- 文档大小:741.01 KB
- 文档格式:pdf
- 约 3页
- 2022-04-11 发布
- 举报
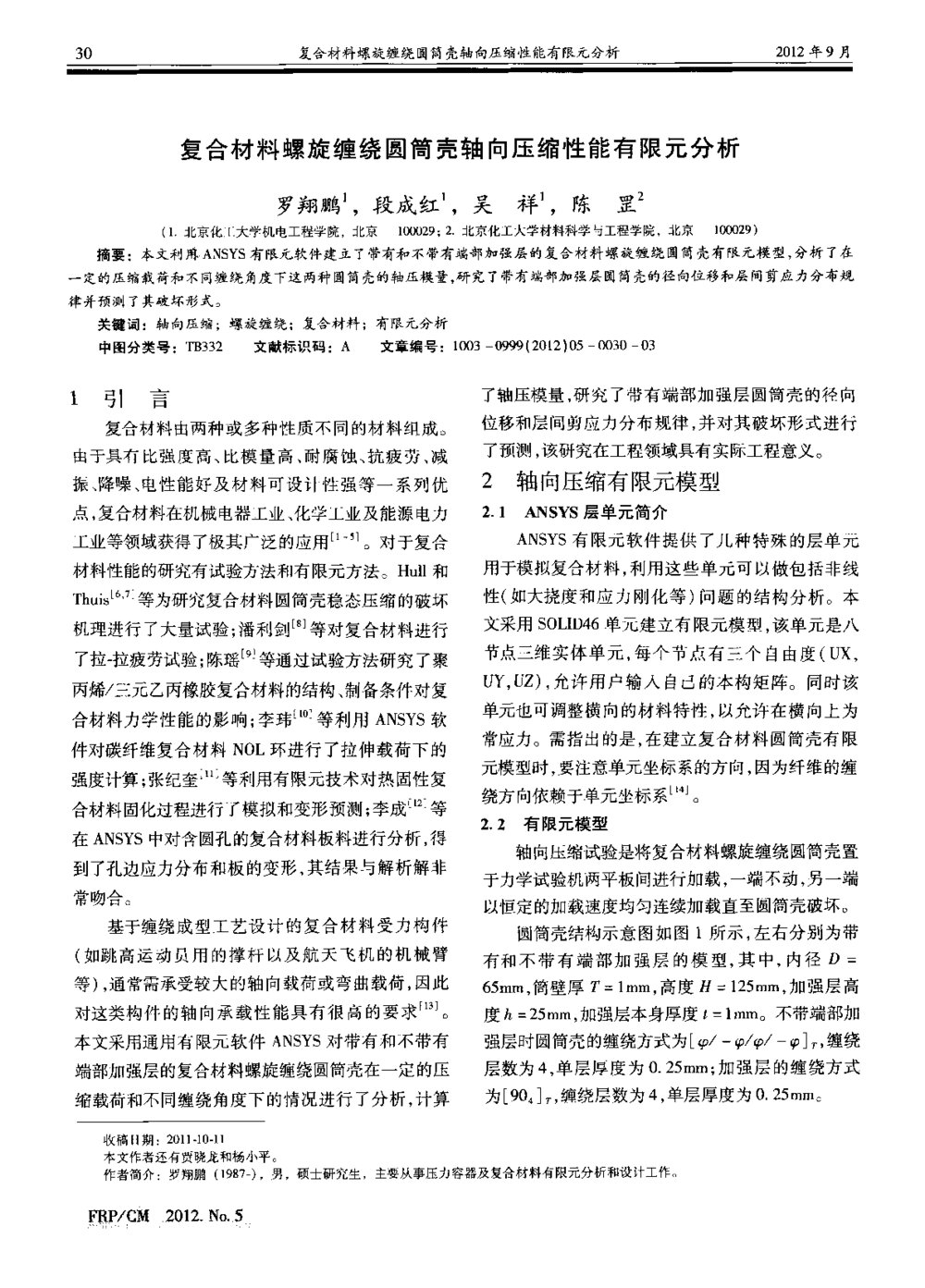
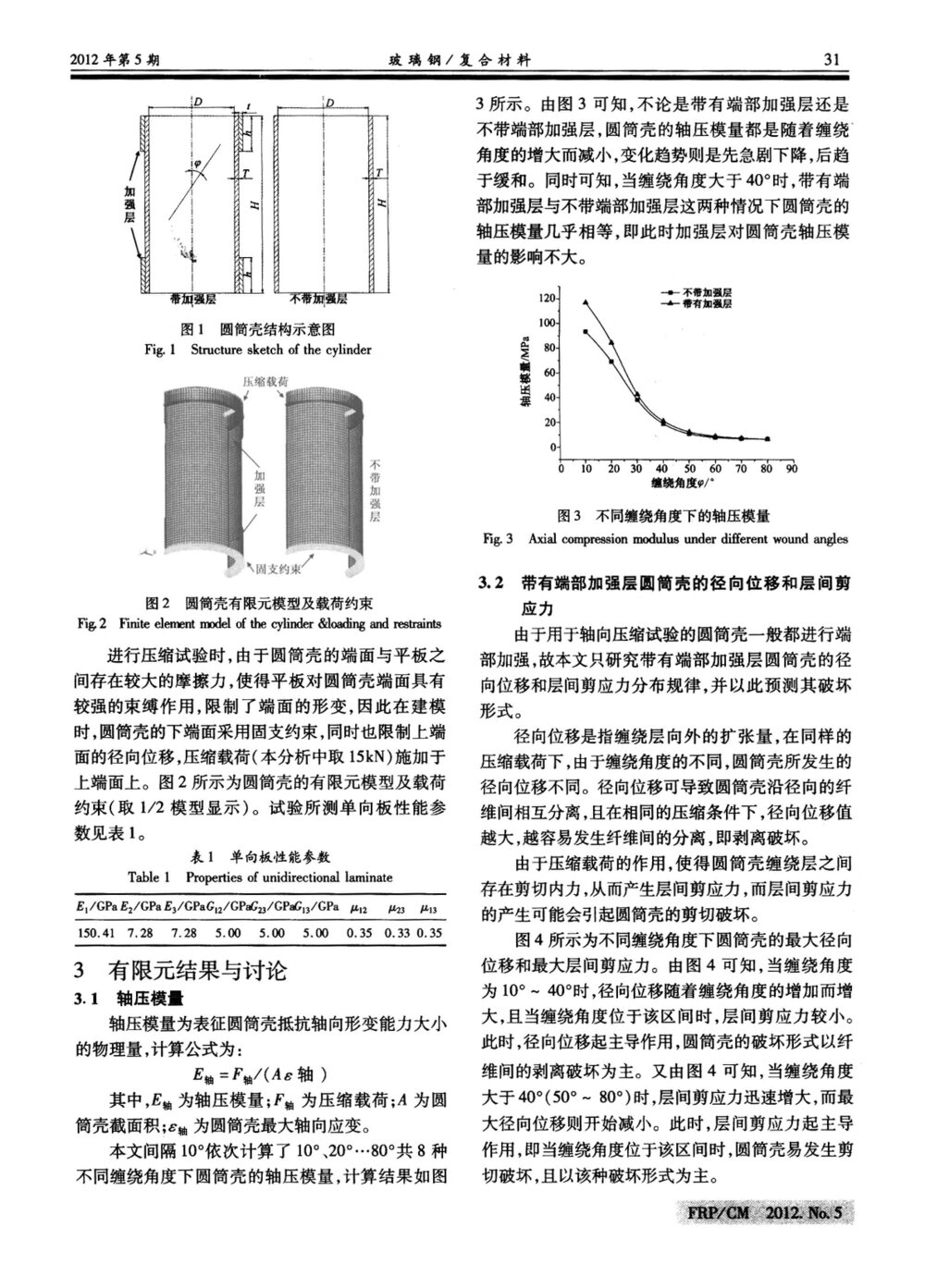
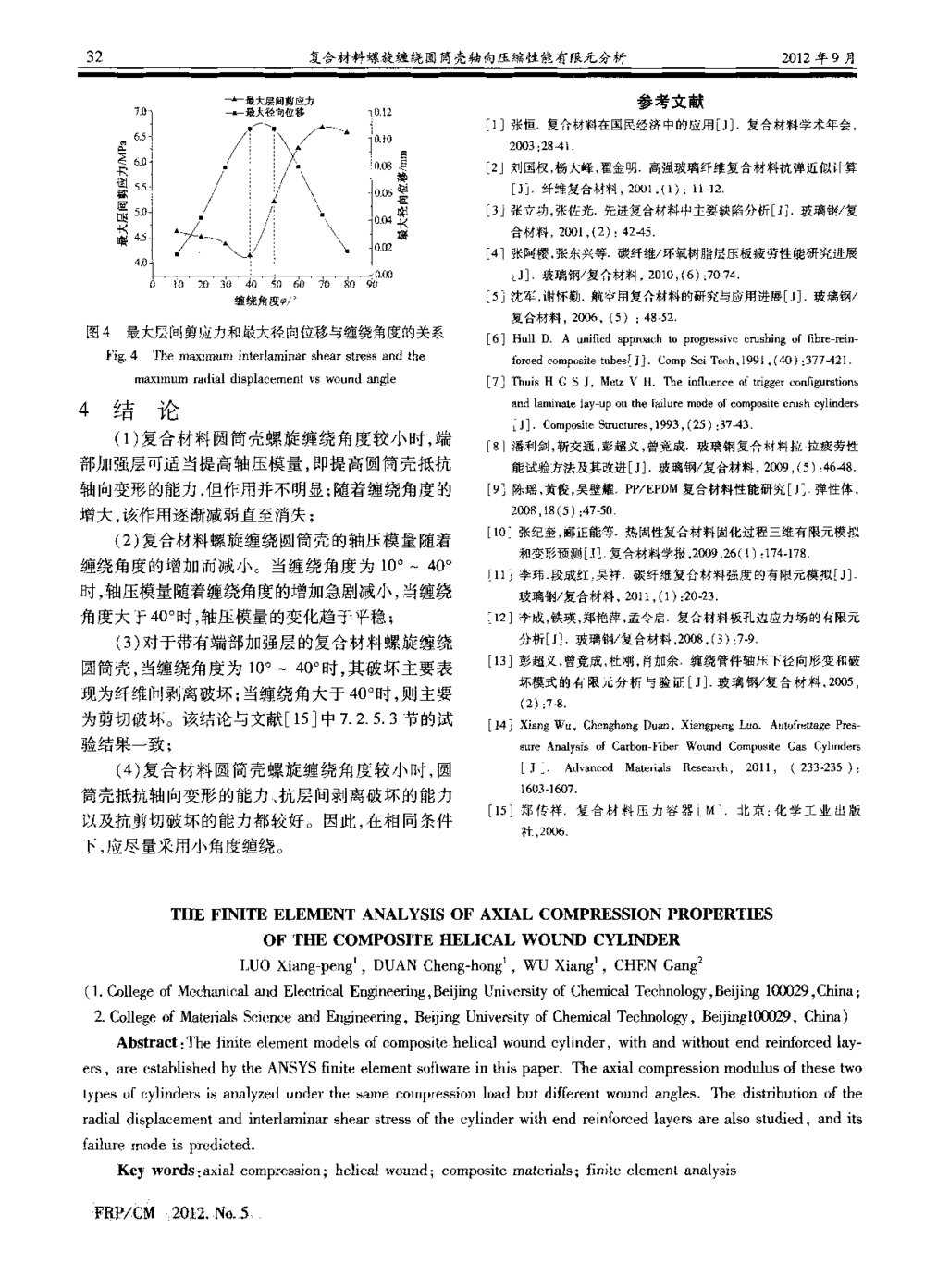
已阅读完毕,您还可以下载文档进行保存
- 1、本文档共3页,内容下载后可编辑。
- 2、本文档内容版权归属内容提供方,所产生的收益全部归内容提供方所有。如果您对本文有版权争议,可选择认领。
- 3、本文档由用户上传,本站不保证质量和数量令人满意,可能有诸多瑕疵,付费之前,请仔细先通过免费阅读内容等途径辨别内容交易风险。如存在严重挂羊头卖狗肉之情形,可联系本站下载客服投诉处理。
30复合材料螺旋缠绕圆筒壳轴向压缩性能有限元分析2012年9月复合材料螺旋缠绕圆筒壳轴向压缩性能有限元分析罗翔鹏1,段成红1,吴祥1,陈罡2(1.北京化工大学机电工程学院,北京100029;2.北京化工大学材料科学与工程学院,北京100029)摘要:本文利群ANSYS有限元软件建立了带有和不带有端部加强层的复合材料螺旋缠绕圆筒壳有限元模型,分析了在一定的压缩载荷和不同缠绕角度下这两种圆筒壳的轴压模量,研究了带有端部加强层圆筒壳的径向位移和层间剪应力分布规律并预测了其破坏形式。关键词:轴向压缩;螺旋缠绕;复合材料;有限元分析中图分类号:TB332文献标识码:A文章编号:1003—0999(2012)05—0030—031引言复合材料由两种或多种性质不同的材料组成。由于具有比强度高、比模量高、耐腐蚀、抗疲劳、减振、降噪、电性能好及材料可设计性强等一系列优点,复合材料在机械电器工业、化学工业及能源电力工业等领域获得了极其广泛的应用¨。]。对于复合材料性能的研究有试验方法和有限元方法。Hull和Thuis∞’刊等为研究复合材料圆筒壳稳态压缩的破坏机理进行了大量试验;潘利剑旧1等对复合材料进行了拉.