- 文档大小:227.19 KB
- 文档格式:pdf
- 约 3页
- 2022-04-02 发布
- 举报
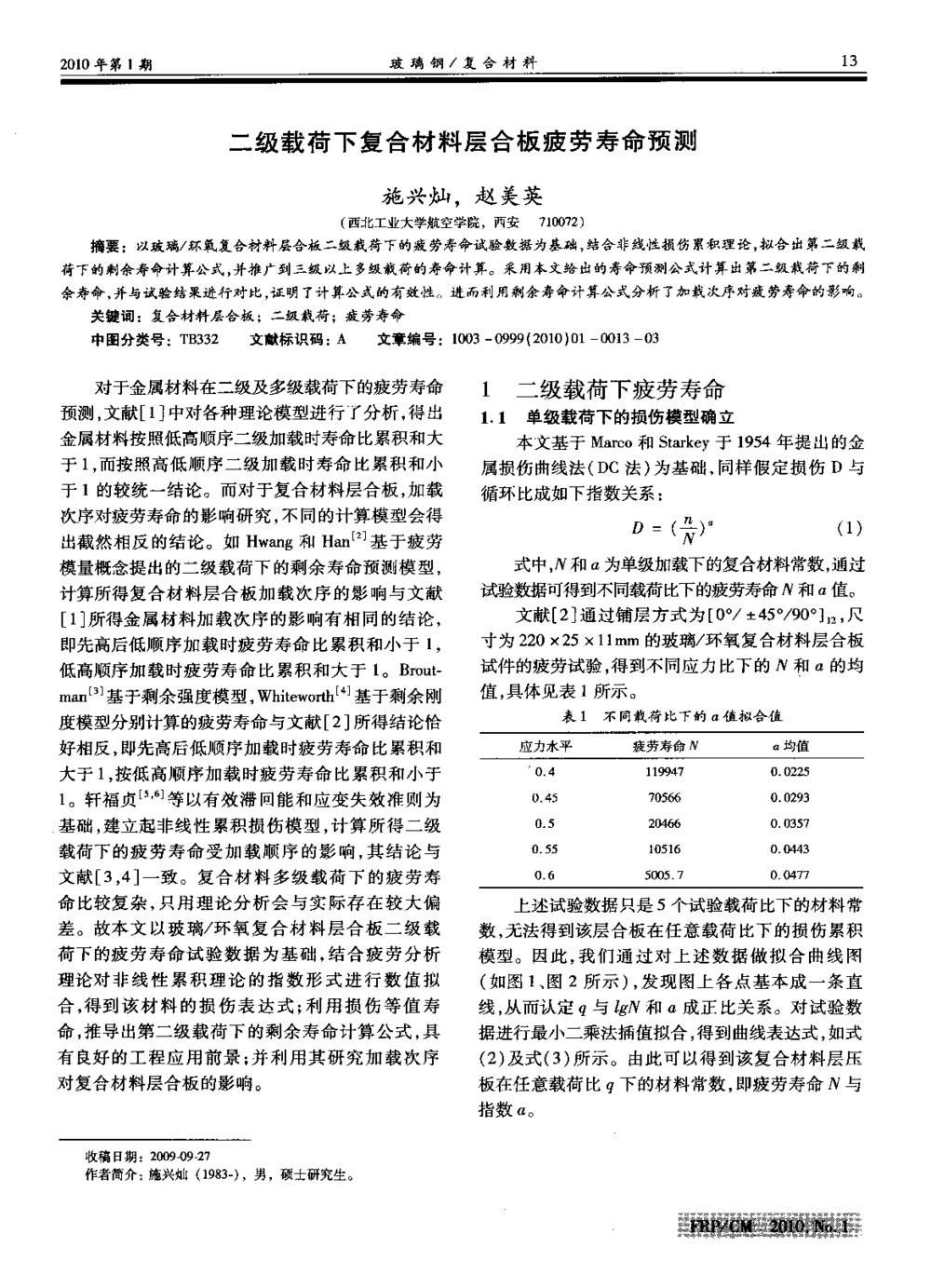
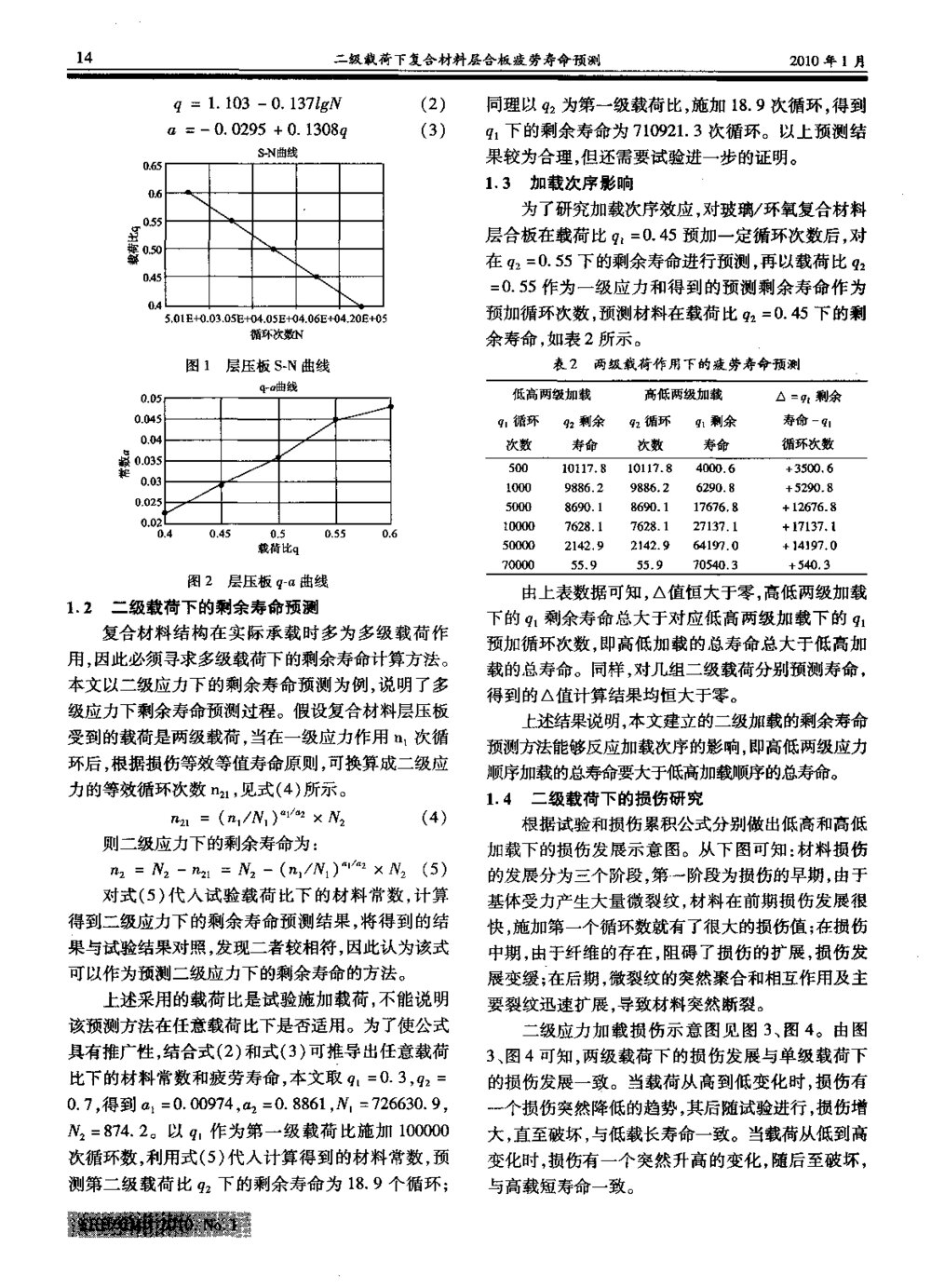
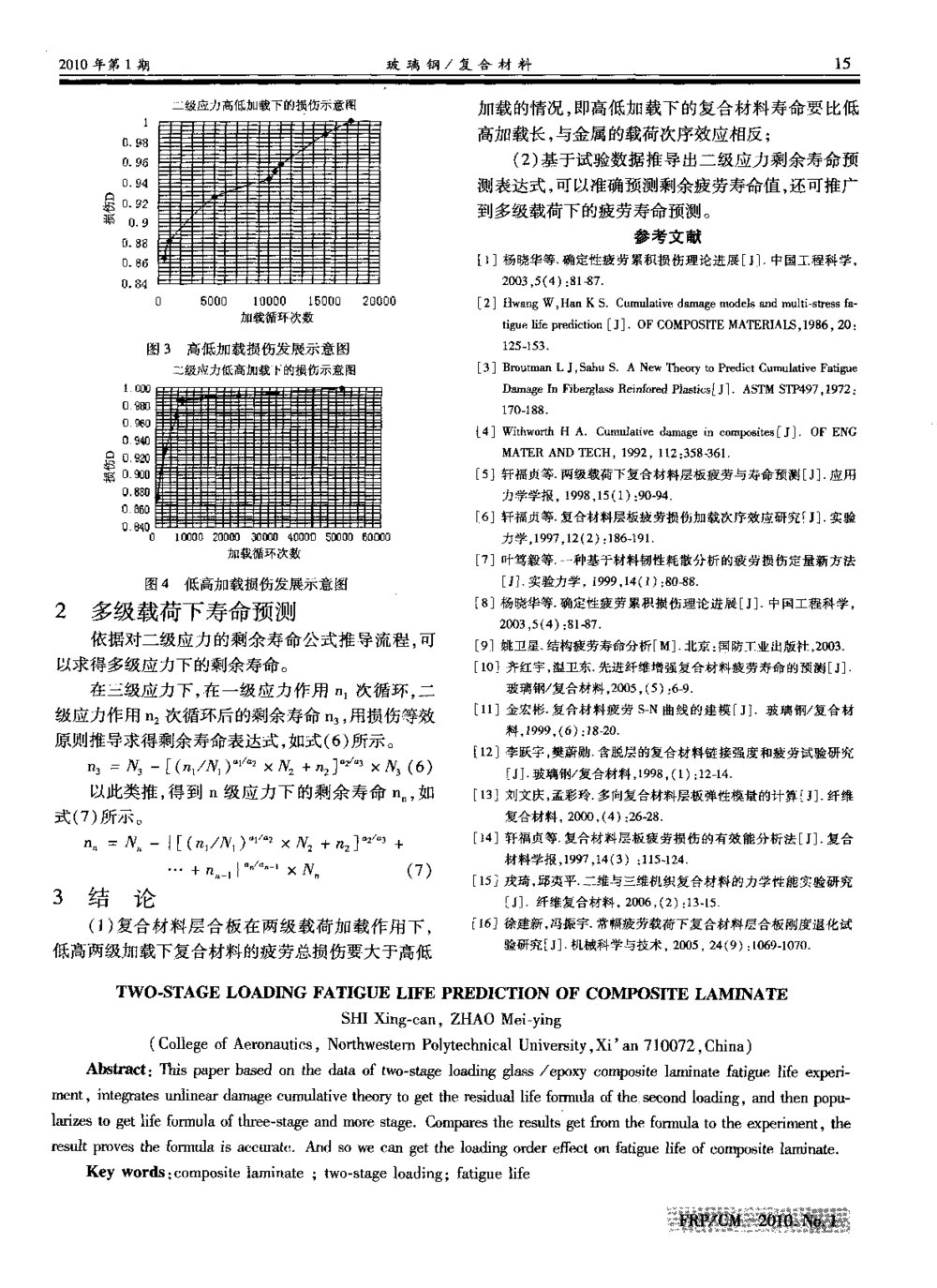
已阅读完毕,您还可以下载文档进行保存
- 1、本文档共3页,内容下载后可编辑。
- 2、本文档内容版权归属内容提供方,所产生的收益全部归内容提供方所有。如果您对本文有版权争议,可选择认领。
- 3、本文档由用户上传,本站不保证质量和数量令人满意,可能有诸多瑕疵,付费之前,请仔细先通过免费阅读内容等途径辨别内容交易风险。如存在严重挂羊头卖狗肉之情形,可联系本站下载客服投诉处理。
2010年第1期玻璃钢/复合材料l3二级载荷下复合材料层合板疲劳寿命预测施兴灿.赵美英(西北工业大学航空学院,西安710072)摘要:以玻璃/gg氧复合材料层合板二级栽荷下的疲劳寿命试验数据为基础,结合非线性损伤累积理论,拟合出第二级载荷下的剩余寿命计算公式,并推广到 ̄vX_E多级栽荷的寿命计算。采用本文给出的寿命预测公式计算出第二级载荷下的剩余寿命,并与试验结果进行对比,证明了计算公式的有效性。进而利用剩余寿命计算公式分析了加载次序对疲劳寿命的影响。关键词:复合材料层合板;二级载荷;疲劳寿命———中图分类号:TB332文献标识码:A文章编号:10030999(2010)01001303对于金属材料在二级及多级载荷下的疲劳寿命预测,文献[1]中对各种理论模型进行了分析,得出金属材料按照低高顺序二级加载时寿命比累积和大于1,而按照高低顺序二级加载时寿命比累积和小于1的较统一结论。而对于复合材料层合板,加载次序对疲劳寿命的影响研究,不同的计算模型会得出截然相反的结论。如Hwang和Han基于疲劳模量概念提出的二级载荷下的剩余寿命预测模型,计算所得复合材料层合板加载次序的影响与文献[1]所得金属材料加载次序的影响有相同的结论,即先高后低顺序加载时疲劳寿命比累积和小于1,—低高顺序加载时疲劳寿命比累积和大于1。Broutman【3基于剩余强度模型,Whiteworth_4基于剩余刚度模型分别计算的疲劳寿命与文献[2]所得结论恰好相反,即先高后低顺序加载时疲劳寿命比累积和大于1,按低高顺序加载时疲劳寿命比累积和小于1。