- 文档大小:3.36 MB
- 文档格式:pdf
- 约 6页
- 2022-04-11 发布
- 举报
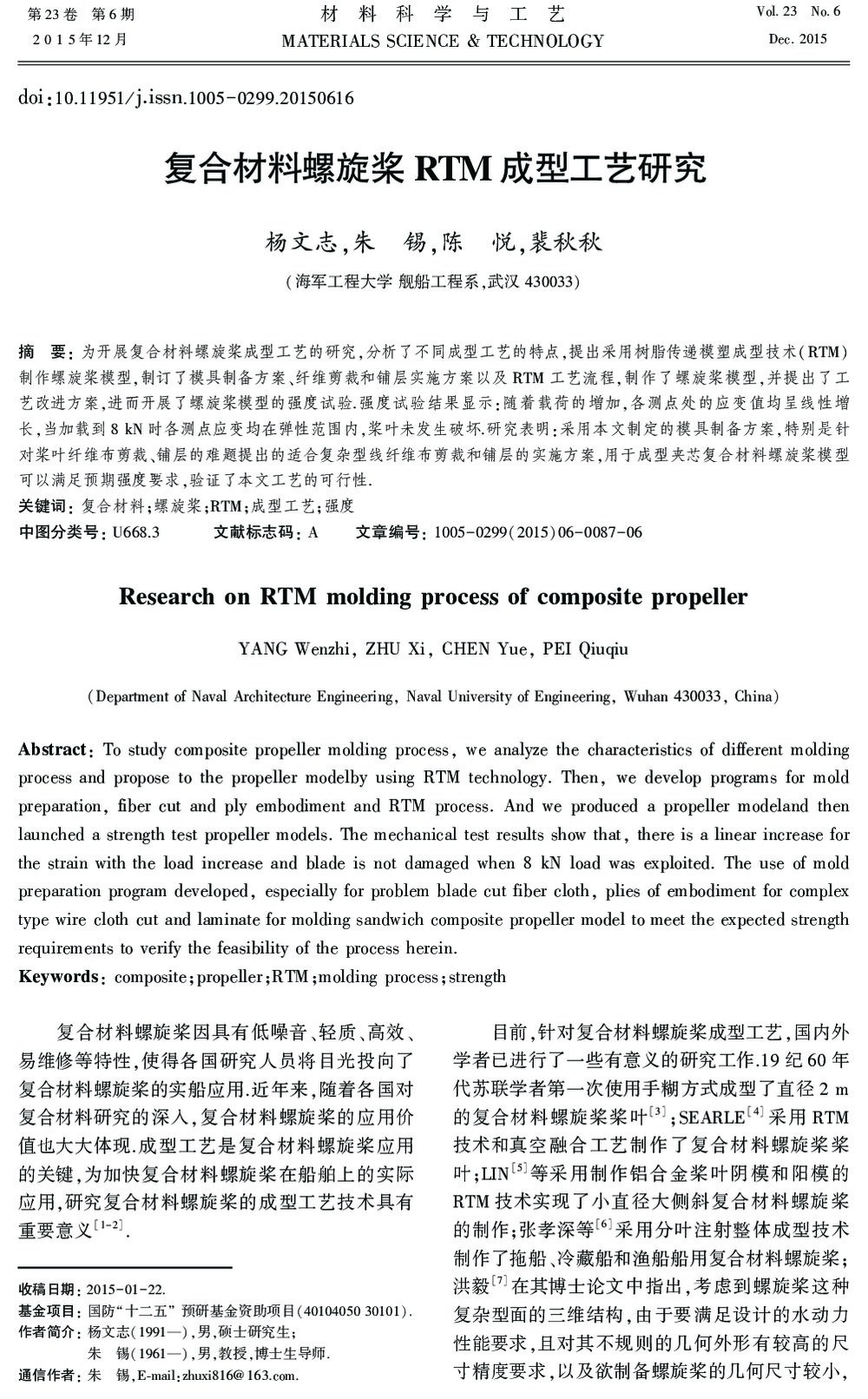
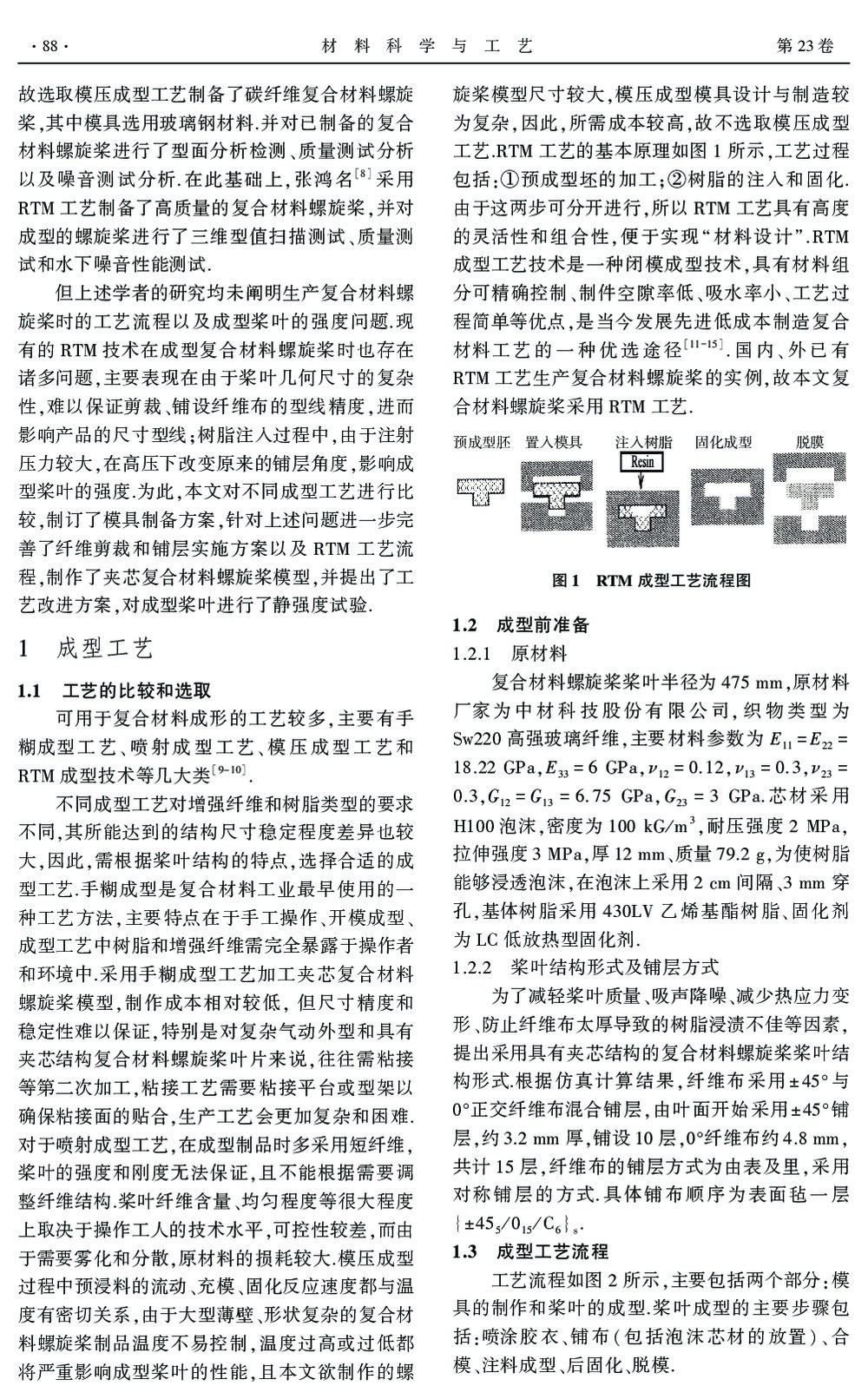
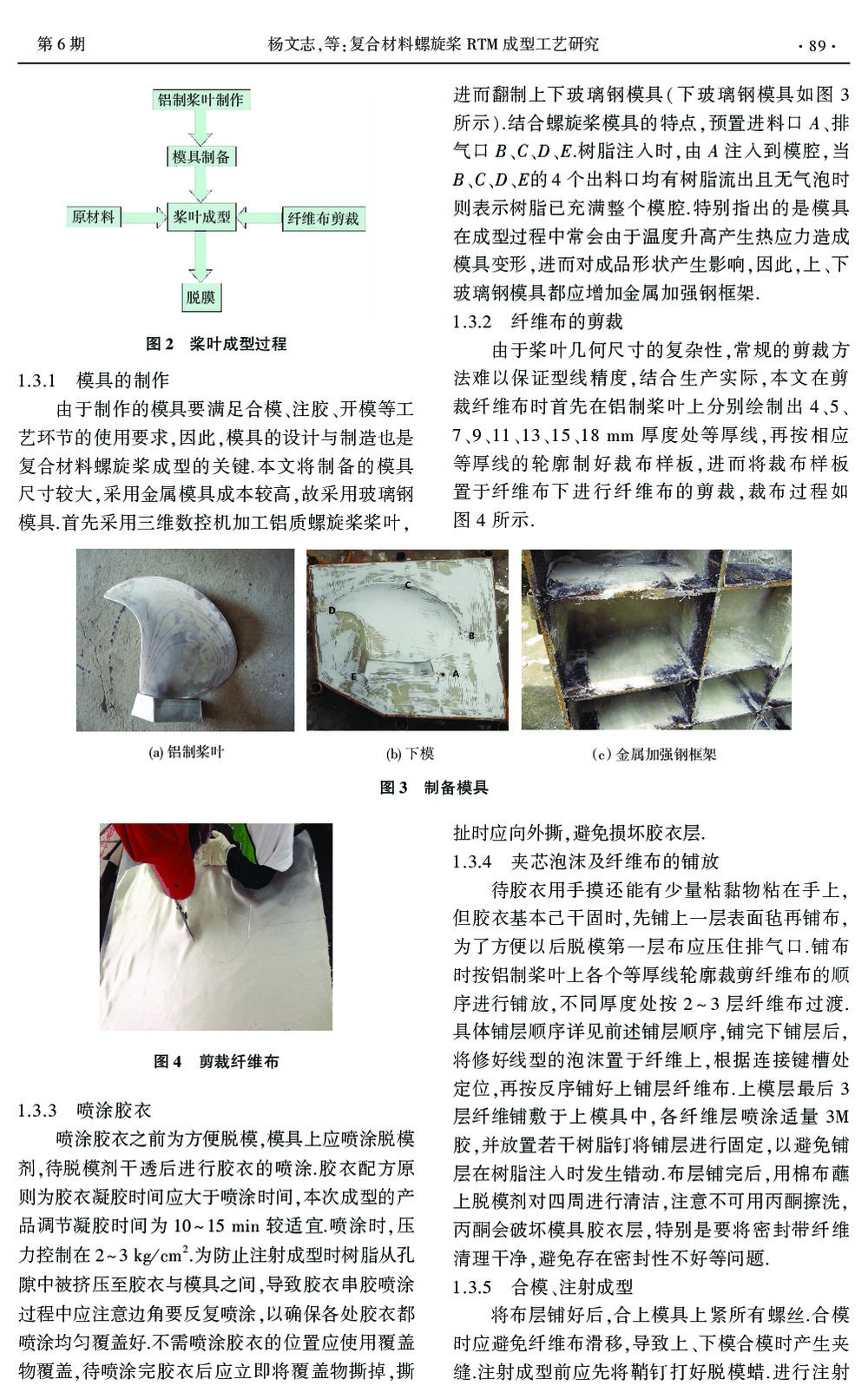
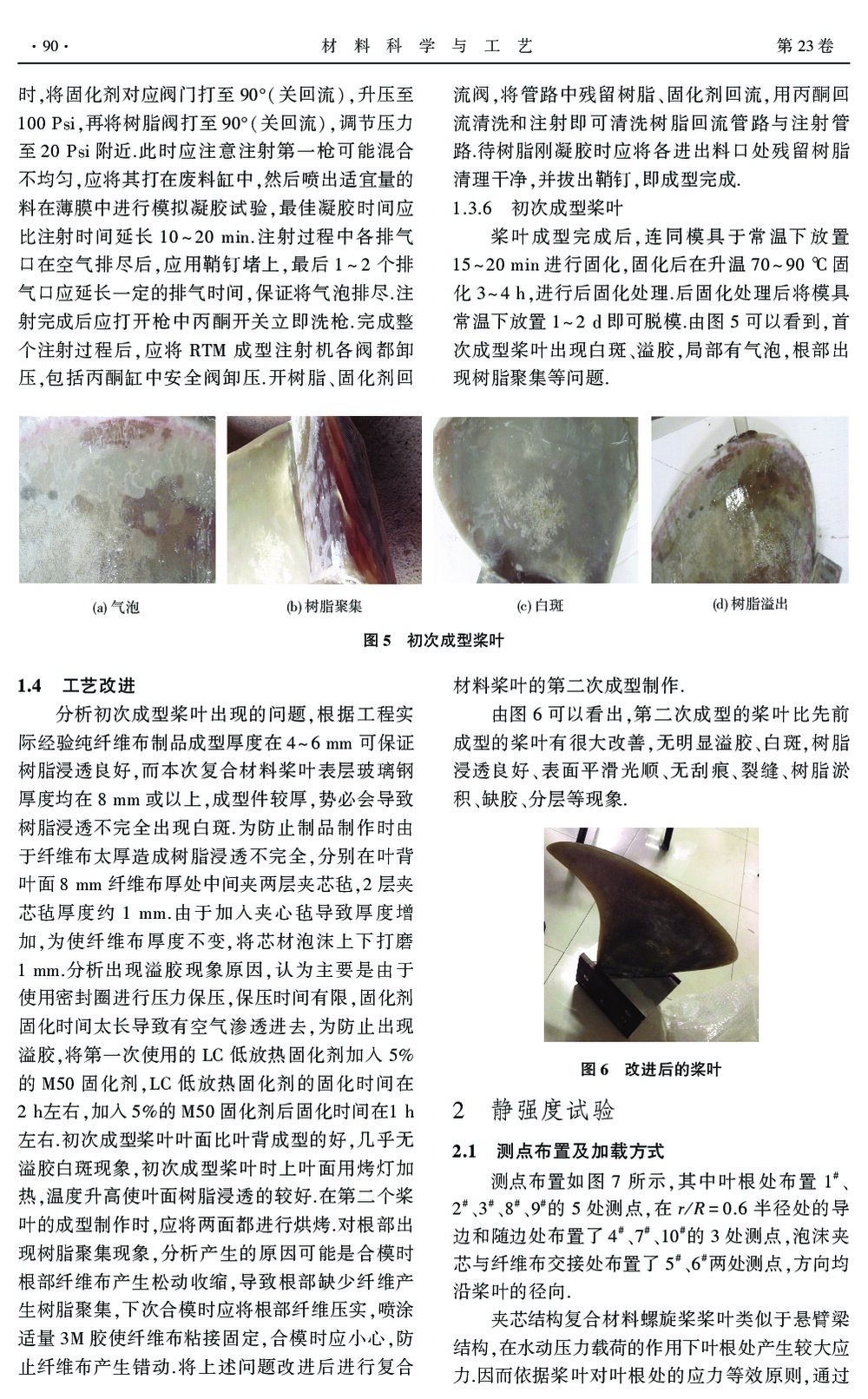
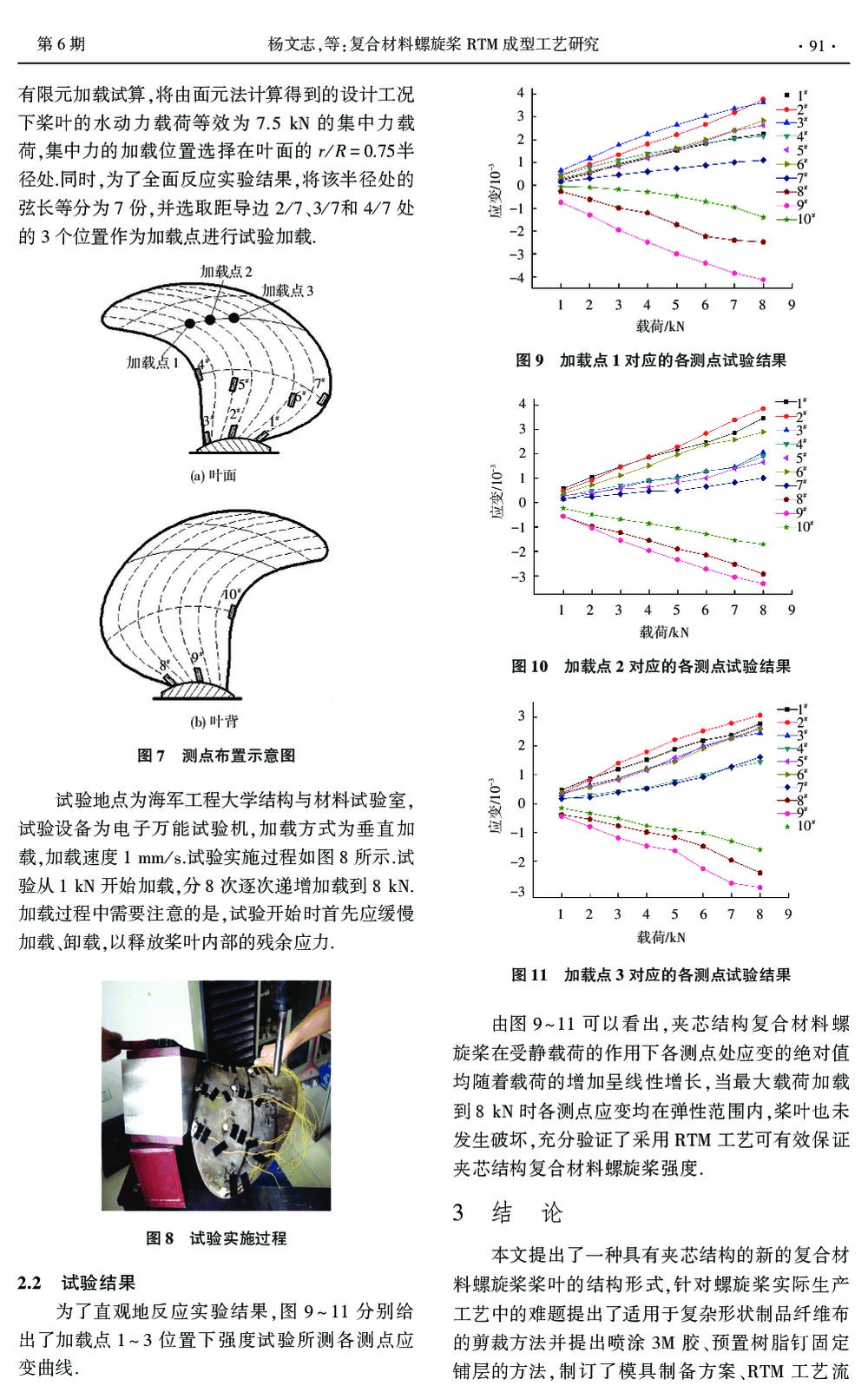
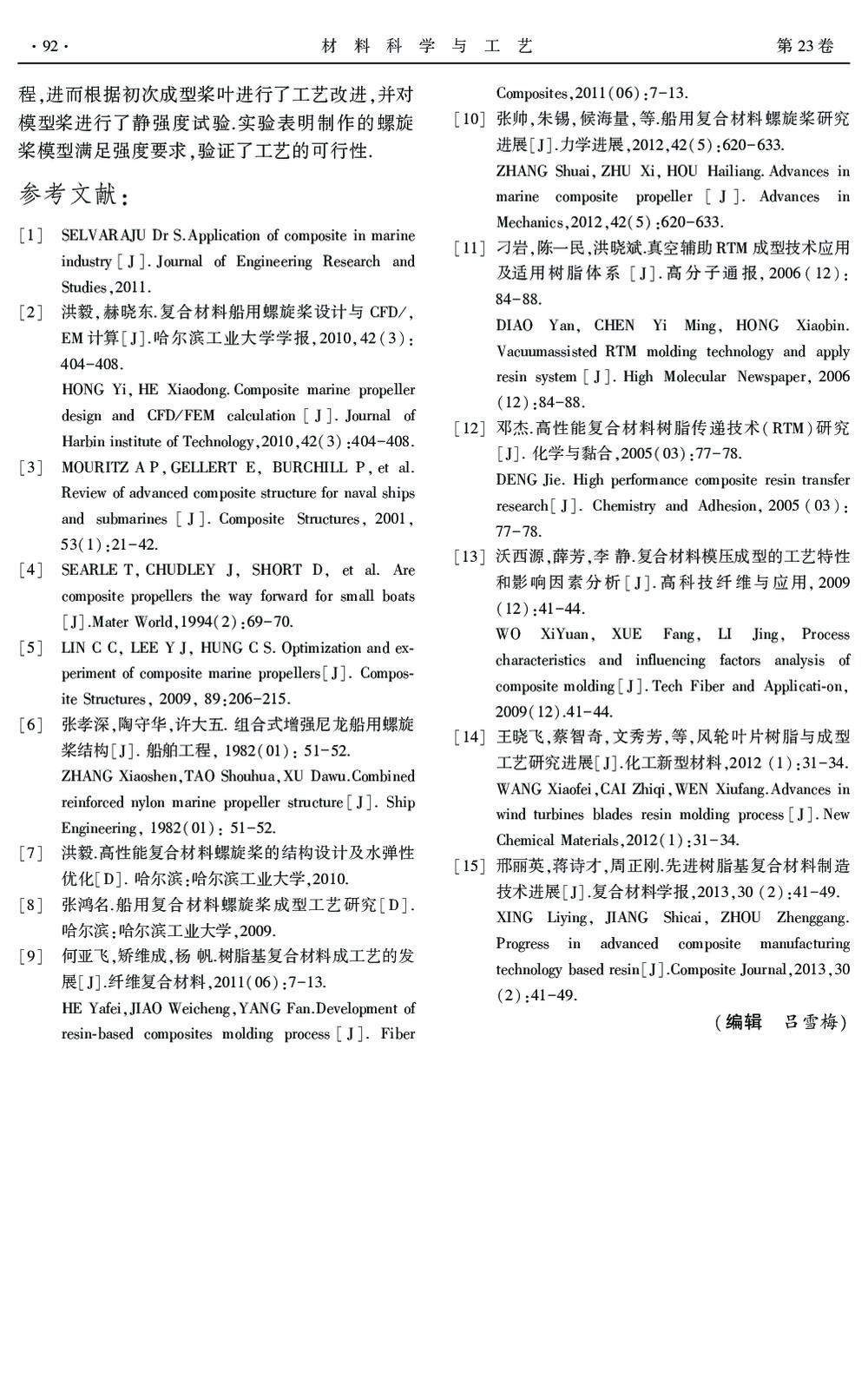
已阅读完毕,您还可以下载文档进行保存
- 1、本文档共6页,内容下载后可编辑。
- 2、本文档内容版权归属内容提供方,所产生的收益全部归内容提供方所有。如果您对本文有版权争议,可选择认领。
- 3、本文档由用户上传,本站不保证质量和数量令人满意,可能有诸多瑕疵,付费之前,请仔细先通过免费阅读内容等途径辨别内容交易风险。如存在严重挂羊头卖狗肉之情形,可联系本站下载客服投诉处理。
第23卷第6期2015年12月材料科学与工艺MATERIALSSCIENCE&TECHNOLOGYllVol23lll6Dec.2015doi:10.11951/j.issn.1005-0299.20150616复合材料螺旋桨RTM成型工艺研究杨文志,朱锡,陈悦,裴秋秋(海军工程大学舰船工程系,武汉430033)摘要:为开展复合材料螺旋桨成型工艺的研究,分析了不同成型工艺的特点,提出采用树脂传递模塑成型技术(RTM)制作螺旋桨模型,制订了模具制备方案、纤维剪裁和铺层实施方案以及RTM工艺流程,制作了螺旋桨模型,并提出了工艺改进方案,进而开展了螺旋桨模型的强度试验.强度试验结果显示:随着载荷的增加,各测点处的应变值均呈线性增长,当加载到8kN时各测点应变均在弹性范围内,桨叶未发生破坏.研究表明:采用本文制定的模具制备方案,特别是针对桨叶纤维布剪裁、铺层的难题提出的适合复杂型线纤维布剪裁和铺层的实施方案,用于成型夹芯复合材料螺旋桨模型可以满足预期强度要求,验证了本文工艺的可行性.关键词:复合材料;螺旋桨;RTM;成型工艺;强度中图分类号:U668.3文献标志码:A文章编号:1005-0299(2015)06-0087-06ResearchonRTMmoldingprocessofcompositepropellerYANGWenzhi,ZHUXi,CHENYue,PEIQiuqiu(DepartmentofNavalArchitectureEngineering,NavalUniversityofEngineering,Wuhan430033,China)Abstract:Tostudycompositepropellermoldingprocess,weanalyzethecharacteristicsofdifferentmoldingprocessandproposetothepropellermodelbyusingRTMtechnology.Then,wedevelopprogramsformoldpreparation,fibercutandplyembodimentandRTMprocess.Andweproducedapropellermodelandthenlaunchedastrengthtestpropellermodels.Themechanicaltestresultsshowthat,thereisalinearincreaseforthestrainwiththeloadincreaseandbladeisnotdamagedwhen8kNloadwasexploited.Theuseofmoldpreparationprogramdeveloped,especiallyforproblembladecutfibercloth,pliesofembodimentforcomplextypewireclothcutandlaminateformoldingsandwichcompositepropellermodeltomeettheexpectedstrengthrequirementstoverifythefeasibilityoftheprocessherein.Keywords:composite;propeller;RTM;moldingprocess;strength收稿日期:2015-01-22.基金项目:国防“十二五”预研基金资助项目(4010405030101).作者简介:杨文志—(1991),男,硕士研究生;朱锡—(1961),男,教授,博士生导师.通信作者:朱锡⁃,Email:zhuxi816@163.com.复合材料螺旋桨因具有低噪音、轻质、高效、易维修等特性,使得各国研究人员将目光投向了复合材料螺旋桨的实船应用.近年来,随着各国对复合材料研究的深入,复合材料螺旋桨的应用价值也大大体现.成型工艺是复合材料螺旋桨应用的关键,为加快复合材料螺旋桨在船舶上的实际应用,研究复合材料螺旋桨的成型工艺技术具有重要意义[1-2].目前,针对复合材料螺旋桨成型工艺,国内外学者已进行了一些有意义的研究工作.19纪60年代苏联学者第一次使用手糊方式成型了直径2m的复合材料螺旋桨桨叶[3];SEARLE[4]采用RTM技术和真空融合工艺制作了复合材料螺旋桨桨叶;LIN[5]等采用制作铝合金桨叶阴模和阳模的RTM技术实现了小直径大侧斜复合材料螺旋桨的制作;张孝深等[6]采用分叶注射整体成型技术制作了拖船、冷藏船和渔船船用复合材料螺旋桨;洪毅[7]在其博士论文中指出,考虑到螺旋桨这种复杂型面的三维结构,由于要满足设计的水动力性能要求,且对其不规则的几何外形有较高的尺寸精度要求,以及欲制备螺旋桨的几何尺寸较小,故选取模压成型工艺制备了碳纤维复合材料螺旋桨,其中模具选用玻璃钢材料.并对已制备的复合材料螺旋桨进行了型面分析检测、质量测试分析以及噪音测试分析.在此基础上,张鸿名[8]采用RTM工艺制备了高质量的复合材料螺旋桨,并对成型的螺旋桨进行了三维型值扫描测试、质量测试和水下噪音性能测试.但上述学者的研究均未阐明生产复合材料螺旋桨时的工艺流程以及成型桨叶的强度问题.