- 文档大小:536.95 KB
- 文档格式:pdf
- 约 4页
- 2022-04-07 发布
- 举报
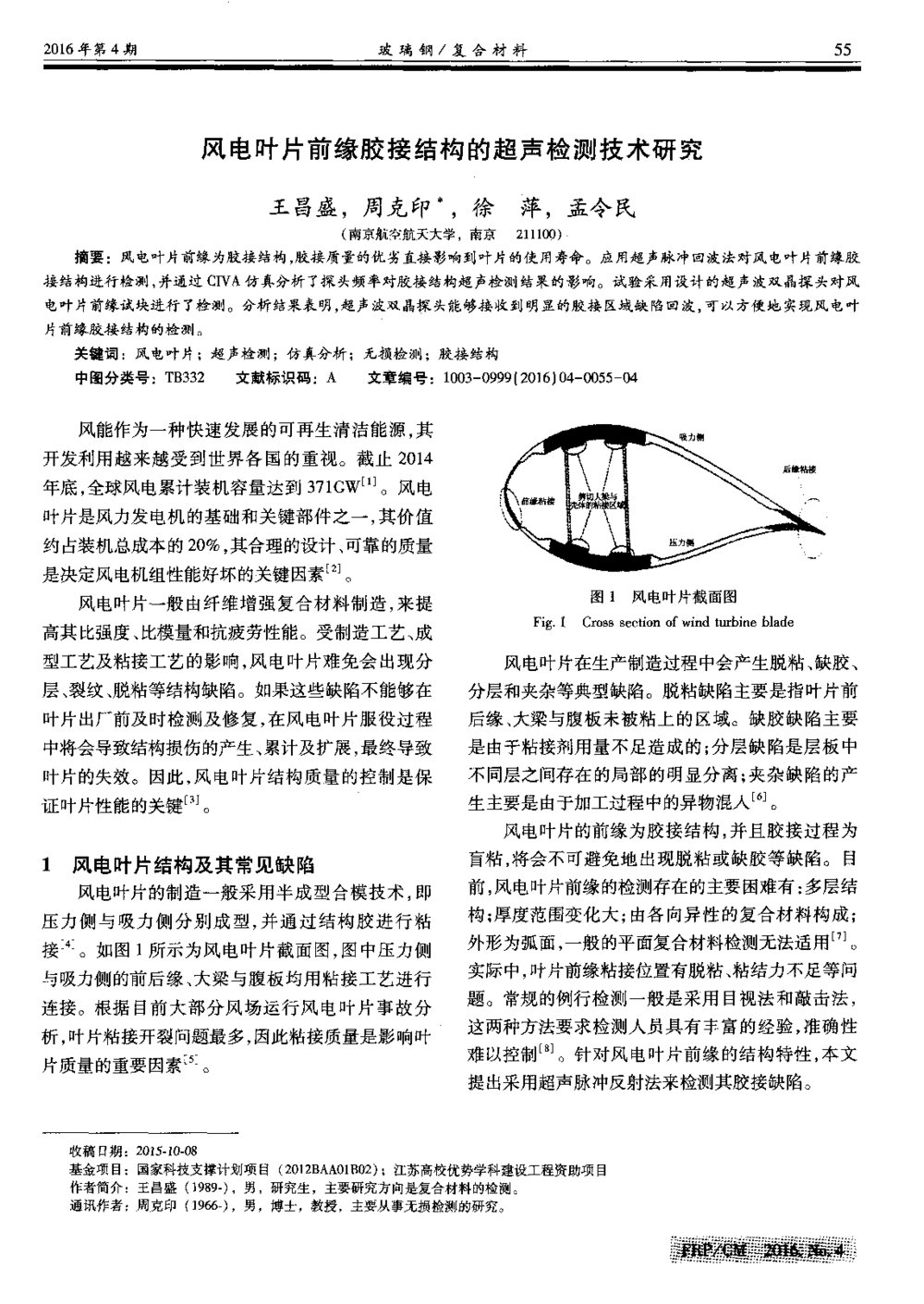
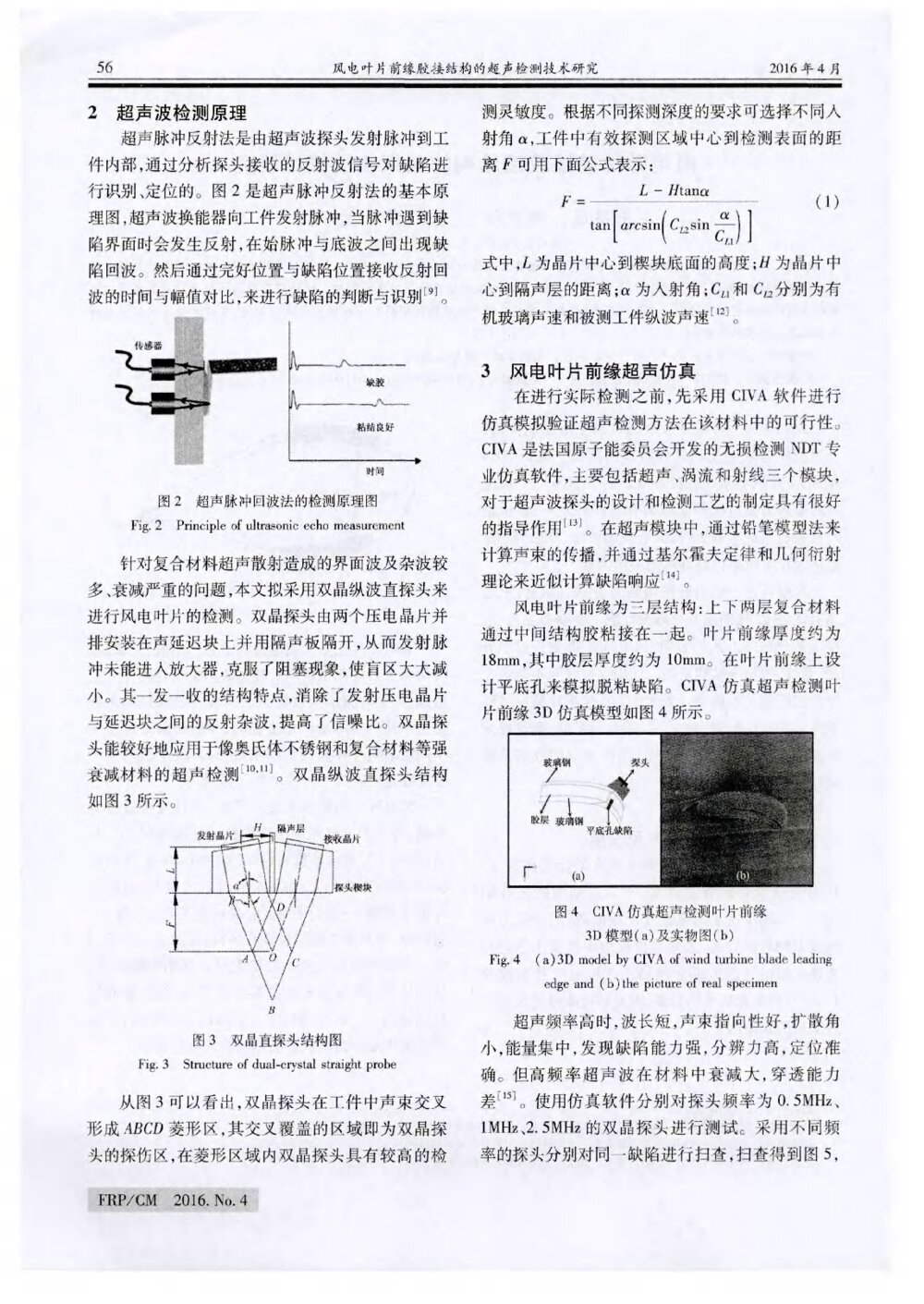
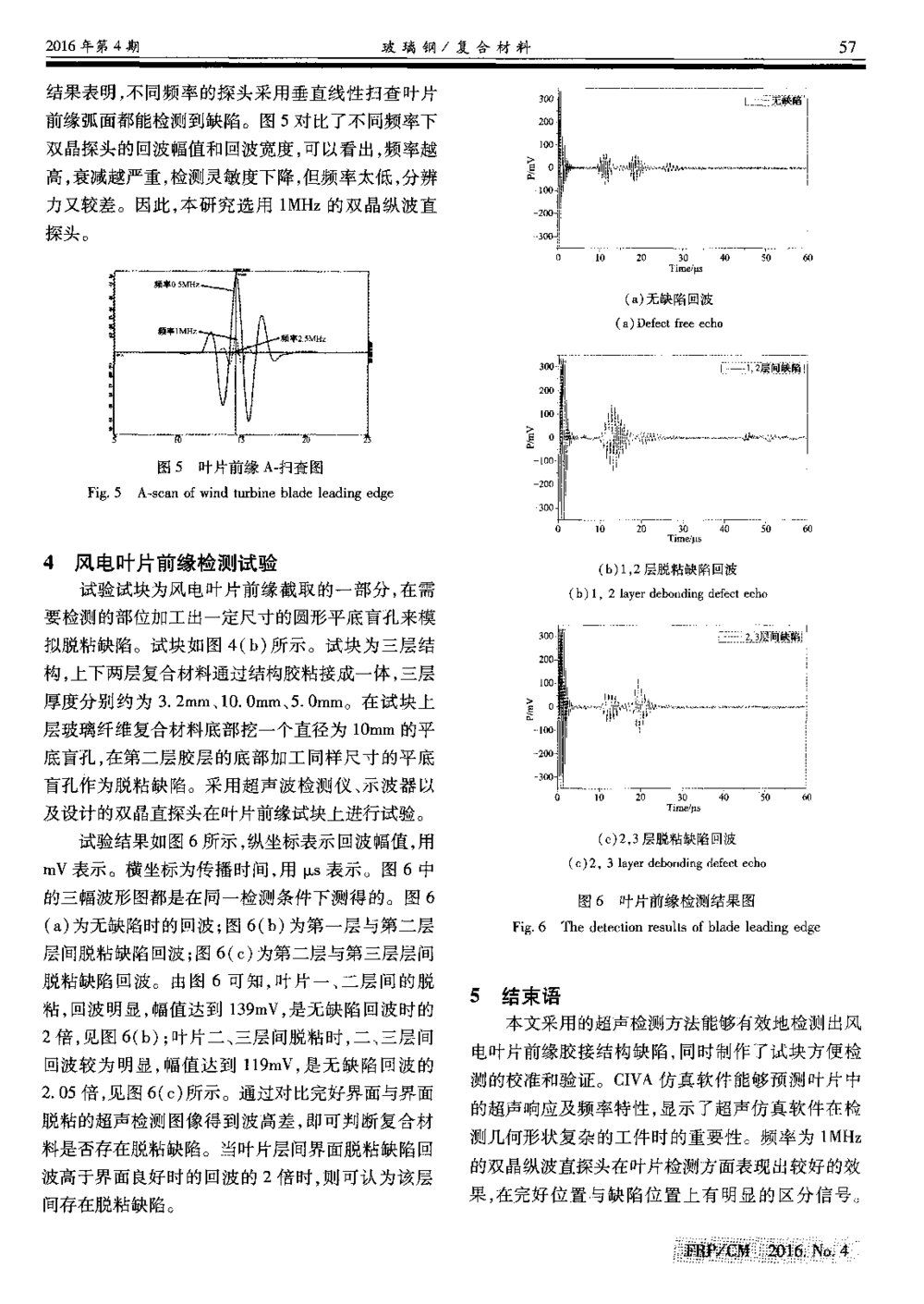
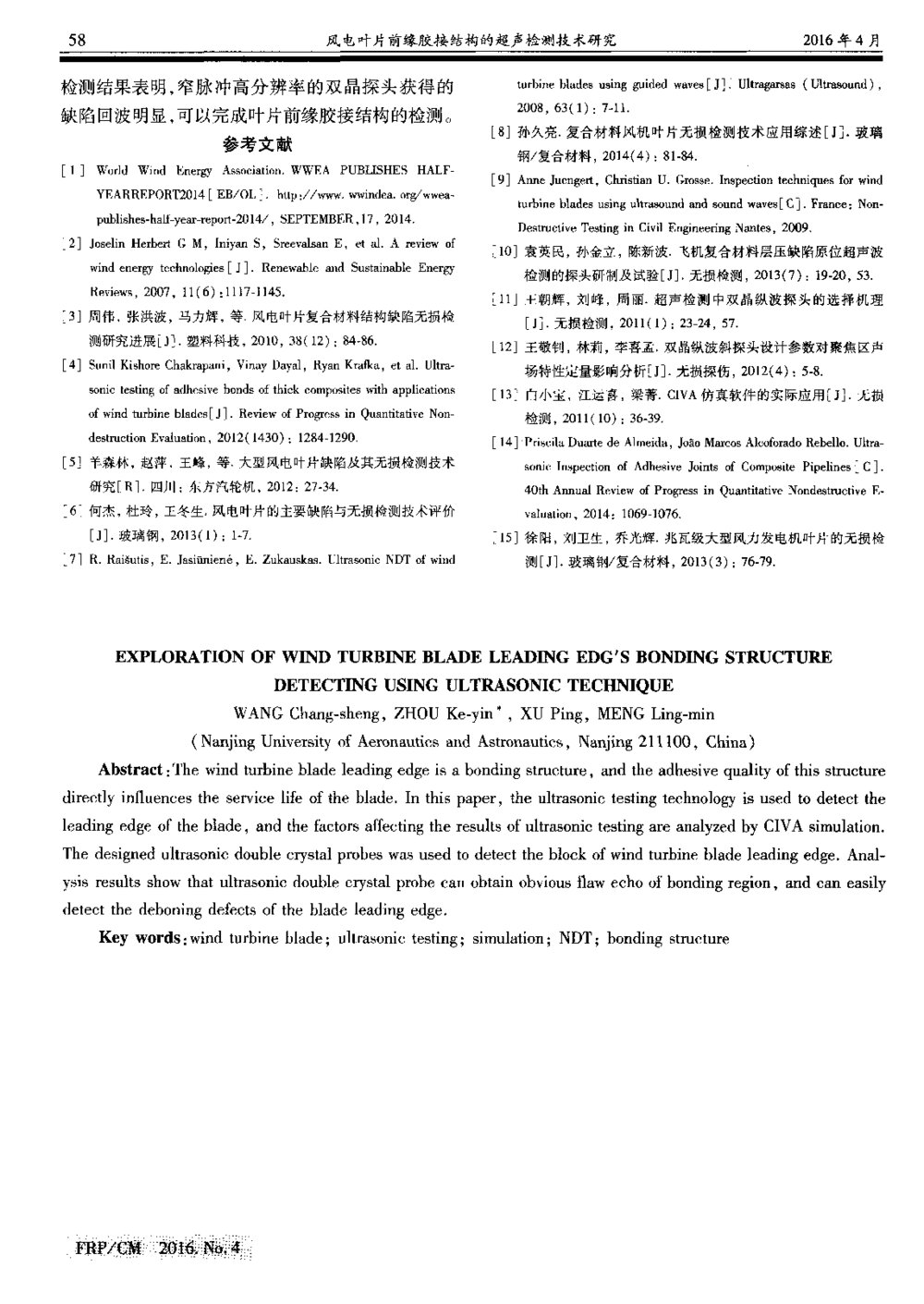
已阅读完毕,您还可以下载文档进行保存
- 1、本文档共4页,内容下载后可编辑。
- 2、本文档内容版权归属内容提供方,所产生的收益全部归内容提供方所有。如果您对本文有版权争议,可选择认领。
- 3、本文档由用户上传,本站不保证质量和数量令人满意,可能有诸多瑕疵,付费之前,请仔细先通过免费阅读内容等途径辨别内容交易风险。如存在严重挂羊头卖狗肉之情形,可联系本站下载客服投诉处理。
2016年第4期玻璃钢/复合材料55风电叶片前缘胶接结构的超声检测技术研究王昌盛,周克印,徐萍,孟令民(南京航空航天大学,南京211100)摘要:风电叶片前缘为胶接结构,胶接质量的优劣直接影响到叶片的使用寿命。应用超声脉冲回波法对风电叶片前缘胶接结构进行检测,并通过CIVA仿真分析了探头频率对胶接结构超声检测结果的影响。试验采用设计的超声波双晶探头对风电叶片前缘试块进行了检测。分析结果表明,超声波双晶探头能够接收到明显的胶接区域缺陷回波,可以方便地实现风电叶片前缘胶接结构的检测。关键词:风电叶片;超声检测;仿真分析;无损检测;胶接结构—中图分类号:TB332文献标识码:A文章编号:1003-0999(2016)040055-04风能作为一种快速发展的可再生清洁能源,其开发利用越来越受到世界各国的重视。截止2014年底,全球风电累计装机容量达到371GW_lJ。风电叶片是风力发电机的基础和关键部件之一,其价值约占装机总成本的20%,其合理的设计、可靠的质量是决定风电机组性能好坏的关键因素J。