轩福贞_5.6等以有效滞回能和应变失效准则为基础,建立起非线性累积损伤模型,计算所得二级载荷下的疲劳寿命受加载顺序的影响,其结论与文献[3,4]一致。复合材料多级载荷下的疲劳寿命比较复杂,只用理论分析会与实际存在较大偏差。故本文以玻璃/环氧复合材料层合板二级载荷下的疲劳寿命试验数据为基础,结合疲劳分析理论对非线性累积理论的指数形式进行数值拟合,得到该材料的损伤表达式;利用损伤等值寿命,推导出第二级载荷下的剩余寿命计算公式,具有良好的工程应用前景;并利用其研究加载次序对复合材料层合板的影响。收稿日期:2009-0927作者简介:施兴灿(1983一),男,硕士研究生。1二级载荷下疲劳寿命1.1单级载荷下的损伤模型确立本文基于Marco和Starkey于1954年提出的金属损伤曲线法(DC法)为基础,同样假定损伤D与循环比成如下指数关系:D=Ⅳ式中,和0为单级加载下的复合材料常数,通过试验数据可得到不同载荷比下的疲劳寿命N和口值。文献[2]通过铺层方式为[0 ̄/ ̄45。/90。]尺寸为220×25×11mm的玻璃/环氧复合材料层合板Ⅳ试件的疲劳试验,得到不同应力比下的和口的均值,具体见表1所示。表1不同栽荷比下的口值拟合值上述试验数据只是5个试验载荷比下的材料常数,无法得到该层合板在任意载荷比下的损伤累积模型。因此,我们通过对上述数据做拟合曲线图(如图1、图2所示),发现图上各点基本成一条直线,从而认定q与lgN和口成正比关系。对试验数据进行最小二乘法插值拟合,得到曲线表达式,如式(2)及式(3)所示。由此可以得到该复合材料层压板在任意载荷比q下的材料常数,即疲劳寿命J7、r与指数口。:14二级载荷下复合材料层合板疲劳寿命预测2010年1月≈籁靶—q=1.1030.1371gN口=一0.0295+0.1308qS.-Nlttl线\\、I\.\\\一\\5.0lE+O.03.05E+O4.05E+04.06E+04.2OE+O5循环次数N图1层压板S-N曲线q-alibi线//////(2)(3)图2层压板q-a曲线1.2二级载荷下的剩余寿命预测复合材料结构在实际承载时多为多级载荷作用,因此必须寻求多级载荷下的剩余寿命计算方法。本文以二级应力下的剩余寿命预测为例,说明了多级应力下剩余寿命预测过程。假设复合材料层压板受到的载荷是两级载荷,当在一级应力作用11次循环后,根据损伤等效等值寿命原则,可换算成二级应力的等效循环次数n。,见式(4)所示。