- 文档大小:965.06 KB
- 文档格式:pdf
- 约 6页
- 2022-04-08 发布
- 举报
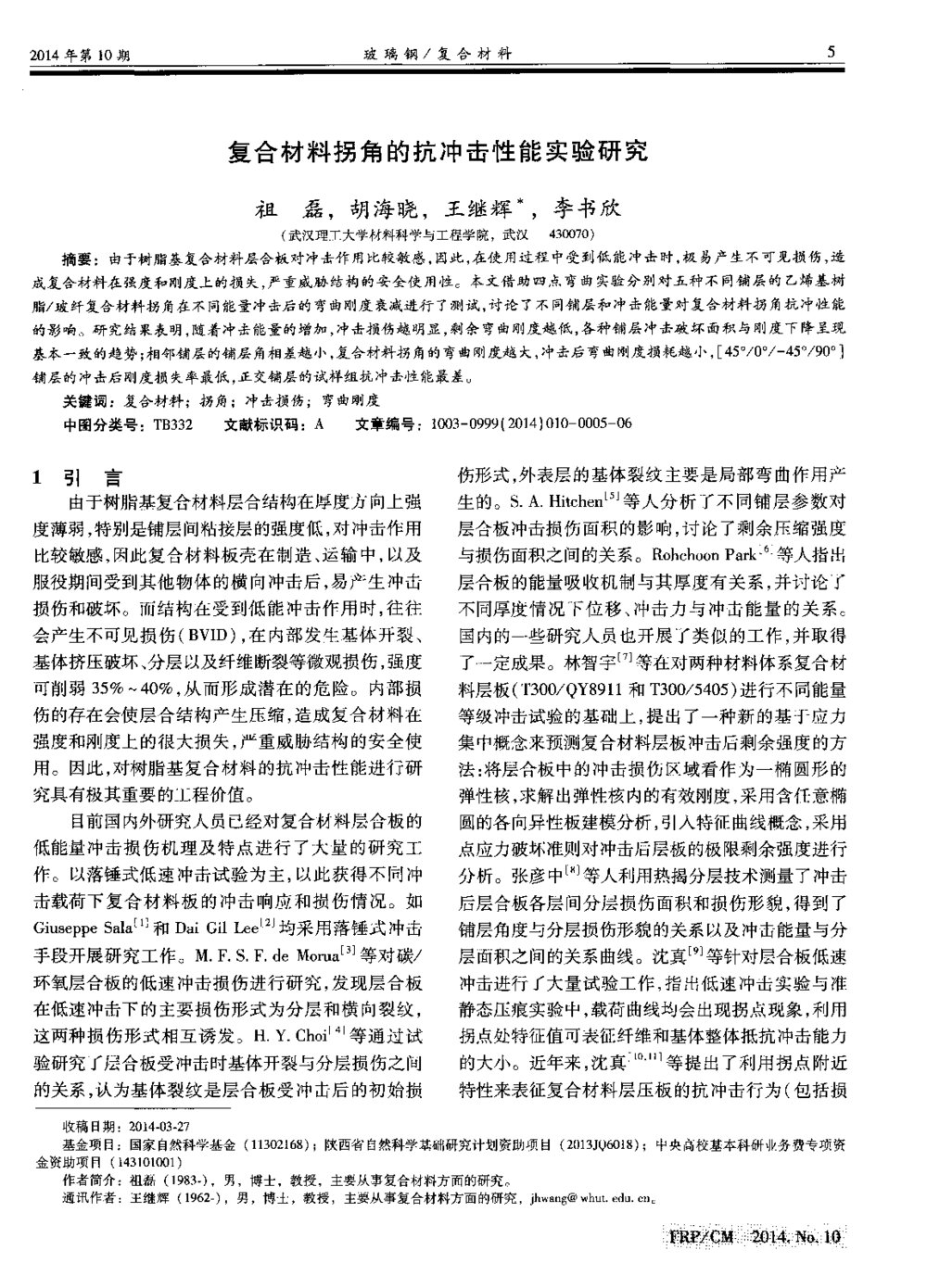
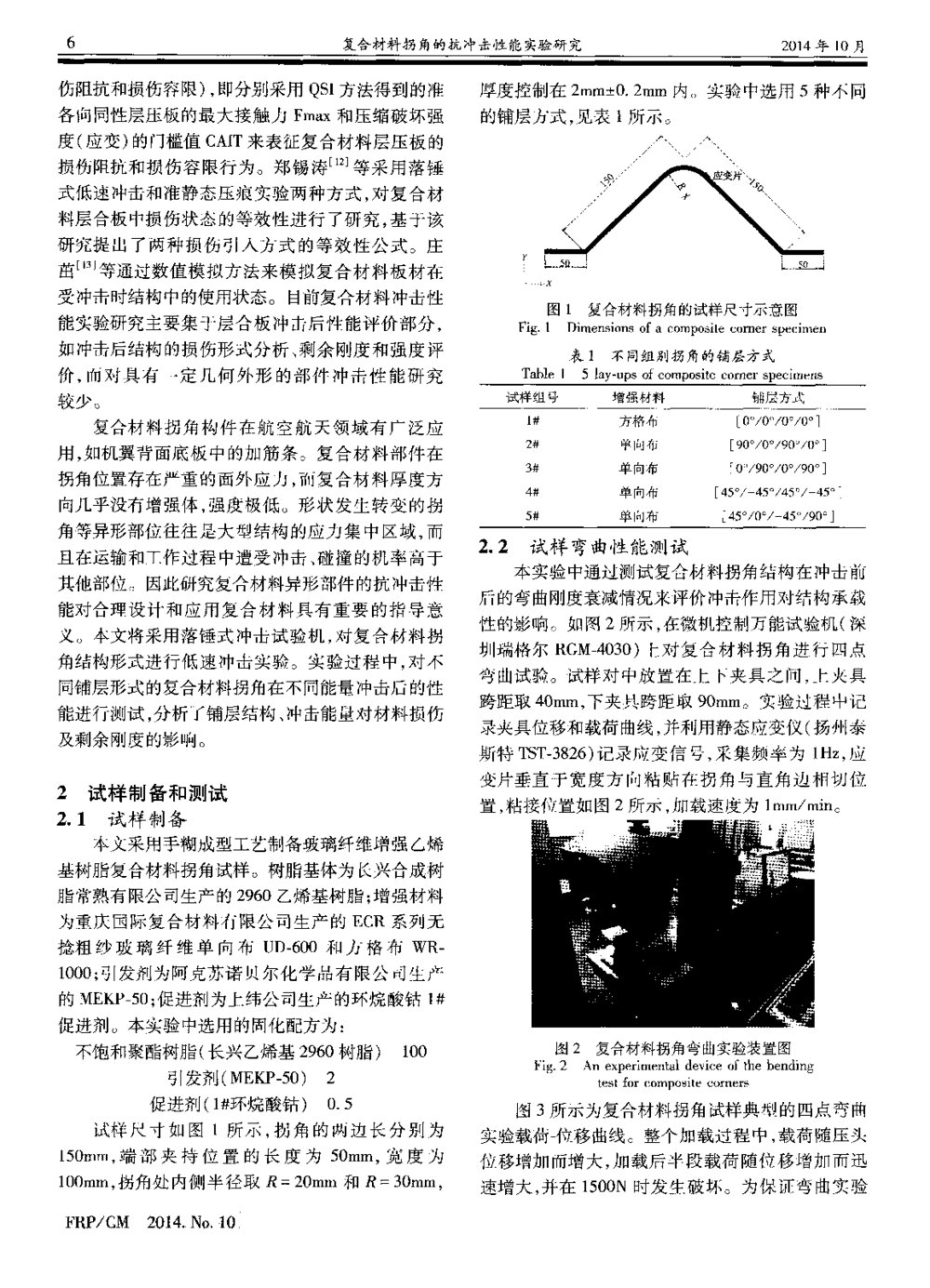
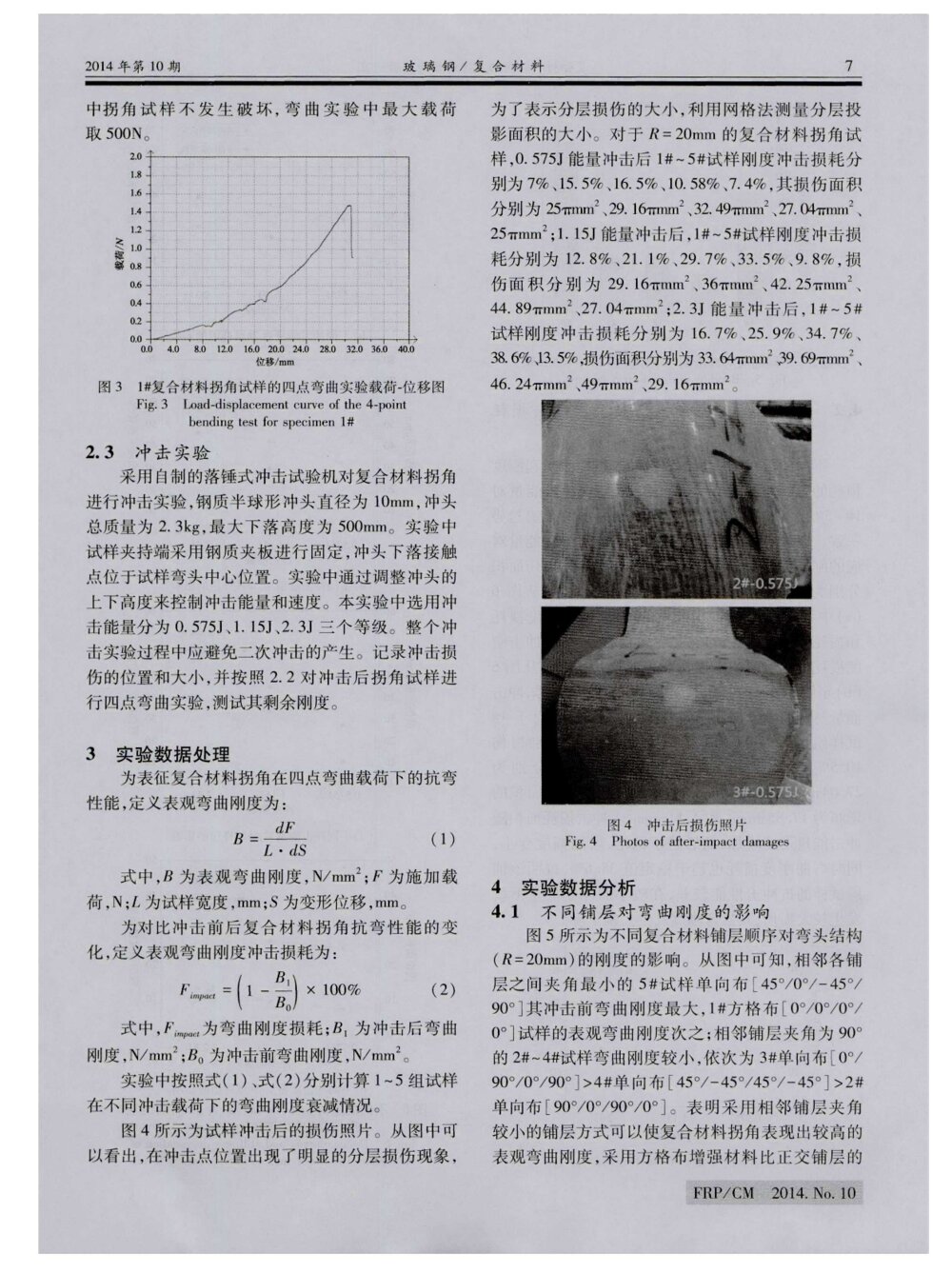
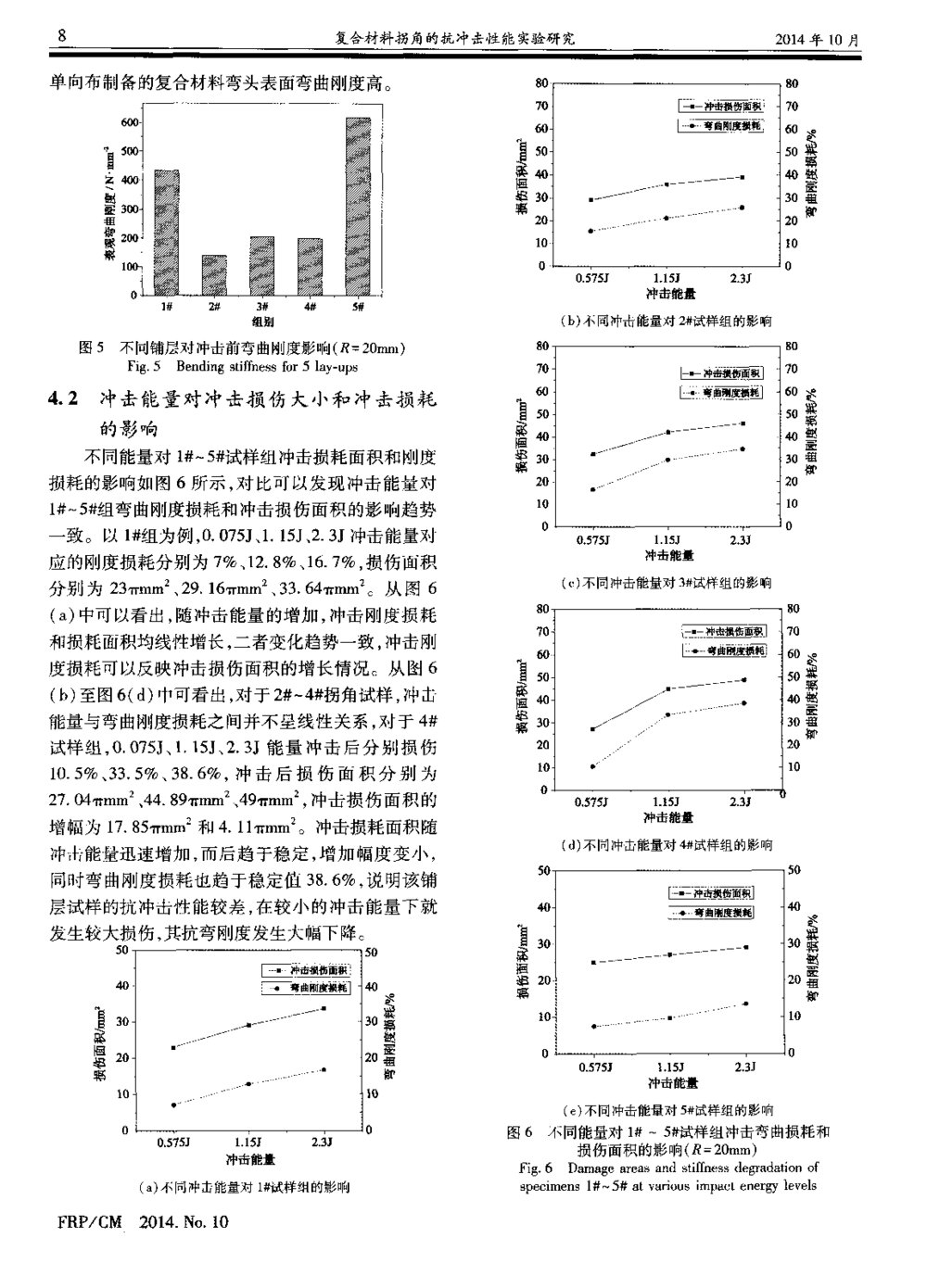
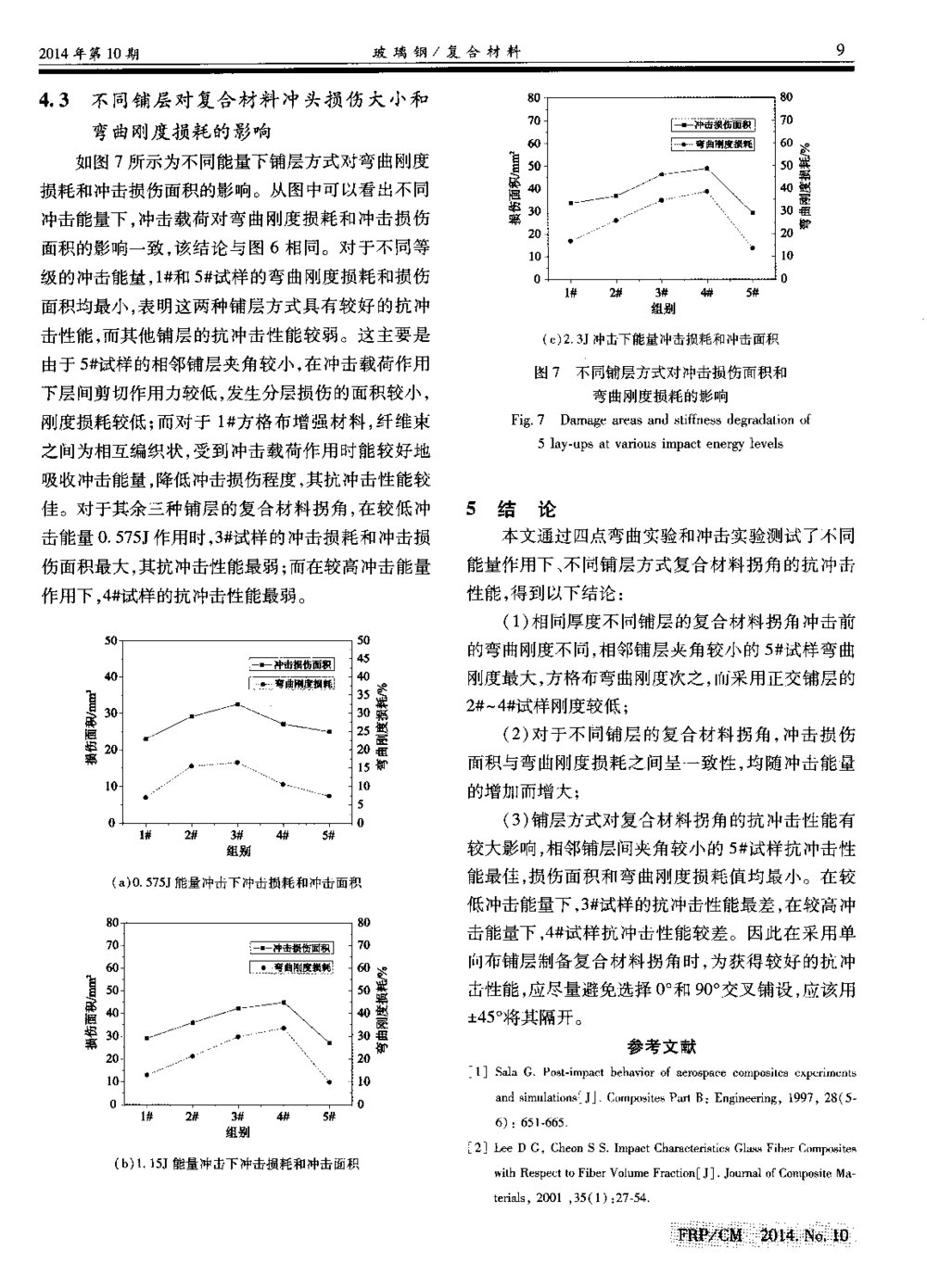
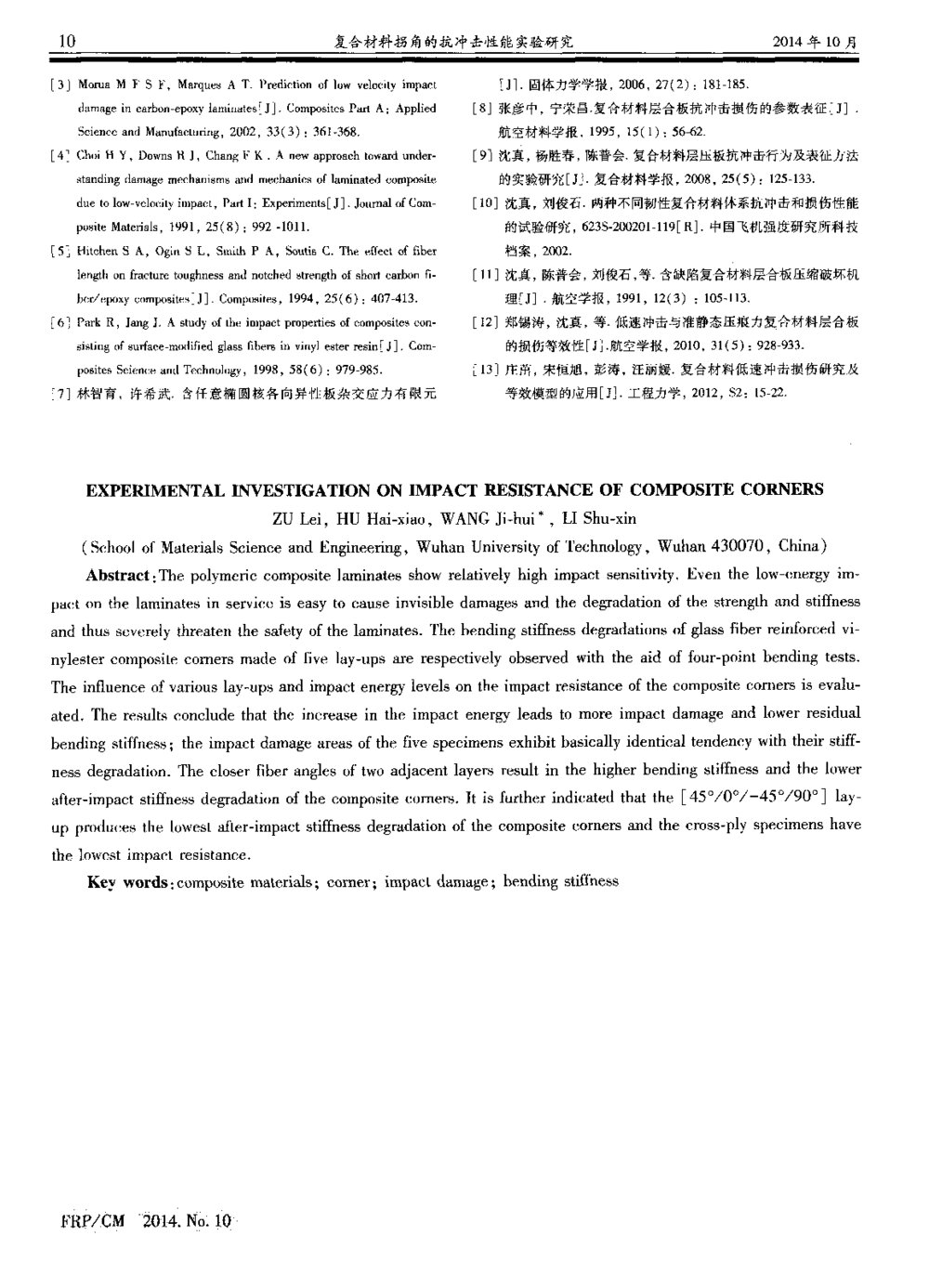
已阅读完毕,您还可以下载文档进行保存
- 1、本文档共6页,内容下载后可编辑。
- 2、本文档内容版权归属内容提供方,所产生的收益全部归内容提供方所有。如果您对本文有版权争议,可选择认领。
- 3、本文档由用户上传,本站不保证质量和数量令人满意,可能有诸多瑕疵,付费之前,请仔细先通过免费阅读内容等途径辨别内容交易风险。如存在严重挂羊头卖狗肉之情形,可联系本站下载客服投诉处理。
2014年第10期玻璃钢/复合材料5复合材料拐角的抗冲击性能实验研究祖磊,胡海晓,王继辉,李书欣(武汉理工大学材料科学与工程学院,武汉430070)摘要:由于树脂基复合材料层合板对冲击作用比较敏感,因此,在使用过程中受到低能冲击时,极易产生不可见损伤,造成复合材料在强度和刚度上的损失,严重威胁结构的安全使用性。本文借助四点弯曲实验分别对五种不同铺层的乙烯基树脂/玻纤复合材料拐角在不同能量冲击后的弯曲刚度衰减进行了测试,讨论了不同铺层和冲击能量对复合材料拐角抗冲性能的影响。研究结果表明,随着冲击能量的增加,冲击损伤越明显,剩余弯曲刚度越低,各种铺层冲击破坏面积与刚度下降呈现基本一致的趋势;相邻铺层的铺层角相差越小,复合材料拐角的弯曲刚度越大,冲击后弯曲刚度损耗越小,[45。/0。/一45。/90。]铺层的冲击后刚度损失率最低,正交铺层的试样组抗冲击性能最差。关键词:复合材料;拐角;冲击损伤;弯曲刚度———中图分类号:TB332文献标识码:A文章编号:10030999(2014)0100005061引言由于树脂基复合材料层合结构在厚度方向上强度薄弱,特别是铺层间粘接层的强度低,对冲击作用比较敏感,因此复合材料板壳在制造、运输中,以及服役期间受到其他物体的横向冲击后,易产生冲击损伤和破坏。而结构在受到低能冲击作用时,往往会产生不可见损伤(BVID),在内部发生基体开裂、基体挤压破坏、分层以及纤维断裂等微观损伤,强度可削弱35%一40%,从而形成潜在的危险。内部损伤的存在会使层合结构产生压缩,造成复合材料在强度和刚度上的很大损失,严重威胁结构的安全使用。因此,对树脂基复合材料的抗冲击性能进行研究具有极其重要的工程价值。目前国内外研究人员已经对复合材料层合板的低能量冲击损伤机理及特点进行了大量的研究工作。以落锤式低速冲击试验为主,以此获得不同冲击载荷下复合材料板的冲击响应和损伤情况。