现有的RTM技术在成型复合材料螺旋桨时也存在诸多问题,主要表现在由于桨叶几何尺寸的复杂性,难以保证剪裁、铺设纤维布的型线精度,进而影响产品的尺寸型线;树脂注入过程中,由于注射压力较大,在高压下改变原来的铺层角度,影响成型桨叶的强度.为此,本文对不同成型工艺进行比较,制订了模具制备方案,针对上述问题进一步完善了纤维剪裁和铺层实施方案以及RTM工艺流程,制作了夹芯复合材料螺旋桨模型,并提出了工艺改进方案,对成型桨叶进行了静强度试验.1成型工艺1.1工艺的比较和选取可用于复合材料成形的工艺较多,主要有手糊成型工艺、喷射成型工艺、模压成型工艺和RTM成型技术等几大类[9-10].不同成型工艺对增强纤维和树脂类型的要求不同,其所能达到的结构尺寸稳定程度差异也较大,因此,需根据桨叶结构的特点,选择合适的成型工艺.手糊成型是复合材料工业最早使用的一种工艺方法,主要特点在于手工操作、开模成型、成型工艺中树脂和增强纤维需完全暴露于操作者和环境中.采用手糊成型工艺加工夹芯复合材料螺旋桨模型,制作成本相对较低,但尺寸精度和稳定性难以保证,特别是对复杂气动外型和具有夹芯结构复合材料螺旋桨叶片来说,往往需粘接等第二次加工,粘接工艺需要粘接平台或型架以确保粘接面的贴合,生产工艺会更加复杂和困难.对于喷射成型工艺,在成型制品时多采用短纤维,桨叶的强度和刚度无法保证,且不能根据需要调整纤维结构.桨叶纤维含量、均匀程度等很大程度上取决于操作工人的技术水平,可控性较差,而由于需要雾化和分散,原材料的损耗较大.模压成型过程中预浸料的流动、充模、固化反应速度都与温度有密切关系,由于大型薄壁、形状复杂的复合材料螺旋桨制品温度不易控制,温度过高或过低都将严重影响成型桨叶的性能,且本文欲制作的螺旋桨模型尺寸较大,模压成型模具设计与制造较为复杂,因此,所需成本较高,故不选取模压成型工艺.RTM工艺的基本原理如图1所示,工艺过程包括①:预成型坯的加工②;树脂的注入和固化.由于这两步可分开进行,所以RTM工艺具有高度的灵活性和组合性,便于实现“材料设计”.RTM成型工艺技术是一种闭模成型技术,具有材料组分可精确控制、制件空隙率低、吸水率小、工艺过程简单等优点,是当今发展先进低成本制造复合材料工艺的一种优选途径[11-15].国内、外已有RTM工艺生产复合材料螺旋桨的实例,故本文复合材料螺旋桨采用RTM工艺.预成型胚置入模具注入树脂固化成型脱膜图1RTM成型工艺流程图1.2成型前准备1.2.1原材料复合材料螺旋桨桨叶半径为475mm,原材料厂家为中材科技股份有限公司,织物类型为Sw220高强玻璃纤维,主要材料参数为E11=E22=18.22GPa,E33=6GPa,ν12=0.12,ν13=0.3,ν23=0.3,G12=G13=6.75GPa,G23=3GPa.芯材采用H100泡沫,密度为100kG/m3,耐压强度2MPa,拉伸强度3MPa,厚12mm、质量79.2g,为使树脂能够浸透泡沫,在泡沫上采用2cm间隔、3mm穿孔,基体树脂采用430LV乙烯基酯树脂、固化剂为LC低放热型固化剂.1.2.2桨叶结构形式及铺层方式为了减轻桨叶质量、吸声降噪、减少热应力变形、防止纤维布太厚导致的树脂浸渍不佳等因素,提出采用具有夹芯结构的复合材料螺旋桨桨叶结构形式.