- 文档大小:426.8 KB
- 文档格式:pdf
- 约 6页
- 2022-04-08 发布
- 举报
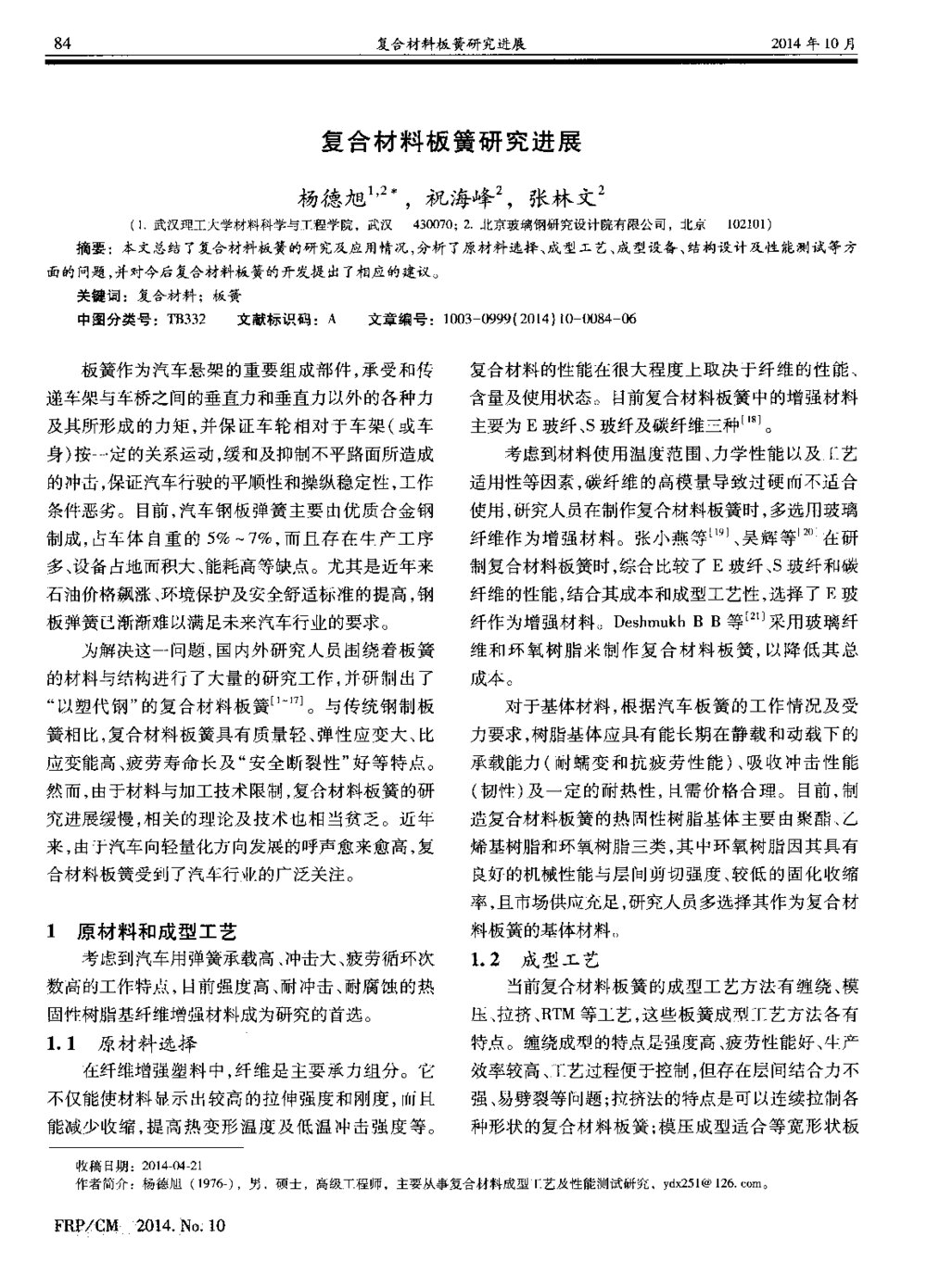
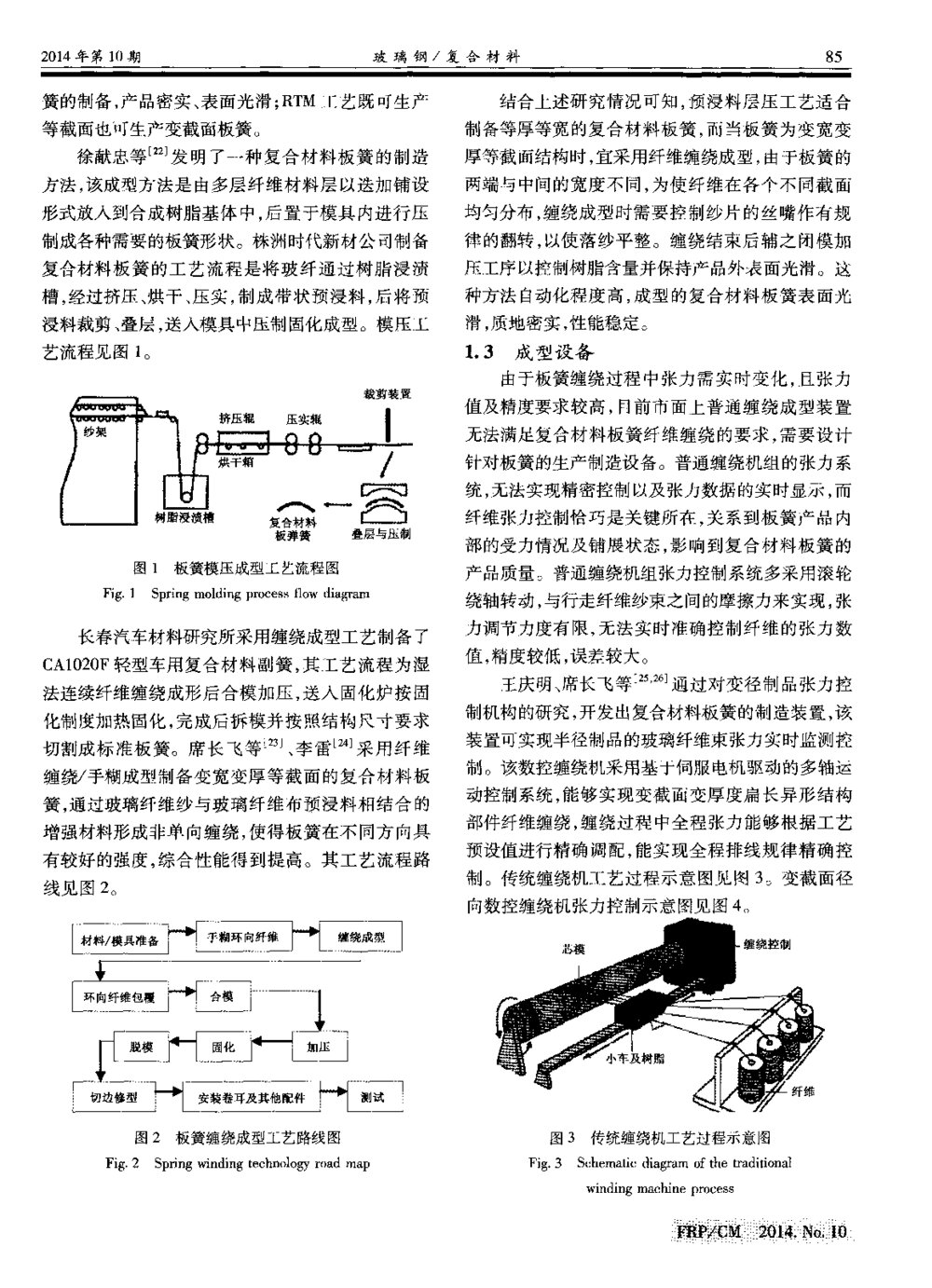
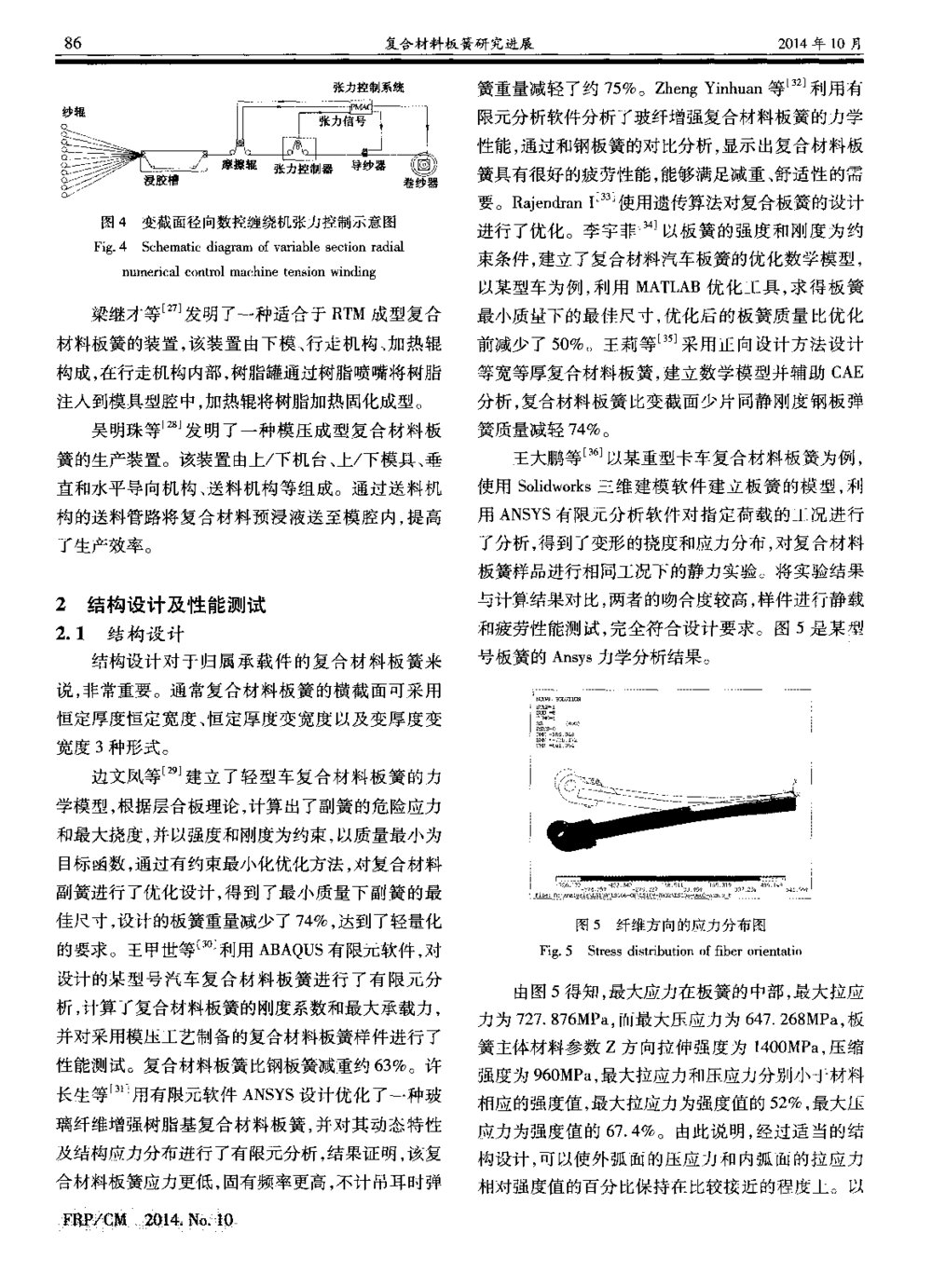
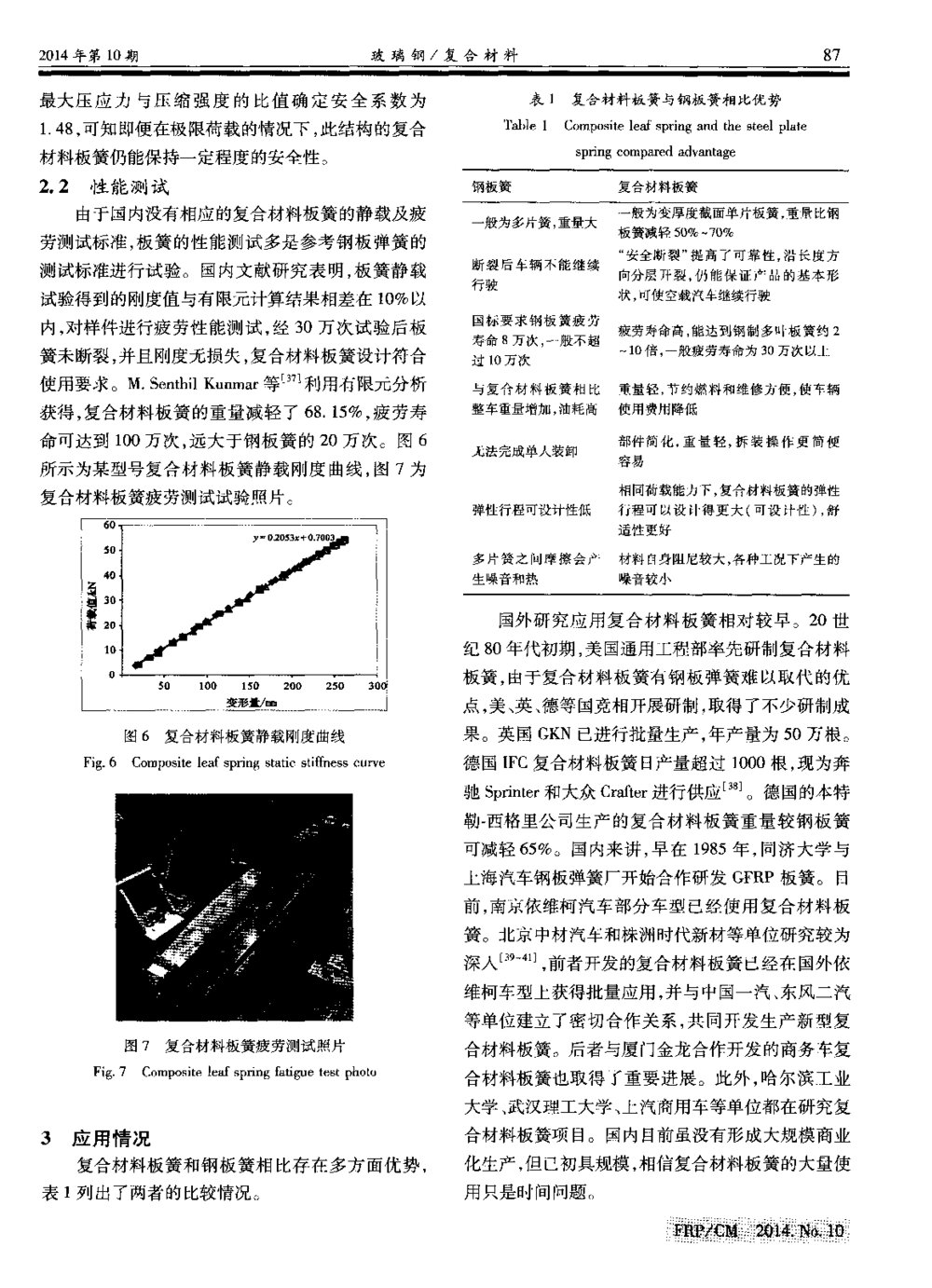
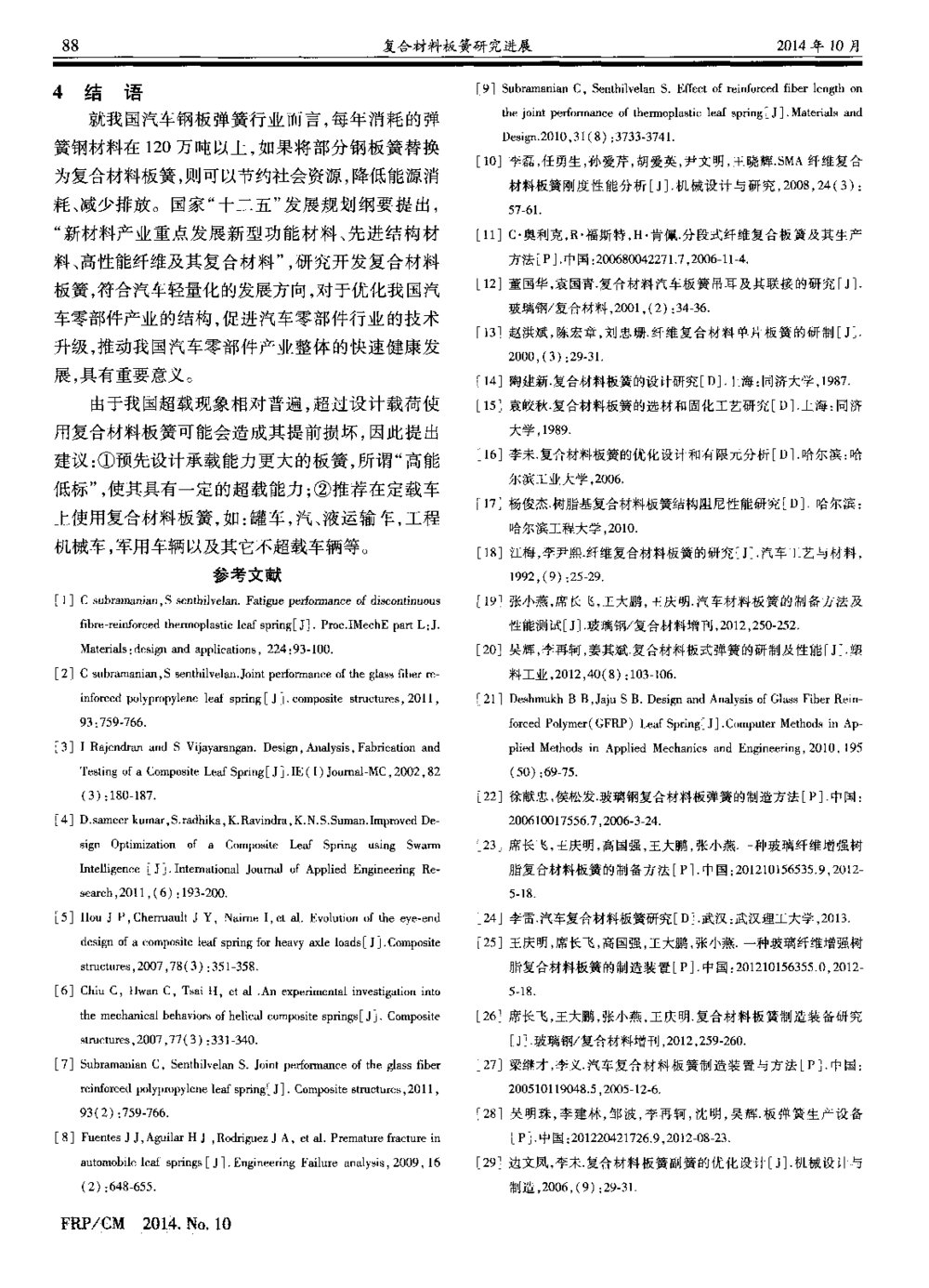
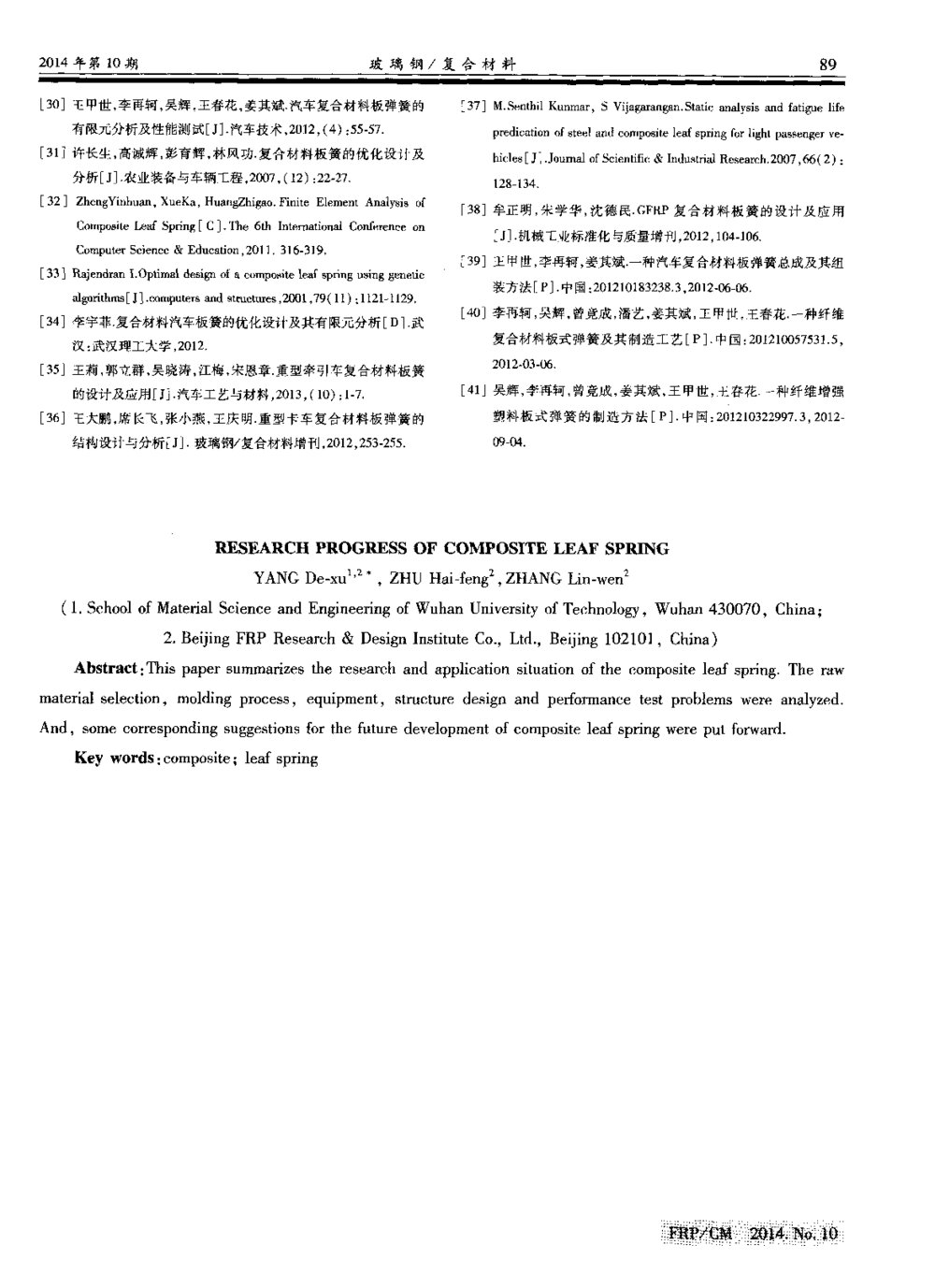
已阅读完毕,您还可以下载文档进行保存
- 1、本文档共6页,内容下载后可编辑。
- 2、本文档内容版权归属内容提供方,所产生的收益全部归内容提供方所有。如果您对本文有版权争议,可选择认领。
- 3、本文档由用户上传,本站不保证质量和数量令人满意,可能有诸多瑕疵,付费之前,请仔细先通过免费阅读内容等途径辨别内容交易风险。如存在严重挂羊头卖狗肉之情形,可联系本站下载客服投诉处理。
复合材料板簧研究进展2014年10月复合材料板簧研究进展杨德旭l,,祝海峰,张林文(1.武汉理工大学材料科学与工程学院,武汉430070;2.北京玻璃钢研究设计院有限公司,北京102101)摘要:本文总结了复合材料板簧的研究及应用情况,分析了原材料选择、成型工艺、成型设备、结构设计及性能测试等方面的问题,并对今后复合材料板簧的开发提出了相应的建议。关键词:复合材料;板簧中图分类号:TB332文献标识码:A———文章编号:10030999(2014)10008406板簧作为汽车悬架的重要组成部件,承受和传递车架与车桥之间的垂直力和垂直力以外的各种力及其所形成的力矩,并保证车轮相对于车架(或车身)按一定的关系运动,缓和及抑制不平路面所造成的冲击,保证汽车行驶的平顺性和操纵稳定性,工作条件恶劣。目前,汽车钢板弹簧主要由优质合金钢制成,占车体自重的5%~7%,而且存在生产工序多、设备占地面积大、能耗高等缺点。尤其是近年来石油价格飙涨、环境保护及安全舒适标准的提高,钢板弹簧已渐渐难以满足未来汽车行业的要求。为解决这一问题,国内外研究人员围绕着板簧的材料与结构进行了大量的研究工作,并研制出了“”以塑代钢的复合材料板簧。与传统钢制板簧相比,复合材料板簧具有质量轻、弹性应变大、比“”应变能高、疲劳寿命长及安全断裂性好等特点。然而,由于材料与加工技术限制,复合材料板簧的研究进展缓慢,相关的理论及技术也相当贫乏。近年来,由于汽车向轻量化方向发展的呼声愈来愈高,复合材料板簧受到了汽车行业的广泛关注。1原材料和成型工艺考虑到汽车用弹簧承载高、冲击大、疲劳循环次数高的工作特点,目前强度高、耐冲击、耐腐蚀的热固性树脂基纤维增强材料成为研究的首选。1.1原材料选择在纤维增强塑料中,纤维是主要承力组分。它不仅能使材料显示出较高的拉伸强度和刚度,而且能减少收缩,提高热变形温度及低温冲击强度等。复合材料的性能在很大程度上取决于纤维的性能、含量及使用状态。目前复合材料板簧中的增强材料主要为E玻纤、s玻纤及碳纤维三种¨引。考虑到材料使用温度范围、力学性能以及工艺适用性等因素,碳纤维的高模量导致过硬而不适合使用,研究人员在制作复合材料板簧时,多选用玻璃纤维作为增强材料。