- 文档大小:458.46 KB
- 文档格式:pdf
- 约 7页
- 2022-04-11 发布
- 举报

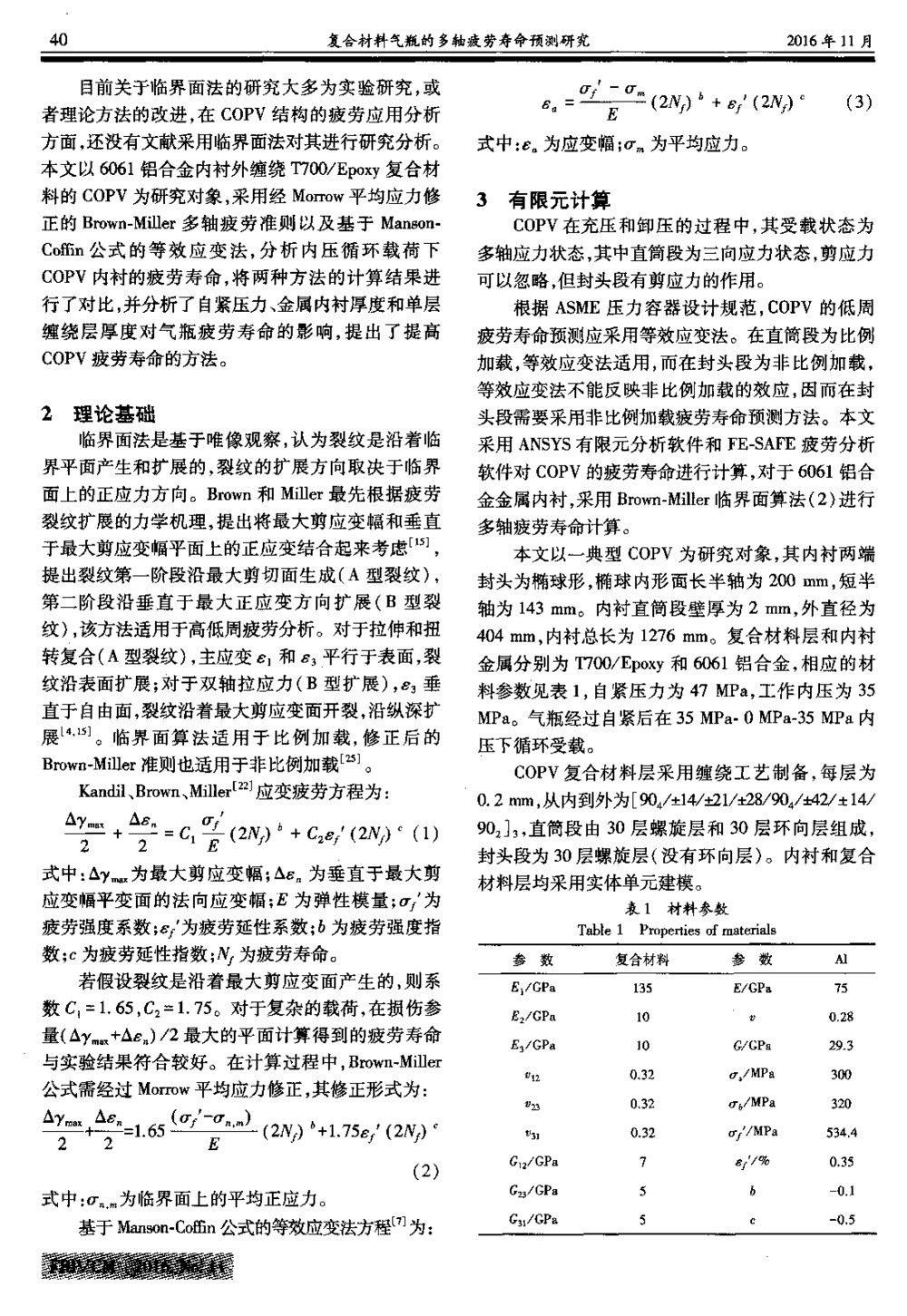
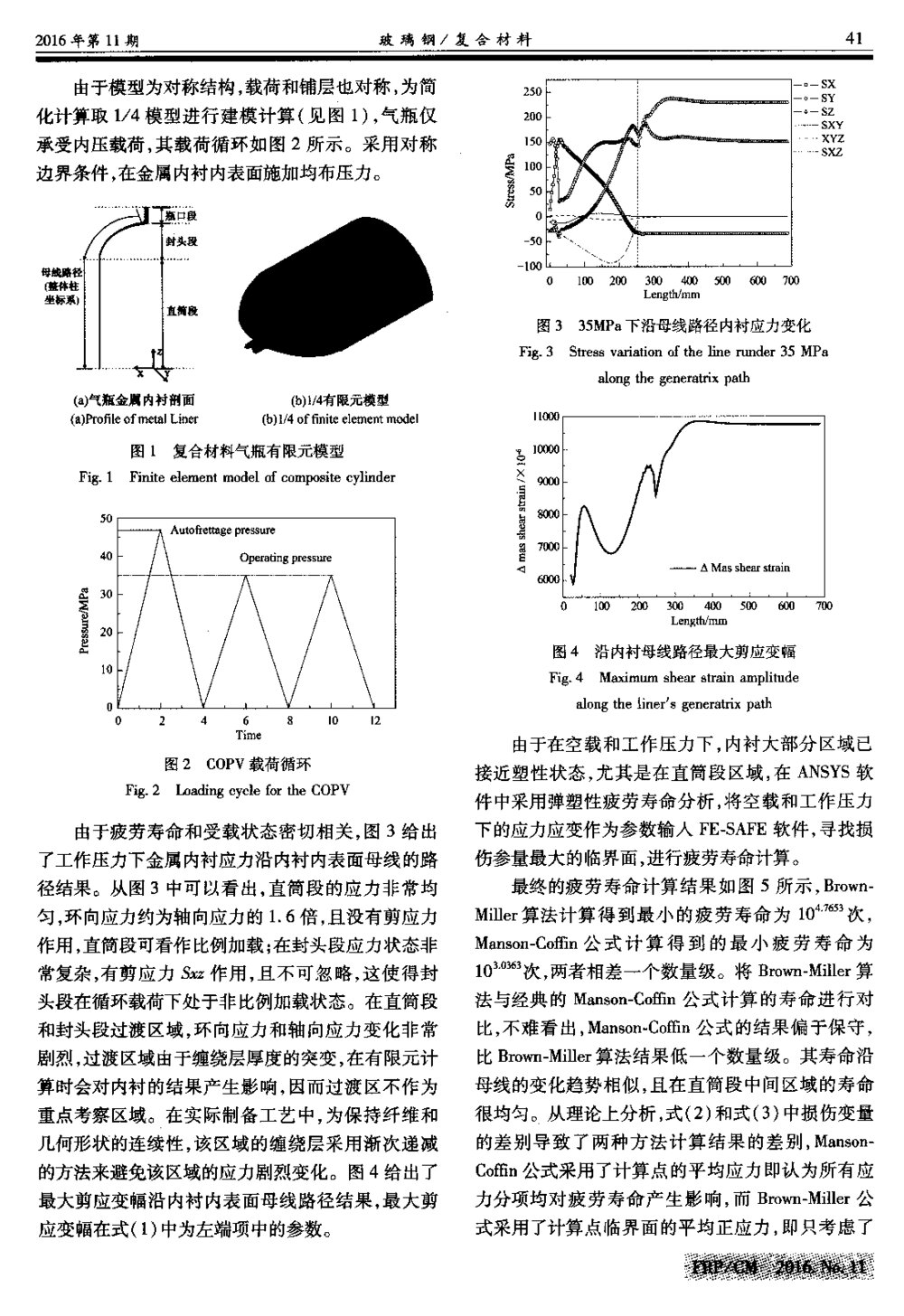
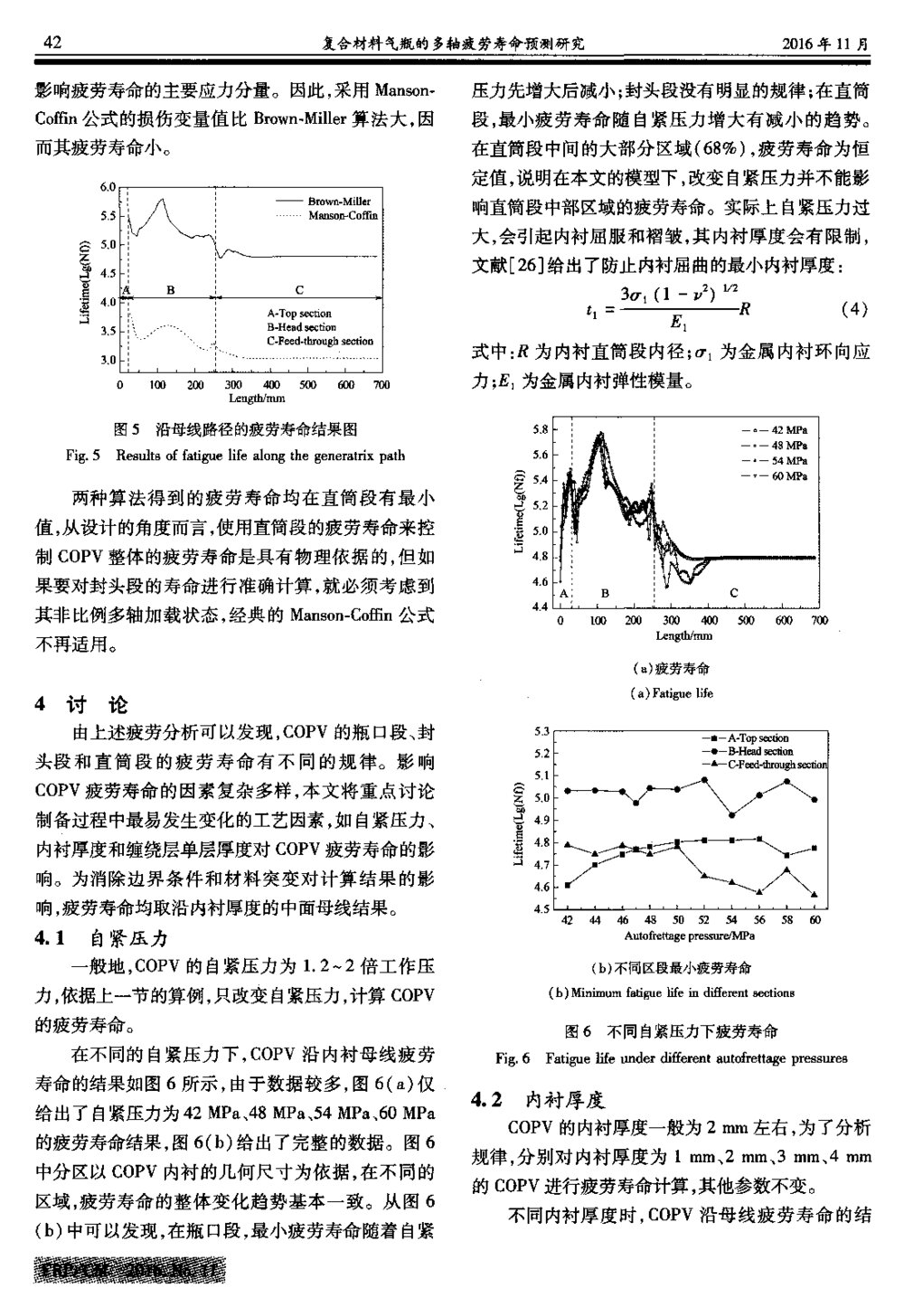
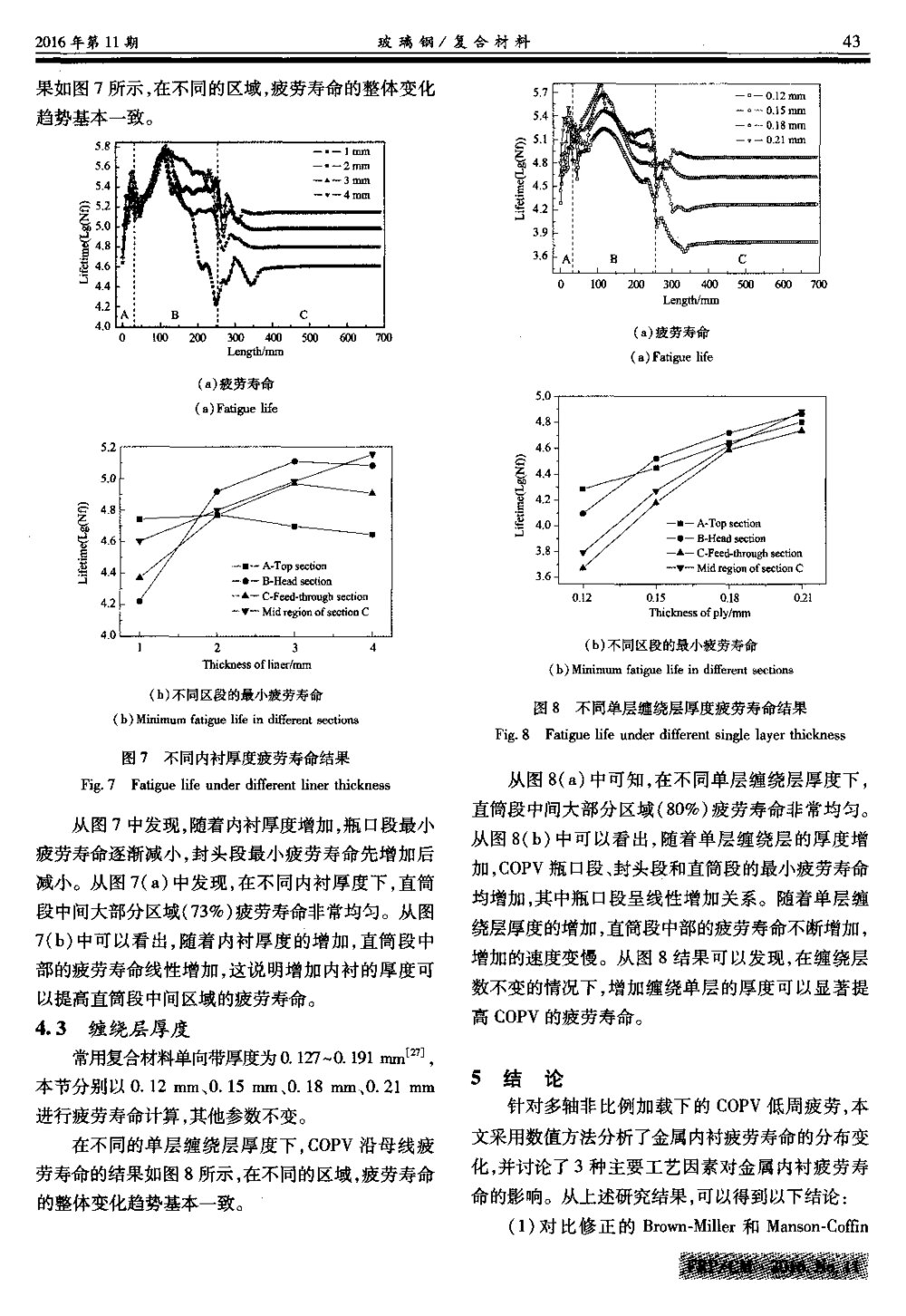
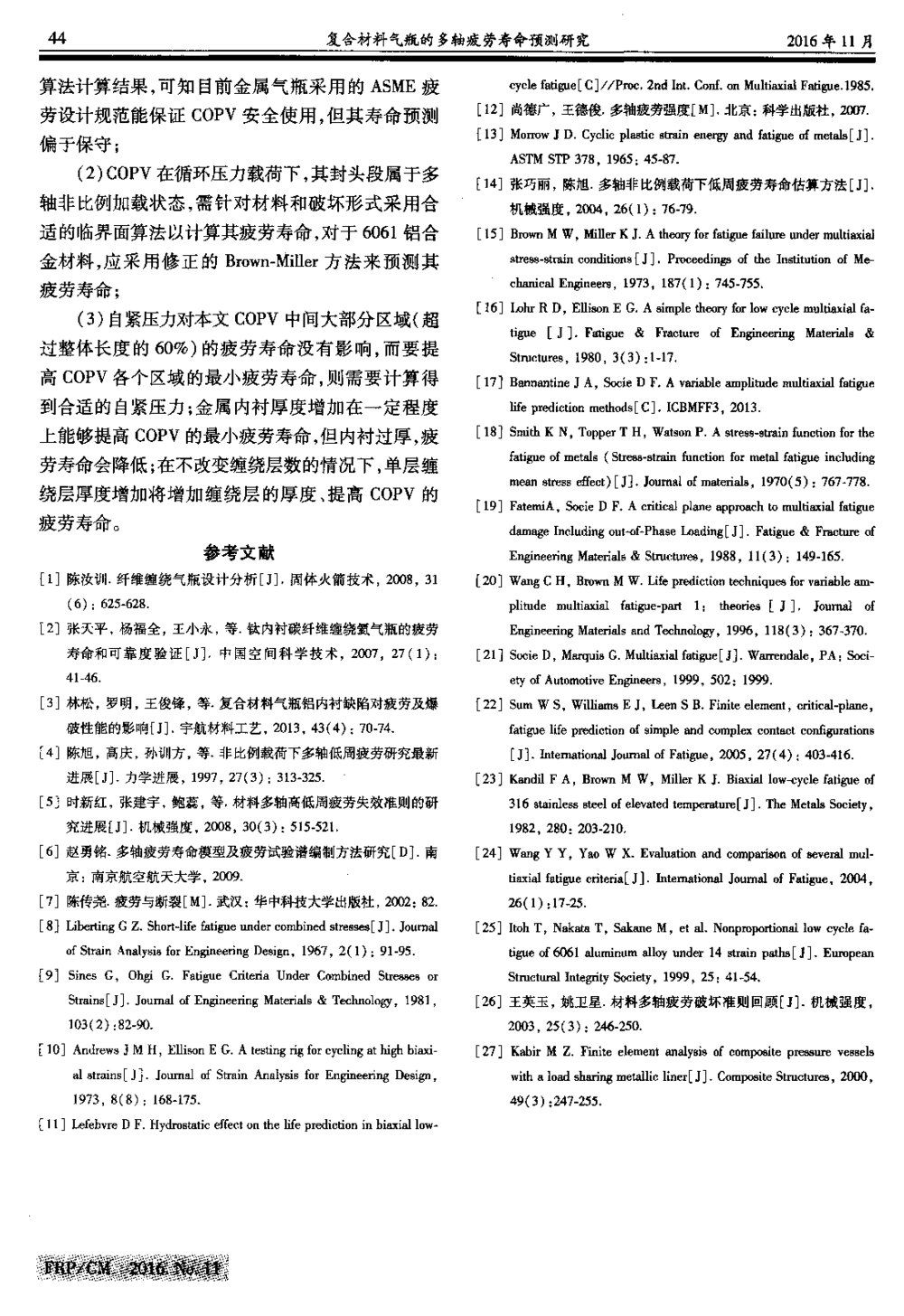
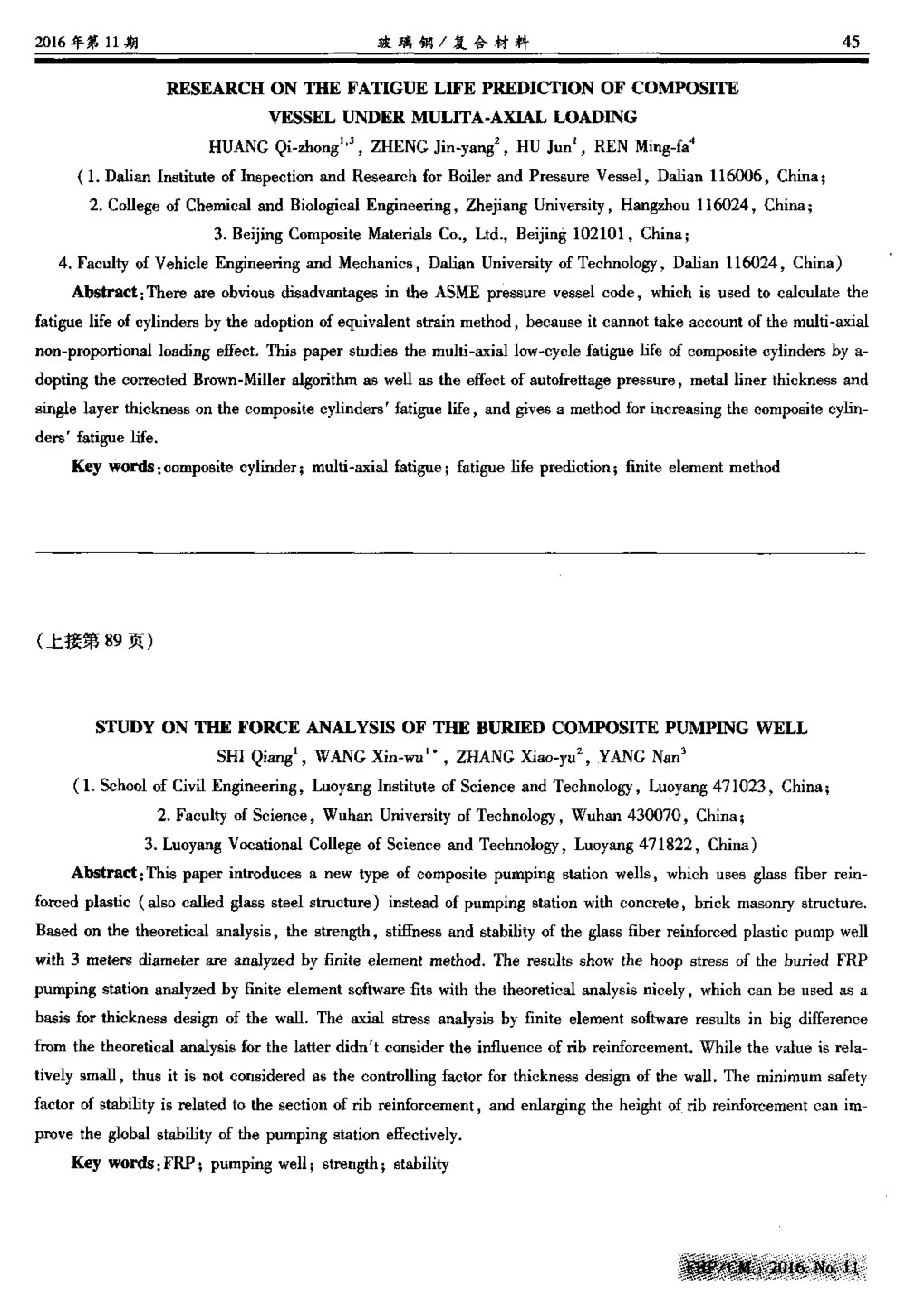
已阅读完毕,您还可以下载文档进行保存
- 1、本文档共7页,内容下载后可编辑。
- 2、本文档内容版权归属内容提供方,所产生的收益全部归内容提供方所有。如果您对本文有版权争议,可选择认领。
- 3、本文档由用户上传,本站不保证质量和数量令人满意,可能有诸多瑕疵,付费之前,请仔细先通过免费阅读内容等途径辨别内容交易风险。如存在严重挂羊头卖狗肉之情形,可联系本站下载客服投诉处理。
2016年第11期玻璃钢/复合材料39复合材料气瓶的多轴疲劳寿命预测研究黄其忠l,,郑津洋,胡军,任明法4(1.大连市锅炉压力容器检验研究院,大连116006;2.浙江大学化学工程与生物工程学院,杭州116024;3.北京玻钢院复合材料有限公司,北京102101;4.大连理工大学运载工程与力学学部,大连116024)摘要:采用等效应变法计算气瓶疲劳寿命的ASME压力容器规范,不能考虑多轴非比例加栽效应,具有明显的不足。针对复合材料气瓶,采用修正的Brown.MiUer算法研究其多轴低周疲劳寿命,并分析了自紧压力、金属内衬厚度和单层缠绕层厚度对复合材料气瓶疲劳寿命的影响,给出了提高复合材料气瓶疲劳寿命的方法。关键词:复合材料气瓶;多轴疲劳;疲劳寿命预测;有限元法中图分类号:TB332文献标识码:A文章编号:1003-0999(2016)11-0039-071前言由金属内衬和复合材料缠绕层构成的复合材料缠绕气瓶(CompositeOverwrappedPressureVessels,“”简称COPV),其中金属内衬主要用于防止气体泄漏并承担部分载荷,复合材料缠绕层为主要承载结构,已被广泛应用于航空航天和汽车领域_1J。在服役中COPV要经历多次的加压和卸压,是典型的疲劳循环加载过程,精确预测COPV的疲劳寿命具有重要的应用意义。纤维增强树脂基复合材料的抗疲劳性能一般比金属材料优越。COPV结构的破坏往往由金属内衬的低疲劳寿命引起,导致介质泄漏而失效J。本文认为与金属内衬相比,复合材料具有优良的抗疲劳性能,在COPV服役过程中疲劳寿命的衰减可忽略不计。因此,文中的疲劳特指金属内衬的疲劳。工程上一般采用单轴疲劳寿命模型分析金属疲劳问题。然而,COPV金属内衬处于典型的多轴低周疲劳载荷中L3J,采用单轴疲劳模型显然不适用。ASME压力容器设计规范采用最大剪应变作为等效应变,计算压力容器的疲劳寿命HJ,能用于比例加载情况,但不适用于多轴非比例加载。目前,尚缺乏一种对各种材料和载荷都普遍适用的多轴低周疲劳理论,。已有的多轴低周疲劳寿命预测方法大致可分为三种:等效应变法、能量法和临界面法J。等效应变—法,最著名的是MansonCoffin公式,其损伤参量—为塑性应变。在早期的多轴低周疲劳研究中,Bonaeuse和Zamfik等将单轴拉压低周疲劳模型推广到多轴情况,将等效应变作为损伤参量,可以是最大正应变]、最大切应变,加]、VonMises等效应变[11],或者是这些应变的塑性分量。等效应变法对于比例加载简单有效,但它没有明确的物理基础,不能体现加载路径和应力状态对疲劳寿命的影响。能量法是基于功、能守恒的关系被提出来的,该观点认为材料不可逆的损伤进而疲劳破坏是由于塑性功的不断累计造成的。能量法的优点在于应用范围广、适用于各种载荷,但是其判据并没有得到学者们的普遍认可,且需要一个精确的本构方程,难以在工程中得到实际应用1。