Ⅳ凡21=(n1/1)al/a2×N2(4)则二级应力下的剩余寿命为:ⅣⅣn2=N2一21=N2一(几1/1)al/a2X2(5)对式(5)代入试验载荷比下的材料常数,计算得到二级应力下的剩余寿命预测结果,将得到的结果与试验结果对照,发现二者较相符,因此认为该式可以作为预测二级应力下的剩余寿命的方法。上述采用的载荷比是试验施加载荷,不能说明该预测方法在任意载荷比下是否适用。为了使公式具有推广性,结合式(2)和式(3)可推导出任意载荷比下的材料常数和疲劳寿命,本文取q。=0.3,q=0.7,得到口1=0.00974,口2=0.8861,Nl=726630.9,Ⅳ2=874.2。以g,作为第一级载荷比施加100000次循环数,利用式(5)代入计算得到的材料常数,预测第二级载荷比q下的剩余寿命为18.9个循环;同理以q为第一级载荷比,施加18.9次循环,得到q。下的剩余寿命为710921.3次循环。以上预测结果较为合理,但还需要试验进一步的证明。1.3加载次序影响为了研究加载次序效应,对玻璃/环氧复合材料层合板在载荷比q=0.45预加一定循环次数后,对在q:=0.55下的剩余寿命进行预测,再以载荷比q=0.55作为一级应力和得到的预测剩余寿命作为预加循环次数,预测材料在载荷比q=0.45下的剩余寿命,如表2所示。表2两级栽荷作用下的疲劳寿命预测△由上表数据可知,值恒大于零,高低两级加载下的q。剩余寿命总大于对应低高两级加载下的q预加循环次数,即高低加载的总寿命总大于低高加载的总寿命。同样,对几组二级载荷分别预测寿命,△得到的值计算结果均恒大于零。上述结果说明,本文建立的二级加载的剩余寿命预测方法能够反应加载次序的影响,即高低两级应力顺序加载的总寿命要大于低高加载JI赙的总寿命。1.4二级载荷下的损伤研究根据试验和损伤累积公式分别做出低高和高低加载下的损伤发展示意图。从下图可知:材料损伤的发展分为三个阶段,第一阶段为损伤的早期,由于基体受力产生大量微裂纹,材料在前期损伤发展很快,施加第一个循环数就有了很大的损伤值;在损伤中期,由于纤维的存在,阻碍了损伤的扩展,损伤发展变缓;在后期,微裂纹的突然聚合和相互作用及主要裂纹迅速扩展,导致材料突然断裂。二级应力加载损伤示意图见图3、图4。由图3、图4可知,两级载荷下的损伤发展与单级载荷下的损伤发展一致。当载荷从高到低变化时,损伤有一个损伤突然降低的趋势,其后随试验进行,损伤增大,直至破坏,与低载长寿命一致。当载荷从低到高变化时,损伤有一个突然升高的变化,随后至破坏,与高载短寿命一致。