如…GiuseppeSala和DaiGilLee均采用落锤式冲击手段开展研究工作。M.F.S.F.deMorua等对碳/环氧层合板的低速冲击损伤进行研究,发现层合板在低速冲击下的主要损伤形式为分层和横向裂纹,这两种损伤形式相互诱发。H.Y.Choil4等通过试验研究了层合板受冲击时基体开裂与分层损伤之间的关系,认为基体裂纹是层合板受冲击后的初始损伤形式,外表层的基体裂纹主要是局部弯曲作用产生的。S.A.Hitchen等人分析了不同铺层参数对层合板冲击损伤面积的影响,讨论了剩余压缩强度与损伤面积之间的关系。RohchoonPark等人指出层合板的能量吸收机制与其厚度有关系,并讨论了不同厚度情况下位移、冲击力与冲击能量的关系。国内的一些研究人员也开展了类似的工作,并取得了一定成果。林智宇等在对两种材料体系复合材料层板(T300/QY8911和T300/5405)进行不同能量等级冲击试验的基础上,提出了一种新的基于应力集中概念来预测复合材料层板冲击后剩余强度的方法:将层合板中的冲击损伤区域看作为一椭圆形的弹性核,求解出弹性核内的有效刚度,采用含任意椭圆的各向异性板建模分析,引入特征曲线概念,采用点应力破坏准则对冲击后层板的极限剩余强度进行分析。张彦中等人利用热揭分层技术测量了冲击后层合板各层间分层损伤面积和损伤形貌,得到了铺层角度与分层损伤形貌的关系以及冲击能量与分层面积之间的关系曲线。沈真_9等针对层合板低速冲击进行了大量试验工作,指出低速冲击实验与准静态压痕实验中,载荷曲线均会出现拐点现象,利用拐点处特征值可表征纤维和基体整体抵抗冲击能力“的大小。近年来,沈真等提出了利用拐点附近特性来表征复合材料层压板的抗冲击行为(包括损—收稿日期:2014.0327基金项目:国家自然科学基金(11302168);陕西省自然科学基础研究计划资助项目(2O13JQ6Ol8);中央高校基本科研业务费专项资金资助项目(143101001)作者简介:祖磊(1983一),男,博士,教授,主要从事复合材料方面的研究。通讯作者:王继辉(1962-),男,博士,教授,主要从事复合材料方面的研究,jhwang@whut.edu.ca。/C2014:No:t06复合材料拐角的抗冲击性能实验研究伤阻抗和损伤容限),即分别采用QSI方法得到的准各向同性层压板的最大接触力Fmax和压缩破坏强度(应变)的门槛值CAtT来表征复合材料层压板的损伤阻抗和损伤容限行为。郑锡涛¨等采用落锤式低速冲击和准静态压痕实验两种方式,对复合材料层合板中损伤状态的等效性进行了研究,基于该研究提出了两种损伤引入方式的等效性公式。庄茁¨等通过数值模拟方法来模拟复合材料板材在受冲击时结构中的使用状态。目前复合材料冲击性能实验研究主要集于层合板冲击后性能评价部分,如冲击后结构的损伤形式分析、剩余刚度和强度评价,而对具有一定几何外形的部件冲击性能研究较少。复合材料拐角构件在航空航天领域有广泛应用,如机翼背面底板中的加筋条。复合材料部件在拐角位置存在严重的面外应力,而复合材料厚度方向几乎没有增强体,强度极低。形状发生转变的拐角等异形部位往往是大型结构的应力集中区域,而且在运输和工作过程中遭受冲击、碰撞的机率高于其他部位。