根据仿真计算结果,纤维布采用±45°与0°正交纤维布混合铺层,由叶面开始采用±45°铺层,约3.2mm厚,铺设10层,0°纤维布约4.8mm,共计15层,纤维布的铺层方式为由表及里,采用对称铺层的方式.具体铺布顺序为表面毡一层{±455/015/C6}s.1.3成型工艺流程工艺流程如图2所示,主要包括两个部分:模具的制作和桨叶的成型.桨叶成型的主要步骤包括:喷涂胶衣、铺布(包括泡沫芯材的放置)、合模、注料成型、后固化、脱模.·88·材料科学与工艺第23卷铝制桨叶制作模具制备原材料桨叶成型纤维布剪裁脱膜图2桨叶成型过程1.3.1模具的制作由于制作的模具要满足合模、注胶、开模等工艺环节的使用要求,因此,模具的设计与制造也是复合材料螺旋桨成型的关键.本文将制备的模具尺寸较大,采用金属模具成本较高,故采用玻璃钢模具.首先采用三维数控机加工铝质螺旋桨桨叶,进而翻制上下玻璃钢模具(下玻璃钢模具如图3所示).结合螺旋桨模具的特点,预置进料口A、排气口B、C、D、E.树脂注入时,由A注入到模腔,当B、C、D、E的4个出料口均有树脂流出且无气泡时则表示树脂已充满整个模腔.特别指出的是模具在成型过程中常会由于温度升高产生热应力造成模具变形,进而对成品形状产生影响,因此,上、下玻璃钢模具都应增加金属加强钢框架.1.3.2纤维布的剪裁由于桨叶几何尺寸的复杂性,常规的剪裁方法难以保证型线精度,结合生产实际,本文在剪裁纤维布时首先在铝制桨叶上分别绘制出4、5、7、9、11、13、15、18mm厚度处等厚线,再按相应等厚线的轮廓制好裁布样板,进而将裁布样板置于纤维布下进行纤维布的剪裁,裁布过程如图4所示.(a)铝制桨叶(b)下模(c)金属加强钢框架图3制备模具图4剪裁纤维布1.3.3喷涂胶衣喷涂胶衣之前为方便脱模,模具上应喷涂脱模剂,待脱模剂干透后进行胶衣的喷涂.胶衣配方原则为胶衣凝胶时间应大于喷涂时间,本次成型的产品调节凝胶时间为10~15min较适宜.喷涂时,压力控制在2~3kg/cm2.为防止注射成型时树脂从孔隙中被挤压至胶衣与模具之间,导致胶衣串胶喷涂过程中应注意边角要反复喷涂,以确保各处胶衣都喷涂均匀覆盖好.不需喷涂胶衣的位置应使用覆盖物覆盖,待喷涂完胶衣后应立即将覆盖物撕掉,撕扯时应向外撕,避免损坏胶衣层.1.3.4夹芯泡沫及纤维布的铺放待胶衣用手摸还能有少量粘黏物粘在手上,但胶衣基本己干固时,先铺上一层表面毡再铺布,为了方便以后脱模第一层布应压住排气口.铺布时按铝制桨叶上各个等厚线轮廓裁剪纤维布的顺序进行铺放,不同厚度处按2~3层纤维布过渡.具体铺层顺序详见前述铺层顺序,铺完下铺层后,将修好线型的泡沫置于纤维上,根据连接键槽处定位,再按反序铺好上铺层纤维布.上模层最后3层纤维铺敷于上模具中,各纤维层喷涂适量3M胶,并放置若干树脂钉将铺层进行固定,以避免铺层在树脂注入时发生错动.布层铺完后,用棉布蘸上脱模剂对四周进行清洁,注意不可用丙酮擦洗,丙酮会破坏模具胶衣层,特别是要将密封带纤维清理干净,避免存在密封性不好等问题.1.3.5合模、注射成型将布层铺好后,合上模具上紧所有螺丝.合模时应避免纤维布滑移,导致上、下模合模时产生夹缝.