- 文档大小:923.89 KB
- 文档格式:pdf
- 约 5页
- 2022-04-07 发布
- 举报
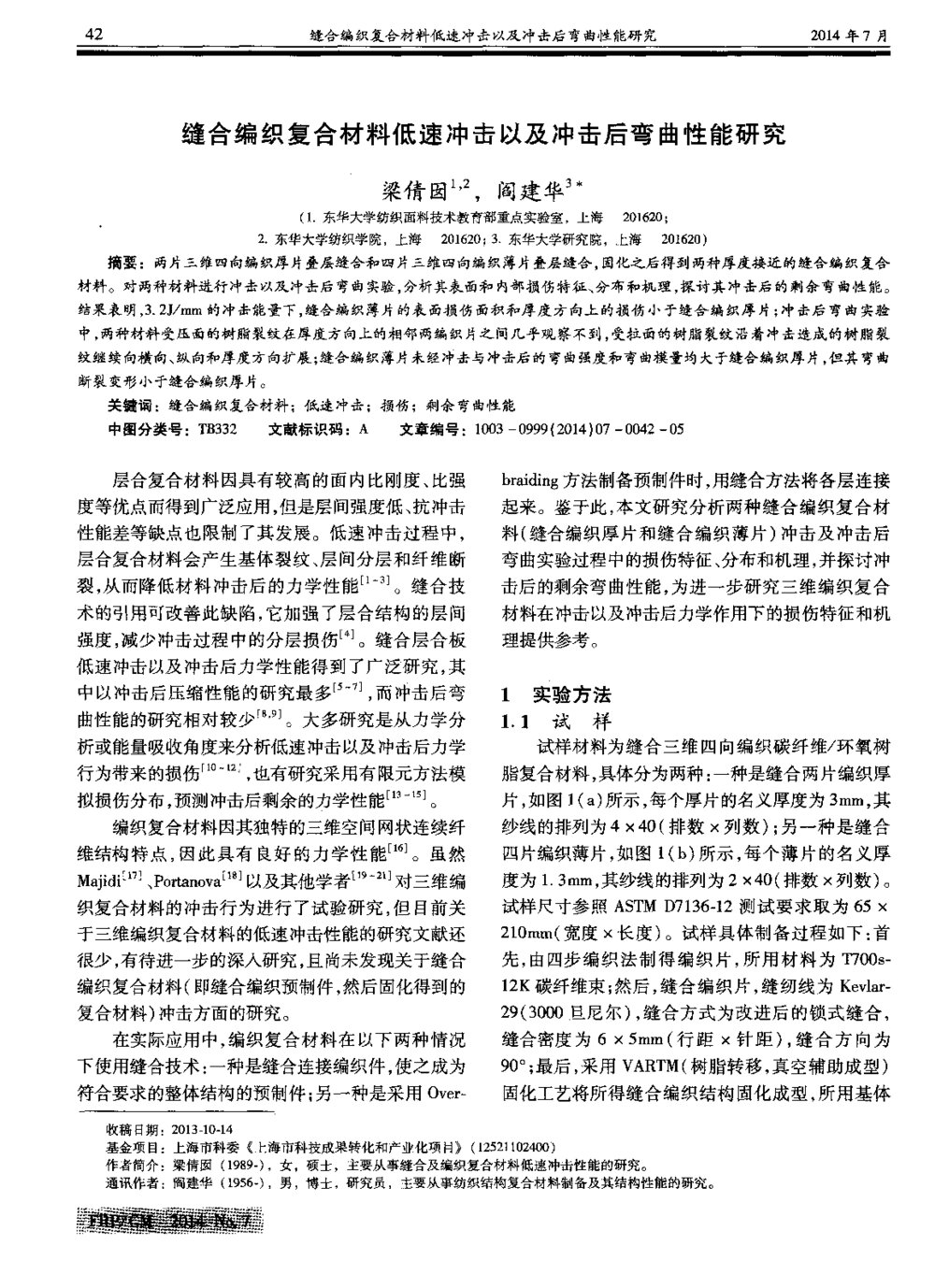
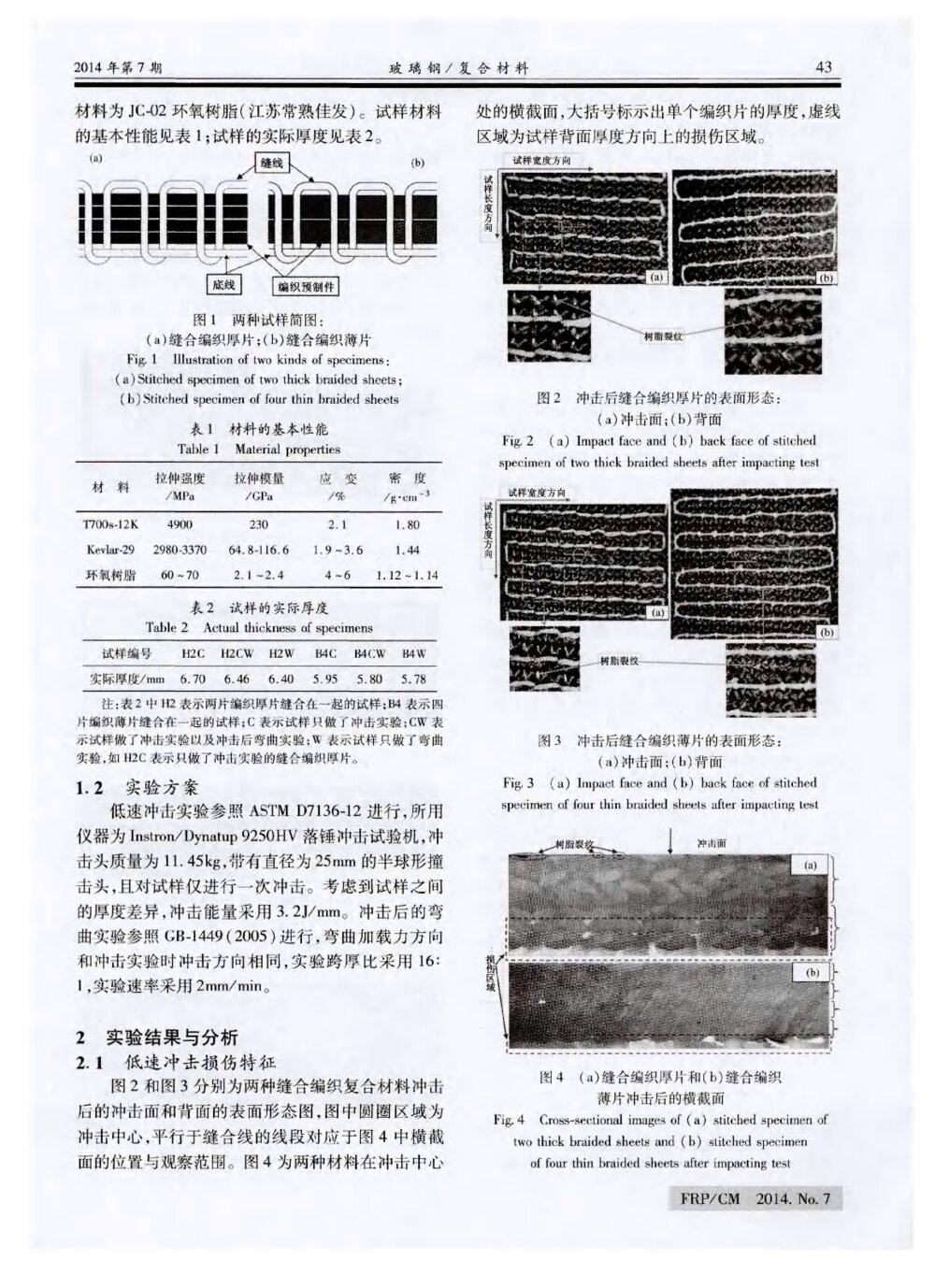
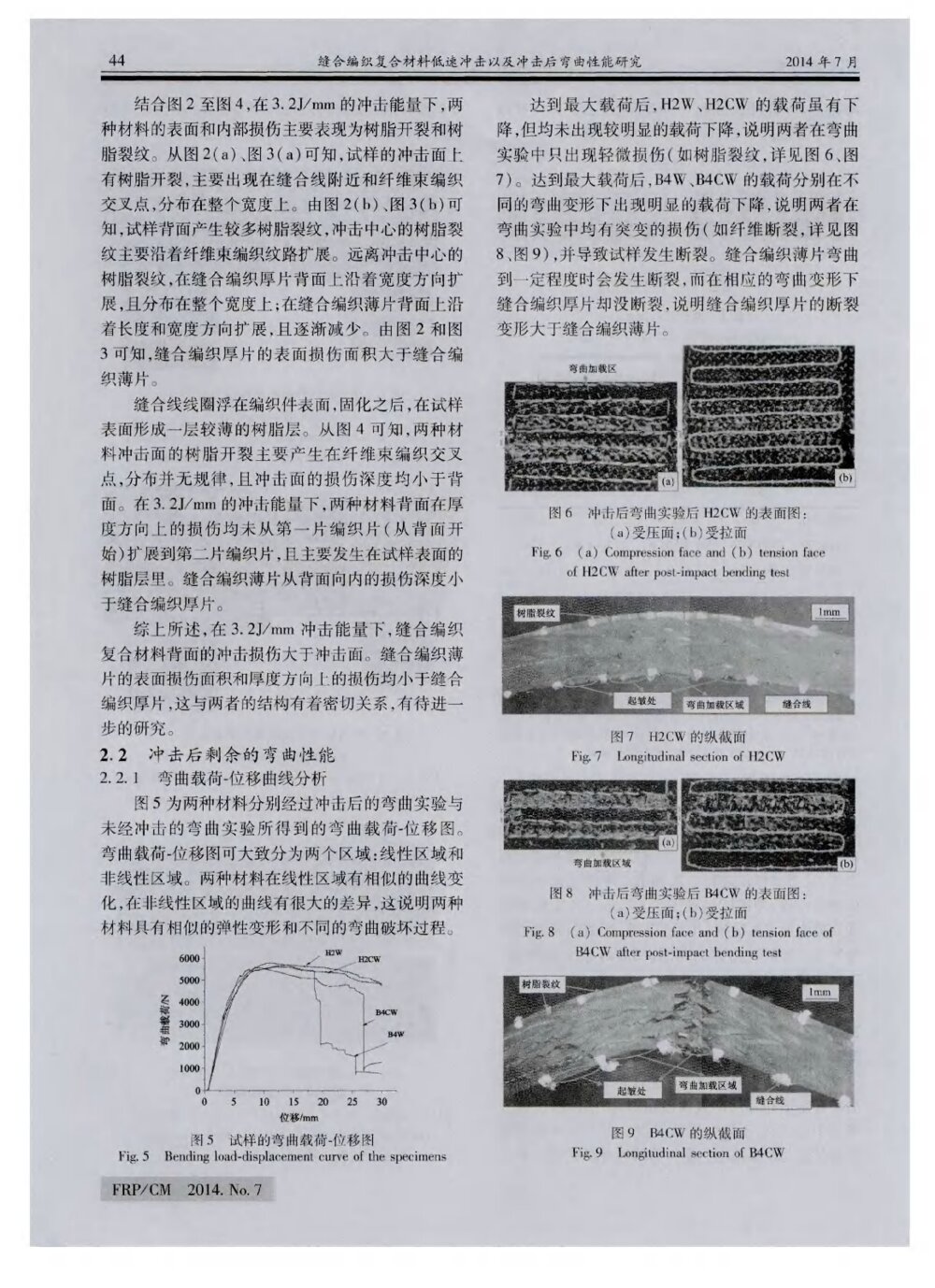
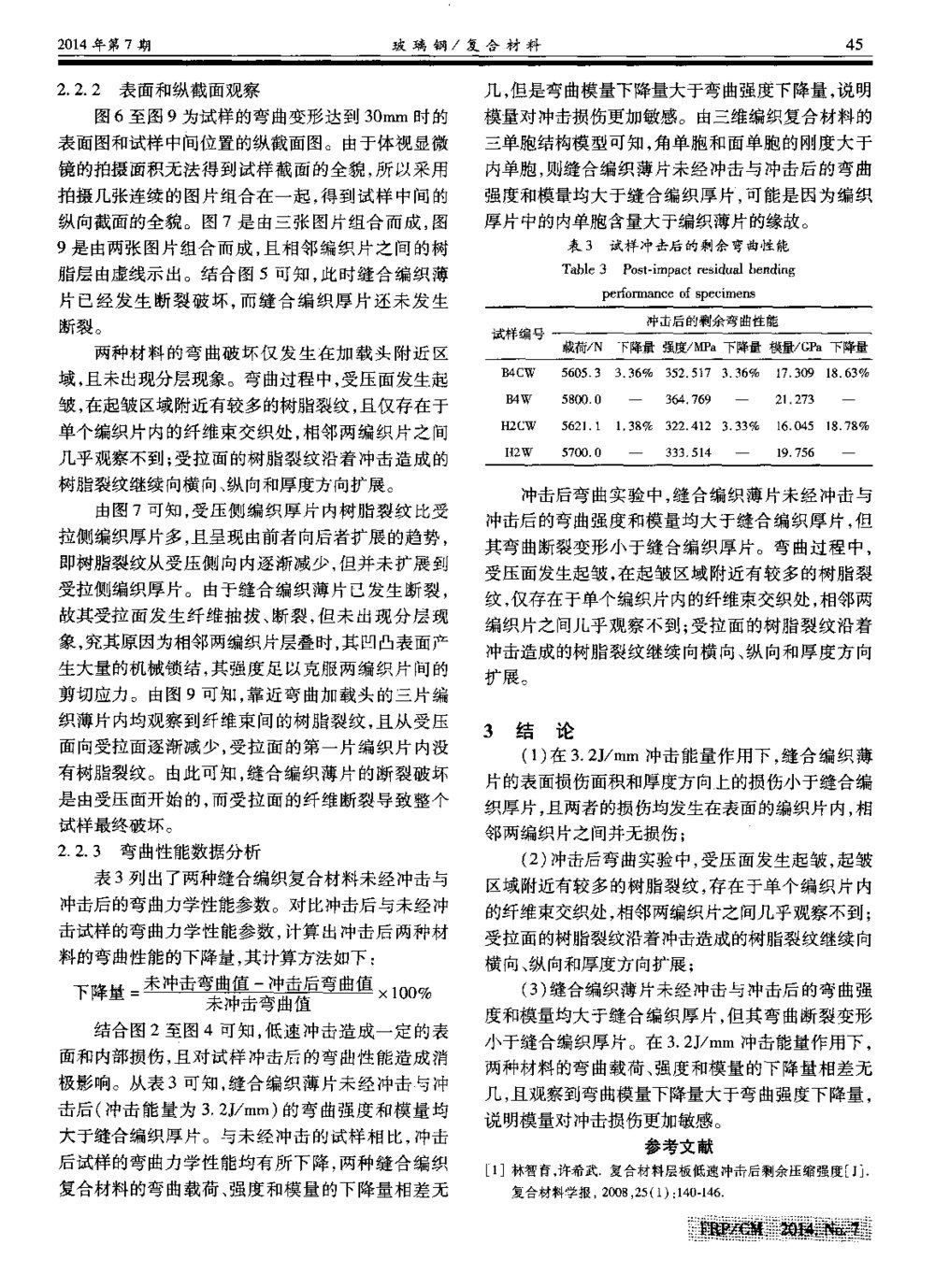
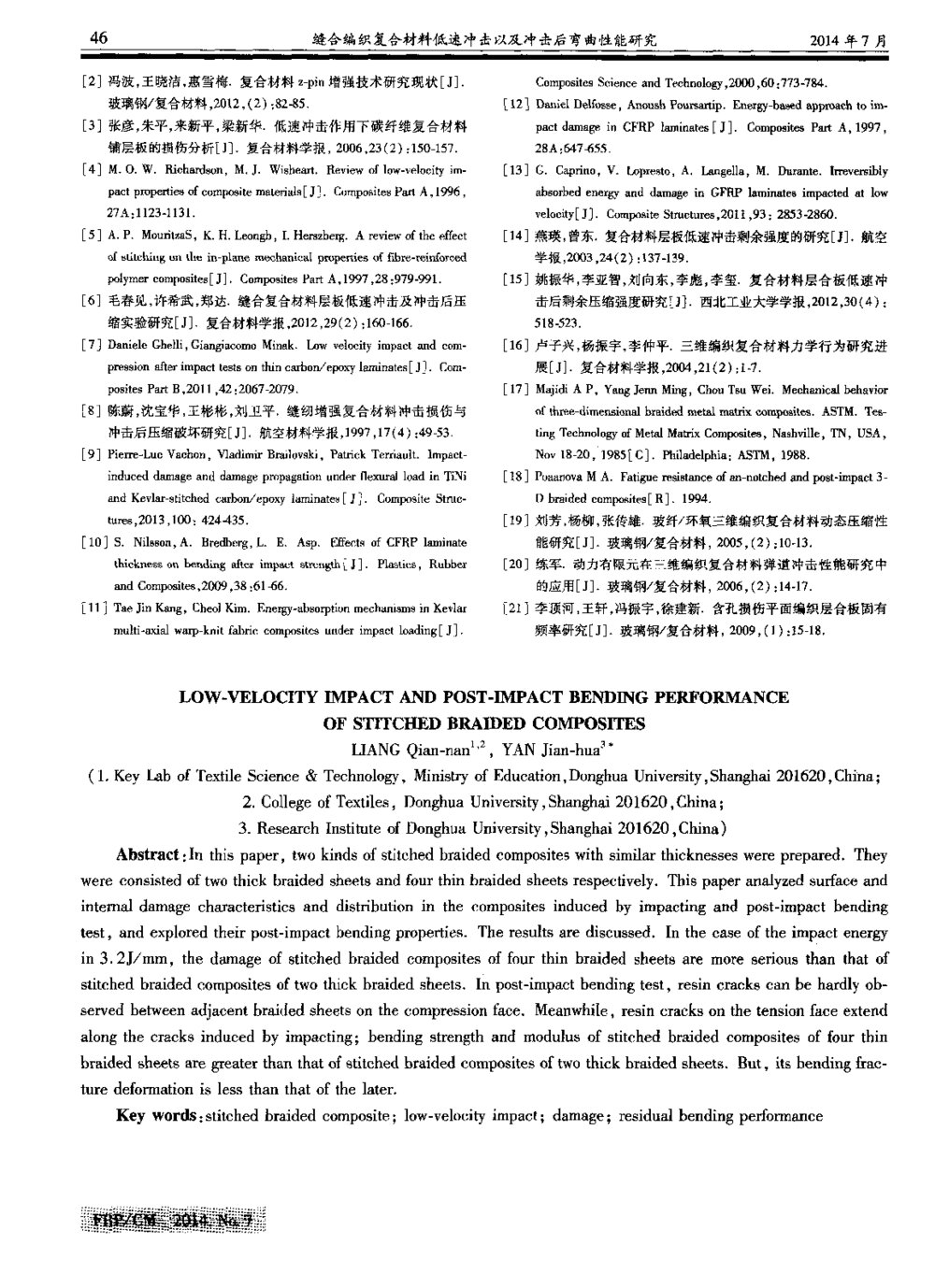
已阅读完毕,您还可以下载文档进行保存
- 1、本文档共5页,内容下载后可编辑。
- 2、本文档内容版权归属内容提供方,所产生的收益全部归内容提供方所有。如果您对本文有版权争议,可选择认领。
- 3、本文档由用户上传,本站不保证质量和数量令人满意,可能有诸多瑕疵,付费之前,请仔细先通过免费阅读内容等途径辨别内容交易风险。如存在严重挂羊头卖狗肉之情形,可联系本站下载客服投诉处理。
42 缝合编织复合材料低速冲击以及冲击后弯曲性能研究 2014年7月 缝合编织复合材料低速冲击以及冲击后弯曲性能研究 梁倩囡,阎建华 (1.东华大学纺织面料技术教育部重点实验室,上海201620; 2.东华大学纺织学院,上海201620;3.东华大学研究院,上海201620) 摘要:两片三维四向编织厚片叠层缝合和四片三维四向编织薄片叠层缝合,固化之后得到两种厚度接近的缝合编织复合 材料。对两种材料进行冲击以及冲击后弯曲实验,分析其表面和内部损伤特征、分布和机理,探讨其冲击后的剩余弯曲性能。 结果表明,3.2J/mm的冲击能量下,缝合编织薄片的表面损伤面积和厚度方向上的损伤小于缝合编织厚片;冲击后弯曲实验 中,两种材料受压面的树脂裂纹在厚度方向上的相邻两编织片之间几乎观察不到,受拉面的树脂裂纹沿着冲击造成的树脂裂 纹继续向横向、纵向和厚度方向扩展;缝合编织薄片未经冲击与冲击后的弯曲强度和弯曲模量均大于缝合编织厚片,但其弯曲 断裂变形小于缝合编织厚片。 关键词:缝合编织复合材料;低速冲击;损伤;剩余弯曲性能 ——— 中图分类号iTB332文献标识码:A文章编号:10030999(2014)07004205 层合复合材料因具有较高的面内比刚度、比强 度等优点而得到广泛应用,但是层间强度低、抗冲击 性能差等缺点也限制了其发展。低速冲击过程中, 层合复合材料会产生基体裂纹、层间分层和纤维断裂,从而降低材料冲击后的力学性能¨ -3]。