- 文档大小:441.33 KB
- 文档格式:pdf
- 约 7页
- 2022-04-11 发布
- 举报
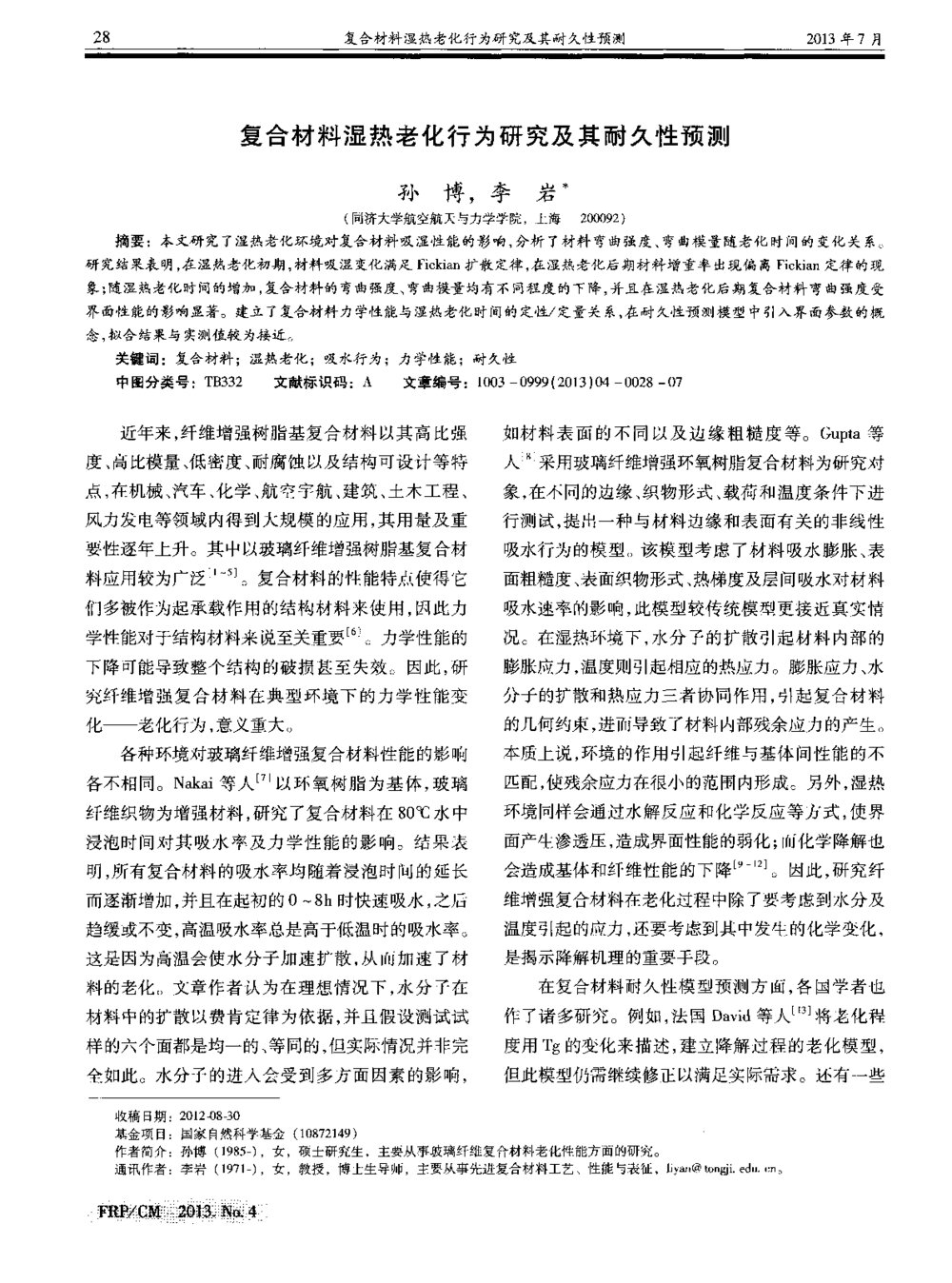
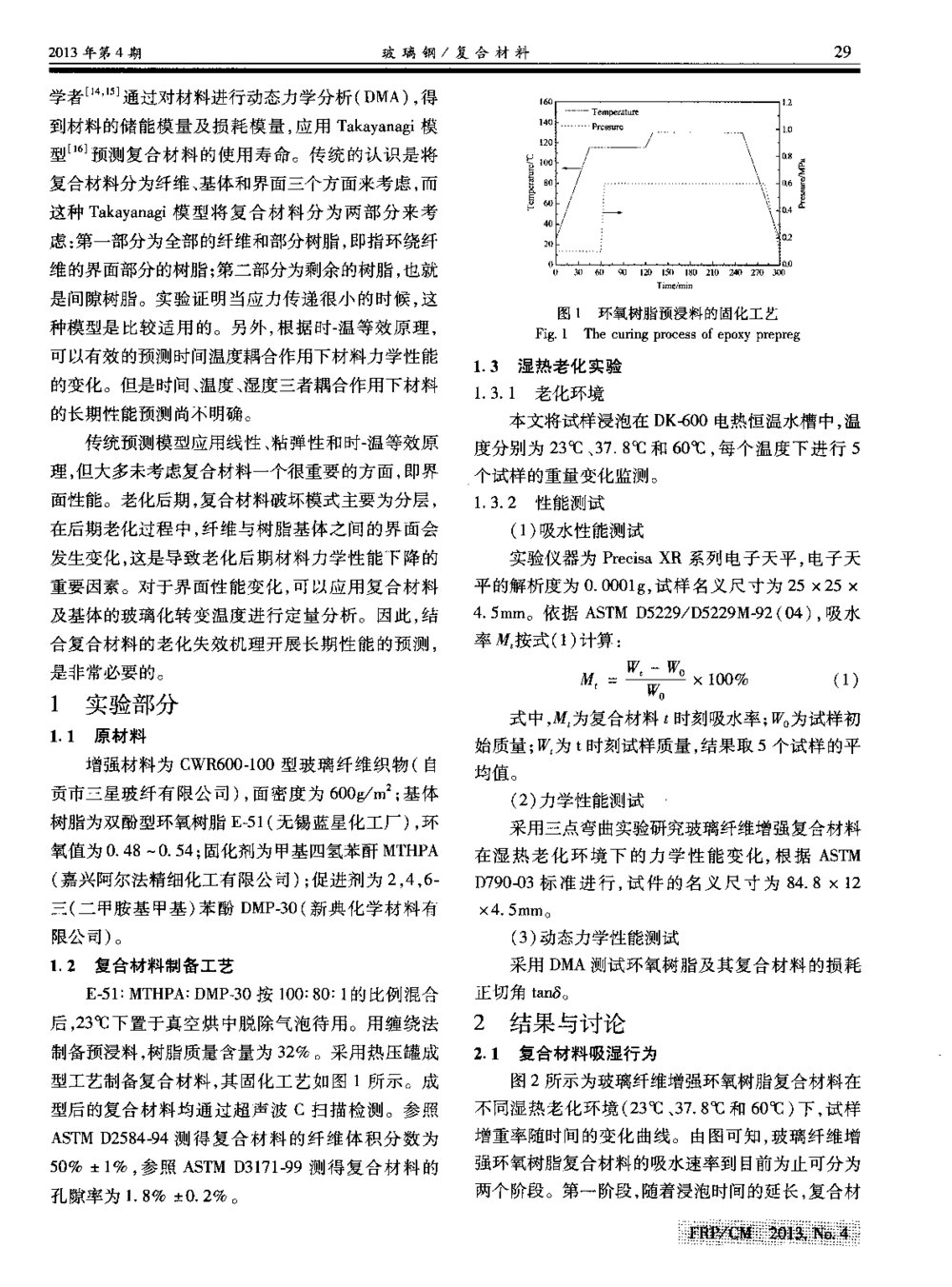
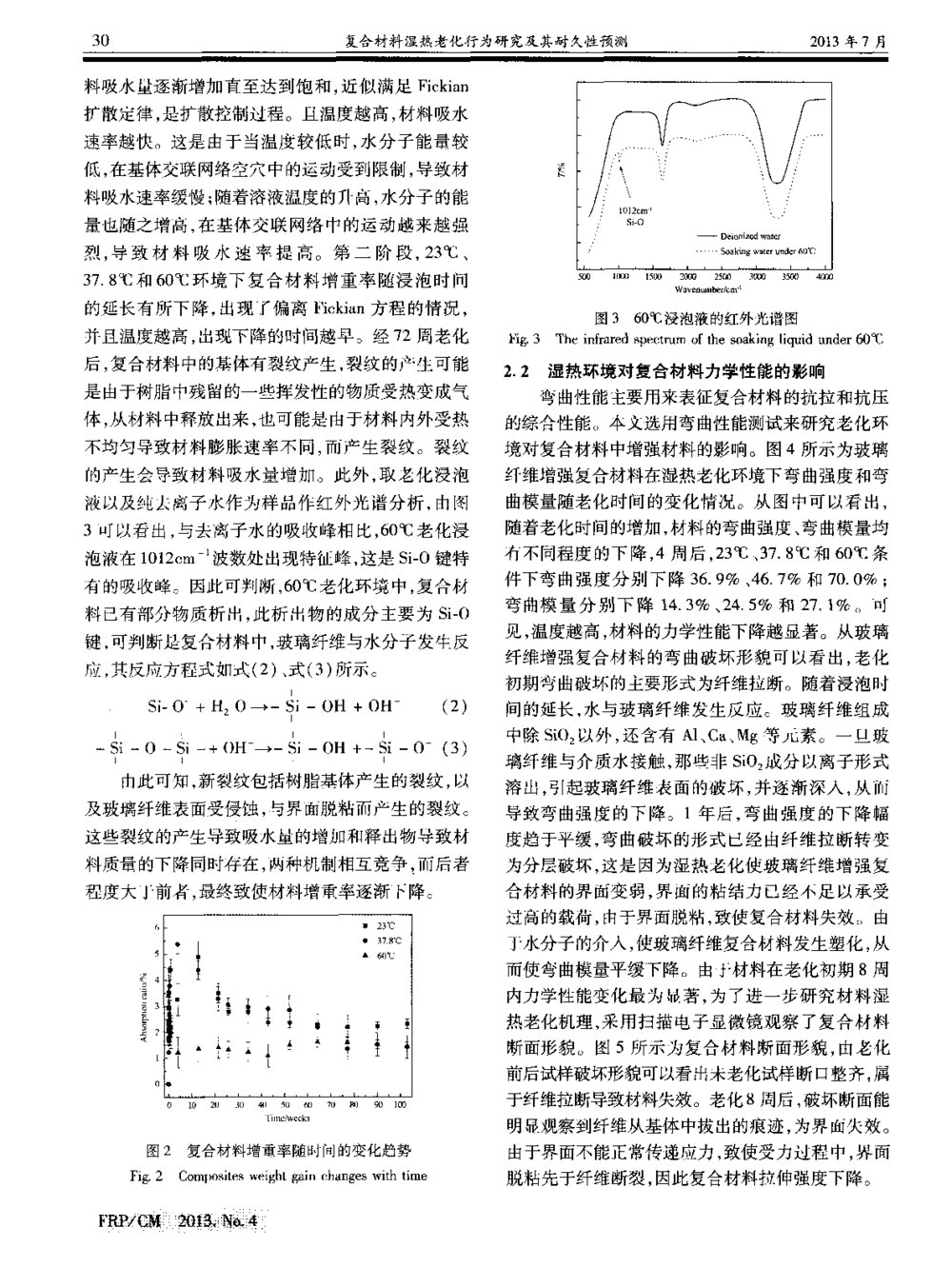
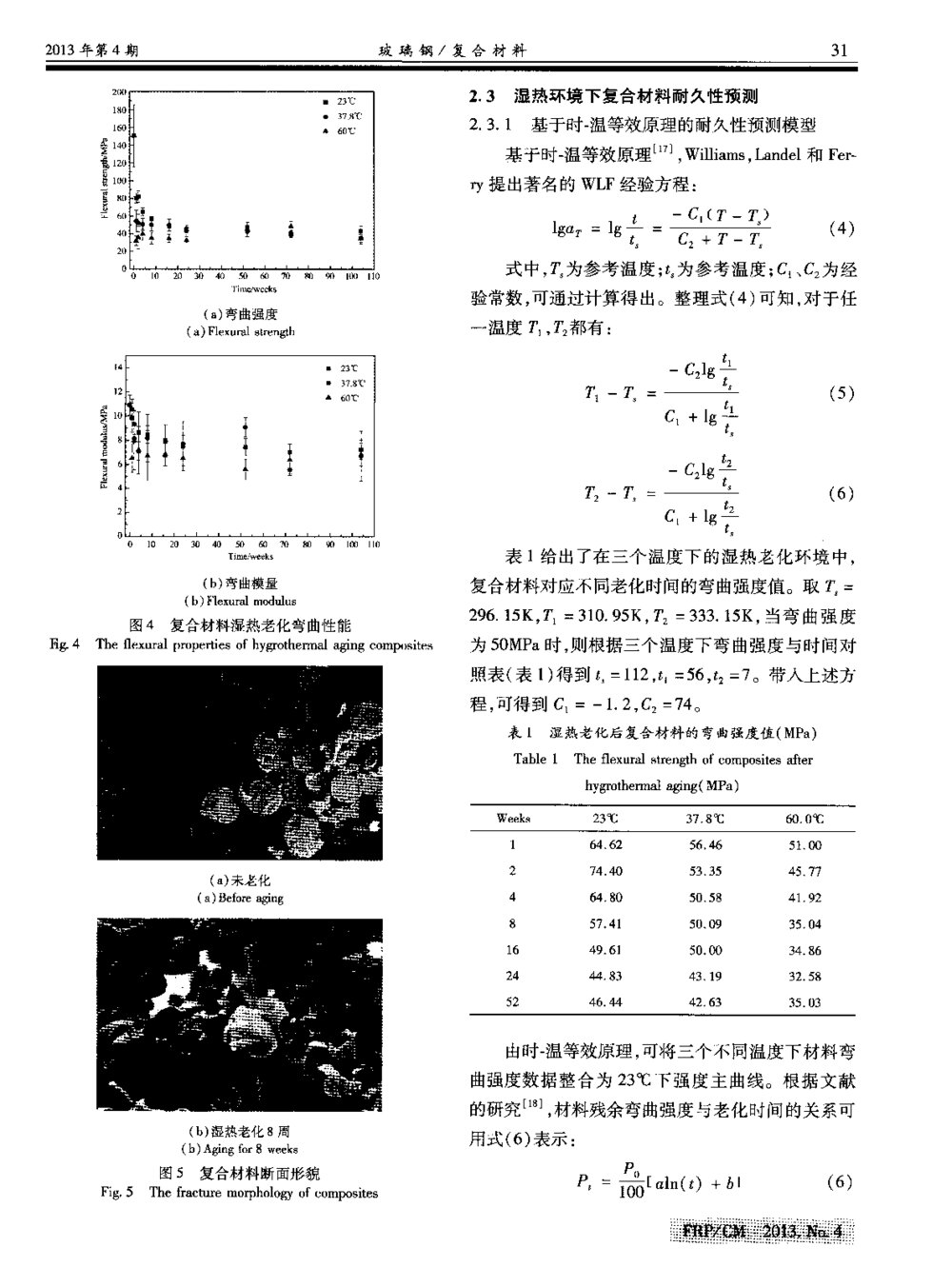
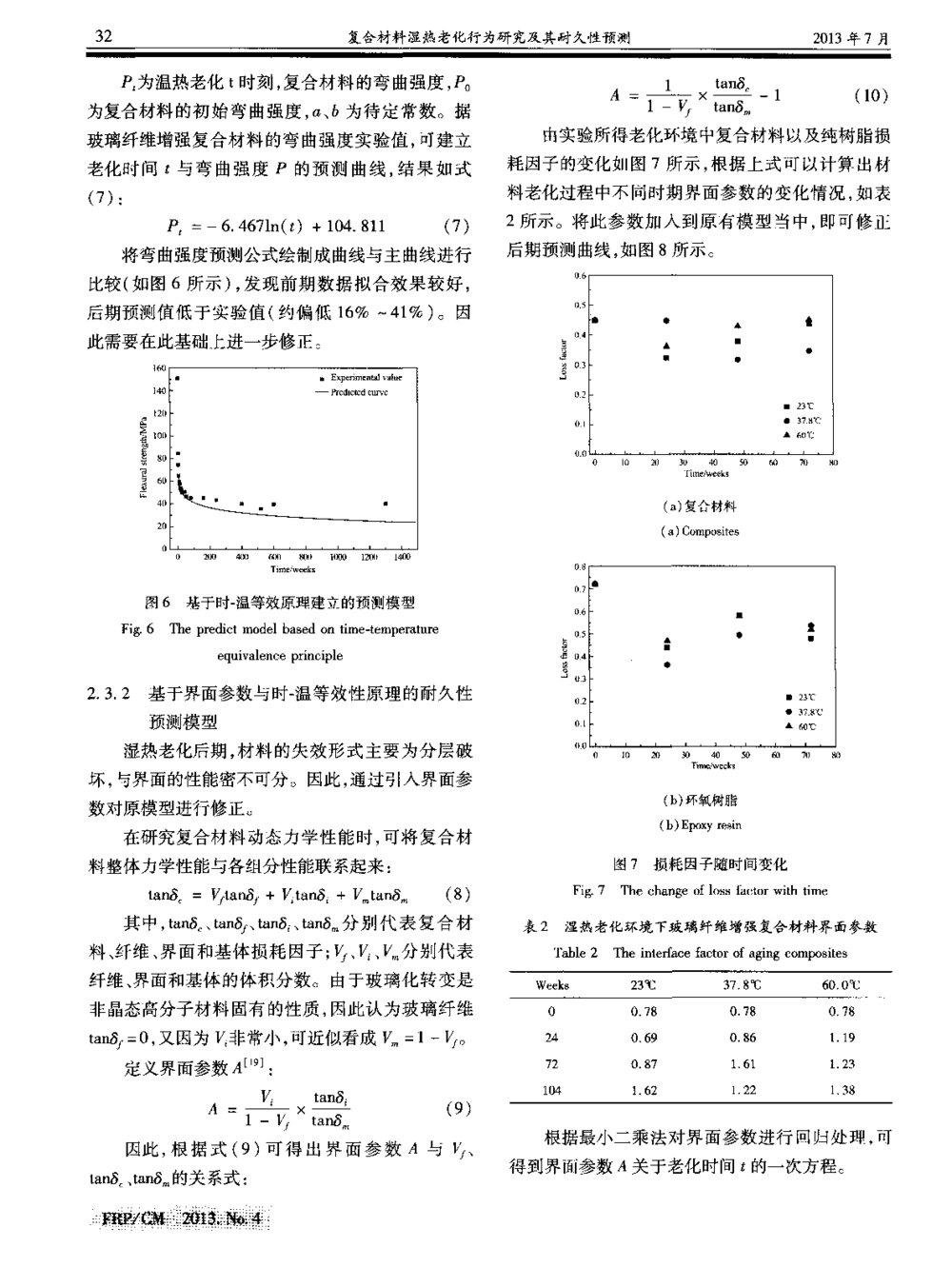
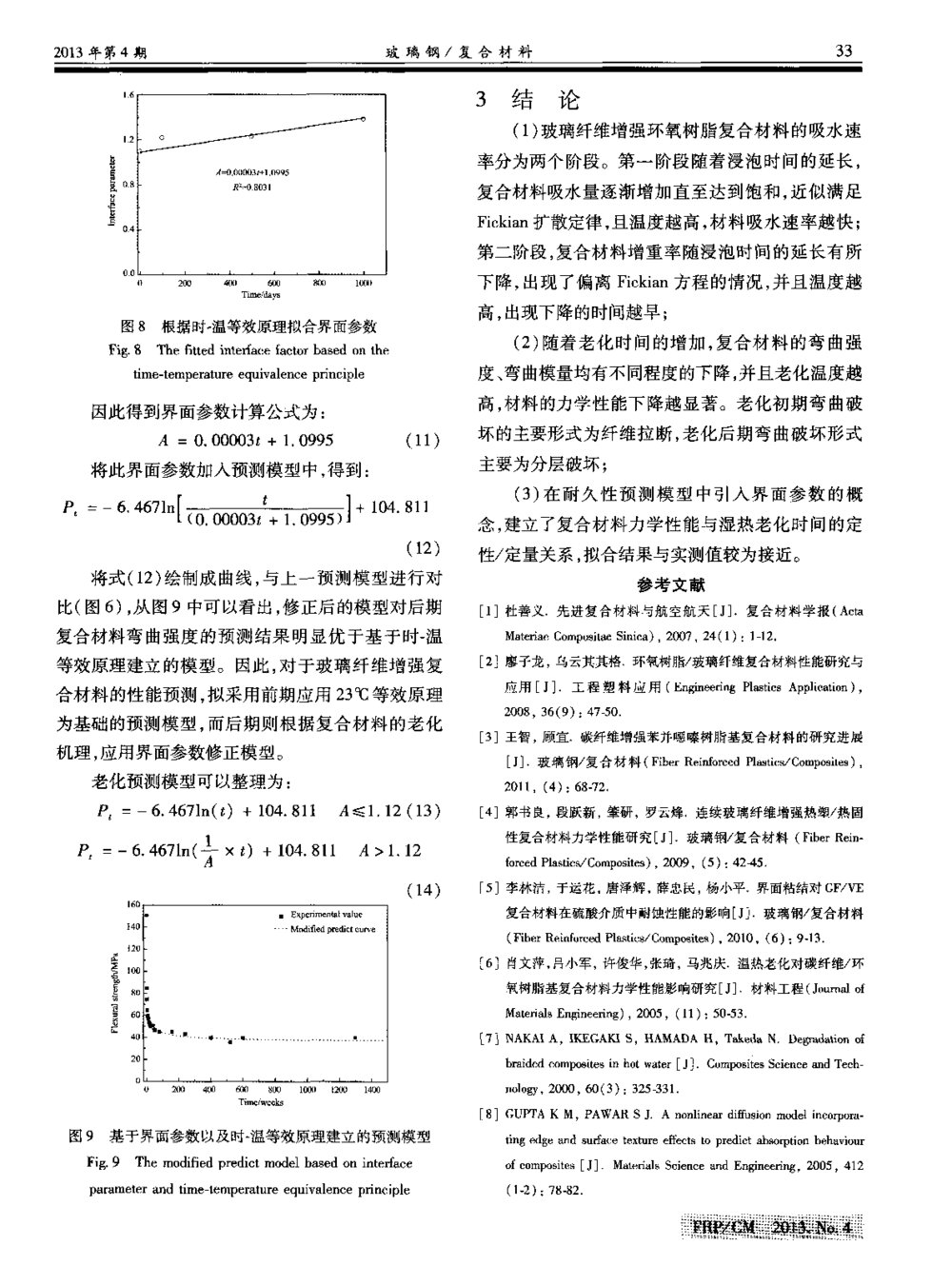
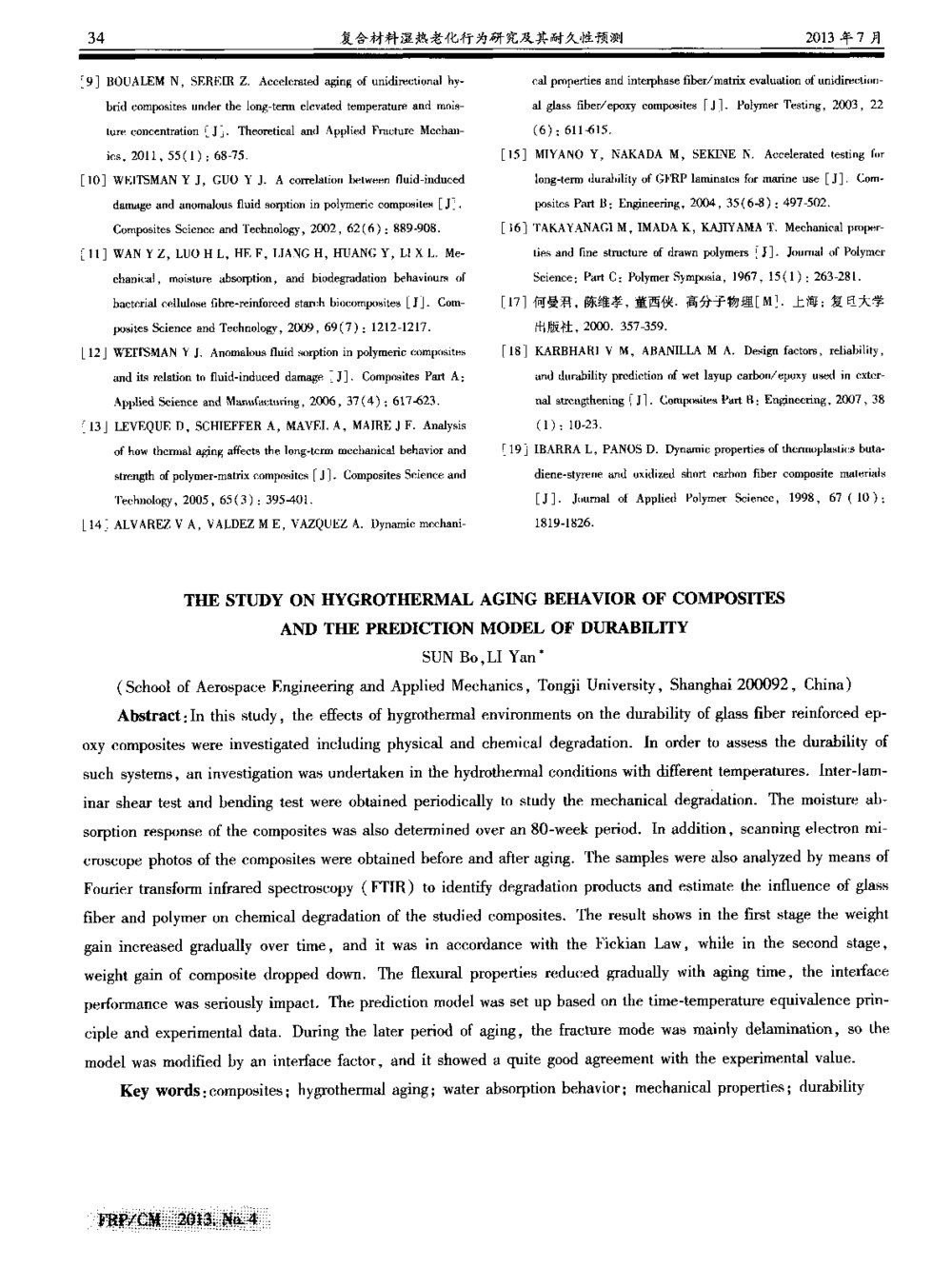
已阅读完毕,您还可以下载文档进行保存
- 1、本文档共7页,内容下载后可编辑。
- 2、本文档内容版权归属内容提供方,所产生的收益全部归内容提供方所有。如果您对本文有版权争议,可选择认领。
- 3、本文档由用户上传,本站不保证质量和数量令人满意,可能有诸多瑕疵,付费之前,请仔细先通过免费阅读内容等途径辨别内容交易风险。如存在严重挂羊头卖狗肉之情形,可联系本站下载客服投诉处理。
28 复合材料湿热老化行为研究及其耐久性预测 复合材料湿热老化行为研究及其耐久性预测 孙博,李岩 (同济大学航空航天与力学学院,上海200092) 摘要:本文研究了湿热老化环境对复合材料吸湿性能的影响,分析了材料弯曲强度、弯曲模量随老化时间的变化关系。 研究结果表明,在湿热老化初期,材料吸湿变化满足Fickian扩散定律,在湿热老化后期材料增重率出现偏离Fickian定律的现 象;随湿热老化时间的增加,复合材料的弯曲强度、弯曲模量均有不同程度的下降,并且在湿热老化后期复合材料弯曲强度受 界面性能的影响显著。建立了复合材料力学性能与湿热老化时间的定性/定量关系,在耐久性预测模型中引入界面参数的概 念,拟合结果与实测值较为接近。 关键词:复合材料;湿热老化;吸水行为;力学性能;耐久性 中图分类号:TB332 文献标识码:A ——— 文章编号:10030999(2013)04002807 近年来,纤维增强树脂基复合材料以其高比强 度、高比模量、低密度、耐腐蚀以及结构可设计等特 点,在机械、汽车、化学、航空宇航、建筑、土木工程、 风力发电等领域内得到大规模的应用,其用量及重 要性逐年上升。其中以玻璃纤维增强树脂基复合材 料应用较为广泛J。复合材料的性能特点使得它 们多被作为起承载作用的结构材料来使用,因此力 学性能对于结构材料来说至关重要』。力学性能的 下降可能导致整个结构的破损甚至失效。因此,研 究纤维增强复合材料在典型环境下的力学性能变—— 化老化行为,意义重大。 各种环境对玻璃纤维增强复合材料性能的影响 各不相同。Nakai等人以环氧树脂为基体,玻璃 ℃ 纤维织物为增强材料,研究了复合材料在8O水中 浸泡时间对其吸水率及力学性能的影响。结果表 明,所有复合材料的吸水率均随着浸泡时间的延长 而逐渐增加,并且在起初的0~8h时快速吸水,之后 趋缓或不变,高温吸水率总是高于低温时的吸水率。 这是因为高温会使水分子加速扩散,从而加速了材 料的老化。文章作者认为在理想情况下,水分子在 材料中的扩散以费肯定律为依据,并且假设测试试 样的六个面都是均一的、等同的,但实际情况并非完 全如此。水分子的进入会受到多方面因素的影响, 收稿日期: 基金项目: 作者简介: 通讯作者: 如材料表面的不同以及边缘粗糙度等。Gupta等 人采用玻璃纤维增强环氧树脂复合材料为研究对 象,在不同的边缘、织物形式、载荷和温度条件下进 行测试,提出一种与材料边缘和表面有关的非线性 吸水行为的模型。