- 文档大小:682.94 KB
- 文档格式:pdf
- 约 6页
- 2022-04-07 发布
- 举报
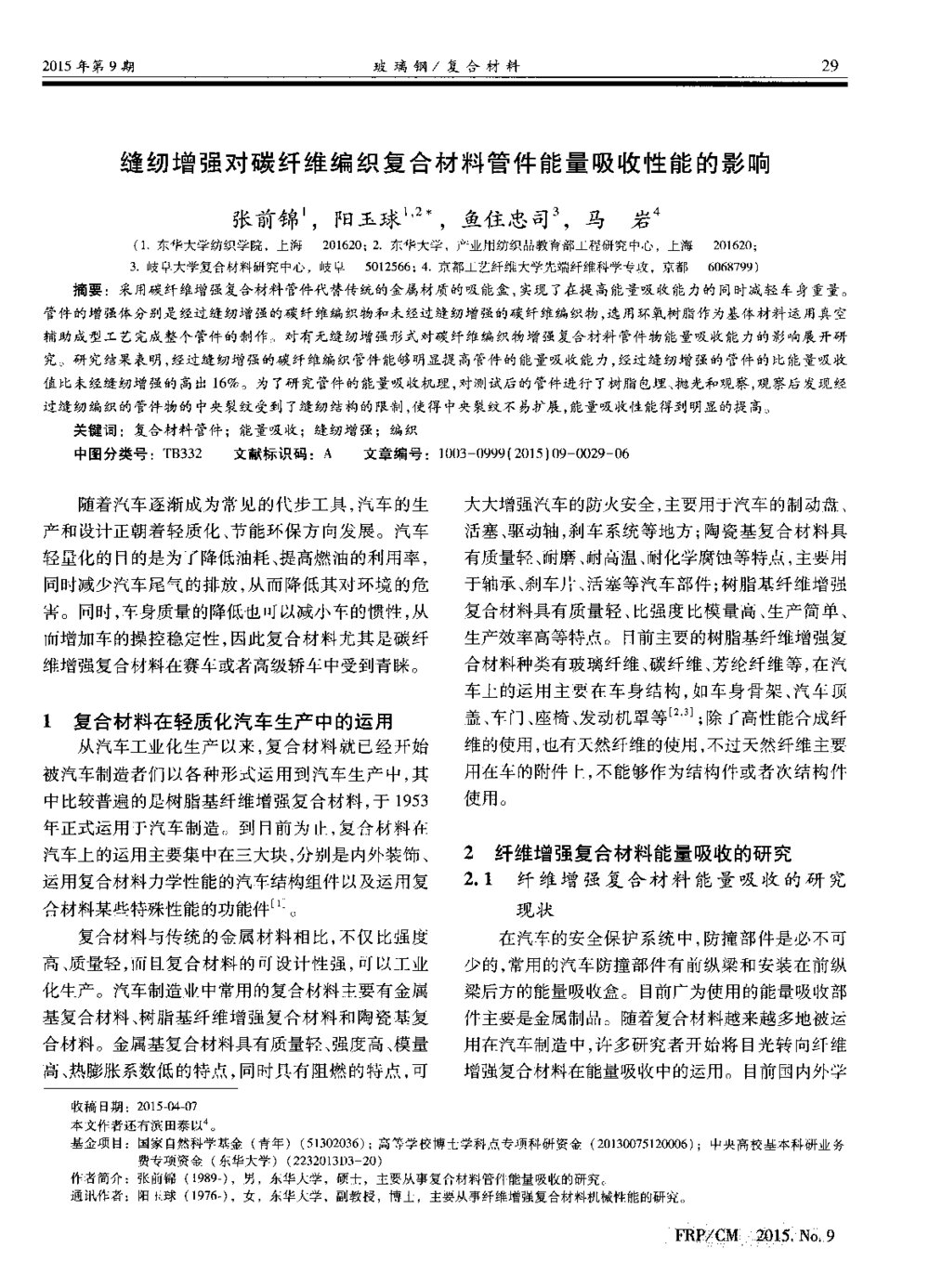
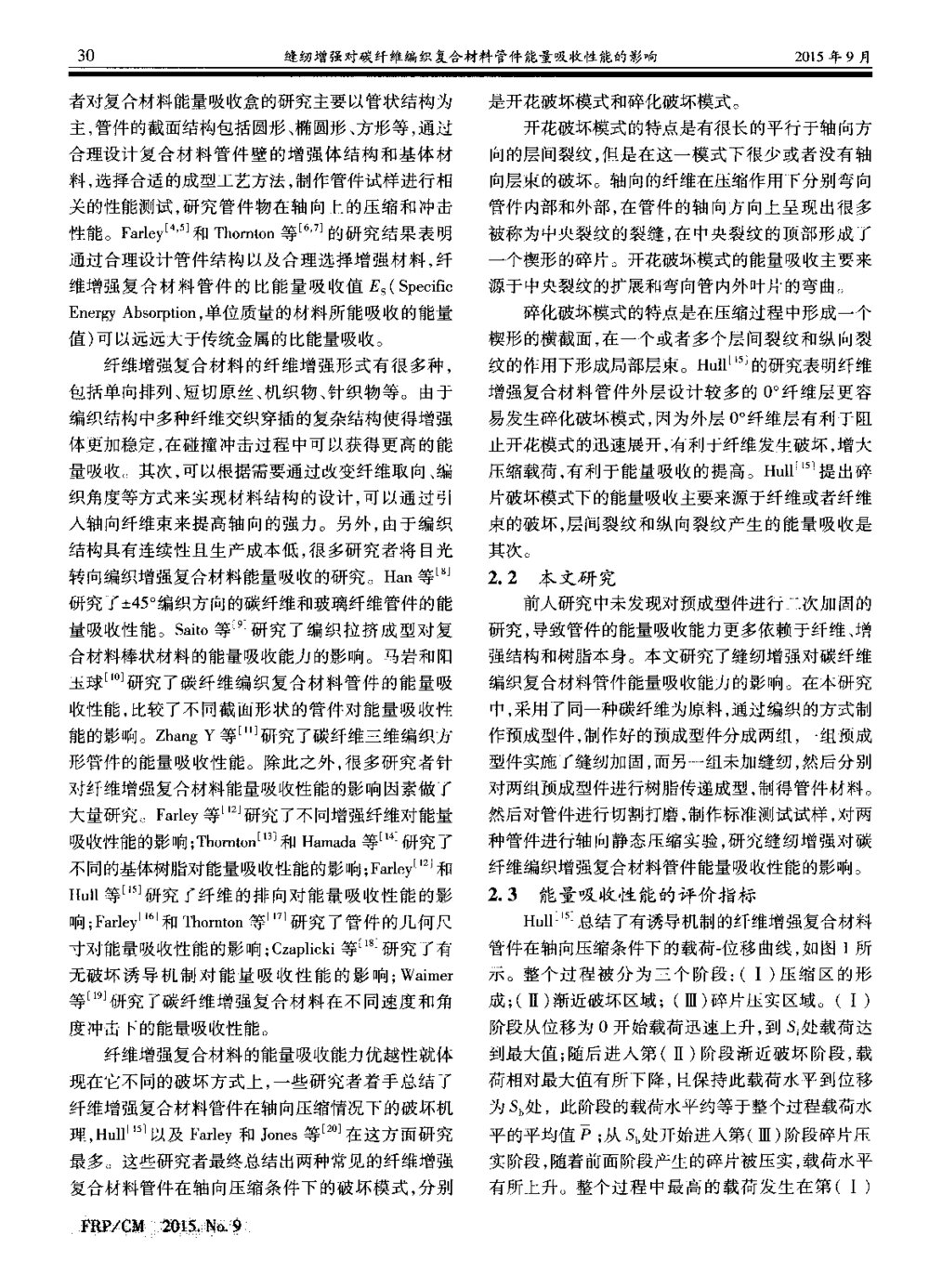
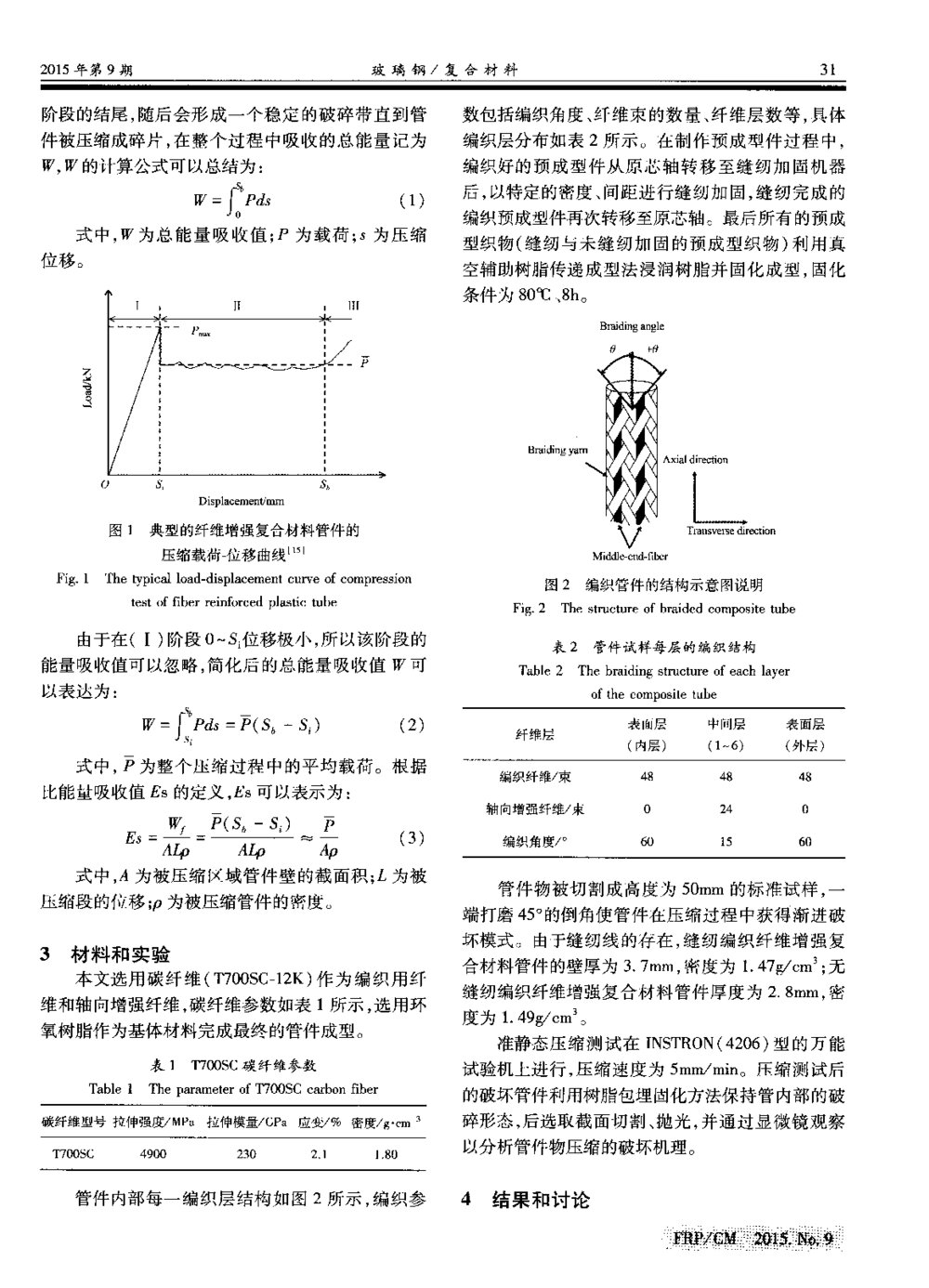
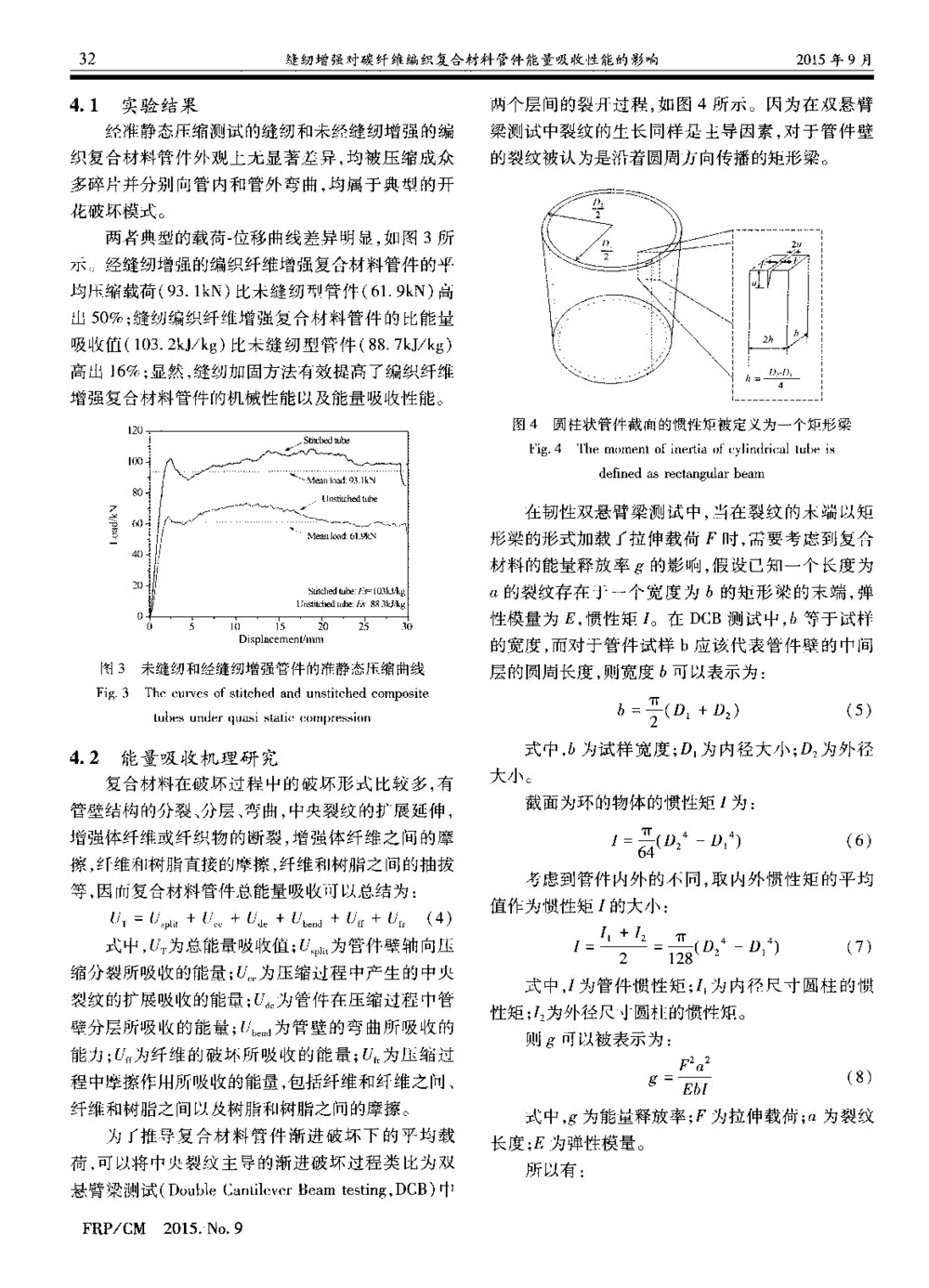
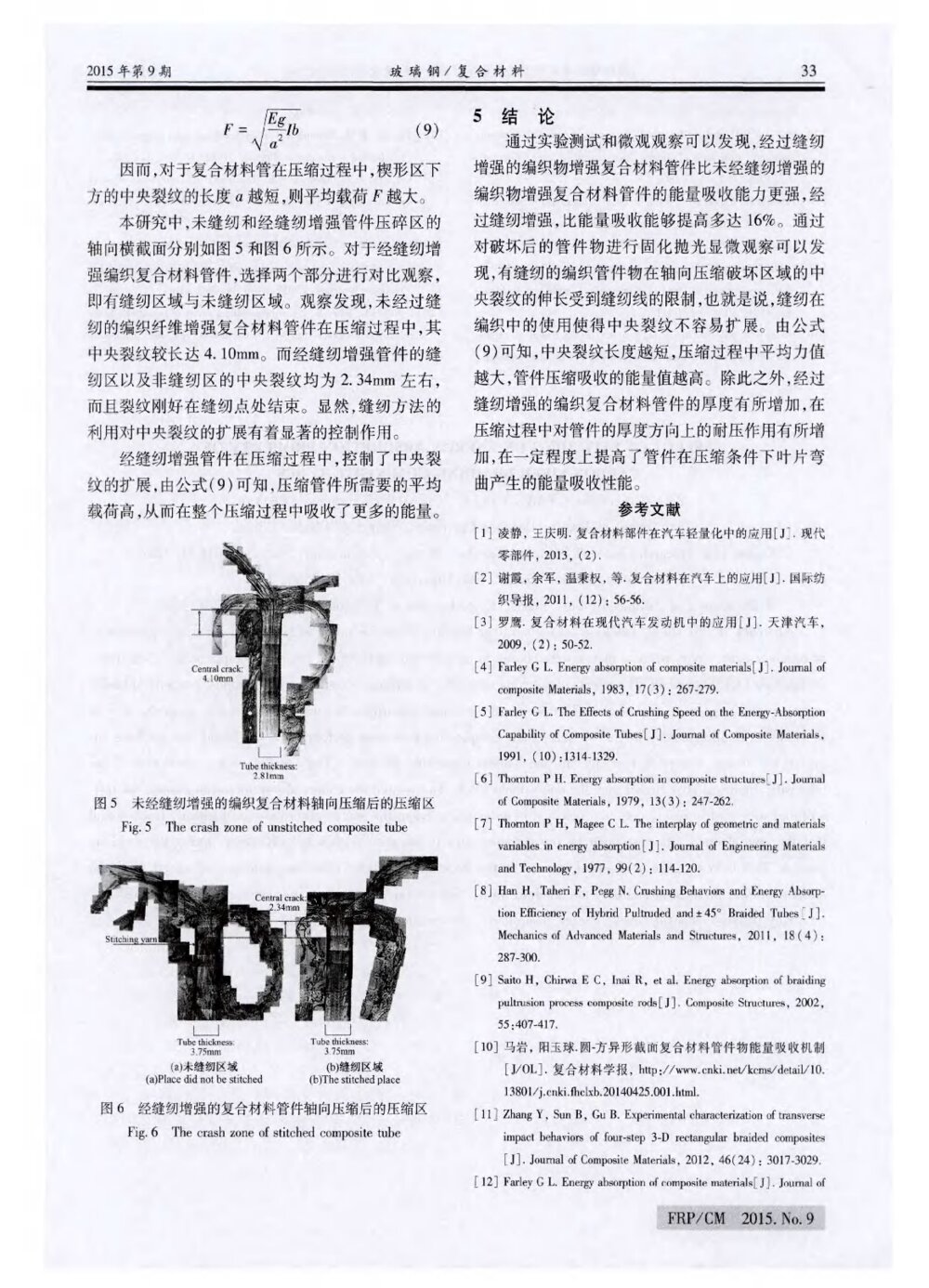
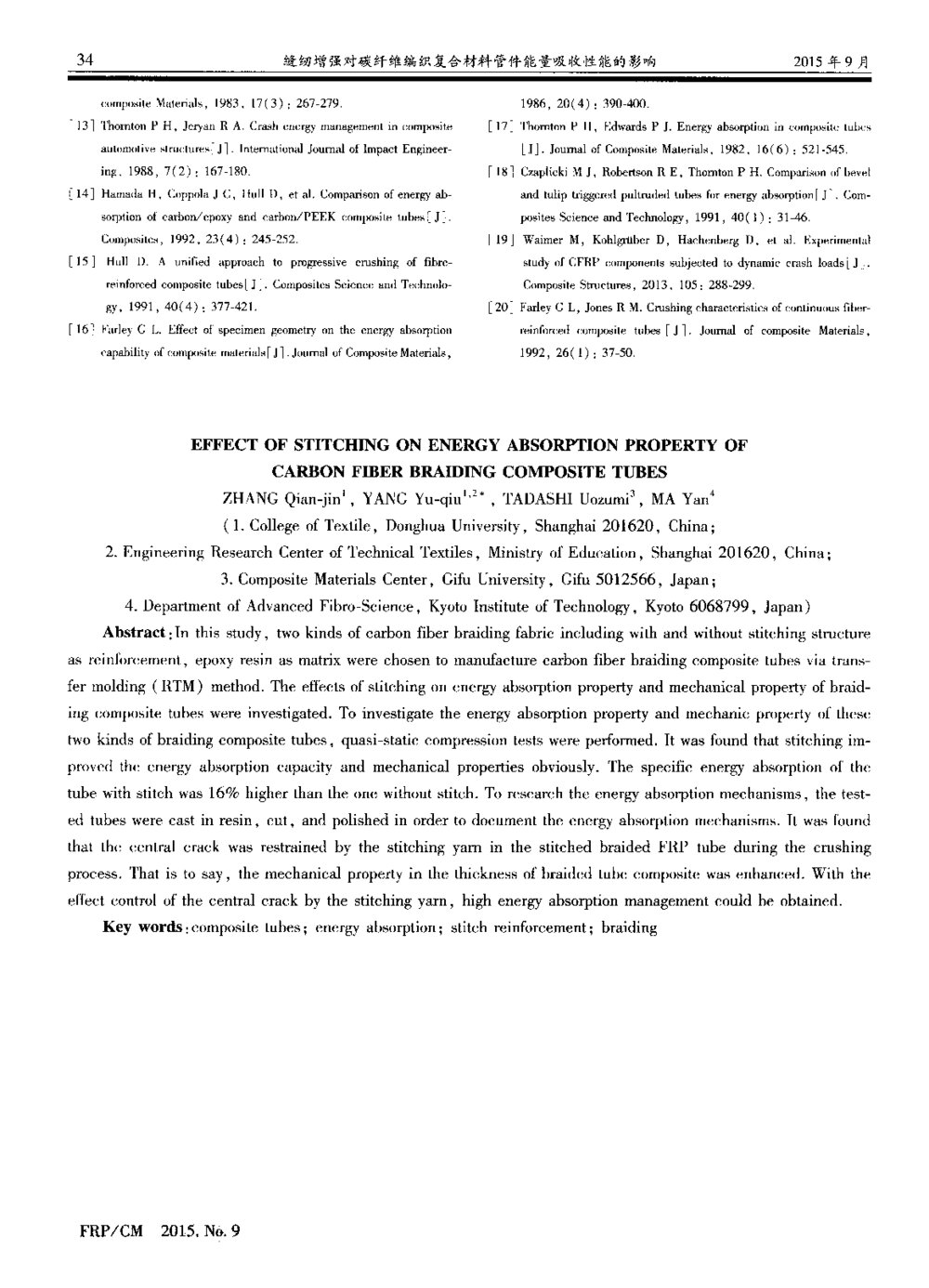
已阅读完毕,您还可以下载文档进行保存
- 1、本文档共6页,内容下载后可编辑。
- 2、本文档内容版权归属内容提供方,所产生的收益全部归内容提供方所有。如果您对本文有版权争议,可选择认领。
- 3、本文档由用户上传,本站不保证质量和数量令人满意,可能有诸多瑕疵,付费之前,请仔细先通过免费阅读内容等途径辨别内容交易风险。如存在严重挂羊头卖狗肉之情形,可联系本站下载客服投诉处理。
2015年第9期玻璃钢/复合材料29缝纫增强对碳纤维编织复合材料管件能量吸收性能的影响张前锦。,阳玉球,鱼住忠司,马岩(1.东华大学纺织学院,上海201620;2.东华大学,产业用纺织品教育部工程研究中心,上海201620;3.岐阜大学复合材料研究中心,岐阜5012566;4.京都工艺纤维大学先端纤维科学专攻,京都6068799)摘要:采用碳纤维增强复合材料管件代替传统的金属材质的吸能盒,实现了在提高能量吸收能力的同时减轻车身重量。管件的增强体分别是经过缝纫增强的碳纤维编织物和未经过缝纫增强的碳纤维编织物,选用环氧树脂作为基体材料运用真空辅助成型工艺完成整个管件的制作。对有无缝纫增强形式对碳纤维编织物增强复合材料管件物能量吸收能力的影响展开研究。研究结果表明,经过缝纫增强的碳纤维编织管件能够明显提高管件的能量吸收能力,经过缝纫增强的管件的比能量吸收值比未经缝纫增强的高出16%。为了研究管件的能量吸收机理,对测试后的管件进行了树脂包埋、抛光和观察,观察后发现经过缝纫编织的管件物的中央裂纹受到了缝纫结构的限制,使得中央裂纹不易扩展,能量吸收性能得到明显的提高。关键词:复合材料管件;能量吸收;缝纫增强;编织中图分类号:TB332文献标识码:A——文章编号:10030999(2015)090029一O6随着汽车逐渐成为常见的代步工具,汽车的生产和设计正朝着轻质化、节能环保方向发展。汽车轻量化的目的是为了降低油耗、提高燃油的利用率,同时减少汽车尾气的排放,从而降低其对环境的危害。同时,车身质量的降低也可以减小车的惯性,从而增加车的操控稳定性,因此复合材料尤其是碳纤维增强复合材料在赛车或者高级轿车中受到青睐。1复合材料在轻质化汽车生产中的运用从汽车工业化生产以来,复合材料就已经开始被汽车制造者们以各种形式运用到汽车生产中,其中比较普遍的是树脂基纤维增强复合材料,于1953年正式运用于汽车制造。