张小燕等H、吴辉等在研制复合材料板簧时,综合比较了E玻纤、s玻纤和碳纤维的性能,结合其成本和成型工艺性,选择了E玻纤作为增强材料。DeshmukhBB等采用玻璃纤维和环氧树脂来制作复合材料板簧,以降低其总成本。对于基体材料,根据汽车板簧的工作情况及受力要求,树脂基体应具有能长期在静载和动载下的承载能力(耐蠕变和抗疲劳性能)、吸收冲击性能(韧性)及一定的耐热性,且需价格合理。目前,制造复合材料板簧的热固性树脂基体主要由聚酯、乙烯基树脂和环氧树脂三类,其中环氧树脂因其具有良好的机械性能与层间剪切强度、较低的固化收缩率,且市场供应充足,研究人员多选择其作为复合材料板簧的基体材料。1.2成型工艺当前复合材料板簧的成型工艺方法有缠绕、模压、拉挤、RTM等工艺,这些板簧成型工艺方法各有特点。缠绕成型的特点是强度高、疲劳性能好、生产效率较高、工艺过程便于控制,但存在层间结合力不强、易劈裂等问题;拉挤法的特点是可以连续拉制各种形状的复合材料板簧;模压成型适合等宽形状板—收稿日期:2014-0421作者简介:杨德旭(1976.),男,硕士,高级工程师,主要从事复合材料成型工艺及性能测试研究,ydx251@126.eom。FRP/CM20l4.N0.102014年第10期玻璃钢/复合材料85簧的制备,产品密实、表面光滑;RTM工艺既可生产等截面也可生产变截面板簧。徐献忠等发明了一种复合材料板簧的制造方法,该成型方法是由多层纤维材料层以迭加铺设形式放人到合成树脂基体中,后置于模具内进行压制成各种需要的板簧形状。株洲时代新材公司制备复合材料板簧的工艺流程是将玻纤通过树脂浸渍槽,经过挤压、烘干、压实,制成带状预浸料,后将预浸料裁剪、叠层,送人模具中压制固化成型。模压工艺流程见图1。图1板簧模压成型工艺流程图Fig.1Springmoldingprocessflowdiagram长春汽车材料研究所采用缠绕成型工艺制备了CA1020F轻型车用复合材料副簧,其工艺流程为湿法连续纤维缠绕成形后合模加压,送人固化炉按固化制度加热固化,完成后拆模并按照结构尺寸要求切割成标准板簧。席长飞等l2引、李雷采用纤维缠绕/手糊成型制备变宽变厚等截面的复合材料板簧,通过玻璃纤维纱与玻璃纤维布预浸料相结合的增强材料形成非单向缠绕,使得板簧在不同方向具有较好的强度,综合性能得到提高。其工艺流程路线见图2。图2板簧缠绕成型工艺路线图Fig.2Springwindingtechnologyroadmap结合上述研究情况可知,预浸料层压工艺适合制备等厚等宽的复合材料板簧,而当板簧为变宽变厚等截面结构时,宜采用纤维缠绕成型,由于板簧的两端与中间的宽度不同,为使纤维在各个不同截面均匀分布,缠绕成型时需要控制纱片的丝嘴作有规律的翻转,以使落纱平整。缠绕结束后辅之闭模加压工序以控制树脂含量并保持产品外表面光滑。这种方法自动化程度高,成型的复合材料板簧表面光滑,质地密实,性能稳定。1.3成型设备由于板簧缠绕过程中张力需实时变化,且张力值及精度要求较高,目前市面上普通缠绕成型装置无法满足复合材料板簧纤维缠绕的要求,需要设计针对板簧的生产制造设备。普通缠绕机组的张力系统,无法实现精密控制以及张力数据的实时显示,而纤维张力控制恰巧是关键所在,关系到板簧产品内部的受力情况及铺展状态,影响到复合材料板簧的产品质量。普通缠绕机组张力控制系统多采用滚轮绕轴转动,与行走纤维纱束之间的摩擦力来实现,张力调节力度有限,无法实时准确控制纤维的张力数值,精度较低,误差较大。