该模型考虑了材料吸水膨胀、表 面粗糙度、表面织物形式、热梯度及层间吸水对材料 吸水速率的影响,此模型较传统模型更接近真实情 况。在湿热环境下,水分子的扩散引起材料内部的 膨胀应力,温度则引起相应的热应力。膨胀应力、水 分子的扩散和热应力三者协同作用,引起复合材料 的几何约束,进而导致了材料内部残余应力的产生。 本质上说,环境的作用引起纤维与基体间性能的不 匹配,使残余应力在很小的范围内形成。另外,湿热 环境同样会通过水解反应和化学反应等方式,使界 面产生渗透压,造成界面性能的弱化;而化学降解也 会造成基体和纤维性能的下降 。因此,研究纤 维增强复合材料在老化过程中除了要考虑到水分及 温度引起的应力,还要考虑到其中发生的化学变化, 是揭示降解机理的重要手段。 在复合材料耐久性模型预测方面,各国学者也 作了诸多研究。例如,法国David等人¨ 将老化程 度用的变化来描述,建立降解过程的老化模型, 但此模型仍需继续修正以满足实际需求。还有一些 20128-30 国家自然科学基金(10872149) 孙博(1985一),女,硕士研究生,主要从事玻璃纤维复合材料老化性能方面的研究。 李岩(1971一),女,教授,博士生导师,主要从事先进复合材料工艺、性能与表征,liyan@tongji.edu.CR。 FRP/CN ̄i3No.4 2013年第4期 玻璃钢/复合材料 29学者¨ '通过对材料进行动态力学分析(DMA),得 到材料的储能模量及损耗模量,应用Takayanagi模 型_】刮预测复合材料的使用寿命。传统的认识是将 复合材料分为纤维、基体和界面三个方面来考虑,而 这种Takayanagi模型将复合材料分为两部分来考 虑:第一部分为全部的纤维和部分树脂,即指环绕纤 维的界面部分的树脂;第二部分为剩余的树脂,也就 是间隙树脂。实验证明当应力传递很小的时候,这 种模型是比较适用的。另外,根据时.温等效原理, 可以有效的预测时间温度耦合作用下材料力学性能 的变化。但是时间、温度、湿度三者耦合作用下材料 的长期性能预测尚不明确。 传统预测模型应用线性、粘弹性和时一温等效原 理,但大多未考虑复合材料一个很重要的方面,即界 面性能。老化后期,复合材料破坏模式主要为分层, 在后期老化过程中,纤维与树脂基体之间的界面会 发生变化,这是导致老化后期材料力学性能下降的 重要因素。对于界面性能变化,可以应用复合材料 及基体的玻璃化转变温度进行定量分析。因此,结 合复合材料的老化失效机理开展长期性能的预测, 是非常必要的。 1实验部分 1.1原材料 增强材料为CWR600.100型玻璃纤维织物(自 贡市三星玻纤有限公司),面密度为600g/m;基体 树脂为双酚型环氧树脂E一51(无锡蓝星化工厂),环 氧值为0.48~0.54;固化剂为甲基四氢苯酐MTHPA (嘉兴阿尔法精细化工有限公司);促进剂为2,4,6一 三(二甲胺基甲基)苯酚DMP-30(新典化学材料有 限公司)。 1.2复合材料制备工艺 E-51:MTHPA:DMP一30按100:80:1的比例混合 ℃ 后,23下置于真空烘中脱除气泡待用。用缠绕法 制备预浸料,树脂质量含量为32%。采用热压罐成 型工艺制备复合材料,其固化工艺如图1所示。成 型后的复合材料均通过超声波C扫描检测。参照 ASTMD2584-94测得复合材料的纤维体积分数为 50%± 1%,参照ASTMD3171-99测得复合材料的 孔隙率为1.8%± 0.2%。 