到目前为止,复合材料在汽车上的运用主要集中在三大块,分别是内外装饰、运用复合材料力学性能的汽车结构组件以及运用复合材料某些特殊性能的功能件¨J。复合材料与传统的金属材料相比,不仅比强度高、质量轻,而且复合材料的可设计性强,可以工业化生产。汽车制造业中常用的复合材料主要有金属基复合材料、树脂基纤维增强复合材料和陶瓷基复合材料。金属基复合材料具有质量轻、强度高、模量高、热膨胀系数低的特点,同时具有阻燃的特点,可大大增强汽车的防火安全,主要用于汽车的制动盘、活塞、驱动轴,刹车系统等地方;陶瓷基复合材料具有质量轻、耐磨、耐高温、耐化学腐蚀等特点,主要用于轴承、刹车片、活塞等汽车部件;树脂基纤维增强复合材料具有质量轻、比强度比模量高、生产简单、生产效率高等特点。目前主要的树脂基纤维增强复合材料种类有玻璃纤维、碳纤维、芳纶纤维等,在汽车上的运用主要在车身结构,如车身骨架、汽车顶’盖、车门、座椅、发动机罩等;除了高性能合成纤维的使用,也有天然纤维的使用,不过天然纤维主要用在车的附件上,不能够作为结构件或者次结构件使用。2纤维增强复合材料能量吸收的研究2.1纤维增强复合材料能量吸收的研究现状在汽车的安全保护系统中,防撞部件是必不可少的,常用的汽车防撞部件有前纵梁和安装在前纵梁后方的能量吸收盒。目前广为使用的能量吸收部件主要是金属制品。随着复合材料越来越多地被运用在汽车制造中,许多研究者开始将目光转向纤维增强复合材料在能量吸收中的运用。目前国内外学—收稿日期:2015-0407本文作者还有滨田泰以。基金项目:国家自然科学基金(青年)(51302036);高等学校博士学科点专项科研资金(20l30075120006);中央高校基本科研业务费专项资金(东华大学)(2232013D3-20)作者简介:张前锦(1989一),男,东华大学,硕士,主要从事复合材料管件能量吸收的研究。通讯作者:阳玉球(1976一),女,东华大学,副教授,博士,主要从事纤维增强复合材料机械性能的研究。FRP/CM20I5,No.930缝纫增强对碳纤维编织复合材料管件能量吸收性能的影响2015年9月者对复合材料能量吸收盒的研究主要以管状结构为主,管件的截面结构包括圆形、椭圆形、方形等,通过合理设计复合材料管件壁的增强体结构和基体材料,选择合适的成型工艺方法,制作管件试样进行相关的性能测试,研究管件物在轴向上的压缩和冲击’性能。Farley和Thornton等的研究结果表明通过合理设计管件结构以及合理选择增强材料,纤维增强复合材料管件的比能量吸收值E(SpecificEnergyAbsorption,单位质量的材料所能吸收的能量值)可以远远大于传统金属的比能量吸收。纤维增强复合材料的纤维增强形式有很多种,包括单向排列、短切原丝、机织物、针织物等。由于编织结构中多种纤维交织穿插的复杂结构使得增强体更加稳定,在碰撞冲击过程中可以获得更高的能量吸收。其次,可以根据需要通过改变纤维取向、编织角度等方式来实现材料结构的设计,可以通过引入轴向纤维束来提高轴向的强力。