注射成型前应先将鞘钉打好脱模蜡.进行注射·98·第6期杨文志,等:复合材料螺旋桨RTM成型工艺研究时,将固化剂对应阀门打至90°(关回流),升压至100Psi,再将树脂阀打至90°(关回流),调节压力至20Psi附近.此时应注意注射第一枪可能混合不均匀,应将其打在废料缸中,然后喷出适宜量的料在薄膜中进行模拟凝胶试验,最佳凝胶时间应比注射时间延长10~20min.注射过程中各排气口在空气排尽后,应用鞘钉堵上,最后1~2个排气口应延长一定的排气时间,保证将气泡排尽.注射完成后应打开枪中丙酮开关立即洗枪.完成整个注射过程后,应将RTM成型注射机各阀都卸压,包括丙酮缸中安全阀卸压.开树脂、固化剂回流阀,将管路中残留树脂、固化剂回流,用丙酮回流清洗和注射即可清洗树脂回流管路与注射管路.待树脂刚凝胶时应将各进出料口处残留树脂清理干净,并拔出鞘钉,即成型完成.1.3.6初次成型桨叶桨叶成型完成后,连同模具于常温下放置15~20min进行固化,固化后在升温℃70~90固化3~4h,进行后固化处理.后固化处理后将模具常温下放置1~2d即可脱模.由图5可以看到,首次成型桨叶出现白斑、溢胶,局部有气泡,根部出现树脂聚集等问题.(a)气泡(b)树脂聚集(c)白斑(d)树脂溢出图5初次成型桨叶1.4工艺改进分析初次成型桨叶出现的问题,根据工程实际经验纯纤维布制品成型厚度在4~6mm可保证树脂浸透良好,而本次复合材料桨叶表层玻璃钢厚度均在8mm或以上,成型件较厚,势必会导致树脂浸透不完全出现白斑.为防止制品制作时由于纤维布太厚造成树脂浸透不完全,分别在叶背叶面8mm纤维布厚处中间夹两层夹芯毡,2层夹芯毡厚度约1mm.由于加入夹心毡导致厚度增加,为使纤维布厚度不变,将芯材泡沫上下打磨1mm.分析出现溢胶现象原因,认为主要是由于使用密封圈进行压力保压,保压时间有限,固化剂固化时间太长导致有空气渗透进去,为防止出现溢胶,将第一次使用的LC低放热固化剂加入5%的M50固化剂,LC低放热固化剂的固化时间在2h左右,加入5%的M50固化剂后固化时间在1h左右.初次成型桨叶叶面比叶背成型的好,几乎无溢胶白斑现象,初次成型桨叶时上叶面用烤灯加热,温度升高使叶面树脂浸透的较好.在第二个桨叶的成型制作时,应将两面都进行烘烤.对根部出现树脂聚集现象,分析产生的原因可能是合模时根部纤维布产生松动收缩,导致根部缺少纤维产生树脂聚集,下次合模时应将根部纤维压实,喷涂适量3M胶使纤维布粘接固定,合模时应小心,防止纤维布产生错动.将上述问题改进后进行复合材料桨叶的第二次成型制作.由图6可以看出,第二次成型的桨叶比先前成型的桨叶有很大改善,无明显溢胶、白斑,树脂浸透良好、表面平滑光顺、无刮痕、裂缝、树脂淤积、缺胶、分层等现象.图6改进后的桨叶2静强度试验2.1测点布置及加载方式测点布置如图7所示,其中叶根处布置1#、2#、3#、8#、9#的5处测点,在r/R=0.6半径处的导边和随边处布置了4#、7#、10#的3处测点,泡沫夹芯与纤维布交接处布置了5#、6#两处测点,方向均沿桨叶的径向.夹芯结构复合材料螺旋桨桨叶类似于悬臂梁结构,在水动压力载荷的作用下叶根处产生较大应力.