图1环氧树脂预浸料的固化工艺 Fig.1Thecuringprocessofepoxyprepreg 1.3湿热老化实验 1.3.1老化环境 本文将试样浸泡在DK-600电热恒温水槽中,温 ℃ 度分别为23 ̄C、37.8 ̄C和60,每个温度下进行5 个试样的重量变化监测。 1.3.2性能测试 (1)吸水性能测试 实验仪器为PrecisaXR系列电子天平,电子天 平的解析度为0.0001g,试样名义尺寸为25×25× 4.5mm。依据ASTMD5229/D5229M_92(o4),吸水 率按式(1)计算: M:× 100% (1) =× (1) w0 式中,为复合材料t时刻吸水率;w0为试样初 始质量;为t时刻试样质量,结果取5个试样的平 均值。 (2)力学性能测试 采用三点弯曲实验研究玻璃纤维增强复合材料 在湿热老化环境下的力学性能变化,根据ASTM D790-03标准进行,试件的名义尺寸为84.8× 12× 4.5ramo (3)动态力学性能测试 采用DMA测试环氧树脂及其复合材料的损耗 正切角tant ̄。 2结果与讨论 2.1复合材料吸湿行为 图2所示为玻璃纤维增强环氧树脂复合材料在 不同湿热老化环境(23 ̄C、37.8 ̄C和60 ̄C)下,试样 增重率随时间的变化曲线。由图可知,玻璃纤维增 强环氧树脂复合材料的吸水速率到目前为止可分为 两个阶段。第一阶段,随着浸泡时间的延长,复合材 30 复合材料湿热老化行为研究及其耐久性预测 料吸水量逐渐增加直至达到饱和,近似满足Fickian 扩散定律,是扩散控制过程。且温度越高,材料吸水 速率越快。这是由于当温度较低时,水分子能量较 低,在基体交联网络空穴中的运动受到限制,导致材 料吸水速率缓慢;随着溶液温度的升高,水分子的能 量也随之增高,在基体交联网络中的运动越来越强 ℃ 烈,导致材料吸水速率提高。第二阶段,23、℃ 37.8和60 ̄C环境下复合材料增重率随浸泡时间 的延长有所下降,出现了偏离Fickian方程的情况, 并且温度越高,出现下降的时间越早。经72周老化 后,复合材料中的基体有裂纹产生,裂纹的产生可能 是由于树脂中残留的一些挥发性的物质受热变成气 体,从材料中释放出来,也可能是由于材料内外受热 不均匀导致材料膨胀速率不同,而产生裂纹。裂纹 的产生会导致材料吸水量增加。此外,取老化浸泡 液以及纯去离子水作为样品作红外光谱分析,由图℃ 3可以看出,与去离子水的吸收峰相比,60老化浸 — 泡液在lO12cm波数处出现特征峰,这是SiO键特 有的吸收峰。因此可判断,60 ̄C老化环境中,复合材 料已有部分物质析出,此析出物的成分主要为Si.0 键,可判断是复合材料中,玻璃纤维与水分子发生反 应,其反应方程式如式(2)、式(3)所示。 I Si.0一+H,0一一Si一0H+0H一 (2)一S. i一0一S, i一+OH一一一Si一0H+一S. i一0一(3) 由此可知,新裂纹包括树脂基体产生的裂纹,以 及玻璃纤维表面受侵蚀,与界面脱粘而产生的裂纹。 这些裂纹的产生导致吸水量的增加和释出物导致材 料质量的下降同时存在,两种机制相互竞争,而后者 程度大于前者,最终致使材料增重率逐渐下降。 图2复合材料增重率随时间的变化趋势 Fig.2Compositesweightgainchangeswithtime FRP/CM2013io. 图360oC浸泡液的红外光谱图 Fig.3Theinfraredspectrumofthesoakingliquidunder60% 2.2湿热环境对复合材料力学性能的影响 弯曲性能主要用来表征复合材料的抗拉和抗压 的综合性能。本文选用弯曲性能测试来研究老化环 境对复合材料中增强材料的影响。图4所示为玻璃 纤维增强复合材料在湿热老化环境下弯曲强度和弯 曲模量随老化时间的变化情况。