王庆明、席长飞等刮通过对变径制品张力控制机构的研究,开发出复合材料板簧的制造装置,该装置可实现半径制品的玻璃纤维束张力实时监测控制。该数控缠绕机采用基于伺服电机驱动的多轴运动控制系统,能够实现变截面变厚度扁长异形结构部件纤维缠绕,缠绕过程中全程张力能够根据工艺预设值进行精确调配,能实现全程排线规律精确控制。传统缠绕机工艺过程示意图见图3。变截面径向数控缠绕机张力控制示意图见图4。图3传统缠绕机工艺过程示意图Fig.3SchematicdiagramofthetraditionalwindingmachineprocessI)/2014iNoilO复合材料板簧研究进展2014年10月张力控制系统图4变截面径向数控缠绕机张力控制不意图Fig.4Schematicdiagramofvariablesectionradialnumericalcontrolmachinetensionwinding梁继才等发明了一种适合于RTM成型复合材料板簧的装置,该装置由下模、行走机构、加热辊构成,在行走机构内部,树脂罐通过树脂喷嘴将树脂注入到模具型腔中,加热辊将树脂加热固化成型。吴明珠等副发明了一种模压成型复合材料板簧的生产装置。该装置由上/下机台、上/下模具、垂直和水平导向机构、送料机构等组成。通过送料机构的送料管路将复合材料预浸液送至模腔内,提高了生产效率。2结构设计及性能测试2.1结构设计结构设计对于归属承载件的复合材料板簧来说,非常重要。通常复合材料板簧的横截面可采用恒定厚度恒定宽度、恒定厚度变宽度以及变厚度变宽度3种形式。边文风等建立了轻型车复合材料板簧的力学模型,根据层合板理论,计算出了副簧的危险应力和最大挠度,并以强度和刚度为约束,以质量最小为目标函数,通过有约束最小化优化方法,对复合材料副簧进行了优化设计,得到了最小质量下副簧的最佳尺寸,设计的板簧重量减少了74%,达到了轻量化的要求。王甲世等利用ABAQUS有限元软件,对设计的某型号汽车复合材料板簧进行了有限元分析,计算了复合材料板簧的刚度系数和最大承载力,并对采用模压工艺制备的复合材料板簧样件进行了性能测试。复合材料板簧比钢板簧减重约63%。许长生等用有限元软件ANSYS设计优化了一种玻璃纤维增强树脂基复合材料板簧,并对其动态特性及结构应力分布进行了有限元分析,结果证明,该复合材料板簧应力更低,固有频率更高,不计吊耳时弹FRP/CM刃j4.No;10簧重量减轻了约75%。ZhengYinhuan等利用有限元分析软件分析了玻纤增强复合材料板簧的力学性能,通过和钢板簧的对比分析,显示出复合材料板簧具有很好的疲劳性能,能够满足减重、舒适性的需要。RajendranIl3使用遗传算法对复合板簧的设计进行了优化。李宇菲以板簧的强度和刚度为约束条件,建立了复合材料汽车板簧的优化数学模型,以某型车为例,利用MATLAB优化工具,求得板簧最小质量下的最佳尺寸,优化后的板簧质量比优化前减少了50%。王莉等3采用正向设计方法设计等宽等厚复合材料板簧,建立数学模型并辅助CAE分析,复合材料板簧比变截面少片同静刚度钢板弹簧质量减轻74%。王大鹏等刮以某重型卡车复合材料板簧为例,使用Solidworks三维建模软件建立板簧的模型,利用ANSYS有限元分析软件对指定荷载的工况进行了分析,得到了变形的挠度和应力分布,对复合材料板簧样品进行相同工况下的静力实验。