另外,由于编织结构具有连续性且生产成本低,很多研究者将目光转向编织增强复合材料能量吸收的研究。Han等研究了+45。编织方向的碳纤维和玻璃纤维管件的能量吸收性能。Saito等研究了编织拉挤成型对复合材料棒状材料的能量吸收能力的影响。马岩和阳玉球¨研究了碳纤维编织复合材料管件的能量吸收性能,比较了不同截面形状的管件对能量吸收性能的影响。ZhangY等¨研究了碳纤维三维编织方形管件的能量吸收性能。除此之外,很多研究者针对纤维增强复合材料能量吸收性能的影响因素做了大量研究。Farley等¨。研究了不同增强纤维对能量吸收性能的影响;Thornton【13]和Hamada等研究了不同的基体树脂对能量吸收性能的影响;Farley¨和Hull等¨研究了纤维的排向对能量吸收性能的影响;Farleyl16]和Thornton等¨研究了管件的几何尺寸对能量吸收性能的影响;Czaplicki等¨驯研究了有无破坏诱导机制对能量吸收性能的影响;Waimer等¨研究了碳纤维增强复合材料在不同速度和角度冲击下的能量吸收性能。纤维增强复合材料的能量吸收能力优越性就体现在它不同的破坏方式上,一些研究者着手总结了纤维增强复合材料管件在轴向压缩情况下的破坏机理,Hull15]以及Farley和Jones等在这方面研究最多。这些研究者最终总结出两种常见的纤维增强复合材料管件在轴向压缩条件下的破坏模式,分别m,CM2015iNO:9是开花破坏模式和碎化破坏模式。开花破坏模式的特点是有很长的平行于轴向方向的层间裂纹,但是在这一模式下很少或者没有轴向层束的破坏。轴向的纤维在压缩作用下分别弯向管件内部和外部,在管件的轴向方向上呈现出很多被称为中央裂纹的裂缝,在中央裂纹的顶部形成了一个楔形的碎片。开花破坏模式的能量吸收主要来源于中央裂纹的扩展和弯向管内外叶片的弯曲。碎化破坏模式的特点是在压缩过程中形成一个楔形的横截面,在一个或者多个层间裂纹和纵向裂纹的作用下形成局部层束。Hull_1的研究表明纤维增强复合材料管件外层设计较多的0。纤维层更容易发生碎化破坏模式,因为外层0。纤维层有利于阻止开花模式的迅速展开,有利于纤维发生破坏,增大压缩载荷,有利于能量吸收的提高。Hullll提出碎片破坏模式下的能量吸收主要来源于纤维或者纤维束的破坏,层间裂纹和纵向裂纹产生的能量吸收是其次。2.2本文研究前人研究中未发现对预成型件进行二次加固的研究,导致管件的能量吸收能力更多依赖于纤维、增强结构和树脂本身。本文研究了缝纫增强对碳纤维编织复合材料管件能量吸收能力的影响。在本研究中,采用了同一种碳纤维为原料,通过编织的方式制作预成型件,制作好的预成型件分成两组,一组预成型件实施了缝纫加固,而另一组未加缝纫,然后分别对两组预成型件进行树脂传递成型,制得管件材料。然后对管件进行切割打磨,制作标准测试试样,对两种管件进行轴向静态压缩实验,研究缝纫增强对碳纤维编织增强复合材料管件能量吸收性能的影响。