从图中可以看出, 随着老化时间的增加,材料的弯曲强度、弯曲模量均 ℃ ℃ 有不同程度的下降,4周后,23、37.8 ̄C和60条 件下弯曲强度分别下降36.9%、46.7%和70.0%; 弯曲模量分别下降14.3%、24.5%和27.1%。可 见,温度越高,材料的力学性能下降越显著。从玻璃 纤维增强复合材料的弯曲破坏形貌可以看出,老化 初期弯曲破坏的主要形式为纤维拉断。随着浸泡时 间的延长,水与玻璃纤维发生反应。玻璃纤维组成 中除SiO,以外,还含有Al、Ca、Mg等元素。一旦玻 璃纤维与介质水接触,那些非SiO:成分以离子形式 溶出,引起玻璃纤维表面的破坏,并逐渐深入,从而 导致弯曲强度的下降。1年后,弯曲强度的下降幅 度趋于平缓,弯曲破坏的形式已经由纤维拉断转变 为分层破坏,这是因为湿热老化使玻璃纤维增强复 合材料的界面变弱,界面的粘结力已经不足以承受 过高的载荷,由于界面脱粘,致使复合材料失效。由 于水分子的介入,使玻璃纤维复合材料发生塑化,从 而使弯曲模量平缓下降。由于材料在老化初期8周 内力学性能变化最为显著,为了进一步研究材料湿 热老化机理,采用扫描电子显微镜观察了复合材料 断面形貌。图5所示为复合材料断面形貌,由老化 前后试样破坏形貌可以看出未老化试样断口整齐,属 于纤维拉断导致材料失效。老化8周后,破坏断面能 明显观察到纤维从基体中拔出的痕迹,为界面失效。 由于界面不能正常传递应力,致使受力过程中,界面 脱粘先于纤维断裂,因此复合材料拉伸强度下降。 2013年第4期 玻璃钢/复合材料 31 (a)弯曲强度 (a)Flexuralstrength (b)弯曲模量 (b)Flexuralmodulus 图4复合材料湿热老化弯曲性能 Hg.4Theflexuralpropertiesofhygrothermalagingcomposites (a)未老化(a)Bef oreaging (b)湿热老化8周 (b)Agingfor8weeks 图5复合材料断面形貌 Fig.5Thefracturemorphologyofcomposites 2.3湿热环境下复合材料耐久性预测 2.3.1基于时-温等效原理的耐久性预测模型 基于时一温等效原理n,Williams,Landel和Fer. ry提出著名的WLF经验方程: g。=g= 二 c4, 式中,为参考温度;t为参考温度;C、C:为经 验常数,可通过计算得出。整理式(4)可知,对于任一 温度,都有:一 C2lg— =— (5) C1+lg一 C2lg一 =——_÷ (6) C1+lgt, 2 表1给出了在三个温度下的湿热老化环境中, 复合材料对应不同老化时间的弯曲强度值。取= 296.15K,Tl=310.95K,=333.15K,当弯曲强度 为50MPa时,则根据三个温度下弯曲强度与时间对 照表(表1)得到t=112,t=56,t:=7。带入上述方 程,可得到C=一1.2,C=74。 表1湿热老化后复合材料的弯曲强度值(MPa) Table1Theflexuralstrengthofcompositesafter hygrothermalaging(MPa) 由时-温等效原理,可将三个不同温度下材料弯 曲强度数据整合为23 ̄C下强度主曲线。根据文献的研究¨ ,材料残余弯曲强度与老化时间的关系可 用式(6)表示: P Pt 。1n(f)+6】 (6)I ll≥ _∞ ∞ ∞ 柏蛐印蚰加0 B.喜口§ ≥ l_g 32 复合材料湿热老化行为研究及其耐久性预测 2013年7月 P为温热老化t时刻,复合材料的弯曲强度, 为复合材料的初始弯曲强度,a、b为待定常数。