临界面法是构造疲劳破坏的临界面,以临界面上应力应变历程作为损伤参量来建立疲劳损伤模型,该方法具有一定的物理意义。1973年Brown和Miller¨提出临界面法,Lohr和Ellison于1980年也给出了类似的方法¨。临界面法以最大剪应变幅和最大剪应变幅平面上的法向应变幅作为损伤参量oBannanfine¨将单轴Smith-Watson-Topper¨副损伤模型推广到多轴,建立新的多轴疲劳损伤模型。Fatemi和Socie¨将剪应变幅和最大正应力进行组合建立了一个多轴疲劳损伤参量。Wang和Brown等.2考虑最大剪切面上的法向应变幅,对由Kandil、Brown和Miller给出的损伤参量进行了修—正。王英玉通过对比Ito等的实验,得到Kandil、Brown和MiNer提出的疲劳准则在预测6061铝合金的高低周疲劳方面精度很高。收稿日期:2016 ̄5-25本文作者还有张靖。作者简介:黄其忠(1983一),男,博士,高级工程师,主要从事复合材料结构设计方面的研究,qizhongh@126.corn。复合材料气瓶的多轴疲劳寿命预测研究2016年11月目前关于临界面法的研究大多为实验研究,或者理论方法的改进,在COPV结构的疲劳应用分析方面,还没有文献采用临界面法对其进行研究分析。本文以6061铝合金内衬外缠绕T700/Epoxy复合材料的COPV为研究对象,采用经Morrow平均应力修—正的BrownMiUer多轴疲劳准则以及基于Manson-Coffin公式的等效应变法,分析内压循环载荷下COPV内衬的疲劳寿命,将两种方法的计算结果进行了对比,并分析了自紧压力、金属内衬厚度和单层缠绕层厚度对气瓶疲劳寿命的影响,提出了提高COPV疲劳寿命的方法。2理论基础临界面法是基于唯像观察,认为裂纹是沿着临界平面产生和扩展的,裂纹的扩展方向取决于临界面上的正应力方向。Brown和Miller最先根据疲劳裂纹扩展的力学机理,提出将最大剪应变幅和垂直于最大剪应变幅平面上的正应变结合起来考虑¨,提出裂纹第一阶段沿最大剪切面生成(A型裂纹),第二阶段沿垂直于最大正应变方向扩展(B型裂纹),该方法适用于高低周疲劳分析。对于拉伸和扭转复合(A型裂纹),主应变占和平行于表面,裂纹沿表面扩展;对于双轴拉应力(B型扩展),垂直于自由面,裂纹沿着最大剪应变面开裂,沿纵深扩展'J。临界面算法适用于比例加载,修正后的—BrownMiller准则也适用于非比例加载J。Kandil、Brown、Miller【2应变疲劳方程为:A ̄max+ⅣⅣ:c。(2,)+C:,(2,)c(1)二二凸△△式中:为最大剪应变幅;s为垂直于最大剪应变幅平变面的法向应变幅;E为弹性模量;o7为疲劳强度系数;,为疲劳延性系数;b为疲劳强度指Ⅳ数;c为疲劳延性指数;,为疲劳寿命。若假设裂纹是沿着最大剪应变面产生的,则系数C=1.65,c:=1.75。对于复杂的载荷,在损伤参△△量(一+)/2最大的平面计算得到的疲劳寿命—与实验结果符合较好。在计算过程中,BrownMiller公式需经过Morrow平均应力修正,其修正形式为:A ̄/max+Ⅳ竽:1.65孚(2Ns)6+1.75,(2,)c‘二凸(2)式中:or.为临界面上的平均正应力。基于Manson-Coffin公式的等效应变法方程为:华(2(2(3)式中:占。为应变幅;为平均应力。3有限元计算COPV在充压和卸压的过程中,其受载状态为多轴应力状态,其中直筒段为三向应力状态,剪应力可以忽略,但封头段有剪应力的作用。根据ASME压力容器设计规范,COPV的低周疲劳寿命预测应采用等效应变法。在直筒段为比例加载,等效应变法适用,而在封头段为非比例加载,等效应变法不能反映非比例加载的效应,因而在封头段需要采用非比例加载疲劳寿命预测方法。本文—采用ANSYS有限元分析软件和FESAFE疲劳分析软件对COPV的疲劳寿命进行计算,对于6061铝合—金金属内衬,采用BrownMiller临界面算法(2)进行多轴疲劳寿命计算。