风电叶片一般由纤维增强复合材料制造,来提高其比强度、比模量和抗疲劳陛能。受制造工艺、成型工艺及粘接工艺的影响,风电叶片难免会出现分层、裂纹、脱粘等结构缺陷。如果这些缺陷不能够在叶片出厂前及时检测及修复,在风电叶片服役过程中将会导致结构损伤的产生、累计及扩展,最终导致叶片的失效。因此,风电叶片结构质量的控制是保证叶片性能的关键J。1风电叶片结构及其常见缺陷风电叶片的制造一般采用半成型合模技术,即压力侧与吸力侧分别成型,并通过结构胶进行粘接J。如图1所示为风电叶片截面图,图中压力侧与吸力侧的前后缘、大梁与腹板均用粘接工艺进行连接。根据目前大部分风场运行风电叶片事故分析,叶片粘接开裂问题最多,因此粘接质量是影响叶片质量的重要因素。——’,,17]'膳离套域I一)图1风电叶片截面图Fig.1Crosssectionofwindturbineblade风电叶片在生产制造过程中会产生脱粘、缺胶、分层和夹杂等典型缺陷。脱粘缺陷主要是指叶片前后缘、大梁与腹板未被粘上的区域。缺胶缺陷主要是由于粘接剂用量不足造成的;分层缺陷是层板中不同层之间存在的局部的明显分离;夹杂缺陷的产生主要是由于加工过程中的异物混入。风电叶片的前缘为胶接结构,并且胶接过程为盲粘,将会不可避免地出现脱粘或缺胶等缺陷。目前,风电叶片前缘的检测存在的主要困难有:多层结构;厚度范围变化大;由各向异性的复合材料构成;外形为弧面,一般的平面复合材料检测无法适用。实际中,叶片前缘粘接位置有脱粘、粘结力不足等问题。常规的例行检测一般是采用目视法和敲击法,这两种方法要求检测人员具有丰富的经验,准确性难以控制J。针对风电叶片前缘的结构特性,本文提出采用超声脉冲反射法来检测其胶接缺陷。—收稿日期:201510一o8基金项目:国家科技支撑计划项目(2012BAAO1B02);江苏高校优势学科建设工程资助项目作者简介:王昌盛(1989一),男,研究生,主要研究方向是复合材料的检测。通讯作者:周克印(1966一),男,博士,教授,主要从事无损检测的研究。哪瓣2016年第4期玻璃钢/复合材料57结果表明,不同频率的探头采用垂直线性扫查叶片前缘弧面都能检测到缺陷。