拉疲劳试验;陈瑶一1等通过试验方法研究了聚丙烯/三元乙丙橡胶复合材料的结构、制备条件对复合材料力学性能的影响;李玮¨刨等利用ANSYS软件对碳纤维复合材料NOL环进行了拉伸载荷下的强度计算;张纪奎¨¨等利用有限元技术对热固性复合材料固化过程进行了模拟和变形预测;李成¨2o等在ANSYS中对含圆孑L的复合材料板料进行分析,得到了孔边应力分布和板的变形,其结果与解析解非常吻合。基于缠绕成型工艺设计的复合材料受力构件(如跳高运动员用的撑杆以及航天飞机的机械臂等),通常需承受较大的轴向载荷或弯曲载荷,因此对这类构件的轴向承载性能具有很高的要求¨川。本文采用通用有限元软件ANSYS对带有和不带有端部加强层的复合材料螺旋缠绕圆筒壳在一定的压缩载荷和不同缠绕角度下的情况进行了分析,计算了轴压模量,研究了带有端部加强层圆筒壳的径向位移和层间剪应力分布规律,并对其破坏形式进行了预测,该研究在工程领域具有实际工程意义。2轴向压缩有限元模型2.1ANSYS层单元简介ANSYS有限元软件提供了几种特殊的层单元用于模拟复合材料,利用这些单元可以做包括非线性(如大挠度和应力刚化等)问题的结构分析。本文采用SOLID46单元建立有限元模型,该单元是八节点三维实体单元,每个节点有三个自由度(UX,UY,Uz),允许用户输人自己的本构矩阵。同时该单元也可调整横向的材料特性,以允许在横向上为常应力。需指出的是,在建立复合材料圆筒壳有限元模型时,要注意单元坐标系的方向,因为纤维的缠绕方向依赖于单元坐标系¨4|。2.2有限元模型轴向压缩试验是将复合材料螺旋缠绕圆筒壳置于力学试验机两平板间进行加载,一端不动,另一端以恒定的加载速度均匀连续加载直至圆筒壳破坏。圆筒壳结构示意图如图1所示,左右分别为带有和不带有端部加强层的模型,其中,内径D=65mm,筒壁厚T=1mm,高度H=125mm,加强层高度h=25mm,加强层本身厚度t=1mm。不带端部加强层时圆筒壳的缠绕方式为[9/一q,/q)/一妒],,缠绕层数为4,单层厚度为0.25mm;加强层的缠绕方式为[90。],,缠绕层数为4,单层厚度为0.25ram。收稿日期:2011—10-11本文作者还有贾晓龙和杨小平。作者简介:罗翔鹏(1987一),男,硕士研究生,主要从事压力容器及复合材料有限元分析和设计工作。