据 玻璃纤维增强复合材料的弯曲强度实验值,可建立 老化时间t与弯曲强度P的预测曲线,结果如式 (7): P=一6.4671n(t)+104.811 (7) 将弯曲强度预测公式绘制成曲线与主曲线进行 比较(如图6所示),发现前期数据拟合效果较好, 后期预测值低于实验值(约偏低16%~41%)。因 此需要在此基础上进一步修正。 图6基于时一温等效原理建立的预测模型 — Fig.6Thepredictmodelbasedontimetemperature equivalenceprinciple 2.3.2基于界面参数与时.温等效性原理的耐久性 预测模型 湿热老化后期,材料的失效形式主要为分层破 坏,与界面的性能密不可分。因此,通过引入界面参 数对原模型进行修正。 在研究复合材料动态力学性能时,可将复合材 料整体力学性能与各组分性能联系起来: tans。=VftanSy+Vitan6+Vmtan8 (8) 其中,tan8、tanSf、tans、tans分别代表复合材 料、纤维、界面和基体损耗因子;、、Vm分别代表 纤维、界面和基体的体积分数。由于玻璃化转变是 非晶态高分子材料固有的性质,因此认为玻璃纤维 ta,=0,又因为非常小,可近似看成Vm=1一。 定义界面参数A[I9]: A=× 因此,根据式(9)可得出界面参数A与、 tans、tant ̄的关系式: |2 | 南× (10) 由实验所得老化环境中复合材料以及纯树脂损 耗因子的变化如图7所示,根据上式可以计算出材 料老化过程中不同时期界面参数的变化情况,如表 2所示。将此参数加人到原有模型当中,即可修正 后期预测曲线,如图8所示。 (a)复合材料 (a)Composites (b)环氧树脂 (b)Epoxyresin 图7损耗因子随时间变化 Fig.7Thechangeoflossfactorwithtime 表2湿热老化环境下玻璃纤维增强复合材料界面参数 Table2Theinterfacefactorofagingcomposites 根据最小二乘法对界面参数进行回归处理,可 得到界面参数A关于老化时间t的一次方程。 2013年第4期 玻璃钢/复合材料 33 图8根据时-温等效原理拟合界面参数 Fig.8Thefittedinter facefactorbasedonthe time-temperatureequivalenceprinciple 因此得到界面参数计算公式为: A=0.00003t+1.0995 (11) 将此界面参数加入预测模型中,得到:————————— —————— P.=一6.4671nl一l+104.811‘ L(0. 00003t+1.0995)J (12) 将式(12)绘制成曲线,与上一预测模型进行对 比(图6),从图9中可以看出,修正后的模型对后期 复合材料弯曲强度的预测结果明显优于基于时一温 等效原理建立的模型。因此,对于玻璃纤维增强复 ℃ 合材料的性能预测,拟采用前期应用23等效原理 为基础的预测模型,而后期则根据复合材料的老化 机理,应用界面参数修正模型。 老化预测模型可以整理为: ≤ P=一6.4671n(t)+104.811A1.12(13) ■P=一6.4671n(1r× t)+104.811A>1.12 (14) 图9基于界面参数以及时一温等效原理建立的预测模型 Fig.9Themodif iedpredictmodelbasedoninterface — parameterandtimetemperatureequivalenceprinciple 3结论 (1)玻璃纤维增强环氧树脂复合材料的吸水速 率分为两个阶段。