因而依据桨叶对叶根处的应力等效原则,通过·09·材料科学与工艺第23卷有限元加载试算,将由面元法计算得到的设计工况下桨叶的水动力载荷等效为7.5kN的集中力载荷,集中力的加载位置选择在叶面的r/R=0.75半径处.同时,为了全面反应实验结果,将该半径处的弦长等分为7份,并选取距导边2/7、3/7和4/7处的3个位置作为加载点进行试验加载.加载点2加载点3加载点11#2#3#4#5#6#7#8#9#10#(a)叶面(b)叶背图7测点布置示意图试验地点为海军工程大学结构与材料试验室,试验设备为电子万能试验机,加载方式为垂直加载,加载速度1mm/s.试验实施过程如图8所示.试验从1kN开始加载,分8次逐次递增加载到8kN.加载过程中需要注意的是,试验开始时首先应缓慢加载、卸载,以释放桨叶内部的残余应力.图8试验实施过程2.2试验结果为了直观地反应实验结果,图9~11分别给出了加载点1~3位置下强度试验所测各测点应变曲线.43210-1-2-3-4123456789载荷/kN应变/10-31#2#3#4#5#6#7#8#9#10#图9加载点1对应的各测点试验结果43210-1-2-3123456789载荷/kN1#2#3#4#5#6#7#8#9#10#应变/10-3图10加载点2对应的各测点试验结果123456789载荷/kN1#2#3#4#5#6#7#8#9#10#应变/10-33210-1-2-3图11加载点3对应的各测点试验结果由图9~11可以看出,夹芯结构复合材料螺旋桨在受静载荷的作用下各测点处应变的绝对值均随着载荷的增加呈线性增长,当最大载荷加载到8kN时各测点应变均在弹性范围内,桨叶也未发生破坏,充分验证了采用RTM工艺可有效保证夹芯结构复合材料螺旋桨强度.3结论本文提出了一种具有夹芯结构的新的复合材料螺旋桨桨叶的结构形式,针对螺旋桨实际生产工艺中的难题提出了适用于复杂形状制品纤维布的剪裁方法并提出喷涂3M胶、预置树脂钉固定铺层的方法,制订了模具制备方案、RTM工艺流·19·第6期杨文志,等:复合材料螺旋桨RTM成型工艺研究程,进而根据初次成型桨叶进行了工艺改进,并对模型桨进行了静强度试验.实验表明制作的螺旋桨模型满足强度要求,验证了工艺的可行性.参考文献:[1]SELVARAJUDrS.Applicationofcompositeinmarineindustry[J].JournalofEngineeringResearchandStudies,2011.[2]洪毅,赫晓东.复合材料船用螺旋桨设计与CFD/,EM计算[J].哈尔滨工业大学学报,2010,42(3):404-408.HONGYi,HEXiaodong.CompositemarinepropellerdesignandCFD/FEMcalculation[J].JournalofHarbininstituteofTechnology,2010,42(3):404-408.[3]MOURITZAP,GELLERTE,BURCHILLP,etal.Reviewofadvancedcompositestructurefornavalshipsandsubmarines[J].CompositeStructures,2001,53(1):21-42.