2.3能量吸收性能的评价指标Hulll151总结了有诱导机制的纤维增强复合材料管件在轴向压缩条件下的载荷.位移曲线,如图1所示。整个过程被分为三个阶段:(I)压缩区的形成;(1I)渐近破坏区域;(HI)碎片压实区域。(I)阶段从位移为0开始载荷迅速上升,到5i处载荷达到最大值;随后进入第(1I)阶段渐近破坏阶段,载荷相对最大值有所下降,且保持此载荷水平到位移为5处,此阶段的载荷水平约等于整个过程载荷水平的平均值P;从Js处开始进入第(1lI)阶段碎片压实阶段,随着前面阶段产生的碎片被压实,载荷水平有所上升。整个过程中最高的载荷发生在第(I)2015年第9期玻璃钢/复合材料31阶段的结尾,随后会形成一个稳定的破碎带直到管件被压缩成碎片,在整个过程中吸收的总能量记为,的计算公式可以总结为:rsbW=IPds(1)J0式中,为总能量吸收值;P为载荷;s为压缩位移。II儿-III—’’一:一:一:一==:=::F,UDisplacement,mm图1典型的纤维增强复合材料管件的压缩载荷一位移曲线n]Fig.1Thetypicalload-displacementcurveofcompressiontestoffiberreinforcedplastictube由于在(I)阶段0~S;位移极小,所以该阶段的能量吸收值可以忽略,简化后的总能量吸收值可以表达为:r一=IPds=P(S6一S)(2)JSi式中,P为整个压缩过程中的平均载荷。根据比能量吸收值Es的定义,Es可以表示为:EsP(S一S)——=一≈——AAAp(3)式中,A为被压缩区域管件壁的截面积;L为被压缩段的位移;p为被压缩管件的密度。3材料和实验本文选用碳纤维(T700SC一12K)作为编织用纤维和轴向增强纤维,碳纤维参数如表1所示,选用环氧树脂作为基体材料完成最终的管件成型。表1T700SC碳纤维参数Table1TheparameterofT700SCcarbonfiber碳纤维型号拉伸强度/MPa拉伸模 ̄/GPa应变/%密度/g.cm数包括编织角度、纤维束的数量、纤维层数等,具体编织层分布如表2所示。在制作预成型件过程中,编织好的预成型件从原芯轴转移至缝纫加固机器后,以特定的密度、间距进行缝纫加固,缝纫完成的编织预成型件再次转移至原芯轴。最后所有的预成型织物(缝纫与未缝纫加固的预成型织物)利用真空辅助树脂传递成型法浸润树脂并固化成型,固化℃条件为80、8h。BraidingangleiI.......-_.图2编织管件的结构示意图说明Fig.2Thestructureofbraidedcompositetube表2管件试样每层的编织结构Table2Thebraidingstructureofeachlayerofthecompositetube管件物被切割成高度为50mm的标准试样,一端打磨45。的倒角使管件在压缩过程中获得渐进破坏模式。由于缝纫线的存在,缝纫编织纤维增强复合材料管件的壁厚为3.7mm,密度为1.47g/cm;无缝纫编织纤维增强复合材料管件厚度为2.8ram,密度为1.49g/cm。