本文以一典型COPV为研究对象,其内衬两端封头为椭球形,椭球内形面长半轴为200mm,短半轴为143mm。内衬直筒段壁厚为2mm,外直径为404mm,内衬总长为1276mm。复合材料层和内衬金属分别为T700/Epoxy和6061铝合金,相应的材料参数见表1,自紧压力为47MPa,工作内压为35MPa。气瓶经过自紧后在35MPa一0MPa一35MPa内压下循环受载。COPV复合材料层采用缠绕工艺制备,每层为0.2mln,从内到外为[904/+14/_+_21/:t=28/904/:L-,42/=1:14/90:],,直筒段由30层螺旋层和3O层环向层组成,封头段为30层螺旋层(没有环向层)。内衬和复合材料层均采用实体单元建模。表1材料参数Table1Propertiesofmaterials2016年第11期玻璃钢/复合材料41由于模型为对称结构,载荷和铺层也对称,为简化计算取1/4模型进行建模计算(见图1),气瓶仅承受内压载荷,其载荷循环如图2所示。采用对称边界条件,在金属内衬内表面施加均布压力。一(a)气瓶金属内衬剖面(b)l/4有限元模型(a)Profi ̄ofmealLiner(b)1/4offini ̄elementmodel图1复合材料气瓶有限元模型Fig.1Finiteelementmodelofcomposi ̄cylinder图2COPV载荷循环Fig.2Loadingcyclef0rtheCOPV由于疲劳寿命和受载状态密切相关,图3给出了工作压力下金属内衬应力沿内衬内表面母线的路径结果。从图3中可以看出,直筒段的应力非常均匀,环向应力约为轴向应力的1.6倍,且没有剪应力作用,直筒段可看作比例加载;在封头段应力状态非常复杂,有剪应力Sxz作用,且不可忽略,这使得封头段在循环载荷下处于非比例加载状态。在直筒段和封头段过渡区域,环向应力和轴向应力变化非常剧烈,过渡区域由于缠绕层厚度的突变,在有限元计算时会对内衬的结果产生影响,因而过渡区不作为重点考察区域。在实际制备工艺中,为保持纤维和几何形状的连续性,该区域的缠绕层采用渐次递减的方法来避免该区域的应力剧烈变化。图4给出了最大剪应变幅沿内衬内表面母线路径结果,最大剪应变幅在式(1)中为左端项中的参数。SXSYSZSXYXYZS)(z图335MPa下沿母线路径内衬应力变化Fig.3Stressvari ̄ionofthelinerunder35MPaMongthegeneratfixpath墨量il司图4沿内衬母线路径最大剪应变幅Fig.4MaximumshearstrainamplitudeMongthelinerSgeneratfixpath由于在空载和工作压力下,内衬大部分区域已接近塑性状态,尤其是在直筒段区域,在ANSYS软件中采用弹塑性疲劳寿命分析,将空载和工作压力—下的应力应变作为参数输入FESAFE软件,寻找损伤参量最大的临界面,进行疲劳寿命计算。最终的疲劳寿命计算结果如图5所示,Brown-Mil‘ler算法计算得到最小的疲劳寿命为10次,—MansonCoffin公式计算得到的最小疲劳寿命为’10。次,两者相差一个数量级。将Brown.Miller算法与经典的Manson-Coffin公式计算的寿命进行对比,不难看出,Manson.Coffin公式的结果偏于保守,比Brown.Miller算法结果低一个数量级。其寿命沿母线的变化趋势相似,且在直筒段中间区域的寿命很均匀。从理论上分析,式(2)和式(3)中损伤变量的差别导致了两种方法计算结果的差别,Manson-Coffin公式采用了计算点的平均应力即认为所有应—力分项均对疲劳寿命产生影响,而BrownMiller公式采用了计算点临界面的平均正应力,即只考虑了∞∞∞苣当日∞aJa242复合材料气瓶的多轴疲劳寿命预测研究2016年11月影响疲劳寿命的主要应力分量。因此,采用Manson.—Coffin公式的损伤变量值比BrownMiller算法大,因而其疲劳寿命小。