缝合技 术的引用可改善此缺陷,它加强了层合结构的层间 强度,减少冲击过程中的分层损伤J。缝合层合板 低速冲击以及冲击后力学性能得到了广泛研究,其 中以冲击后压缩性能的研究最多J,而冲击后弯 曲性能的研究相对较少J。大多研究是从力学分 析或能量吸收角度来分析低速冲击以及冲击后力学 行为带来的损伤』,也有研究采用有限元方法模 拟损伤分布,预测冲击后剩余的力学性能 。 编织复合材料因其独特的三维空间网状连续纤 维结构特点,因此具有良好的力学性能¨ 。虽然” Majidi[]、Portanova以及其他学者 对三维编 织复合材料的冲击行为进行了试验研究,但目前关 于三维编织复合材料的低速冲击性能的研究文献还 很少,有待进一步的深入研究,且尚未发现关于缝合 编织复合材料(即缝合编织预制件,然后固化得到的 复合材料)冲击方面的研究。 在实际应用中,编织复合材料在以下两种情况 下使用缝合技术:一种是缝合连接编织件,使之成为 符合要求的整体结构的预制件;另一种是采用Over一 收稿日期: 基金项目: 作者简介: 通讯作者: braiding方法制备预制件时,用缝合方法将各层连接 起来。鉴于此,本文研究分析两种缝合编织复合材 料(缝合编织厚片和缝合编织薄片)冲击及冲击后 弯曲实验过程中的损伤特征、分布和机理,并探讨冲 击后的剩余弯曲性能,为进一步研究三维编织复合 材料在冲击以及冲击后力学作用下的损伤特征和机 理提供参考。 1实验方法 1.1试 样 试样材料为缝合三维四向编织碳纤维/环氧树 脂复合材料,具体分为两种:一种是缝合两片编织厚 片,如图1(a)所示,每个厚片的名义厚度为3mm,其纱线的排列为4× 40(排数× 列数);另一种是缝合 四片编织薄片,如图1(b)所示,每个薄片的名义厚 度为1.3mm,其纱线的排列为2× 40(排数× 列数)。 — 试样尺寸参照ASTMD713612测试要求取为65× 210mm(宽度× 长度)。试样具体制备过程如下:首 先,由四步编织法制得编织片,所用材料为TT00s- 12K碳纤维束;然后,缝合编织片,缝纫线为Kevlar一 29(3000旦尼尔),缝合方式为改进后的锁式缝合, 缝合密度为6× 5mm(行距× 针距),缝合方向为 90。;最后,采用VARTM(树脂转移,真空辅助成型) 固化工艺将所得缝合编织结构固化成型,所用基体 2013.1O一14 上海市科委《上海市科技成果转化和产业化项目》(12521102400) 梁倩囡(1989一),女,硕士,主要从事缝合及编织复合材料低速冲击性能的研究。 