准静态压缩测试在INSTRON(4206)型的万能试验机上进行,压缩速度为5mm/min。压缩测试后的破坏管件利用树脂包埋固化方法保持管内部的破碎形态,后选取截面切割、抛光,并通过显微镜观察以分析管件物压缩的破坏机理。管件内部每一编织层结构如图2所示,编织参4结果和讨论’/(&2So・9薯■蚕京032缝纫增强对碳纤维编织复合材料管件能量吸收性能的影响4.1实验结果经准静态压缩测试的缝纫和未经缝纫增强的编织复合材料管件外观上无显著差异,均被压缩成众多碎片并分别向管内和管外弯曲,均属于典型的开花破坏模式。两者典型的载荷一位移曲线差异明显,如图3所示。经缝纫增强的编织纤维增强复合材料管件的平均压缩载荷(93.1kN)比未缝纫型管件(61.9kN)高出50%;缝纫编织纤维增强复合材料管件的比能量吸收值(103.2kJ/kg)比未缝纫型管件(88.7kJ/kg)高出16%;显然,缝纫加固方法有效提高了编织纤维增强复合材料管件的机械性能以及能量吸收性能。图3未缝纫和经缝纫增强管件的准静态压缩曲线Fig.3Thecurvesofstitchedandunstitchedcompositetubesunderquasistaticcompression4.2能量吸收机理研究复合材料在破坏过程中的破坏形式比较多,有管壁结构的分裂、分层、弯曲,中央裂纹的扩展延伸,增强体纤维或纤织物的断裂,增强体纤维之间的摩擦,纤维和树脂直接的摩擦,纤维和树脂之间的抽拔等,因而复合材料管件总能量吸收可以总结为:Ur=U。1.t+U+Ⅱ+Ubd++U(4)式中,为总能量吸收值;U为管件壁轴向压缩分裂所吸收的能量;为压缩过程中产生的中央裂纹的扩展吸收的能量;U为管件在压缩过程中管壁分层所吸收的能量;U为管壁的弯曲所吸收的能力;U为纤维的破坏所吸收的能量;U为压缩过程中摩擦作用所吸收的能量,包括纤维和纤维之问、纤维和树脂之间以及树脂和树脂之间的摩擦。为了推导复合材料管件渐进破坏下的平均载荷,可以将中央裂纹主导的渐进破坏过程类比为双悬臂梁测试(DoubleCantileverBeamtesting,DCB)中FRP/CM2015.No.9两个层间的裂开过程,如图4所示。因为在双悬臂梁测试中裂纹的生长同样是主导因素,对于管件壁的裂纹被认为是沿着圆周方向传播的矩形梁。图4圆柱状管件截面的惯性矩被定义为一个矩形梁ng.4Themomentofinertiaofcylindricaltubeisdefinedasrectangularbeam在韧性双悬臂梁测试中,当在裂纹的末端以矩形梁的形式加载了拉伸载荷F时,需要考虑到复合材料的能量释放率g的影响,假设已知一个长度为a的裂纹存在于一个宽度为b的矩形梁的末端,弹性模量为E,惯性矩,。在DCB测试中,b等于试样的宽度,而对于管件试样b应该代表管件壁的中间层的圆周长度,则宽度b可以表示为:b=(D+D)(5)式中,b为试样宽度;D。为内径大小;D为外径大小。