因此研究复合材料异形部件的抗冲击性能对合理设计和应用复合材料具有重要的指导意义。本文将采用落锤式冲击试验机,对复合材料拐角结构形式进行低速冲击实验。实验过程中,对不同铺层形式的复合材料拐角在不同能量冲击后的性能进行测试,分析了铺层结构、冲击能量对材料损伤及剩余刚度的影响。2试样制备和测试2.1试样制备本文采用手糊成型工艺制备玻璃纤维增强乙烯基树脂复合材料拐角试样。树脂基体为长兴合成树脂常熟有限公司生产的2960乙烯基树脂;增强材料为重庆国际复合材料有限公司生产的ECR系列无捻粗纱玻璃纤维单向布UD.600和方格布WR.1000;引发剂为阿克苏诺贝尔化学品有限公司生产的MEKP一50;促进剂为上纬公司生产的环烷酸钴l#促进剂。本实验中选用的固化配方为:不饱和聚酯树脂(长兴乙烯基2960树脂)100引发剂(MEKP一50)2促进剂(1#环烷酸钴)0.5试样尺寸如图1所示,拐角的两边长分别为150ram,端部夹持位置的长度为50mm,宽度为100mm,拐角处内侧半径取R=20mm和R=30mm,FRP/CM2014.No.10厚度控制在2mm_+0.2mm内。实验中选用5种不同的铺层方式,见表1所示。图1复合材料拐角的试样尺寸示意图Fig.1Dimensionsofacompositecomerspecimen表1不同组别拐角的铺层方式—Table15layupsofcompositecornerspecimens2.2试样弯曲性能测试本实验中通过测试复合材料拐角结构在冲击前后的弯曲刚度衰减情况来评价冲击作用对结构承载性的影响。如图2所示,在微机控制万能试验机(深圳瑞格尔RGM.4030)上对复合材料拐角进行四点弯曲试验。试样对中放置在上下夹具之间,上夹具跨距取40mm,下夹具跨距取90mm。实验过程中记录夹具位移和载荷曲线,并利用静态应变仪(扬州泰斯特TST一3826)记录应变信号,采集频率为1Hz,应变片垂直于宽度方向粘贴在拐角与直角边相切位置,粘接位置如图2所示,加载速度为lmm/min。图2复合材料拐角弯曲实验装置图Fig.2AnexperimentaldeviceofthebendingtestforcompositeeolTlers图3所示为复合材料拐角试样典型的四点弯曲实验载荷一位移曲线。整个加载过程中,载荷随压头位移增加而增大,加载后半段载荷随位移增加而迅速增大,并在1500N时发生破坏。为保证弯曲实验2014年第10期玻璃钢/复合材料7中拐角试样不发生破坏,弯曲实验中最大载荷取500N图31#复合材料拐角试样的四点弯曲实验载荷一位移图—Fig.3Loaddisplacementcurveofthe4-pointbendingtestforspecimen1#2.3冲击实验采用自制的落锤式冲击试验机对复合材料拐角进行冲击实验,钢质半球形冲头直径为10mm,冲头总质量为2.3kg,最大下落高度为500mm。实验中试样夹持端采用钢质夹板进行固定,冲头下落接触点位于试样弯头中心位置。实验中通过调整冲头的上下高度来控制冲击能量和速度。