嘶啷啷¨口茁捂耱2010年第1期玻璃钢/复合材料l0.980.96O.94星0.920.90.880.860.84二级应力高低加载下的损伤示意图06000l0000l500020000加载循环次数图3高低加载损伤发展示意图二级应力低高加载下的损伤示意图l加00q踟09600940星。一92009000.88o08600.8吐0Ul000UZOgO0:30001[]qOOOU5000050UO0加载循环次数图4低高加载损伤发展示意图2多级载荷下寿命预测依据对二级应力的剩余寿命公式推导流程,可以求得多级应力下的剩余寿命。在三级应力下,在一级应力作用n。次循环,二级应力作用n次循环后的剩余寿命n,,用损伤等效原则推导求得剩余寿命表达式,如式(6)所示。ⅣⅡⅣn3=一[(nI/N1),口X2+2]2/X3(6)以此类推,得到n级应力下的剩余寿命13,如式(7)所示。n=^一{[(1/N1)al/a2×^,2+2]叼+…+n}XNn(7)3结论(1)复合材料层合板在两级载荷加载作用下,低高两级加载下复合材料的疲劳总损伤要大于高低加载的情况,即高低加载下的复合材料寿命要比低高加载长,与金属的载荷次序效应相反;(2)基于试验数据推导出二级应力剩余寿命预测表达式,可以准确预测剩余疲劳寿命值,还可推广到多级载荷下的疲劳寿命预测。参考文献[1]杨晓华等,确定性疲劳累积损伤理论进展[J].中国工程科学,2003,5(4):81-87.—[2]HwangW,HanKS.Cumulativedamagemodelsandmultistressfa-figuelifeprediction[J].OFCOMPOSITEMATERIALS,1986,20:125153.[3]BroutmanLJ,SahuS.ANewTheorytoPredictCumulativeFatigueDamageInFiberglassReinforedPlastics[J].ASTMSTP497,1972:170188.[4]WithworthHA.Cumulativedamageincomposites[J].OFENGMATERANDTECH,1992,112:358,361.[5]轩福贞等.两级载荷下复合材料层板疲劳与寿命预测[J].应用力学学报,1998,15(1):90-94.[6]轩福贞等.复合材料层板疲劳损伤加载次序效应研究[J].实验力学,1997,12(2):186-191.【7]叶笃毅等.