第一阶段随着浸泡时间的延长, 复合材料吸水量逐渐增加直至达到饱和,近似满足 Fickian扩散定律,且温度越高,材料吸水速率越快; 第二阶段,复合材料增重率随浸泡时间的延长有所 下降,出现了偏离Fickian方程的情况,并且温度越 高,出现下降的时间越早; (2)随着老化时间的增加,复合材料的弯曲强 度、弯曲模量均有不同程度的下降,并且老化温度越 高,材料的力学性能下降越显著。老化初期弯曲破 坏的主要形式为纤维拉断,老化后期弯曲破坏形式 主要为分层破坏; (3)在耐久性预测模型中引入界面参数的概 念,建立了复合材料力学性能与湿热老化时间的定 性/定量关系,拟合结果与实测值较为接近。 参考文献 [1]杜善义.先进复合材料与航空航天[J].复合材料学报(Aeta — MateriaeCompositaeSinica),2007,24(1):112. [2]廖子龙,乌云其其格.环氧树脂/玻璃纤维复合材料性能研究与 应用[J].工程塑料应用(EngineeringPlasticsApplication), 2008,36(9):47-50. [3]王智,顾宜.碳纤维增强苯并嗯嗪树脂基复合材料的研究进展 [J].玻璃钢/复合材料(FiberReinforcedPlastics/Composites), 2011,(4):68-72. [4]郭书良,段跃新,肇研,罗云烽.连续玻璃纤维增强热塑/热固 性复合材料力学性能研究[J].玻璃钢/复合材料(FiberRein. forcedPlastics/Composites),2009,(5):42-45. [5]李林洁,于运花,唐泽辉,薛忠民,杨小平.界面粘结对GF/VE 复合材料在硫酸介质中耐蚀性能的影响[J].玻璃钢/复合材料 (FiberReinforcedPlastics/Composites),2010,(6):9-13. [6]肖文萍,吕小军,许俊华,张琦,马兆庆.温热老化对碳纤维/环 氧树脂基复合材料力学性能影响研究[J].材料工程(Journalof MaterialsEngineering),2005,(11):50-53. [7]NAKAIA,IKEGAKIS,HAMADAH,TakedaN.Degradationof — braidedcompositesinhotwater[J].CompositesScienceandTeeh nology,2000,60(3):325-331. [8]GUPTAKM,PAWARSJ.Anonlineardiffusionmodelineorpora.r ingedgeandsurfacetextureeffectstopredictabsorptionbehaviour ofcomposites[J].MaterialsScienceandEngineering,2005,412 (1-2):78{2. 瓣 复合材料湿热老化行为研究及其耐久性预测 2013年7月 — [9]BOUALEMN,SEREIRZ.Acceleratedagingofunidirectionalhy — — bridcompositesunderthelongtermelevatedtemperatureandmois — tureconcentration[J].TheoreticalandAppliedFractureMechan ics,2011,55(1):68-75. — [10]WEITSMANYJ,GUOYJ.Acorrelationbetweenfluidinduced