本实验中选用冲击能量分为0.575J、1.15J、2.3J三个等级。整个冲击实验过程中应避免二次冲击的产生。记录冲击损伤的位置和大小,并按照2.2对冲击后拐角试样进行四点弯曲实验,测试其剩余刚度。3实验数据处理为表征复合材料拐角在四点弯曲载荷下的抗弯性能,定义表观弯曲刚度为:B=㈩L・以5式中,B为表观弯曲刚度,N/mm;F为施加载荷,N;L为试样宽度,mm;S为变形位移,mm。为对比冲击前后复合材料拐角抗弯性能的变化,定义表观弯曲刚度冲击损耗为:,Bl\…l1一--II×100%(2)…式中,F为弯曲刚度损耗;B为冲击后弯曲刚度,N/ram;B为冲击前弯曲刚度,N/ram。实验中按照式(1)、式(2)分别计算1~5组试样在不同冲击载荷下的弯曲刚度衰减情况。图4所示为试样冲击后的损伤照片。从图中可以看出,在冲击点位置出现了明显的分层损伤现象,为了表示分层损伤的大小,利用网格法测量分层投影面积的大小。对于R=20ram的复合材料拐角试样,0.575J能量冲击后l#~5#试样刚度冲击损耗分别为7%、15.5%、16.5%、10.58%、7.4%,其损伤面积分别为25q'rmm!、29.16,rrmm、32.49rrmm、27.04-rrmm!、25'rrmm;1.15J能量冲击后,l#~5#试样刚度冲击损耗分别为l2.8%、21.1%、29.7%、33.5%、9.8%,损伤面积分别为29.16"rrmm、36-rrmm、42.25'rrmrn、44.89Trmm、27.04"rrmm;2.3J能量冲击后,1#~5#试样刚度冲击损耗分别为16.7%、25.9%、34.7%、38.、13.5%,损伤面积分别为33.64'n'nun39.69wnun、46.24'rrmm、49霄mm、29.16'rrmm!图4冲击后损伤J!f{片Fig.4Photosof'’aftel一impactdamages4实验数据分析4.1不同铺层对弯曲刚度的影响图5所示为不同复合材料铺层顺序埘弯头结构(R=20mm)的刚度的影响。从中可知,相邻各铺层之间夹角最小的5样试样单向[45。/0。/一45。/90。]其冲击前弯曲刚度最大,1#方格布[0。/0。/0。/0。]试样的表观弯曲刚度次之;相邻铺层火角为90。的2#~4#斌样弯曲刚度较小,依次为3#向布[0。/90。/0。/90。]>4#单向布[45。/一45。/45。/一45。J>2#单向布[90。/0。/90。/0。]。表明采用相邻铺层夹角较小的铺层方式可以使复合材料拐角表现出较高的表观弯曲刚度,采用方格布增强材料比交铺层的FRP/(:M2014.NO.108复合材料拐角的抗冲击性能实验研究2014年10月单向布制备的复合材料弯头表面弯曲刚度高。詈蓦纂图5不同铺层对冲击前弯曲刚度影响(R=20mm)—Fig.5Bendingstiffnessfor5layups4.2冲击能量对冲击损伤大小和冲击损耗的影响不同能量对1#-5#试样组冲击损耗面积和刚度损耗的影响如图6所示,对比可以发现冲击能量对1#-5#组弯曲刚度损耗和冲击损伤面积的影响趋势一致。