一种基于材料韧性耗散分析的疲劳损伤定量新方法[J].实验力学,1999,14(1):80--88.[8]杨晓华等.确定性疲劳累积损伤理论进展[J].中国工程科学,2003,5(4):81-87.[9]姚卫星.结构疲劳寿命分析[M].北京:国防工业出版社,2003.[1O]齐红宇,温卫东.先进纤维增强复合材料疲劳寿命的预测[J].玻璃钢/复合材料,2005,(5):6-9.[11]金宏彬.复合材料疲劳S-N曲线的建模[J].玻璃钢/复合材料,1999,(6):18-20.[12]李跃宇,樊蔚勋.含脱层的复合材料链接强度和疲劳试验研究[JJ.玻璃钢/复合材料,1998,(1):l2.14.[13]刘文庆,孟彩玲.多向复合材料层板弹性模量的计算[J].纤维复合材料,2000,(4):26-28.[14]轩福贞等.复合材料层板疲劳损伤的有效能分析法[J].复合材料学报,1997,14(3):115.124.[15]戎琦,邱夷平.二维与三维机织复合材料的力学性能实验研究[J].纤维复合材料,2006,(2):l3.15.f16J徐建新,冯振字.常幅疲劳载荷下复合材料层合板刚度退化试—验研究[J].机械科学与技术,2005,24(9):10691070.TWO-STAGELOADINGFATIGUELIFEPREDICTION0FCoM_POSITELAMINATE——SHIXingcan,ZHAOMeiying’(CollegeofAeronautics,NorthwesternPolytechniealUniversity,Xian710072,China)——Abstract:Thispaperbasedonthedataoftwostageloadingass/epoxycompositelaminatefatiguelifeexperiment,integratesunlineardamagecumulativetheorytogettheresiduallifeformulaofthesecondloading,andthenpopu.—1arizestogetlifeformulaofthreestageandmorestage.Comparestheresultsgetfromtheformulatotheexperiment,theresultprovestheformulaisaccurate.AndSOwecangettheloadingordereffectonfatiguelifeofcompositelaminate.—Keywords:compositelaminate;twostageloading;fatiguelife匆峨