聩P/CM2012.No.52012年第5期玻璃钢/复合材料3l图1圆筒壳结构示意图Fig.1Structuresketchofthecylinder图2圆筒壳有限元模型及载荷约束Fig.2FinitedementrIHklofthecylinder&loadingandrestraints进行压缩试验时,由于圆筒壳的端面与平板之间存在较大的摩擦力,使得平板对圆筒壳端面具有较强的束缚作用,限制了端面的形变,因此在建模时,圆筒壳的下端面采用固支约束,同时也限制上端面的径向位移,压缩载荷(本分析中取15kN)施加于上端面上。图2所示为圆筒壳的有限元模型及载荷约束(取1/2模型显示)。试验所测单向板性能参数见表1。表1单向板性能参数Table1PropertiesofunidirectionallaminateEI/GPaE2/GPaE3/GPaGl2/GPaG∞/GPaGl3/GPap12舰3p13150.417.287.285.005.005.000.350.330.353有限元结果与讨论3.1■轴压模轴压模量为表征圆筒壳抵抗轴向形变能力大小的物理量,计算公式为:E轴=F轴/(A占轴)其中,E轴为轴压模量;F轴为压缩载荷;A为圆筒壳截面积;占轴为圆筒壳最大轴向应变。本文间隔100依次计算了10。、20…。800共8种不同缠绕角度下圆筒壳的轴压模量,计算结果如图3所示。由图3可知,不论是带有端部加强层还是不带端部加强层,圆筒壳的轴压模量都是随着缠绕角度的增大而减小,变化趋势则是先急剧下降,后趋于缓和。同时可知,当缠绕角度大于400时,带有端部加强层与不带端部加强层这两种情况下圆筒壳的轴压模量几乎相等,即此时加强层对圆筒壳轴压模量的影响不大。£罨一轼甚暴缠绕角度p/6图3不同缠绕角度下的轴压模量Fig.3Axialcompressionmodulusunderdifferentwoundangoles3.2带有端部加强层圆筒壳的径向位移和层间剪应力由于用于轴向压缩试验的圆筒壳一般都进行端部加强,故本文只研究带有端部加强层圆筒壳的径向位移和层间剪应力分布规律,并以此预测其破坏形式。径向位移是指缠绕层向外的扩张量,在同样的压缩载荷下,由于缠绕角度的不同,圆筒壳所发生的径向位移不同。