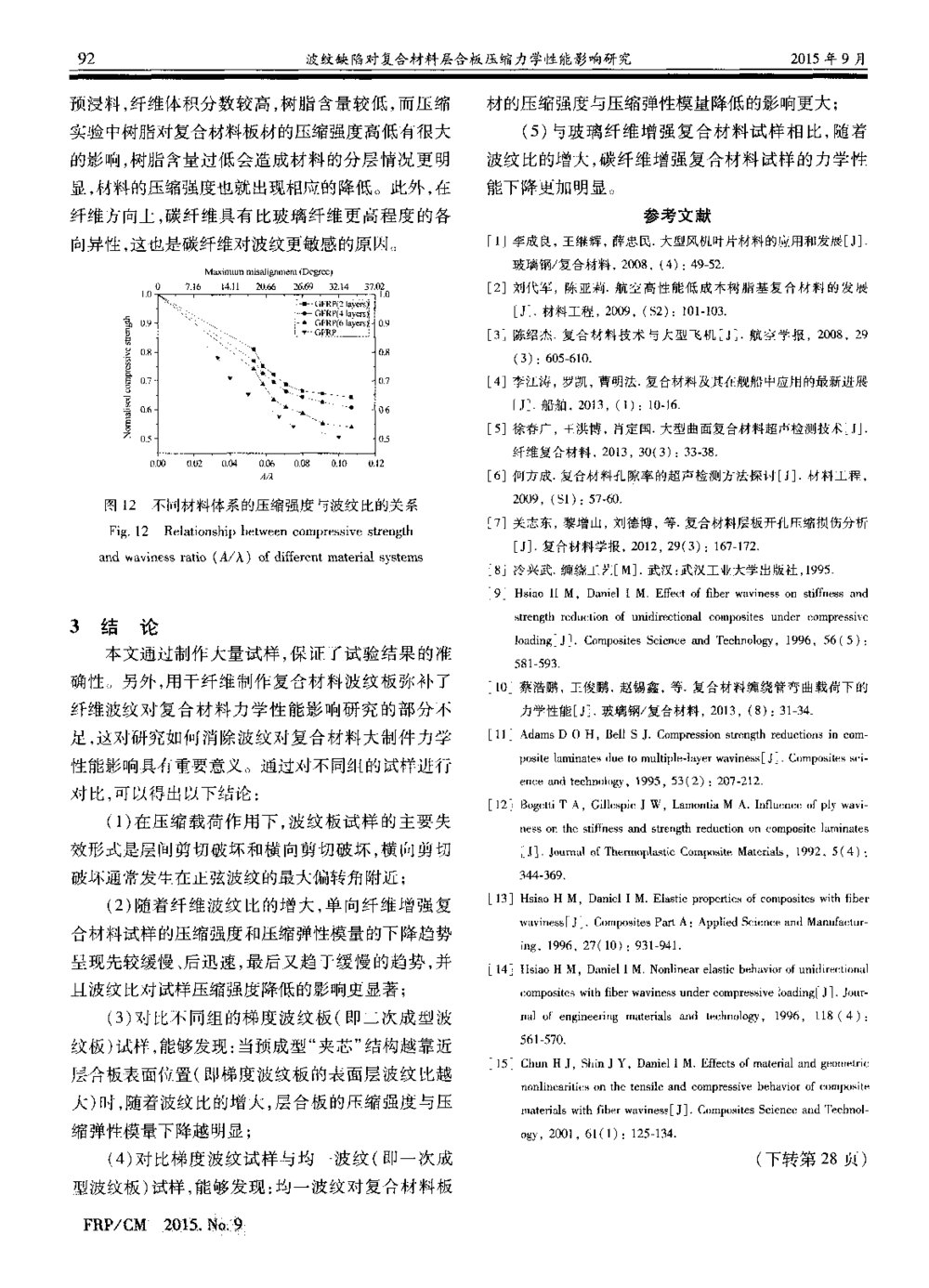
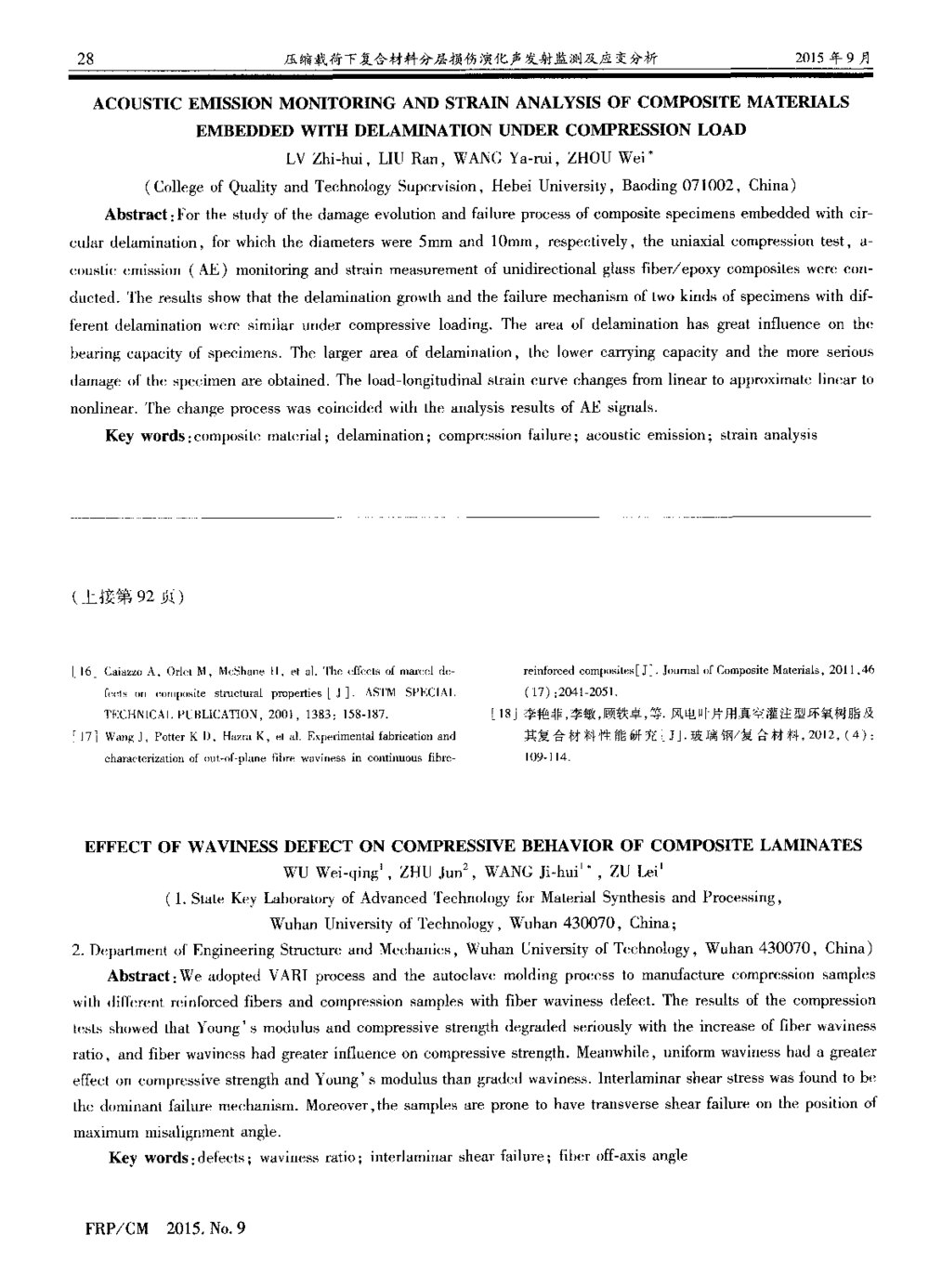
已阅读完毕,您还可以下载文档进行保存
- 1、本文档共7页,内容下载后可编辑。
- 2、本文档内容版权归属内容提供方,所产生的收益全部归内容提供方所有。如果您对本文有版权争议,可选择认领。
- 3、本文档由用户上传,本站不保证质量和数量令人满意,可能有诸多瑕疵,付费之前,请仔细先通过免费阅读内容等途径辨别内容交易风险。如存在严重挂羊头卖狗肉之情形,可联系本站下载客服投诉处理。
2015年第9期玻璃钢/复合材料87波纹缺陷对复合材料层合板压缩力学性能影响研究吴维清,朱俊,王继辉,祖磊(1.材料复合新技术国家重点实验室,武汉430070;2.武汉理工大学工程结构与力学系,武汉430070)摘要:采用真空辅助灌注成型工艺与热压罐成型工艺,分别制备不同增强材料的标准压缩试样和含缺陷的压缩试样。压缩测试实验结果表明,压缩载荷下波纹缺陷引起压缩弹性模量和强度显著减小,并且对压缩强度的影响更加明显;同时,均一波纹对复合材料板材的压缩强度与压缩弹性模量的影响比梯度波纹更大;此外,波纹对碳纤维预浸料增强复合材料的力学性能影响更大,层间剪切破坏是试样主要失效机制,并且在纤维波纹的最大偏转角处,试样易发生横向剪切破坏。关键词:缺陷;波纹比;层间剪切破坏;纤维偏转角中图分类号:TB332文献标识码:A———文章编号:10030999(2015)08008707复合材料具有比强度大、比模量高、可设计性等特点,近年来被应用于越来越多的领域和行业,如航空航天、新型汽车、化工储罐、压力容器、排水管道、风机叶片、船舶、电厂脱硫用烟囱烟道等¨J。由于复合材料各向异性的本质特点,其微观结构形态复杂多变,这极易导致缺陷的产生。缺陷种类繁多,如气泡、孔隙、皱褶、分层、白斑、纤维位错等,波纹是复合材料制造过程中最常见的一种缺陷[5-。产生波纹缺陷的原因是多种多样的,如在纤维缠绕过程中,纤维层之间的压力容易引起内部纤维弯曲;在正交或者多轴向平面层合板成型过程中,残余应力导致波纹的产生,这主要是因为聚合物基体、增强纤维和模具之间热膨胀系数不匹配,在部分区域形成纵向和横向应力;在成型过程中,树脂的不均匀固化导致树脂基体剧烈收缩和纤维屈曲;复合材料固化过程中,温度场时空梯度差会影响树脂基体的粘弹性行为,引起部分树脂固化、载荷转移,而其他部分树脂尚未固化以及改变纤维铺层位置,最终引起波纹的出现;在层合板制造过程中,工艺参数如保压时间、保压温度、压力、冷却率、预成形体尺寸(长度、宽度、厚度等)、模具材料等,也是引起波纹的原因之一_8。常见波纹缺陷有两种,一种是—面外波(outof-planewaviness),是单层或多层单层—板的整体呈现波形弯曲;另一种是面内波(inplanewaviness),也叫纤维波纹(fiberwaviness),是一束或多束纤维在某一平面内出现波浪形弯曲¨。波纹缺陷导致复合材料结构件刚度和强度等力学性能下降,设计寿命缩短,在一些应用了复合材料结构件的工程领域引起了严重的事故。因此,对波纹缺陷的研究成为近年来复合材料领域的热点之一。Bogetti等¨基于经典层合板理论构建了预测波纹对复合材料刚度和强度下降影响的模型。