[4]SEARLET,CHUDLEYJ,SHORTD,etal.Arecompositepropellersthewayforwardforsmallboats[J].MaterWorld,1994(2):69-70.[5]LINCC,LEEYJ,HUNGCS.⁃Optimizationandexperimentofcompositemarinepropellers[J].⁃CompositeStructures,2009,89:206-215.[6]张孝深,陶守华,许大五.组合式增强尼龙船用螺旋桨结构[J].船舶工程,1982(01):51-52.ZHANGXiaoshen,TAOShouhua,XUDawu.Combinedreinforcednylonmarinepropellerstructure[J].ShipEngineering,1982(01):51-52.[7]洪毅.高性能复合材料螺旋桨的结构设计及水弹性优化[D].哈尔滨:哈尔滨工业大学,2010.[8]张鸿名.船用复合材料螺旋桨成型工艺研究[D].哈尔滨:哈尔滨工业大学,2009.[9]何亚飞,矫维成,杨帆.树脂基复合材料成工艺的发展[J].纤维复合材料,2011(06):7-13.HEYafei,JIAOWeicheng,YANGFan.Developmentof⁃resinbasedcompositesmoldingprocess[J].FiberComposites,2011(06):7-13.[10]张帅,朱锡,候海量,等.船用复合材料螺旋桨研究进展[J].力学进展,2012,42(5):620-633.ZHANGShuai,ZHUXi,HOUHailiang.Advancesinmarinecompositepropeller[J].AdvancesinMechanics,2012,42(5):620-633.[11]刁岩,陈一民,洪晓斌.真空辅助RTM成型技术应用及适用树脂体系[J].高分子通报,2006(12):84-88.DIAOYan,CHENYiMing,HONGXiaobin.VacuumassistedRTMmoldingtechnologyandapplyresinsystem[J].HighMolecularNewspaper,2006(12):84-88.[12]邓杰.高性能复合材料树脂传递技术(RTM)研究[J].化学与黏合,2005(03):77-78.DENGJie.Highperformancecompositeresintransferresearch[J].ChemistryandAdhesion,2005(03):77-78.[13]沃西源,薛芳,李静.复合材料模压成型的工艺特性和影响因素分析[J].高科技纤维与应用,2009(12):41-44.WOXiYuan,XUEFang,LIJing,Processcharacteristicsandinfluencingfactorsanalysisofcompositemolding[J].TechFiber⁃andApplication,2009(12).41-44.