截面为环的物体的惯性矩,为:,=(D24)(6)考虑到管件内外的不同,取内外惯性矩的平均值作为惯性矩,的大小:,=2=128(。4一(7)、J,/式中,,为管件惯性矩;,为内径尺寸圆柱的惯性矩;,为外径尺寸圆柱的惯性矩。则g可以被表示为:g=(8)L式中,g为能量释放率;F为拉伸载荷;a为裂纹长度;E为弹性模量。所以有:34缝纫增强对碳纤维编织复合材料管件能量吸收性能的影响2015年9月—compositeMaterials,1983,17(3):267279.[13]ThorntonPH,JeryanRA.Crashenergymanagementincomposite—automotivestructures[J].InternationalJournalofImpactEngineering,1988,7(2):167-180.—[14]HamadaH,CoppolaJC,HullD,eta1.Comparisonofenergyabsorptionofcarbon/epoxyandcarbon/PEEKcompositetubes[J].—Composites,1992,23(4):245252.—[15]HullDAunifiedapproachtoprogressivecrushingoffibre—reinforcedcmnpositetubes[J].CompositesScienceandTechnologY,1991,40(4):377-421.[16]FarleyGI.Effectofspecimengeometryontheenergyabsorptioncapabilityofcompositematerials[J].JournalofCompositeMaterials,—1986,20(4):390400.[17]ThorntonPH,EdwardsPJ.Energyabsorptionincompositetubes—[J].JournalofCompositeMaterials,1982,16(6):521545.[18]CzaplickiMJ,RobertsonRE,ThorntonPH.Comparisonofbevel—andtuliptriggeredpultrudedtubesforenergyabsorption[J].Corn—positesScienceandTechnology,1991,40(1):3146.[19]WaimerM,KohlgraberD,HachenbergD,eta1.ExperimentalstudyofCFRPcomponentssubjectedtodynamiccrashloads[J].—CompositeStructures,2013,105:288299.