以1样组为例,0.075J、1.15J、2.3J冲击能量对应的刚度损耗分别为7%、12.8%、16.7%,损伤面积分别为23'rrmm、29.16vrmm、33.64-trmm。从图6(a)中可以看出,随冲击能量的增加,冲击刚度损耗和损耗面积均线性增长,二者变化趋势一致,冲击刚度损耗可以反映冲击损伤面积的增长情况。从图6(b)至图6(d)中可看出,对于2#-4#拐角试样,冲击能量与弯曲刚度损耗之间并不呈线性关系,对于4#试样组,0.o75J、1.15.1、2.3.I能量冲击后分别损伤10.5%、33.5%、38.6%,冲击后损伤面积分别为27.04'rrmm、44.89-rrmm、49"rrmm,冲击损伤面积的增幅为17.85'rrmm和4.11'Tl'mm。冲击损耗面积随冲击能量迅速增加,而后趋于稳定,增加幅度变小,同时弯曲刚度损耗也趋于稳定值38.6%,说明该铺层试样的抗冲击性能较差,在较小的冲击能量下就发生较大损伤,其抗弯刚度发生大幅下降。妻譬(a)不同冲击能量对1#试样组的影响FRP/CM2014.No.10簧曩妻薰(b)不同冲击能量对2#试样组的影响(C)不同冲击能量对3样试样组的影响(d)不同冲击能量对4#试样组的影响(e)不同冲击能量对5#t式样组的影响图6不同能量对1#~5拌试样组冲击弯曲损耗和损伤面积的影响(R=20mm)Fig.6Damageareasandstiffnessdegradationofspecimensl#一5#atvarioHsimpactenel'gylevels2014年第10期玻璃钢/复合材料94.3不同铺层对复合材料冲头损伤大小和弯曲刚度损耗的影响如图7所示为不同能量下铺层方式对弯曲刚度损耗和冲击损伤面积的影响。从图中可以看出不同冲击能量下,冲击载荷对弯曲刚度损耗和冲击损伤面积的影响一致,该结论与图6相同。对于不同等级的冲击能量,1#和5#试样的弯曲刚度损耗和损伤面积均最小,表明这两种铺层方式具有较好的抗冲击性能,而其他铺层的抗冲击性能较弱。这主要是由于5样试样的相邻铺层夹角较小,在冲击载荷作用下层间剪切作用力较低,发生分层损伤的面积较小,刚度损耗较低;而对于1#方格布增强材料,纤维束之间为相互编织状,受到冲击载荷作用时能较好地吸收冲击能量,降低冲击损伤程度,其抗冲击性能较佳。对于其余三种铺层的复合材料拐角,在较低冲击能量o.575J作用时,3#试样的冲击损耗和冲击损伤面积最大,其抗冲击性能最弱;而在较高冲击能量作用下,4#试样的抗冲击性能最弱。童薰(a)0.575J能量冲击下冲击损耗和冲击面积(b)1.15J能量冲击下冲击损耗和冲击面积(C)2.3J冲击下能量冲击损耗和冲击面积图7不同铺层方式对冲击损伤面积和弯曲刚度损耗的影响Fig.7Damageareasandstiffnessdegradationof5lay-upsatvariousimpactenergylevels5结论本文通过四点弯曲实验和冲击实验测试了不同能量作用下、不同铺层方式复合材料拐角的抗冲击性能,得到以下结论:(1)相同厚度不同铺层的复合材料拐角冲击前的弯曲刚度不同,相邻铺层夹角较小的5#试样弯曲刚度最大,方格布弯曲刚度次之,而采用正交铺层的2#-4#试样刚度较低;(2)对于不同铺层的复合材料拐角,冲击损伤面积与弯曲刚度损耗之间呈一致性,均随冲击能量的增加而增大;(3)铺层方式对复合材料拐角的抗冲击性能有较大影响,相邻铺层问夹角较小的5#试样抗冲击性能最佳,损伤面积和弯曲刚度损耗值均最小。