图5对比了不同频率下双晶探头的回波幅值和回波宽度,可以看出,频率越高,衰减越严重,检测灵敏度下降,但频率太低,分辨力又较差。因此,本研究选用1MHz的双晶纵波直探头。图5叶片前缘A一扫查图—Fig.5Ascanofwindturbinebladeleadingedge4风电叶片前缘检测试验试验试块为风电叶片前缘截取的一部分,在需要检测的部位加工出一定尺寸的圆形平底盲孔来模拟脱粘缺陷。试块如图4(b)所示。试块为三层结构,上下两层复合材料通过结构胶粘接成一体,三层厚度分别约为3.2mm、10.0mm、5.0ram。在试块上层玻璃纤维复合材料底部挖一个直径为10mm的平底盲孔,在第二层胶层的底部加工同样尺寸的平底盲孔作为脱粘缺陷。采用超声波检测仪、示波器以及设计的双晶直探头在叶片前缘试块上进行试验。试验结果如图6所示,纵坐标表示回波幅值,用mV表示。横坐标为传播时间,用s表示。图6中的三幅波形图都是在同一检测条件下测得的。图6(a)为无缺陷时的回波;图6(b)为第一层与第二层层间脱粘缺陷回波;图6(e)为第二层与第三层层间脱粘缺陷回波。由图6可知,叶片一、二层间的脱粘,回波明显,幅值达到139mV,是无缺陷回波时的2倍,见图6(b);叶片二、三层间脱粘时,二、三层间回波较为明显,幅值达到119mV,是无缺陷回波的2.05倍,见图6(c)所示。通过对比完好界面与界面脱粘的超声检测图像得到波高差,即可判断复合材料是否存在脱粘缺陷。当叶片层间界面脱粘缺陷回波高于界面良好时的回波的2倍时,则可认为该层间存在脱粘缺陷。(a)无缺陷回波(a)De ̄ctfreeecho(b)1,2层脱粘缺陷回波(b)1,2layerdebondingdefectecho(C)2,3层脱粘缺陷回波(C)2,3layerdebondingdefectecho图6叶片前缘检测结果图Fig.6Thedetectionresultsofbladeleadingedge5结束语本文采用的超声检测方法能够有效地检测出风电叶片前缘胶接结构缺陷,同时制作了试块方便检测的校准和验证。