径向位移可导致圆筒壳沿径向的纤维间相互分离,且在相同的压缩条件下,径向位移值越大,越容易发生纤维间的分离,即剥离破坏。由于压缩载荷的作用,使得圆筒壳缠绕层之间存在剪切内力,从而产生层间剪应力,而层间剪应力的产生可能会引起圆筒壳的剪切破坏。图4所示为不同缠绕角度下圆筒壳的最大径向位移和最大层间剪应力。由图4可知,当缠绕角度为10。一400时,径向位移随着缠绕角度的增加而增大,且当缠绕角度位于该区间时,层间剪应力较小。此时,径向位移起主导作用,圆筒壳的破坏形式以纤维间的剥离破坏为主。又由图4可知,当缠绕角度大于400(50。一800)时,层间剪应力迅速增大,而最大径向位移则开始减小。此时,层间剪应力起主导作用,即当缠绕角度位于该区间时,圆筒壳易发生剪切破坏,且以该种破坏形式为主。嗣强;,它酶12012.,蟹酝jS32复合材料螺旋缠绕圆筒壳轴向压缩性能有限元分析2012年9月7.o日6.5室6.o穴器ss蠢50蔷。s4.o——^_一最大层间剪应力缠绕角度p/。图4最大层间剪应力和最大径向位移与缠绕角度的关系Fig.4ThemaximuminterlaminarshearstressandthemaximumradialdisplacementVSwoundangle4结论(1)复合材料圆筒壳螺旋缠绕角度较小时,端部加强层可适当提高轴压模量,即提高圆筒壳抵抗轴向变形的能力,但作用并不明显;随着缠绕角度的增大,该作用逐渐减弱直至消失;(2)复合材料螺旋缠绕圆筒壳的轴压模量随着缠绕角度的增加而减小。当缠绕角度为100~400时,轴压模量随着缠绕角度的增加急剧减小,当缠绕角度大于400时,轴压模量的变化趋于平稳;(3)对于带有端部加强层的复合材料螺旋缠绕圆筒壳,当缠绕角度为10。一40。时,其破坏主要表现为纤维间剥离破坏;当缠绕角大于400时,则主要为剪切破坏。该结论与文献[15]中7.2.5.3节的试验结果一致;(4)复合材料圆筒壳螺旋缠绕角度较小时,圆筒壳抵抗轴向变形的能力、抗层间剥离破坏的能力以及抗剪切破坏的能力都较好。因此,在相同条件下,应尽量采用小角度缠绕。参考文献[1]张恒.复合材料在国民经济中的应用[J].复合材料学术年会,2003:28-41,[2]刘国权,杨大峰,翟金明.高强玻璃纤维复合材料抗弹近似计算[J]。