在较低冲击能量下,3#试样的抗冲击性能最差,在较高冲击能量下,4#试样抗冲击性能较差。因此在采用单向布铺层制备复合材料拐角时,为获得较好的抗冲击性能,应尽量避免选择0。和9O。交叉铺设,应该用±45。将其隔开。参考文献—[1]SalaG.Postimpactbehaviorofaerospacecompositesexperiments—andsimulations[JJ.CompositesPartB:Engineering,1997,28(56):651-665.[2]LeeDG,CheonSS.ImpactCharacteristicsGlassFiberCompositeswithRespecttoFiberVolumeFraction[J1.JournalofCompositeMa-terials,2001,35(1):27-54./l嗽4・Q骥瑟羞静∞柏如加m0复合材料拐角的抗冲击性能实验研究2014年10月[3]MomaMFSF,MarquesAT.Predictionoflowvelocityimpact—damageinc ̄bonepoxylaminates[J].CompositesPartA:Applied—ScienceandManufacturing,2002,33(3):361368.[4]ChoiHY,DownsRJ,ChangFK.Anewapproachtowardunder-standingdamagemechanismsandmechanicsoflaminatedcomposite—duetolowvelocityimpact,PartI:Experiments[J].JournalofCom-—positeMaterials,1991,25(8):9921011.[5]HitcbenSA,OginSL,SmithPA,SoutisC.Theeffectoffiberlengthonfracturetoughnessandnotchedstrengthofshortcarbonfi-—ber/epoxycomposites[J].Composites,1994,25(6):407413.—[6]ParkR,JangJ.Astudyoftheimpactpropertiesofcompositesconsistingofsurfacemodifiedglassfibersinvinylesterresin[J].Com・positesScienceandTechnology,1998,58(6):979-985.[7]林智育,许希武.含任意椭圆核各向异性板杂交应力有限元[J].固体力学学报,2006,27(2):181-185.