CIVA仿真软件能够预测叶片中的超声响应及频率特性,显示了超声仿真软件在检测几何形状复杂的工件时的重要性。频率为1MHz的双晶纵波直探头在叶片检测方面表现出较好的效果,在完好位置与缺陷位置上有明显的区分信号。靠%g譬∞1碾l=2016誊J、叠4一*t58风电叶片前缘胶接结构的超声检测技术研究2016年4月检测结果表明,窄脉冲高分辨率的双晶探头获得的缺陷回波明显,可以完成叶片前缘胶接结构的检测。参考文献—[1]WorldWindEnergyAssociation.WWEAPUBLISHESHALF—YEARREPORT2014[EB/OL].http://www.wwindea.orgc/wwea—publishes-half-yearreport一2014/,SEPTEMBER,17,2014.[2]JoselinHerbertGM,IniyanS,SreevalsanE,eta1.Areviewofwindenergytechnologies[J].RenewableandSustainableEnergy—Reviews,2007,11(6):11171145.[3]周伟,张洪波,马力辉,等.风电叶片复合材料结构缺陷无损检—测研究进展[J].塑料科技,2010,38(12):8486.—[4]SunilKishoreChakrapani,VinayDayal,RyanKrafka,eta1.Ultrasonictestingofadhesivebondsofthickcompositeswithapplicationsofwindturbineblades[J].ReviewofProgressinQuantitativeNon-destructionEvaluation,2012(1430):1284.1290.[5]羊森林,赵萍,王峰,等.大型风电叶片缺陷及其无损检测技术研究[R].四川:东方汽轮机,2012:27.34.[6]何杰,杜玲,王冬生风电叶片的主要缺陷与无损检测技术评价[J].