—‘——Btown-Miller…t.Manson-Co佑n、/\YBCA-Topsection’B-Headsection』C-Feed-throughsectionUluU2哪juu44XIuu“JU700LengthJmm图5沿母线路径的疲劳寿命结果图Fig.5Resultsoffatiguelifealongthegeneratrixpath两种算法得到的疲劳寿命均在直筒段有最小值,从设计的角度而言,使用直筒段的疲劳寿命来控制COPV整体的疲劳寿命是具有物理依据的,但如果要对封头段的寿命进行准确计算,就必须考虑到其非比例多轴加载状态,经典的Manson-Coffin公式不再适用。4讨论由上述疲劳分析可以发现,COPV的瓶口段、封头段和直筒段的疲劳寿命有不同的规律。影响COPV疲劳寿命的因素复杂多样,本文将重点讨论制备过程中最易发生变化的工艺因素,如自紧压力、内衬厚度和缠绕层单层厚度对COPV疲劳寿命的影响。为消除边界条件和材料突变对计算结果的影响,疲劳寿命均取沿内衬厚度的中面母线结果。4.1自紧压力一般地,COPV的自紧压力为1.2~2倍工作压力,依据上一节的算例,只改变自紧压力,计算COPV的疲劳寿命。在不同的自紧压力下,COPV沿内衬母线疲劳寿命的结果如图6所示,由于数据较多,图6(a)仅给出了自紧压力为42MPa、48MPa、54MPa、60MPa的疲劳寿命结果,图6(b)给出了完整的数据。图6中分区以COPV内衬的几何尺寸为依据,在不同的区域,疲劳寿命的整体变化趋势基本一致。从图6(b)中可以发现,在瓶口段,最小疲劳寿命随着自紧压力先增大后减小;封头段没有明显的规律;在直筒段,最小疲劳寿命随自紧压力增大有减小的趋势。在直筒段中间的大部分区域(68%),疲劳寿命为恒定值,说明在本文的模型下,改变自紧压力并不能影响直筒段中部区域的疲劳寿命。实际上自紧压力过大,会引起内衬屈服和褶皱,其内衬厚度会有限制,文献[26]给出了防止内衬屈曲的最小内衬厚度:(4)4—————£1()式中:为内衬直筒段内径;为金属内衬环向应力;E为金属内衬弹性模量。(a)疲劳寿命(a)Fatiguelife(b)不I司区段最小疲劳寿命(b)Minimumfatiguelifeindifferentsections图6不同白紧压力下疲劳寿命Fig.6Fatiguelifeunderdifferentautofrettagepressures4.2内衬厚度COPV的内衬厚度一般为2mm左右,为了分析规律,分别对内衬厚度为1mm、2mm、3mm、4mm的COPV进行疲劳寿命计算,其他参数不变。不同内衬厚度时,COPV沿母线疲劳寿命的结05050506554433^_}_口I】一,I一口,I_)0m!aJ2016年第11期玻璃钢/复合材料43果如图7所示,在不同的区域,疲劳寿命的整体变化趋势基本一致。(a)疲劳寿命(a)Fatiguelife(b)不同区段的最小疲劳寿命(b)Minimum ̄tiguelifeindiffe ̄nt ̄ctions图7不同内衬厚度疲劳寿命结果Fig.7Fatiguelifeunderdifferentlinerthickness从图7中发现,随着内衬厚度增加,瓶口段最小疲劳寿命逐渐减小,封头段最小疲劳寿命先增加后减小。从图7(a)中发现,在不同内衬厚度下,直筒段中间大部分区域(73%)疲劳寿命非常均匀。从图7(b)中可以看出,随着内衬厚度的增加,直筒段中部的疲劳寿命线性增加,这说明增加内衬的厚度可以提高直筒段中间区域的疲劳寿命。4.3缠绕层厚度—常用复合材料单向带厚度为0.1270.191nlin],本节分别以0.12mm、0.15mm、0.18mm、0.21mm进行疲劳寿命计算,其他参数不变。在不同的单层缠绕层厚度下,COPV沿母线疲劳寿命的结果如图8所示,在不同的区域,疲劳寿命的整体变化趋势基本一致。(8)疲劳寿命(a)Fatiguelife(b)不同区段的最小疲劳寿命(b)Minimum ̄tiguelindifferentsections图8不同单层缠绕层厚度疲劳寿命结果Fig.8Fatiguelifeunderdifferentsin ̄elayerthickness从图8(a)中可知,在不同单层缠绕层厚度下,直筒段中间大部分区域(80%)疲劳寿命非常均匀。