阎建华(1956一),男,博士,研究员,主要从事纺织结构复合材料制备及其结构性能的研究。 2014年第7期 玻璃钢/复合材料 45 2.2.2表面和纵截面观察 图6至图9为试样的弯曲变形达到30mm时的 表面图和试样中间位置的纵截面图。由于体视显微 镜的拍摄面积无法得到试样截面的全貌,所以采用 拍摄几张连续的图片组合在一起,得到试样中间的 纵向截面的全貌。图7是由三张图片组合而成,图 9是由两张图片组合而成,且相邻编织片之间的树 脂层由虚线示出。结合图5可知,此时缝合编织薄 片已经发生断裂破坏,而缝合编织厚片还未发生 断裂。 两种材料的弯曲破坏仅发生在加载头附近区 域,且未出现分层现象。弯曲过程中,受压面发生起 皱,在起皱区域附近有较多的树脂裂纹,且仅存在于 单个编织片内的纤维束交织处,相邻两编织片之间 几乎观察不到;受拉面的树脂裂纹沿着冲击造成的 树脂裂纹继续向横向、纵向和厚度方向扩展。 由图7可知,受压侧编织厚片内树脂裂纹比受 拉侧编织厚片多,且呈现由前者向后者扩展的趋势, 即树脂裂纹从受压侧向内逐渐减少,但并未扩展到 受拉侧编织厚片。由于缝合编织薄片已发生断裂, 故其受拉面发生纤维抽拔、断裂,但未出现分层现 象,究其原因为相邻两编织片层叠时,其凹凸表面产 生大量的机械锁结,其强度足以克服两编织片间的 剪切应力。由图9可知,靠近弯曲加载头的三片编 织薄片内均观察到纤维束间的树脂裂纹,且从受压 面向受拉面逐渐减少,受拉面的第一片编织片内没 有树脂裂纹。由此可知,缝合编织薄片的断裂破坏 是由受压面开始的,而受拉面的纤维断裂导致整个 试样最终破坏。 2.2.3弯曲性能数据分析 表3列出了两种缝合编织复合材料未经冲击与 冲击后的弯曲力学性能参数。对比冲击后与未经冲 击试样的弯曲力学性能参数,计算出冲击后两种材 料的弯曲性能的下降量,其计算方法如下: 下降量=× 10。% 结合图2至图4可知,低速冲击造成一定的表 面和内部损伤,且对试样冲击后的弯曲性能造成消 极影响。从表3可知,缝合编织薄片未经冲击与冲 击后(冲击能量为3.2J/ram)的弯曲强度和模量均 大于缝合编织厚片。与未经冲击的试样相比,冲击 后试样的弯曲力学性能均有所下降,两种缝合编织 复合材料的弯曲载荷、强度和模量的下降量相差无 几,但是弯曲模量下降量大于弯曲强度下降量,说明 模量对冲击损伤更加敏感。