玻璃钢,2013(1):1-7.『7]R.Rai ̄utis,E.Jasi ̄nien6,E.Zukauskas.UltrasonicNDTofwindturbinebladesusingguidedwaves[J].Uhragarsas(Ultrasound),2008,63(1):7-11.[8]孙久亮.复合材料风机叶片无损检测技术应用综述[J].玻璃钢/复合材料,2014(4):81.84.[9]AnneJuengert,ChristianU.Grosse.Inspectiontechniquesforwindturbinebladesusingultrasoundandsoundwaves[C].France:Non-DestructiveTestinginCivilEngineeringNantes,2009.[10]袁英民,孙金立,陈新波.飞机复合材料层压缺陷原位超声波检测的探头研制及试验[J].无损检测,2013(7):19.20,53.[11]王朝辉,刘峰,周丽.超声检测中双晶纵波探头的选择机理—[J].无损检测,2011(1):2324,57.[12]王敬钊,林莉,李喜孟.双晶纵波斜探头设计参数对聚焦区声场特性定量影响分析[J].无损探伤,2012(4):5-8.[13]白小宝,江运喜,梁菁.CIVA仿真软件的实际应用[J].无损—检测,2011(10):3639.[14]PriscilaDua ̄edeAlmeida,Jo§—0MarcosAlcoforadoRebello.UltrasonicInspectionofAdhesiveJointsofCompositePipelines[C].40thAnnualReviewofProg—ressinQuantitativeNondestructiveEvaluation,2014:1069・1076.[15]徐阳,刘卫生,乔光辉.兆瓦级大型风力发电机叶片的无损检测[J].