Hsiao等',H探究了压缩载荷下含三种不同类型波纹(均一型、梯度型和局部型)复合材料层合板的力学性能,并设计实验进行了验证,结果表明,波纹导致层合板压缩强度、主Young模量等显著下降;与单铺层屈曲和分层相比,层间剪切应力对层合板性能影响更大,是试样的主要失效机制;材料各向异性也显著影响波纹层合板强度。基于余能密度和增量法,Chun等采用类似于Hsiao等人的分析模型,进一步研究了单轴向载荷下波纹层合板的拉伸和压缩响应,并开展相关实验验证了预测结果。Caiazzo等¨刮采用类似热压成型法的制作工艺在复合材料平板中制作波纹。Wang等对单向连续纤维增强面外波纹复合材料的制作工艺和试验方法进行了回顾,并总结出了三种采用预浸料制作波纹缺陷的方法:横条法、铺层下降法、等厚度铺层下降法。证明采用这三种方法易于制作不同波纹参数的波纹板。相较而言,等厚度铺层下降法在制作试样中更具优势。本文研究了压缩载荷下纤维面外波纹对单向纤维增强复合材料的强度与模量的影响。已有的研究主要采用碳纤维预浸料来制作波纹板试样,鲜有关于波形玻璃纤维增强层合板制备工艺的报道。VARI—收稿Et期:201503-23作者简介:吴维清(1991-),男,硕士,主要从事聚合物基复合材料研究。通讯作者:王继辉(1962-),男,博士,教授,主要从事聚合物基复合材料力学研究,jhwang@whut.edu.cn。~0u1月珏强2曩。9_■*,0088波纹缺陷对复合材料层合板压缩力学性能影响研究2015年9月(VacuumAssistedResinInfusion)工艺是一种高效、性价比高的树脂基复合材料的成型工艺,目前被广泛应用于如风机叶片、船舶等复合材料大型结构件的制备,本文采用VARI成型工艺制作了玻璃纤维增强单向复合材料波纹板试样,还采用热压罐成型工艺制作了碳纤维增强单向复合材料波纹板试样。进行常规压缩实验得到全部试样的压缩强度与压缩弹性模量,观察试样的破坏形式并采集数据和照片。l试验部分1.1波纹缺陷的几何表征根据复合材料结构件中出现的波纹缺陷形态特征,目前大多数研究都采用三角函数描述波纹几何形状。面外波纹缺陷的主要参数有波长(A)、振幅(A)、最大纤维偏转角(屈曲纤维层与波纹板主轴方向最大夹角(0),如图1所示(0=2A)。此外,波纹大小用波纹比(A/A)表示。图1面外波纹相关参数示意图—Fig.1Schematicofoutof-planewavinessdefect均一波纹与梯度波纹的几何模型分别为:l≤≤()=A[sin(2,rrx/A+盯/2)+1],一A/2A/2(1)-sinc≤≤一A≤≤c+≤≤≤…一拿,式中,^和h分别为波纹区域外边界和波纹区域内边界到轴所在的纤维层的距离;为波纹区域任意一点的z向坐标,如图2所示。因此,均一波纹板与梯度波纹板的纤维偏转角的表达式为:tanOl=2,rrAcos(2,rrx/a+1T/2)/A(3)因此,容易得到最大纤维偏转角(0)与波纹比的关系。对于均一波纹板有:…tanO=2,rrA/A(4)同样地,对于梯度波纹板有:tan0=tanO。l∞‘+)I…c+詈I∞+—2(h1)2,rrAh14-h,___二≤≤—,—2(h,)27rAh+h,,丁≤≤z样;制作CFRP含波纹试样时,采用图4所示的方法铺设碳纤维预浸料。采用类似的工艺制备GFRP与CFRP无缺陷标准试样。1.2VARI成型工艺制作试样采用VARI成型工艺制作GFRP试样,实验用主要原材料及设备如表1所示,一步成型法的材料铺层设置如图2所示。表1实验用主要原材料及设备Table1Mainmaterialsandequipmentsintheexperiment名称规格/牌号生产单位(5)905-2乙烯基酯树脂分析纯(6)制备两种不同增强材料的层合板,即GFRP与CFRP的标准试样组和含波纹缺陷试样组。制作GFRP试样时,采用一步成型法制作了含均一波纹缺陷试样,采用二步成型法制作含梯度波纹缺陷试FRP/CM2O15,No.9过氧化甲乙酮NOROXMEKP925H环烷酸钴SW1305(6%钴含量)单向玻璃纤维布DW(ECR)430-630上纬(上海)精细化工有限公司SYRGIS硕津公司上纬(上海)精细化工有限公司重庆国际复合材料有限公司铁丝D=3.2ram(直径)一循环水多用真空泵ⅢSHZ一巩义市英峪予华仪器厂梅特勒-托利多仪器精密电子天平AG285(上海)有限公司波纹缺陷对复合材料层合板压缩力学性能影响研究“”选取玻璃纤维层数为6层的预成型夹芯结构进行实验,将其分别置于干纤维层的第6层、第11层和第16层处,观察测试过程并记录破坏形式。观察发现部分波纹板发生了分层破坏,且仅有少量夹芯层与干纤维层的界面处会发生分层破坏,这表明用二步成型法制作波纹板的方法是可行的;部分波纹板发生横向剪切破坏,且破坏基本出现在纤维波纹的最大偏转角处(注:由于此处为人为设计缺陷,故试样的失效符合GB/T1448.2005测试标准,为有效试样)。为了更加直观地表现波纹比对波纹板压缩强度及压缩弹性模量的影响,将标准试样的压缩强度及“”压缩弹性模量取为1,并对波纹板试样的压缩强度及压缩弹性模量进行归一化处理(E/E),下同。归一化压缩强度和压缩弹性模量与波纹比的关系分别见图5和图6。通过分析测试结果,可以发现:试“”样的主要破坏形式为层间剪切破坏,预成型夹芯结构处于第6层纤维层位置时(即波纹板试样表面层的波纹比最大时),波纹板的压缩强度下降最明显。同时,随着波纹比的增大,所有试样的压缩强度和压缩弹性模量都出现了显著的降低,并且压缩强度的降低幅度大于压缩弹性模量,从而可以看出:压缩强度对波纹的位置敏感,而压缩弹性模量对波纹的位置不敏感。波纹层越靠近层合板表面,对强度和模量的消弱作用越大。“”图5夹芯层置于不同位置时的压缩强度与波纹比的关系图Fig.5Relationshipbetweencompressivestrengthandwavinessratio(A/A)fordifferent””positionsofsandwichlayerFRP/CM20l5.No.9“”图6夹芯层置于不同位置时的压缩弹性模量与波纹比的关系图Fig.6RelationshipbetweencompressiveYoungSmodulusandwavinessratio(A/A)fordifferent””positionsofsandwichlayer“”2.1.2预成型夹芯结构层数不同时波纹板的压缩强度和模量“将层数不相同(2层、4层、6层)的预成型夹”芯结构分别置于沿干纤维铺层厚度方向的中间位置,通过二步成型法制备波纹层合板。波纹比对压缩强度和压缩弹性模量的影响分别见图7和图8。