您可能关注的文档
- “离位”增韧复合材料准静态压入损伤特性研究.pdf
- “神舟七号”飞船舱外航天服防护头盔组件的研制.pdf
- “十二五”复合材料发展重点和方向解读.pdf
- “珠串”堆叠超结构的介孔铁酸锌的制备与表征.pdf
- (001)应变对正交相Ca2 P0.25 Si0.75能带结构及光学性质的影响.pdf
- 0.8设计系数用X80管线钢在近中性pH溶液中的应力腐蚀开裂行为.pdf
- 0.20mm CGO硅钢高温退火Goss晶粒起源及异常长大行为研究.pdf
- 0Cr16Ni5Mo低碳马氏体不锈钢的热变形行为及其热加工图.pdf
- 0Cr17Ni4Cu4Nb钢制螺钉断裂原因分析.pdf
- 1.5MW风机叶片模具加热工艺研究与技术创新.pdf
- 1.5MW风机叶片VARI工艺模拟分析及验证.pdf
- 2.5维机织复合材料低速冲击性能研究.pdf
- 2.25Cr-1Mo钢后续热处理中的磷偏聚行为.pdf
- 2A50锻铝三点弯曲试验与高分辨率CT成像分析.pdf
- 2A12与2A11铝合金超声波焊接工艺与组织研究.pdf
- 2MW风机复合材料叶片材料及工艺研究.pdf
- 3Cr2W8V模具钢激光表面相变硬化层性能的研究.pdf
- 3D打印技术及先进应用研究进展.pdf
- 3D打印技术研究现状和关键技术.pdf
- 5%鱼藤酮悬浮剂的研制.pdf

- 富富资料
- 该用户很懒,什么也没介绍
相关文档
- “离位”增韧复合材料准静态压入损伤特性研究.pdf2021-11-235页
- “神舟七号”飞船舱外航天服防护头盔组件的研制.pdf2021-11-233页
- “十二五”复合材料发展重点和方向解读.pdf2021-11-232页
- “珠串”堆叠超结构的介孔铁酸锌的制备与表征.pdf2021-11-235页
- (001)应变对正交相Ca2 P0.25 Si0.75能带结构及光学性质的影响.pdf2021-11-236页
- 0.8设计系数用X80管线钢在近中性pH溶液中的应力腐蚀开裂行为.pdf2021-11-237页
- 0.20mm CGO硅钢高温退火Goss晶粒起源及异常长大行为研究.pdf2021-11-237页