—[20]FarleyGL,JonesRM.Crushingcharacteristicsofcontinuousfiberreinforcedcompositetubes[J].JournalofcompositeMaterials,—1992,26(1):3750.’’’’’E量IEC1USl_lICHINGONENERGYABSORPTIONPROPERTYOFCARBONFIBERBRAIDIN『GCOMPoSITETUBES—ZHANGQian-jin,YANGYuqiu',TADASHIUozumi,MAYan(1.CollegeofTextile,DonghuaUniversity,Shanghai201620,China;2.EngineeringResearchCenterofTechnicalTextiles,MinistryofEducation,Shanghai201620,China;3.CompositeMaterialsCenter,GifuUniversity,Gifu5012566,Japan;—4.DepartmentofAdvancedFibroScience,KyotoInstituteofTechnology,Kyoto6068799,Japan)Abstract:Inthisstudy,twokindsofcarbonfiberbraidingfabricincludingwithandwithoutstitchingstructure—asreinforcement,epoxyresinasmatrixwerechosentomanufacturecarbonfiberbraidingcompositetubesviatransfermolding(RTM)method.Theeffectsofstitchingonenergyabsorptionproper—tyandmechanicalpropertyofbraidingcompositetubeswereinvestigated.Toinvestigatetheenergyabsorptionpropertyandmechanicpropertyofthese——twokindsofbraidingcompositetubes,quasistaticcompressiontestswereperformed.Itwasfoundthatstitchingimprovedtheenergyabsorptioncapacityandmechanicalpropertiesobviously.Thespecificenergyabsorptionofthe—tubewithstitchwas16%higherthantheonewithoutstitch.Toresearchtheenergyabsorptionmechanisms,thetestedtubeswerecastinresin,cut,andpolishedinordertodocumenttheenergyabsorptionmechanisms.ItwasfoundthatthecentralcrackwasrestrainedbythestitchingyarninthestitchedbraidedFRPtubeduringthecrushingprocess.Thatistosay,themechanicalpropertyinthethicknessofbraidedtubecompositewasenhanced.Withtheeffectcontrolofthecentralcrackbythestitchingyarn,highenergyabsorptionmanagementcouldbeobtained.Keywords:compositetubes;energyabsorption;stitchreinforcement;braidingFRP/CM20l5.No.9
您可能关注的文档
- “离位”增韧复合材料准静态压入损伤特性研究.pdf
- “神舟七号”飞船舱外航天服防护头盔组件的研制.pdf
- “十二五”复合材料发展重点和方向解读.pdf
- “珠串”堆叠超结构的介孔铁酸锌的制备与表征.pdf
- (001)应变对正交相Ca2 P0.25 Si0.75能带结构及光学性质的影响.pdf
- 0.8设计系数用X80管线钢在近中性pH溶液中的应力腐蚀开裂行为.pdf
- 0.20mm CGO硅钢高温退火Goss晶粒起源及异常长大行为研究.pdf
- 0Cr16Ni5Mo低碳马氏体不锈钢的热变形行为及其热加工图.pdf
- 0Cr17Ni4Cu4Nb钢制螺钉断裂原因分析.pdf
- 1.5MW风机叶片模具加热工艺研究与技术创新.pdf
- 1.5MW风机叶片VARI工艺模拟分析及验证.pdf
- 2.5维机织复合材料低速冲击性能研究.pdf
- 2.25Cr-1Mo钢后续热处理中的磷偏聚行为.pdf
- 2A50锻铝三点弯曲试验与高分辨率CT成像分析.pdf
- 2A12与2A11铝合金超声波焊接工艺与组织研究.pdf
- 2MW风机复合材料叶片材料及工艺研究.pdf
- 3Cr2W8V模具钢激光表面相变硬化层性能的研究.pdf
- 3D打印技术及先进应用研究进展.pdf
- 3D打印技术研究现状和关键技术.pdf
- 5%鱼藤酮悬浮剂的研制.pdf

- 周大爷
- 该用户很懒,什么也没介绍
相关文档
- “离位”增韧复合材料准静态压入损伤特性研究.pdf2021-11-235页
- “神舟七号”飞船舱外航天服防护头盔组件的研制.pdf2021-11-233页
- “十二五”复合材料发展重点和方向解读.pdf2021-11-232页
- “珠串”堆叠超结构的介孔铁酸锌的制备与表征.pdf2021-11-235页
- (001)应变对正交相Ca2 P0.25 Si0.75能带结构及光学性质的影响.pdf2021-11-236页
- 0.8设计系数用X80管线钢在近中性pH溶液中的应力腐蚀开裂行为.pdf2021-11-237页
- 0.20mm CGO硅钢高温退火Goss晶粒起源及异常长大行为研究.pdf2021-11-237页