通过分析测试结果,可以发现:随着波纹比的增大,试样的压缩强度和压缩弹性模量出现了较大的降“”低,且压缩强度降低更显著;预成型夹芯结构的层数越大(即波纹板试样表面层的波纹比越大时),波纹板的压缩强度及压缩弹性模量下降越明显。“”图7夹芯层层数不同时的压缩强度与波纹比的关系图Fig.7Relationshipbetweencompressivestrengthandwavinessratio(A/A)whenthenumberofthe’’”sandwichlayersisdifferent2015年第9期玻璃钢/复合材料91“”图8夹芯层层数不同时的压缩弹性模量与波纹比的关系图Fig.8RelationshipbetweencompressiveYoungSmodulusandwavinessratio(A/A)whenthenumberofthe””sandwichlayersisdifferent2.1.3一步成型与二步成型试样的压缩强度比较将一步成型与二步成型的试样在压缩载荷下的“力学性能进行比较,为了控制波纹位置及预成型夹”“芯结构的层数等变量的影响,仅选取预成型夹”芯结构纤维层数为6层的二步成型波纹板(预成“”型夹芯结构处在纤维层中间位置)与一次成型波纹板进行比较,试样的压缩强度和压缩弹性模量分别见图9和图10。通过分析测试结果,可以发现:随着波纹比的增大,试样的压缩强度和压缩弹性模量出现了较大的降低,且压缩强度降低更显著。此外,还可以看出:纤维波纹对一步成型波纹板的压缩强度与压缩弹性模量的影响更大。图9不同成型方式压缩强度与波纹比的关系图Fig.9Relationshipbetweencompressivestrengthandwavinessratio(A/A)whenthefabricationprocedureisdifferent图10不同成型方式压缩弹性模量与波纹比的关系图Fig.10RelationshipbetweencompressiveYoungSmodulusandwavinessratio(A/a)whenthefabricationprocedureisdifferent2.2碳纤维增强复合材料波纹板试样力学性能分析采用热压罐成型工艺制得试样的压缩强度与波纹比的关系如图11所示。分析结果可以发现,随着波纹比的增大,试样的压缩强度逐渐降低。对比标准试样的压缩强度,含波纹缺陷的试样的压缩强度出现了显著的降低。随波纹比的增大,试样的压缩强度下降幅度呈现逐渐减小的趋势。图11CFRP试样压缩强度与波纹比的关系Fig.11Relationshipbetweencompressivestrengthandwavinessratio(A/A)forCFRPsample采用热压罐成型工艺制备的碳纤维梯度波纹板和VARI成型工艺制得的玻璃纤维梯度波纹板的压缩强度与波纹比之间的关系如图l2所示。从图中可以看出,随着波纹比的增大,碳纤维增强复合材料波纹板的压缩强度下降幅度比玻璃纤维增强复合材料波纹板大。这是因为:实验中所选材料是碳纤维~^%l。嚣:÷_.l,Cl|:m92波纹缺陷对复合材料层合板压缩力学性能影响研究预浸料,纤维体积分数较高,树脂含量较低,而压缩实验中树脂对复合材料板材的压缩强度高低有很大的影响,树脂含量过低会造成材料的分层情况更明显,材料的压缩强度也就出现相应的降低。