将实验结果与计算结果对比,两者的吻合度较高,样件进行静载和疲劳性能测试,完全符合设计要求。图5是某型号板簧的Ansys力学分析结果。图5纤维方向的应力分布图Fig.5Stressdistributionoffiberorientatio由图5得知,最大应力在板簧的中部,最大拉应力为727.876MPa,而最大压应力为647.268MPa,板簧主体材料参数z方向拉伸强度为1400MPa,压缩强度为960MPa,最大拉应力和压应力分别小于材料相应的强度值,最大拉应力为强度值的52%,最大压应力为强度值的67.4%。由此说明,经过适当的结构设计,可以使外弧面的压应力和内弧面的拉应力相对强度值的百分比保持在比较接近的程度上。以2014年第10期玻璃钢/复合材料87最大压应力与压缩强度的比值确定安全系数为1.48,可知即便在极限荷载的情况下,此结构的复合材料板簧仍能保持一定程度的安全性。2.2性能测试由于国内没有相应的复合材料板簧的静载及疲劳测试标准,板簧的性能测试多是参考钢板弹簧的测试标准进行试验。国内文献研究表明,板簧静载试验得到的刚度值与有限元计算结果相差在10%以内,对样件进行疲劳性能测试,经30万次试验后板簧未断裂,并且刚度无损失,复合材料板簧设计符合使用要求。M.SenthilKunmar等利用有限元分析获得,复合材料板簧的重量减轻了68.15%,疲劳寿命可达到100万次,远大于钢板簧的20万次。图6所示为某型号复合材料板簧静载刚度曲线,图7为复合材料板簧疲劳测试试验照片。图6复合材料板簧静载刚度曲线Fig.6Compositeleafspringstaticstiffnesseul ̄e图7复合材料板簧疲劳测试照片Fig.7Compositeleafspnngfatiguetestphoto3应用情况复合材料板簧和钢板簧相比存在多方面优势,表1列出了两者的比较情况。表1复合材料板簧与钢板簧相比优势Table1Compositeleafspringandthesteelplatespringcomparedadvantage钢板簧一般为多片簧,重量大断裂后车辆不能继续行驶国标要求钢板簧疲劳寿命8万次,一般不超过10万次与复合材料板簧相比整车重量增加,油耗高无法完成单人装卸弹性行程可设计性低多片簧之间摩擦会产生噪音和热复合材料板簧一般为变厚度截面单片板簧,重量比钢板簧减轻50%~70%“”安全断裂提高了可靠性,沿长度方向分层开裂,仍能保证产品的基本形状,可使空载汽车继续行驶疲劳寿命高,能达到钢制多叶板簧约2~1O倍,一般疲劳寿命为30万次以上重量轻,节约燃料和维修方便,使车辆使用费用降低部件简化,重量轻,拆装操作更简便容易相同荷载能力下,复合材料板簧的弹性行程可以设计得更大(可设计性),舒适性更好材料自身阻尼较大,各种工况下产生的噪音较小国外研究应用复合材料板簧相对较早。2O世纪80年代初期,美国通用工程部率先研制复合材料板簧,由于复合材料板簧有钢板弹簧难以取代的优点,美、英、德等国竞相开展研制,取得了不少研制成果。英国GKN已进行批量生产,年产量为50万根。德国IFC复合材料板簧日产量超过1000根,现为奔Ⅲ驰Sprinter和大众Crafter进行供应3引。德国的本特勒.西格里公司生产的复合材料板簧重量较钢板簧可减轻65%。国内来讲,早在1985年,同济大学与上海汽车钢板弹簧厂开始合作研发GFRP板簧。目前,南京依维柯汽车部分车型已经使用复合材料板簧。