[14]王晓飞,蔡智奇,文秀芳,等,风轮叶片树脂与成型工艺研究进展[J].化工新型材料,2012(1):31-34.WANGXiaofei,CAIZhiqi,WENXiufang.Advancesinwindturbinesbladesresinmoldingprocess[J].NewChemicalMaterials,2012(1):31-34.[15]邢丽英,蒋诗才,周正刚.先进树脂基复合材料制造技术进展[J].复合材料学报,2013,30(2):41-49.XINGLiying,JIANGShicai,ZHOUZhenggang.Progressinadvancedcompositemanufacturingtechnologybasedresin[J].CompositeJournal,2013,30(2):41-49.(编辑吕雪梅)·29·材料科学与工艺第23卷
您可能关注的文档
- “离位”增韧复合材料准静态压入损伤特性研究.pdf
- “神舟七号”飞船舱外航天服防护头盔组件的研制.pdf
- “十二五”复合材料发展重点和方向解读.pdf
- “珠串”堆叠超结构的介孔铁酸锌的制备与表征.pdf
- (001)应变对正交相Ca2 P0.25 Si0.75能带结构及光学性质的影响.pdf
- 0.8设计系数用X80管线钢在近中性pH溶液中的应力腐蚀开裂行为.pdf
- 0.20mm CGO硅钢高温退火Goss晶粒起源及异常长大行为研究.pdf
- 0Cr16Ni5Mo低碳马氏体不锈钢的热变形行为及其热加工图.pdf
- 0Cr17Ni4Cu4Nb钢制螺钉断裂原因分析.pdf
- 1.5MW风机叶片模具加热工艺研究与技术创新.pdf
- 1.5MW风机叶片VARI工艺模拟分析及验证.pdf
- 2.5维机织复合材料低速冲击性能研究.pdf
- 2.25Cr-1Mo钢后续热处理中的磷偏聚行为.pdf
- 2A50锻铝三点弯曲试验与高分辨率CT成像分析.pdf
- 2A12与2A11铝合金超声波焊接工艺与组织研究.pdf
- 2MW风机复合材料叶片材料及工艺研究.pdf
- 3Cr2W8V模具钢激光表面相变硬化层性能的研究.pdf
- 3D打印技术及先进应用研究进展.pdf
- 3D打印技术研究现状和关键技术.pdf
- 5%鱼藤酮悬浮剂的研制.pdf

- 乘风破浪
- 该用户很懒,什么也没介绍
相关文档
- “离位”增韧复合材料准静态压入损伤特性研究.pdf2021-11-235页
- “神舟七号”飞船舱外航天服防护头盔组件的研制.pdf2021-11-233页
- “十二五”复合材料发展重点和方向解读.pdf2021-11-232页
- “珠串”堆叠超结构的介孔铁酸锌的制备与表征.pdf2021-11-235页
- (001)应变对正交相Ca2 P0.25 Si0.75能带结构及光学性质的影响.pdf2021-11-236页
- 0.8设计系数用X80管线钢在近中性pH溶液中的应力腐蚀开裂行为.pdf2021-11-237页
- 0.20mm CGO硅钢高温退火Goss晶粒起源及异常长大行为研究.pdf2021-11-237页