[8]张彦中,宁荣昌.复合材料层合板抗冲击损伤的参数表征[J].—航空材料学报,1995,15(1):5662.[9]沈真,杨胜春,陈普会.复合材料层压板抗冲击行为及表征方法—的实验研究[J].复合材料学报,2008,25(5):125133.[10]沈真,刘俊石.两种不同韧性复合材料体系抗冲击和损伤性能—的试验研究,623S-200201119[R].中国飞机强度研究所科技档案,2002.[11]沈真,陈普会,刘俊石,等.含缺陷复合材料层合板压缩破坏机—理[J].航空学报,1991,12(3):105113.[12]郑锡涛,沈真,等.低速冲击与准静态压痕力复合材料层合板的损伤等效性[J].航空学报,2010,31(5):928-933.[13]庄茁,宋恒旭,彭涛,汪丽媛.复合材料低速冲击损伤研究及—等效模型的应用[J].工程力学,2012,s2:1522.’EXPERIMENTALINVESTIGATIoNoNIMPACTRESISTANCEOFCOMPUSlrlECORNERS——ZULei,HUHaixiao,WANGjihui,LIShu・xin(SchoolofMaterialsScienceandEngineering,WuhanUniversityofTechnology,Wuhan430070,China)——Abstract:Thepolymericcompositelaminatesshowrelativelyhighimpactsensitivity.Eventhelowenergyimpactonthelaminatesinserviceiseasytocauseinvisibledamagesandthedegradationofthestrengthandstiffness—andthusseverelythreatenthesafetyofthelaminates.Thebendingstiffnessdegradationsofglassfiberreinforcedvi——nylestercompositecomersmadeoffivelayupsarerespectivelyobservedwiththeaidoffourpointbendingtests.——Theinfluenceofvariouslayupsandimpactenergylevelsontheimpactresistanceofthecompositecomersisevaluated.Theresultsconcludethattheincreaseintheimpactenergyleadstomoreimpactdamageandlowerresidualbendingstiffness;theimpactdamageareasofthefivespecimensexhibitbasicallyidenticaltendencywiththeirstiff-nessdegradation.Thecloserfiberanglesoftwoadjacentlayersresultinthehigherbendingstiffnessandthelower—after.impactstiffnessdegradationofthecompositecomers.Itisfurtherindicatedthatthe[45。