北京中材汽车和株洲时代新材等单位研究较为深入,前者开发的复合材料板簧已经在国外依维柯车型上获得批量应用,并与中国一汽、东风二汽等单位建立了密切合作关系,共同开发生产新型复合材料板簧。后者与厦门金龙合作开发的商务车复合材料板簧也取得了重要进展。此外,哈尔滨工业大学、武汉理工大学、上汽商用车等单位都在研究复合材料板簧项目。国内目前虽没有形成大规模商业化生产,但已初具规模,相信复合材料板簧的大量使用只是时间问题。FRCM2o14.1No._1o88复合材料板簧研究进展2014年10月4结语就我国汽车钢板弹簧行业而言,每年消耗的弹簧钢材料在120万吨以上,如果将部分钢板簧替换为复合材料板簧,则可以节约社会资源,降低能源消“”耗、减少排放。国家十二五发展规划纲要提出,“新材料产业重点发展新型功能材料、先进结构材”料、高性能纤维及其复合材料,研究开发复合材料板簧,符合汽车轻量化的发展方向,对于优化我国汽车零部件产业的结构,促进汽车零部件行业的技术升级,推动我国汽车零部件产业整体的快速健康发展,具有重要意义。由于我国超载现象相对普遍,超过设计载荷使用复合材料板簧可能会造成其提前损坏,因此提出①“建议:预先设计承载能力更大的板簧,所谓高能”②低标,使其具有一定的超载能力;推荐在定载车上使用复合材料板簧,如:罐车,汽、液运输车,工程机械车,军用车辆以及其它不超载车辆等。参考文献[1]Csubramanian,Ssenthilvelan.Fatigueperformanceofdiscontinuous—fibrereinforcedthermoplasticleafspring[J].Proc.IMechEpartL:J.—Materials:designandapplications,224:93100.—[2]Csubramanian,Ssenthilvelan.Jointperformanceoftheglassfiberreinforeedpolypropyleneleafspring[J].compositestructures,2011,93:759-766.[3]IRajendranandSVijayarangan.Design,AnMysis,Fabricationand—TestingofaCompositeLeafSpring[J].IE(I)JourualMC,2002,82(3):180-187.—[4]D.sameerkumar,s.radhika,K.Ravindra,K.N.S.Suman.ImpmvedDesignOptimizationofaCompositeLeafSpringusingSwarm—Intelligence[J].InternationalJournalofAppliedEngineeringResearch,2011,(6):193.200.—[5]HouJP,CherruauhJY,NairneI,eta1.Evolution0ftheeyeenddesignofacompositeleafspringforheavyaxleloads[J].Composite—structures,2007,78(3):351358.[6]ChiuC,HwanC,TsaiH,eta1.Anexperimentalinvestigationintothemechanicalbehaviorsofhelicalcompositesprings[J].Compositestructures,2007,77(3):331.340.