从图8(b)中可以看出,随着单层缠绕层的厚度增加,COPV瓶口段、封头段和直筒段的最小疲劳寿命均增加,其中瓶口段呈线性增加关系。随着单层缠绕层厚度的增加,直筒段中部的疲劳寿命不断增加,增加的速度变慢。从图8结果可以发现,在缠绕层数不变的情况下,增加缠绕单层的厚度可以显著提高COPV的疲劳寿命。5结论针对多轴非比例加载下的COPV低周疲劳,本文采用数值方法分析了金属内衬疲劳寿命的分布变化,并讨论了3种主要工艺因素对金属内衬疲劳寿命的影响。从上述研究结果,可以得到以下结论:——(1)对比修正的BrownMiller和MansonCoffin8642O8642O5555544444^口一一Q目一I1—一目口l1∞一口己曩_盘I1复合材料气瓶的多轴疲劳寿命预测研究2016年11月算法计算结果,可知目前金属气瓶采用的ASME疲劳设计规范能保证COPV安全使用,但其寿命预测偏于保守;(2)COPV在循环压力载荷下,其封头段属于多轴非比例加载状态,需针对材料和破坏形式采用合适的临界面算法以计其疲劳寿命,对于6061铝合—金材料,应采用修正的BrownMiner方法来预测其疲劳寿命;(3)自紧压力对本文COPV中间大部分区域(超过整体长度的60%)的疲劳寿命没有影响,而要提高COPV各个区域的最小疲劳寿命,则需要计算得到合适的自紧压力;金属内衬厚度增加在一定程度上能够提高COPV的最小疲劳寿命,但内衬过厚,疲劳寿命会降低;在不改变缠绕层数的情况下,单层缠绕层厚度增加将增加缠绕层的厚度、提高COPV的疲劳寿命。参考文献[1]陈汝训.纤维缠绕气瓶设计分析[J].固体火箭技术,2008,31—(6):625628.[2]张天平,杨福全,王小永,等.钛内衬碳纤维缠绕氦气瓶的疲劳寿命和可靠度验证[J].中国空间科学技术,2007,27(1):—4146.[3]林松,罗明,王俊锋,等.复合材料气瓶铝内衬缺陷对疲劳及爆—破性能的影响[J].宇航材料工艺,2013,43(4):7074.[4]陈旭,高庆,孙训方,等.非比例载荷下多轴低周疲劳研究最新进展[J].力学进展,1997,27(3):313-325.[5]时新红,张建宇,鲍蕊,等.材料多轴高低周疲劳失效准则的研—究进展[J].机械强度,2008,30(3):515521.[6]赵勇铭.多轴疲劳寿命模型及疲劳试验谱编制方法研究[D].南京:南京航空航天大学,2009.[7]陈传尧.疲劳与断裂[M].武汉:华中科技大学出版社,2002:82.—[8]LibertingGZ.Shoalifefatigueundercombinedstresses[J].Journal—ofStrainAnalysisforEngineeringDesign,1967,2(1):9195.[9]SinesG,OhgiG.FatigueCriteriaUnderCombinedStressesorStrains[J].JournalofEngineeringMaterials&Technology,1981,—103(2):8290.—[10]AndrewsJMH,EllisonEG.Atestingrigforcyclingathighbiaxialstrains[J].JournalofStrainAnalysisforEngineeringDesign,1973,8(8):168-175.[11]LefebvreDF.Hydrostaticeffectonthelifepredictioninbiaxiallow.[12][13][14][15][16][17][18][19][2O][21][22][23][24][25][26]cyclefatigue[C]//Proc.2ndInt.Conf.onMultiaxialFatigue.1985.尚德广,王德俊.多轴疲劳强度[M].北京:科学出版社,2007.MorrowJD.Cyclicplasticstrainenergyandfatigueofmetals[J].