damageandanomalousfluidsorptioninpolymericcomposites[J]. CompositesScienceandTechnology,2002,62(6):889-908. — [11]WANYZ,LUOHL,HEF,UANGH,HUANGY,LIXL.Mechaniea l,moistureabsorption,andbiodegradationbehavioursof — — bacterialcellulosefibrereinforcedstarchbiocomposites[J].Com — positesScienceandTechnology,2009,69(7):12121217. [12]WEITSMANYJ.Anomalousfluidsorptioninpolymericcomposites — anditsrelationtofluidinduceddamage[J].CompositesPartA: AppliedScienceandManufacturing,2006,37(4):617-623. [13]LEVEQUED,SCHIEFFERA,MAVELA,MAIREJF.Analysis — ofhowthermalagingaffectsthelongtermmechanicalbehaviorand — strengthofpolymermatrixcomposites[J].CompositesScienceand Technology,2005,65(3):395-401. [14]ALVAREZVA,VALDEZME,VAZQUEZA.Dynamicmechani- — calpropertiesandinterphasefiber/matrixevaluationofunidirection alglassfiber/epoxycomposites[J].PolymerTesting,2003,22 (6):611-615. [15]MIYANOY,NAKADAM,SEKINEN.Acceleratedtestingfor— — longtermdurabilityofGFRPlaminatesformarineuse[J].Com positesPartB:Engineering,2004,35(6-8):497-502. [16]TAKAYANAGIM,IMADAK,KAJIYAMAT.Mechanicalproper- tiesandfinestructureofdrawnpolymers[J].JoumalofPolymer Science:PartC:PolymerSymposia,1967,15(1):263-281. [17]何曼君,陈维孝,董西侠.高分子物理[M].上海:复旦大学 出版社,2000.357-359. [18]KARBHARIVM,ABANILLAMA.Designfactom,reliability,a nddurabilitypredictionofwetlayupcarbon/epoxyusedinexter- halstrengthening[J].CompositesPartB:Engineering,2007,38 (1):103. — [19]IBARRAL,PANOSD.Dynamicpropertiesofthermoplasticsbutadiene-styr enea ndoxidizedshortcarbonfibercompositematerials [J].JournalofAppliedPolymerScience,1998,67(10): 】8】9一】826. THESTUDYoNHYGRoTHERMALAGINGBEHAVIoRoFCoMPoSITES