[7]SubramanianC,SenthilvelanS.Jointperformanceoftheglassfiberreinforcedpolypropyleneleafspring[J].Compositestructures,2011,93(2):759-766.[8]FuentesJJ,AguilarHJ,RodriguezJA,eta1.Prematurefractureinautomobileleafsprings[J].EngineeringFailureanalysis,2009,16—(2):648655.FRP/CM2014。No.10[9]SubramanianC,SenthilvelanS.Effectofreinforcedfiberlengthonthejointperformanceofthermoplasticleafspring[J].Materialsand—Design.2010,31(8):37333741.[1O]李磊,任勇生,孙爱芹,胡爱英,尹文明,王晓辉.SMA纤维复合材料板簧刚度性能分析[J].机械设计与研究,2008,24(3):57.61.[11]C・奥利克,R・福斯特,H・肯佩.分段式纤维复合板簧及其生产——方法[P].中国:200680042271.7,2006114.[12]董国华,袁国青.复合材料汽车板簧吊耳及其联接的研究[J].玻璃钢/复合材料,2001,(2):34-36.[13]赵洪斌,陈宏章,刘忠珊.纤维复合材料单片板簧的研制[J].—2000,(3):2931.[14]陶建新.复合材料板簧的设计研究[D].上海:同济大学,1987.[15]袁皎秋.复合材料板簧的选材和固化工艺研究[D].上海:同济大学,1989.[16]李未.复合材料板簧的优化设计和有限元分析[D].哈尔滨:哈尔滨工业大学,2006.[17]杨俊杰.树脂基复合材料板簧结构阻尼性能研究[D].哈尔滨:哈尔滨工程大学,2010.[18]江梅,李尹熙.纤维复合材料板簧的研究[J].汽车工艺与材料,—1992,(9):2529.[19]张小燕,席长飞,王大鹏,王庆明.汽车材料板簧的制备方法及性能测试[J].玻璃钢/复合材料增刊,2012,250-252.[2O]吴辉,李再轲,姜其斌.复合材料板式弹簧的研制及性能[J].塑—料工业,2012,40(8):103106.—[21]DeshmukhBB,JajuSB.DesignandAn ̄ysisofGlassFiberRein—forcedPolymer(GFRP)LeafSpring[J].ComputerMethodsinAppliedMethodsinAppliedMechanicsandEngineering,2010,195(50):69.75.[22]徐献忠,侯松发.玻璃钢复合材料板弹簧的制造方法[P].中国:——20O61o017556.7.2006324.[23]席长飞,王庆明,高国强,王大鹏,张小燕.一种玻璃纤维增强树—脂复合材料板簧的制备方法[P].中国:201210156535.9,2012—518.[24]李雷.汽车复合材料板簧研究[D].武汉:武汉理工大学,2013.[25]王庆明,席长飞,高国强,王大鹏,张小燕.