—AsTMSTP378。1965:4587.张巧丽,陈旭.多轴非比例载荷下低周疲劳寿命估算方法[J].机械强度,2004,26(1):76-79.BrownMW,MillerKJ.Atheoryforfatiguefailureundermultiaxial—stress-strainconditions[J].ProceedingsoftheInstitutionofMechanicalEngineers,1973,187(1):745-755.LohrRD,EllisonEG.Asimpletheoryforlowcyclemultiaxialfa-tigue[J].Fatigue&FractureofEngineeringMaterials&Structures,1980,3(3):1-17.BannantineJA,SocieDF.Avariableamplitudemultiaxialfatiguelifepredictionmethods[C].ICBMFF3,2013.SmithKN,TopperTH,WatsonP.Astress・strainfunctionforthe—fatigueofmetals(Stressstrainfunctionformetalfatigueincludingmeanstresseffect)[J].Journalofmaterials,1970(5):767-778.FatemiA,SocieDF.Acriticalplaneapproachtomultiaxialfatigueda—mageIncludingoutof-PhaseLoading[J].Fatigue&FractureofEngineeringMaterials&Structures,1988,11(3):149-165.WangCH,BrownMW.Lifepredictiontechniquesforvariablealn-plitudemultiaxialfatigue・part1:theories[J].Journalof—EngineeringMaterialsandTechnology,1996,l18(3):367370.—SocieD,MarquisG.Multiaxialfatigue[J].Warrendale,PA:SocietyofAutomotiveEngineers,1999,502:1999.SumWS,WilliamsEJ,LeenSB.Finiteelement,critical-plane,fatiguelifepredictionofsimpleandcomplexcontactconfigurations[J].InternationalJournalofFatigue,2005,27(4):403-416.Ka—ndilFA,BrownMW,MillerKJ.Biaxiallowcyclefatigueof316s ̄inlesssteelofelevatedtemperature[J].TheMetalsSociety,1982,280:203・210.WangYY,YaoWX.Evaluationandcomparisonofseveralmultiaxialfatiguecriteria[J].InternationalJournalofFatigue,2004。—26(1):1725.hohT,NakataT,SakaneM,eta1.Nonproportionallowcyclefa-tigneof6061aluminumalloyunder14strainpaths[J].European—StructuralIntegritySociety,1999,25:4154.王英玉,姚卫星.材料多轴疲劳破坏准则回顾[J].机械强度,—2003,25(3):246250.