由三维编织复合材料的 三单胞结构模型可知,角单胞和面单胞的刚度大于 内单胞,则缝合编织薄片未经冲击与冲击后的弯曲 强度和模量均大于缝合编织厚片,可能是因为编织 厚片中的内单胞含量大于编织薄片的缘故。 表3试样冲击后的剩余弯曲性能 — Table3Postimpactresidu ̄bendingper formanceofspecimens 冲击后弯曲实验中,缝合编织薄片未经冲击与 冲击后的弯曲强度和模量均大于缝合编织厚片,但 其弯曲断裂变形小于缝合编织厚片。弯曲过程中, 受压面发生起皱,在起皱区域附近有较多的树脂裂 纹,仅存在于单个编织片内的纤维束交织处,相邻两 编织片之间几乎观察不到;受拉面的树脂裂纹沿着 冲击造成的树脂裂纹继续向横向、纵向和厚度方向 扩展。 3结 论 (1)在3.2J/ram冲击能量作用下,缝合编织薄 片的表面损伤面积和厚度方向上的损伤小于缝合编 织厚片,且两者的损伤均发生在表面的编织片内,相 邻两编织片之间并无损伤; (2)冲击后弯曲实验中,受压面发生起皱,起皱 区域附近有较多的树脂裂纹,存在于单个编织片内 的纤维束交织处,相邻两编织片之间几乎观察不到; 受拉面的树脂裂纹沿着冲击造成的树脂裂纹继续向 横向、纵向和厚度方向扩展; (3)缝合编织薄片未经冲击与冲击后的弯曲强 度和模量均大于缝合编织厚片,但其弯曲断裂变形 小于缝合编织厚片。在3.2J/ram冲击能量作用下, 两种材料的弯曲载荷、强度和模量的下降量相差无 几,且观察到弯曲模量下降量大于弯曲强度下降量, 说明模量对冲击损伤更加敏感。 参考文献 [1]林智育,许希武.复合材料层板低速冲击后剩余压缩强度[J]. 复合材料学报,2008,25(1):140.146. l咄 缝合编织复合材料低速冲击以及冲击后弯曲性能研究 2014年7月 — [2]冯波,王晓洁,惠雪梅.复合材料zpin增强技术研究现状[J]. 玻璃钢/复合材料,2012,(2):82-85. [3]张彦,朱平,来新平,梁新华.低速冲击作用下碳纤维复合材料 — 铺层板的损伤分析[J].复合材料学报,2006,23(2):150157. — [4]M.0.W.Richardson,M.J.Wisheart.Reviewoflowvelocityim. pactpr opertiesofcompositemater ials[J].CompositesPartA,1996, 27A:1123-1131. [5]A.P.MouritzaS,K.H.Leongb,I.Herszberg.Areviewoftheeffect ofstitchingonthein・-planemechanicalpropertiesoffibre-reinforced polymercomposites[J].CompositesPartA,1997,28:979-991. [6]毛春见,许希武,郑达.