一种玻璃纤维增强树脂复合材料板簧的制造装置[P].中国:201210156355.0,2012.—518.[26]席长飞,王大鹏,张小燕,王庆明.复合材料板簧制造装备研究[J].玻璃钢/复合材料增刊,2012,259-260.[27]梁继才,李义.汽车复合材料板簧制造装置与方法[P].中国:——200510119048.5,2005126.[28]吴明珠,李建林,邹波,李再轲,沈明,吴辉.板弹簧生产设备[P].中国:201220421726.9,2012.O8.23.[29]边文凤,李未.复合材料板簧副簧的优化设计[J].机械设计与制造,2006,(9):29-31.2014年第10期玻璃钢/复合材料89[3O]王甲世,李再轲,吴辉,王春花,姜其斌.汽车复合材料板弹簧的—有限元分析及性能测试[J].汽车技术,2012,(4):5557.[31]许长生,高诚辉,彭育辉,林风功.复合材料板簧的优化设计及分析[J].农业装备与车辆工程,2007,(12):22,27.[32]ZhengYinhuan,XueKa,HuangZhigao.FiniteElementAnalysisofCompositeLeafSpring[C].The6thInternationalConferenceon—ComputerScience&Education.2011.316319.[33]RajendranI.Optimaldesignofacompositeleafspringusinggenetic—algorithms[J].computersandstructures,2001,79(11):11211129.[34]李宇菲.复合材料汽车板簧的优化设计及其有限元分析[D].武汉:武汉理工大学,2012.[35]王莉,郭立群,吴晓涛,江梅,宋恩章.重型牵引车复合材料板簧的设计及应用[J].汽车工艺与材料,2013,(1O):1-7.[36]王大鹏,席长飞,张小燕,王庆明.重型卡车复合材料板弹簧的—结构设计与分析[J].玻璃钢/复合材料增刊,2012,253255.[37]M.SenthilKunmar,SVijagarangan.Staticanalysisandfatiguelife—predicationofsteelandcompositeleafspringforlightpassengervehieles[J].JournalofScientific&IndustrialResearch.2007,66(2):—128134.[38]牟正明,朱学华,沈德民.GFRP复合材料板簧的设计及应用[J].机械工业标准化与质量增刊,2012,104.106.[39]王甲世,李再轲,姜其斌.一种汽车复合材料板弹簧总成及其组—装方法[P].中国:201210183238.3,2012。0606.[4O]李再轲,吴辉,曾竞成,潘艺,姜其斌,王甲世,王春花.一种纤维复合材料板式弹簧及其制造工艺[P].中国:201210057531.5,—2012.0306.[41]吴辉,李再轲,曾竟成,姜其斌,王甲世,王春花.一种纤维增强塑料板式弹簧的制造方法[P].中国:201210322997.3,2012.