[27]KabirMZ.Finiteelementanalysisofcompositepressurevesselswithaloadsharingmetallicliner[J].CompositeStructures,2000,—49(3):247255.2016年第11期玻璃钢/复合材料45’RESEARCHoNTHEFATIGUELIFEPREDICTIoNoCoMPoSITEⅦSSELUNDERMUUTA.AXIALLoADINGHUANGQi.zhong,ZHENGJin-yang,HUJun,RENMing-fa(1.DalianInstituteofInspectionandResearchforBoilerandPressureVessel,Dalian116006,China;2.CoHegeofChemicalandBiologicalEngineering,ZhejiangUniversity,Hangzhou116024,China;3.BeijingCompositeMaterialsCo.,Ltd.,Beijing102101,China;4.FacultyofVehicleEngineeringandMechanics,DalianUniversityofTechnology,Dalian116024,China)Abstract:TherealeobviousdisadvantagesintheASMEpressurevesselcode,whichisusedtocalculatethefatiguelifeofcylindersbytheadoptionofequiva—lentstrainmethod,becauseitcannottakeaccountofthemultiaxial—nonproportionalloadingeffect.T———hispaperstudiesthemultiaxiallowcyclefatiguelifeofcompositecylindersbyadoptingthecorrectedBrown-Milleralgorithmaswellastheeffectofautofrettagepressure,metallinerthicknessandsinglelayerthicknessonthecompositecylindersfatiguelife,andgivesamethodforincreasingthecompositecylin-dersfatiguelife.Keywords:compositecylinder;multi-axialfatigue;fatiguelifeprediction;finiteelementmethod(上接第89页)’’’’’SlUDY0NTIlEFORCEANALYSlSo~IHEBURmDC0MPI'SIIEPUMPINGWELL—SHIQiang,WANGXinwu,ZHANGXiao-yu,YANGNan(1.SchoolofCivilEngineering,LuoyangInstituteofScienceandTechnology,Luoyang471023,China;2.FacultyofScience,WuhanUniversityofTechnology,Wuhan430070,China;3.LuoyangVocationalCollegeofScienceandTechnology,Luoyang471822,China)—Abstract:Thispaperintroducesanewtypeofcompositepumpingstationwells,whichusesglassfiberreinforcedplastic(alsocalledglasssteelstructure)insteadofpumpingstationwithconcrete,brickmasonrystructure.Basedonthetheoreticalanalysis,thestrength,stiffnessandstabilityoftheglassfiberreinforcedplasticpumpwellwith3metersdiameteraleanalyzedbyfiniteelementmethod.TheresultsshowthehoopstressoftheburiedFRPpumpingstationanalyzedbyfiniteelementsoftwarefitswiththetheoreticalanalysisnicely,whichcanbeusedasabasisforthicknessdesignofthewal1.Theaxialstressanalysisbyfiniteelementsoftwareresultsinbigdifferencefromthetheoreticalanalysisforthelatterdidntconsidertheinfluenceofribreinforcement.Whilethevalueisrela.tivelysmall,thusitisnotconsideredasthecontrollingfactorforthicknessdesignofthewal1.Theminimumsafetyfactorofstabilityisrelatedtothesectionofribreinforcement,andenlargingtheheightofribreinforcementcanim.provetheglobalstabilityofthepumpingstationeffectively.Keywords:FRP;pumpingwell;strength;stability
您可能关注的文档
- “离位”增韧复合材料准静态压入损伤特性研究.pdf
- “神舟七号”飞船舱外航天服防护头盔组件的研制.pdf
- “十二五”复合材料发展重点和方向解读.pdf
- “珠串”堆叠超结构的介孔铁酸锌的制备与表征.pdf
- (001)应变对正交相Ca2 P0.25 Si0.75能带结构及光学性质的影响.pdf
- 0.8设计系数用X80管线钢在近中性pH溶液中的应力腐蚀开裂行为.pdf
- 0.20mm CGO硅钢高温退火Goss晶粒起源及异常长大行为研究.pdf
- 0Cr16Ni5Mo低碳马氏体不锈钢的热变形行为及其热加工图.pdf
- 0Cr17Ni4Cu4Nb钢制螺钉断裂原因分析.pdf
- 1.5MW风机叶片模具加热工艺研究与技术创新.pdf
- 1.5MW风机叶片VARI工艺模拟分析及验证.pdf
- 2.5维机织复合材料低速冲击性能研究.pdf
- 2.25Cr-1Mo钢后续热处理中的磷偏聚行为.pdf
- 2A50锻铝三点弯曲试验与高分辨率CT成像分析.pdf
- 2A12与2A11铝合金超声波焊接工艺与组织研究.pdf
- 2MW风机复合材料叶片材料及工艺研究.pdf
- 3Cr2W8V模具钢激光表面相变硬化层性能的研究.pdf
- 3D打印技术及先进应用研究进展.pdf
- 3D打印技术研究现状和关键技术.pdf
- 5%鱼藤酮悬浮剂的研制.pdf

- 乘风破浪
- 该用户很懒,什么也没介绍
相关文档
- “离位”增韧复合材料准静态压入损伤特性研究.pdf2021-11-235页
- “神舟七号”飞船舱外航天服防护头盔组件的研制.pdf2021-11-233页
- “十二五”复合材料发展重点和方向解读.pdf2021-11-232页
- “珠串”堆叠超结构的介孔铁酸锌的制备与表征.pdf2021-11-235页
- (001)应变对正交相Ca2 P0.25 Si0.75能带结构及光学性质的影响.pdf2021-11-236页
- 0.8设计系数用X80管线钢在近中性pH溶液中的应力腐蚀开裂行为.pdf2021-11-237页
- 0.20mm CGO硅钢高温退火Goss晶粒起源及异常长大行为研究.pdf2021-11-237页