纤维复合材料,2001,(1):11—12.[3]张立功,张佐光.先进复合材料中主要缺陷分析[J].玻璃钢/复合材料,2001,(2):42-45.[4]张阿樱,张东兴等.碳纤维/环氧树脂层压板疲劳性能研究进展[J].玻璃钢/复合材料,2010,(6):70-74.[5]沈军,谢怀勤.航空用复合材料的研究与应用进展[J].玻璃钢/复合材料,2006,(5):48—52.[6]HullD.Aunifiedapproachtoprogressivecrushingoffibre—rein—forcedcompositetubes[J].CompSciTech,1991,(40):377.421.[7]ThuisHGSJ,MetzVH.Theinfluenceoftriggerconfigurationsandlaminatelay—upOnthefailuremodeofcompositecrashcylinders[J].CompositeStructures,1993,(25):3743.[8]潘利剑,靳交通,彭超义,曾竞成.玻璃钢复合材料拉一拉疲劳性能试验方法及其改进[J].玻璃钢/复合材料,2009,(5):46-48.[9]陈瑶,黄俊,吴壁耀.PP/EPDM复合材料性能研究[J].弹性体,2008,18(5):47-50.[10]张纪奎,郦正能等.热固性复合材料固化过程三维有限元模拟和变形预测[J].复合材料学报,2009,26(1):174—178.[11]李玮,段成红,吴祥.碳纤维复合材料强度的有限元模拟[J].玻璃钢/复合材料,2011,(1):20-23.[12]李成,铁瑛,郑艳萍,盂令启.复合材料板孑L边应力场的有限元分析[J].玻璃钢/复合材料,2008,(3):7-9.[13]彭超义,曾竟成,杜刚,肖加余.缠绕管件轴压下径向形变和破坏模式的有限元分析与验证[J].玻璃钢/复合材料,2005,(2):7.8,[14]XiangWu,ChenghongDuan,XiangpengLuo.AutofrettagePres—sureAnalysisofCarbon-FiberWoundCompositeGasCylinders[J].AdvancedMaterialsResearch,2011,(233-235):1603.1607.