此外,在纤维方向上,碳纤维具有比玻璃纤维更高程度的各向异性,这也是碳纤维对波纹更敏感的原因。图12不同材料体系的压缩强度与波纹比的关系Fig.12Relationshipbetweencompressivestrengthandwavinessratio(A/A)ofdifferentmaterialsystems3结论本文通过制作大量试样,保证了试验结果的准确性。另外,用干纤维制作复合材料波纹板弥补了纤维波纹对复合材料力学性能影响研究的部分不足,这对研究如何消除波纹对复合材料大制件力学性能影响具有重要意义。通过对不同组的试样进行对比,可以得出以下结论:(1)在压缩载荷作用下,波纹板试样的主要失效形式是层间剪切破坏和横向剪切破坏,横向剪切破坏通常发生在正弦波纹的最大偏转角附近;(2)随着纤维波纹比的增大,单向纤维增强复合材料试样的压缩强度和压缩弹性模量的下降趋势呈现先较缓慢、后迅速,最后又趋于缓慢的趋势,并且波纹比对试样压缩强度降低的影响更显著;(3)对比不同组的梯度波纹板(即二次成型波“”纹板)试样,能够发现:当预成型夹芯结构越靠近层合板表面位置(即梯度波纹板的表面层波纹比越大)时,随着波纹比的增大,层合板的压缩强度与压缩弹性模量下降越明显;(4)对比梯度波纹试样与均一波纹(即一次成型波纹板)试样,能够发现:均一波纹对复合材料板FRP/CM2015,N0i9材的压缩强度与压缩弹性模量降低的影响更大;(5)与玻璃纤维增强复合材料试样相比,随着波纹比的增大,碳纤维增强复合材料试样的力学性能下降更加明显。参考文献[1]李成良,王继辉,薛忠民.大型风机叶片材料的应用和发展[J].—玻璃钢/复合材料,2008,(4):4952.[2]刘代军,陈亚莉.航空高性能低成本树脂基复合材料的发展[J].材料工程,2009,(s2):101-103.[3]陈绍杰.复合材料技术与大型飞机[J].航空学报,2008,29—(3):605610.[4]李江涛,罗凯,曹明法.复合材料及其在舰船中应用的最新进展—[J].船舶,2013,(1):1016.[5]徐春广,王洪博,肖定国.大型曲面复合材料超声检测技术[J].纤维复合材料,2013,30(3):33-38.[6]何方成.复合材料孔隙率的超声检测方法探讨[J].材料工程,—2009,(S1):5760.[7]关志东,黎增山,刘德博,等.复合材料层板开孔压缩损伤分析[J].复合材料学报,2012,29(3):167.172.[8]冷兴武.缠绕工艺[M].武汉:武汉工业大学出版社,1995.[9]HsiaoHM,DanielIM.Effectoffiberwavinessonstiffnessandstrengthreductionofunidirectionalcompositesundercompressiveloading[J].CompositesScienceandTechnology,1996,56(5):581593.[1O]蔡浩鹏,王俊鹏,赵锡鑫,等.复合材料缠绕管弯曲载荷下的—力学性能[J].玻璃钢/复合材料,2013,(8):3134.—[11]AdamsDOH,BellSJ.Compressionstrengthreductionsincom—positelaminatesduetomuhiple-layerwaviness[J].Compositessci—eneeandtechnology,1995,53(2):207212.