/0。/一45。/90。]lay—upproducesthelowestafterimpactstiffnessdegradationofthecompositecomersandthecrossplyspecimenshavethelowestimpactresistance.Keywords:compositematerials;comer;impactdamage;bendingstiffnessFRP/CM2Ol4。N0.10
您可能关注的文档
- “离位”增韧复合材料准静态压入损伤特性研究.pdf
- “神舟七号”飞船舱外航天服防护头盔组件的研制.pdf
- “十二五”复合材料发展重点和方向解读.pdf
- “珠串”堆叠超结构的介孔铁酸锌的制备与表征.pdf
- (001)应变对正交相Ca2 P0.25 Si0.75能带结构及光学性质的影响.pdf
- 0.8设计系数用X80管线钢在近中性pH溶液中的应力腐蚀开裂行为.pdf
- 0.20mm CGO硅钢高温退火Goss晶粒起源及异常长大行为研究.pdf
- 0Cr16Ni5Mo低碳马氏体不锈钢的热变形行为及其热加工图.pdf
- 0Cr17Ni4Cu4Nb钢制螺钉断裂原因分析.pdf
- 1.5MW风机叶片模具加热工艺研究与技术创新.pdf
- 1.5MW风机叶片VARI工艺模拟分析及验证.pdf
- 2.5维机织复合材料低速冲击性能研究.pdf
- 2.25Cr-1Mo钢后续热处理中的磷偏聚行为.pdf
- 2A50锻铝三点弯曲试验与高分辨率CT成像分析.pdf
- 2A12与2A11铝合金超声波焊接工艺与组织研究.pdf
- 2MW风机复合材料叶片材料及工艺研究.pdf
- 3Cr2W8V模具钢激光表面相变硬化层性能的研究.pdf
- 3D打印技术及先进应用研究进展.pdf
- 3D打印技术研究现状和关键技术.pdf
- 5%鱼藤酮悬浮剂的研制.pdf

- 村长
- 该用户很懒,什么也没介绍
相关文档
- “离位”增韧复合材料准静态压入损伤特性研究.pdf2021-11-235页
- “神舟七号”飞船舱外航天服防护头盔组件的研制.pdf2021-11-233页
- “十二五”复合材料发展重点和方向解读.pdf2021-11-232页
- “珠串”堆叠超结构的介孔铁酸锌的制备与表征.pdf2021-11-235页
- (001)应变对正交相Ca2 P0.25 Si0.75能带结构及光学性质的影响.pdf2021-11-236页
- 0.8设计系数用X80管线钢在近中性pH溶液中的应力腐蚀开裂行为.pdf2021-11-237页
- 0.20mm CGO硅钢高温退火Goss晶粒起源及异常长大行为研究.pdf2021-11-237页