缝合复合材料层板低速冲击及冲击后压— 缩实验研究[J].复合材料学报,2012,29(2):160166. — [7]DanieleGhelli,GiangiacomoMinak.Lowvelocityimpactandcorn pressionafterimpacttestsonthincarbon/epoxylaminates[J].Ca m- positesPartB,2011,42:2067-2079. [8]陈蔚,沈宝华,王彬彬,刘卫平.缝纫增强复合材料冲击损伤与 冲击后压缩破坏研究[J].航空材料学报,1997,17(4):49-53.— — [9]PieceLucVachon,YladimirBrailovski,PatrickTerriault.Impact induceddamageanddamagepropagationunderflexuralloadinTiNi — — andKevlarstitchedcarbon/epoxylaminates[J].CompositeStmc tures,2013,100:424435.[10]S.Nilsson,A.Bredberg,L.E.Asp.Ef fectsofCFRPlaminate thicknessonbendingafterimpactstrength[J].Plastics,Rubber andComposites,2009,38:61-66. — [11]TaeJinKang,CheolKim.EnergyabsorptionmechanismsinKevlar— — multiaxialwarpknitfabriccompositesunderimpactloading[J]. CompositesScienceandTechnology,2000,60:773 ̄84. —[12]DanielDelfosse,AnoushPoursartip.Energyba sedapproachtoim- pactdamageinCFRPlaminates[J].CompositesPartA,1997, 28A:647_655. [13]G.Caprino,V.Lopresto,A.Langella。