玻璃钢/复合材料,2013(3):76-79.EXPLORATIONOFWINDTURBINEBLADELEADlNGEDGSBoDINGSTRUCTUREDETECTINGUSINGULTRASONICTECHNIQUE———WANGChangsheng,ZHOUKeyin,XUPing,MENGLingmin(NanjingUniversityofAeronauticsandAstronautics,Nanjing211100,China)Abstract:Thewindturbinebladeleadingedgeisabondingstructure,andtheadhesivequalityofthisstructuredirectlyinfluencestheservicelifeoftheblade.Inthispaper,theultrasonictestingtechnologyisusedtodetecttheleadingedgeoftheblade,andthefactorsaffectingtheresuhsofultrasonictestingareanalyzedbyCIVAsimulation.—Thedesignedultrasonicdoublecrystalprobeswasusedtodetecttheblockofwindturbinebladeleadingedge.Analysisresultsshowthatultrasonicdoublecrystalprobecanobtainobviousflawechoofbondingregion,andcaneasilydetectthedeboningdefectsofthebladeleadingedge.Keywords:windturbineblade;ultrasonictesting;simulation;NDT;bondingstructureFRP]EM;:6.o.4
您可能关注的文档
- “离位”增韧复合材料准静态压入损伤特性研究.pdf
- “神舟七号”飞船舱外航天服防护头盔组件的研制.pdf