[15]郑传祥.复合材料压力容器[M].北京:化学工业出版社,2006.THEFINITEELEMENTANALYSISOFAXL~LCoMPRESSIONPROPERT皿SoFTHECoMPoSITEHELICALWOUNDCYL姗ERLUOXiang—pen91,DUANCheng-hon91,WUXian91,CHENGan92(1.CollegeofMechanicalandElectricalEngineering,BeijingUniversityofChemicalTechnology,Beijing100029,China;2.CollegeofMaterialsScienceandEngineering,BeijingUniversityofChemicalTechnology,Beijin9100029,China)Abstract:Thefiniteelementmodelsofcompositehelicalwoundcylinder,withandwithoutendreinforcedlay.ers.areestablishedbytheANSYSfiniteelementsoftwareinthispaper.Theaxialcompressionmodulusofthesetwotypesofcylindersisanalyzedunderthesamecompressionloadbutdifferentwoundangles。Thedistributionoftheradialdisplacementandinterlaminarshearstressofthecylinderwithendreinforcedlayersarealsostudied.anditsfailuremodeispredicted.Keywords:axialcompression;helicalwound;compositematerials;finiteelementanalysisFRWCM2012.No.5
您可能关注的文档
- “离位”增韧复合材料准静态压入损伤特性研究.pdf
- “神舟七号”飞船舱外航天服防护头盔组件的研制.pdf
- “十二五”复合材料发展重点和方向解读.pdf
- “珠串”堆叠超结构的介孔铁酸锌的制备与表征.pdf
- (001)应变对正交相Ca2 P0.25 Si0.75能带结构及光学性质的影响.pdf
- 0.8设计系数用X80管线钢在近中性pH溶液中的应力腐蚀开裂行为.pdf
- 0.20mm CGO硅钢高温退火Goss晶粒起源及异常长大行为研究.pdf
- 0Cr16Ni5Mo低碳马氏体不锈钢的热变形行为及其热加工图.pdf
- 0Cr17Ni4Cu4Nb钢制螺钉断裂原因分析.pdf
- 1.5MW风机叶片模具加热工艺研究与技术创新.pdf
- 1.5MW风机叶片VARI工艺模拟分析及验证.pdf
- 2.5维机织复合材料低速冲击性能研究.pdf
- 2.25Cr-1Mo钢后续热处理中的磷偏聚行为.pdf
- 2A50锻铝三点弯曲试验与高分辨率CT成像分析.pdf
- 2A12与2A11铝合金超声波焊接工艺与组织研究.pdf
- 2MW风机复合材料叶片材料及工艺研究.pdf
- 3Cr2W8V模具钢激光表面相变硬化层性能的研究.pdf
- 3D打印技术及先进应用研究进展.pdf
- 3D打印技术研究现状和关键技术.pdf
- 5%鱼藤酮悬浮剂的研制.pdf

- 大叔大爷
- 该用户很懒,什么也没介绍
相关文档
- “离位”增韧复合材料准静态压入损伤特性研究.pdf2021-11-235页
- “神舟七号”飞船舱外航天服防护头盔组件的研制.pdf2021-11-233页
- “十二五”复合材料发展重点和方向解读.pdf2021-11-232页
- “珠串”堆叠超结构的介孔铁酸锌的制备与表征.pdf2021-11-235页
- (001)应变对正交相Ca2 P0.25 Si0.75能带结构及光学性质的影响.pdf2021-11-236页
- 0.8设计系数用X80管线钢在近中性pH溶液中的应力腐蚀开裂行为.pdf2021-11-237页
- 0.20mm CGO硅钢高温退火Goss晶粒起源及异常长大行为研究.pdf2021-11-237页