M.Durante.Irreversibly absorbedenergyanddamageinGFRPlaminatesimpactedatlow velocity[J].CompositeStructures,2011,93:2853-2860. [14]燕瑛,曾东.复合材料层板低速冲击剩余强度的研究[J].航空 — 学报,2003,24(2):137139. [15]姚振华,李亚智,刘向东,李彪,李玺.复合材料层合板低速冲 击后剩余压缩强度研究[J].西北工业大学学报,2012,30(4): 518_523. [16]卢子兴,杨振宇,李仲平.三维编织复合材料力学行为研究进 展[J].复合材料学报,2004,21(2):1-7. [17]MajidiAP,YangJennMing,ChouTsuWei.Mechanicalbehavior — ofthreedimensionalbraidedmetalmatrixcomposites.ASTM.Tes- tingTechnologyofMetalMatrixComposites,Nashville,TN,USA, Nov18-20,1985[C].Philadelphia:ASTM,1988. — [18]PoaanovaMA.Fatigueresistanceofallnotchedandpost・impact3一 Dbraidedcomposites[R].1994. [19]刘芳,杨柳,张传雄.玻纤/环氧三维编织复合材料动态压缩性 能研究[J].玻璃钢/复合材料,2005,(2):1O一13. [20]练军.动力有限元在三维编织复合材料弹道冲击性能研究中— 的应用[J].玻璃钢/复合材料,2006,(2):1417. [21]李顶河,王轩,冯振宇,徐建新.含孔损伤平面编织层合板固有 频率研究[J].玻璃钢/复合材料,2009,(1):15-18. ’ Ⅱ ’ LUW-VELoCIlYPACrlADPUST-PACTBEDINGPERFoRMACE Ⅱ OFSTITCHEDBRA)EDCoMPoSITES LIANGQian.nan.-.YANJian.hua。 (1.KeylabofTextileScience&Technology,MinistryofEducation,DonghuaUniversity,Shanghai201620,China; 2.CollegeofTextiles,DonghuaUniversity,Shanghai201620,China; 3.ResearchInstituteofDonghHaUniversity,Shanghai201620,China) Abstract:Inthispaper,twokindsofstitchedbraidedcompositeswithsimilarthicknesseswereprepared.They wereconsistedoftwothickbraidedsheetsandfourthinbraidedsheetsrespectively.,I1lispaperanalyzedsurfaceand internaldamagecharacteristicsanddistributioninthecompositesinducedbyimpactingandpost-impactbending test,andexploredtheirpost-impactbendingproperties.Theresultsarediscussed.Inthecaseoftheimpactenergy in3.2J/mm.thedamageofstitchedbraidedcompositesoffourthinbraidedsheetsaremoreseriousthanthatof — — stitchedbraidedcompositesoftwothickbraidedsheets.Inpostimpactbendingtest.resincrackscanbehardlyob servedbetweenadjacentbraidedsheetsonthecompressionface.Meanwhile,resincracksonthetensionfaceextend alongthecracksinducedbyimpacting;bendingstrengthandmodulusofstitchedbraidedcompositesoffourthin — braidedsheetsaregreaterthanthatofstitchedbraidedcompositesoftwothickbraidedsheets.But,itsbendingfrac turedeformationislessthanthatofthelater. Keywords:stitchedbraidedcomposite;low-velocityimpact;damage;residualbendingperformance 静醉鼬