—CI904RESEARCHPROGRESSoFCOMP0SITELEAFSPRING——YANGDeXH',ZHUHaifeng,ZHANGLin.wen(1.SchoolofMaterialScienceandEngineeringofWuhanUniversityofTechnology,Wuhan430070,China;2.BeijingFRPResearch&DesignInstituteCo.,Ltd.,Beijing102101,China)Abstract:Thispapersummarizestheresearchandapplicationsituationofthecompositeleafspring.Therawmaterialselection,moldingprocess,equipment,structuredesignandperformancetestproblemswereanalyzed.And,somecorrespondingsuggestionsforthefuturedevelopmentofcompositeleafspringwereputforward.Keywords:composite;leafspringFfu)/1CM20ll4.No.10
您可能关注的文档
- “离位”增韧复合材料准静态压入损伤特性研究.pdf
- “神舟七号”飞船舱外航天服防护头盔组件的研制.pdf
- “十二五”复合材料发展重点和方向解读.pdf
- “珠串”堆叠超结构的介孔铁酸锌的制备与表征.pdf
- (001)应变对正交相Ca2 P0.25 Si0.75能带结构及光学性质的影响.pdf
- 0.8设计系数用X80管线钢在近中性pH溶液中的应力腐蚀开裂行为.pdf
- 0.20mm CGO硅钢高温退火Goss晶粒起源及异常长大行为研究.pdf
- 0Cr16Ni5Mo低碳马氏体不锈钢的热变形行为及其热加工图.pdf
- 0Cr17Ni4Cu4Nb钢制螺钉断裂原因分析.pdf
- 1.5MW风机叶片模具加热工艺研究与技术创新.pdf
- 1.5MW风机叶片VARI工艺模拟分析及验证.pdf
- 2.5维机织复合材料低速冲击性能研究.pdf
- 2.25Cr-1Mo钢后续热处理中的磷偏聚行为.pdf
- 2A50锻铝三点弯曲试验与高分辨率CT成像分析.pdf
- 2A12与2A11铝合金超声波焊接工艺与组织研究.pdf
- 2MW风机复合材料叶片材料及工艺研究.pdf
- 3Cr2W8V模具钢激光表面相变硬化层性能的研究.pdf
- 3D打印技术及先进应用研究进展.pdf
- 3D打印技术研究现状和关键技术.pdf
- 5%鱼藤酮悬浮剂的研制.pdf

- 富富资料
- 该用户很懒,什么也没介绍
相关文档
- “离位”增韧复合材料准静态压入损伤特性研究.pdf2021-11-235页
- “神舟七号”飞船舱外航天服防护头盔组件的研制.pdf2021-11-233页
- “十二五”复合材料发展重点和方向解读.pdf2021-11-232页
- “珠串”堆叠超结构的介孔铁酸锌的制备与表征.pdf2021-11-235页
- (001)应变对正交相Ca2 P0.25 Si0.75能带结构及光学性质的影响.pdf2021-11-236页
- 0.8设计系数用X80管线钢在近中性pH溶液中的应力腐蚀开裂行为.pdf2021-11-237页
- 0.20mm CGO硅钢高温退火Goss晶粒起源及异常长大行为研究.pdf2021-11-237页