- “十二五”复合材料发展重点和方向解读.pdf
- “珠串”堆叠超结构的介孔铁酸锌的制备与表征.pdf
- (001)应变对正交相Ca2 P0.25 Si0.75能带结构及光学性质的影响.pdf
- 0.8设计系数用X80管线钢在近中性pH溶液中的应力腐蚀开裂行为.pdf
- 0.20mm CGO硅钢高温退火Goss晶粒起源及异常长大行为研究.pdf
- 0Cr16Ni5Mo低碳马氏体不锈钢的热变形行为及其热加工图.pdf
- 0Cr17Ni4Cu4Nb钢制螺钉断裂原因分析.pdf
- 1.5MW风机叶片模具加热工艺研究与技术创新.pdf
- 1.5MW风机叶片VARI工艺模拟分析及验证.pdf
- 2.5维机织复合材料低速冲击性能研究.pdf
- 2.25Cr-1Mo钢后续热处理中的磷偏聚行为.pdf
- 2A50锻铝三点弯曲试验与高分辨率CT成像分析.pdf
- 2A12与2A11铝合金超声波焊接工艺与组织研究.pdf
- 2MW风机复合材料叶片材料及工艺研究.pdf
- 3Cr2W8V模具钢激光表面相变硬化层性能的研究.pdf
- 3D打印技术及先进应用研究进展.pdf
- 3D打印技术研究现状和关键技术.pdf
- 5%鱼藤酮悬浮剂的研制.pdf

- 陌南尘
- 该用户很懒,什么也没介绍
相关文档
- “离位”增韧复合材料准静态压入损伤特性研究.pdf2021-11-235页
- “神舟七号”飞船舱外航天服防护头盔组件的研制.pdf2021-11-233页
- “十二五”复合材料发展重点和方向解读.pdf2021-11-232页
- “珠串”堆叠超结构的介孔铁酸锌的制备与表征.pdf2021-11-235页
- (001)应变对正交相Ca2 P0.25 Si0.75能带结构及光学性质的影响.pdf2021-11-236页
- 0.8设计系数用X80管线钢在近中性pH溶液中的应力腐蚀开裂行为.pdf2021-11-237页
- 0.20mm CGO硅钢高温退火Goss晶粒起源及异常长大行为研究.pdf2021-11-237页