[12]BogettiTA,GillespieJW,LamontiaMA.Inf—luenceofplywaviflessonthestiffnessandstrengthreductiononcompositelaminateslJ].JournalofThermoplasticCompositeMaterials,1992,5(4):—344369.[13]HsiaoHM,DanielIM.Elasticpropertiesofcompositeswithfiber—waviness[J].CompositesPartA:AppliedScienceandManufacturing,1996,27(10):931-941.[14]HsiaoHM,DanielIM.Nonlinearelasticbehaviorofunidirectionalcompositeswithfiberwavinessundercompressiveloading【J].Jour-nalofengineeringmaterialsandtechnology,1996,118(4):561570.[15]ChunHJ,ShinJY,DanielIM.Effectsofmaterialandgeometricnonlinearitiesonthetensileandcompressivebehaviorofcomposite—nmtcrialswithfiberwaviness[J].CompositesScienceandTechnol—ogy,2001,61(1):125134.(下转第28页)28压缩栽荷下复合材料分层损伤演化声发射监测及应变分析2015年9月ACOUSTICEMISSIONnONITORINGANDSTRAINANALYSISOFCOMPOSITEMATERIALSEMBEDDEDWITHDELAMINATIONUNDERCOMPRESSIoNLoAD—LVZhi.hui,LIURan,WANGYarui,ZHOUWei(CollegeofQualityandTechnologySupervision,HebeiUniversity,Baoding071002,China)—Abstract:Forthestudyofthedamageevolutionandfailureprocessofcompositespecimensembeddedwithcir—culardelamination,forwhichthediameterswere5mmand10mm,respectively,theuniaxialcompressiontest,a—cousticemission(AE)monitoringandstrainmeasurementofunidirectionalglassfiber/epoxycompositeswereconducted.Theresultsshowthatthedelaminationgrowthandthefailuremechanismoftwokindsofspecimenswithdif-ferentdelaminationweresimilarundercompressiveloading.Theareaofdelaminationhasgreatinfluenceonthebearingcapacityofspecimens.Thelargerareaofdelamination,thelowercarryingcapacityandthemoreserious—damageofthespecimenareobtained.Theloadlongitudinalstraincurvechangesfromlineartoapproximatelineartononlinear.ThechangeprocesswascoincidedwiththeanalysisresultsofAEsignals.Keywords:compositematerial;delamination;compressionfailure;acousticemission;strainanalysis(上接第92页)f16]CaiazzoA,OrletM,McShaneH,cta1.Theeffectsofmarcelde-fects(1flcompositestructuralproperties[J].ASTMSPECIAL—TECHNICALPUBLlCAT10N,200l,1383:158187.[17]WangJ,PotterKD,HazraK,eta1.Experimentalfabricationand———characterizationofoutofplanefibrewavinessincontinuousfibrereinforcedcomposites[J].JournalofCompositeMaterials,2011,46—(17):20412051.[18]李艳菲,李敏,顾轶卓,等.风电叶片用真空灌注型环氧树脂及其复合材料性能研究[J].玻璃钢/复合材料,2012,(4):109.1l4.EFFECTOFWAVINESSDEFECTONCOMPRESSIVEBEHAVIOROFCOnPOSITELAMINATES—WUWei.qing,ZHUJun,WANGJihui,ZULei(1.StateKeyLaboratoryofAdvancedTechnologyforMaterialSynthesisandProcessing,WuhanUniversityofTechnology,Wuhan430070,China;2.DepartmentofEngineeringStructureandMechanics,WuhanUniversityofTechnology,Wuhan430070,China)Abstract:WeadoptedVARIprocessandtheautoclavemoldingprocesstomanufacturecompressionsampleswithdifierentreinforcedfibersandcompressionsampleswithfiberwavinessdefect.Theresultsofthecompression’testsshowedthatYoungsmodulusandcompressivestrengthdegradedseriouslywiththeincreaseoffiberwavinessratio,andfiberwavinesshadgreaterinfluenceoncompressivestrength.Meanwhile,uniformwavinesshadagreater’effectoncompressivestrengthandYoungsmodulusthangradedwaviness.Interlaminarshearstresswasfoundtobethed()minantfailuremechanism.Moreover,thesamplesarepronetohavetransverseshearfailureonthepositionofmaximummisalignmentangle.Keywords:defects;wavinessratio;interlaminarshearfailure;fiberoff-axisangleFRP/CM2015.No.9
您可能关注的文档
- “离位”增韧复合材料准静态压入损伤特性研究.pdf
- “神舟七号”飞船舱外航天服防护头盔组件的研制.pdf
- “十二五”复合材料发展重点和方向解读.pdf
- “珠串”堆叠超结构的介孔铁酸锌的制备与表征.pdf
- (001)应变对正交相Ca2 P0.25 Si0.75能带结构及光学性质的影响.pdf
- 0.8设计系数用X80管线钢在近中性pH溶液中的应力腐蚀开裂行为.pdf
- 0.20mm CGO硅钢高温退火Goss晶粒起源及异常长大行为研究.pdf
- 0Cr16Ni5Mo低碳马氏体不锈钢的热变形行为及其热加工图.pdf
- 0Cr17Ni4Cu4Nb钢制螺钉断裂原因分析.pdf
- 1.5MW风机叶片模具加热工艺研究与技术创新.pdf
- 1.5MW风机叶片VARI工艺模拟分析及验证.pdf
- 2.5维机织复合材料低速冲击性能研究.pdf
- 2.25Cr-1Mo钢后续热处理中的磷偏聚行为.pdf
- 2A50锻铝三点弯曲试验与高分辨率CT成像分析.pdf
- 2A12与2A11铝合金超声波焊接工艺与组织研究.pdf
- 2MW风机复合材料叶片材料及工艺研究.pdf
- 3Cr2W8V模具钢激光表面相变硬化层性能的研究.pdf
- 3D打印技术及先进应用研究进展.pdf
- 3D打印技术研究现状和关键技术.pdf
- 5%鱼藤酮悬浮剂的研制.pdf

- 祥福铺
- 该用户很懒,什么也没介绍
相关文档
- “离位”增韧复合材料准静态压入损伤特性研究.pdf2021-11-235页
- “神舟七号”飞船舱外航天服防护头盔组件的研制.pdf2021-11-233页
- “十二五”复合材料发展重点和方向解读.pdf2021-11-232页
- “珠串”堆叠超结构的介孔铁酸锌的制备与表征.pdf2021-11-235页
- (001)应变对正交相Ca2 P0.25 Si0.75能带结构及光学性质的影响.pdf2021-11-236页
- 0.8设计系数用X80管线钢在近中性pH溶液中的应力腐蚀开裂行为.pdf2021-11-237页
- 0.20mm CGO硅钢高温退火Goss晶粒起源及异常长大行为研究.pdf2021-11-237页