您可能关注的文档
- “离位”增韧复合材料准静态压入损伤特性研究.pdf
- “神舟七号”飞船舱外航天服防护头盔组件的研制.pdf
- “十二五”复合材料发展重点和方向解读.pdf
- “珠串”堆叠超结构的介孔铁酸锌的制备与表征.pdf
- (001)应变对正交相Ca2 P0.25 Si0.75能带结构及光学性质的影响.pdf
- 0.8设计系数用X80管线钢在近中性pH溶液中的应力腐蚀开裂行为.pdf
- 0.20mm CGO硅钢高温退火Goss晶粒起源及异常长大行为研究.pdf
- 0Cr16Ni5Mo低碳马氏体不锈钢的热变形行为及其热加工图.pdf
- 0Cr17Ni4Cu4Nb钢制螺钉断裂原因分析.pdf
- 1.5MW风机叶片模具加热工艺研究与技术创新.pdf
- 1.5MW风机叶片VARI工艺模拟分析及验证.pdf
- 2.5维机织复合材料低速冲击性能研究.pdf
- 2.25Cr-1Mo钢后续热处理中的磷偏聚行为.pdf
- 2A50锻铝三点弯曲试验与高分辨率CT成像分析.pdf
- 2A12与2A11铝合金超声波焊接工艺与组织研究.pdf
- 2MW风机复合材料叶片材料及工艺研究.pdf
- 3Cr2W8V模具钢激光表面相变硬化层性能的研究.pdf
- 3D打印技术及先进应用研究进展.pdf
- 3D打印技术研究现状和关键技术.pdf
- 5%鱼藤酮悬浮剂的研制.pdf

- 分享达人
- 该用户很懒,什么也没介绍
相关文档
- “离位”增韧复合材料准静态压入损伤特性研究.pdf2021-11-235页
- “神舟七号”飞船舱外航天服防护头盔组件的研制.pdf2021-11-233页
- “十二五”复合材料发展重点和方向解读.pdf2021-11-232页
- “珠串”堆叠超结构的介孔铁酸锌的制备与表征.pdf2021-11-235页
- (001)应变对正交相Ca2 P0.25 Si0.75能带结构及光学性质的影响.pdf2021-11-236页
- 0.8设计系数用X80管线钢在近中性pH溶液中的应力腐蚀开裂行为.pdf2021-11-237页
- 0.20mm CGO硅钢高温退火Goss晶粒起源及异常长大行为研究.pdf2021-11-237页