ANDTHEPREDICTIoNMoDELoFDURABILITY SUNBo,LIYan fSchoolofAerospaceEngineeringandAppliedMechanics,Ton ̄iUniversity,Shanghai200092,China) Abstract:Inthisstudy,theeffectsofhygrothermalenvironmentsonthedurabilityofglassfiberreinforcedep。 oxycompositeswereinvestigatedincludingphysicalandchemicaldegradation.Inordertoassessthedurabilityof —— suchsvstems,aninvestigationwasundertakeninthehydrothermalconditionswithdifferenttemperatures.Interlam ’ inarsheartestandbendingtestwereobtainedperiodicallytostudythemechanicaldegradation.Themoistureab — sorptionresponseofthecompositeswasalsodeterminedoveran80一weekperiod.Inaddition,scanningelectronmi croscopephotosofthecompositeswereobtainedbeforeandafteraging.Thesampleswerealsoanalyzedbymeansof Fouriertransforminfraredspectroscopy(FFIR)toidentifydegradationproductsandestimatetheinfluenceofglass fiberandD0lymeronchemicaldegradationofthestudiedcomposites.Theresultshowsinthefirststagetheweight gainincreasedgraduallyovertime,anditwasinaccordancewiththeFickianLaw,whileinthesecondstage, weightgainofcompositedroppeddown.Theflexuralpropertiesreducedgraduallywithagingtime,theinterface Derformancewasseriouslyimpact.Thepredictionmodelwassetupbasedonthetime-temperatureequivalenceprin。 cipleandexperimentaldata.Duringthelaterperiodofaging,thefracturemodewasmainlydelamination,sothe mode1wasmodifiedbyaninterfacefactor,anditshowedaquitegoodagreementwiththeexperimentalvalue Keywords:composites;hygrothermalaging;waterabsorptionbehavior;mechanicalproperties;durability
您可能关注的文档
- “离位”增韧复合材料准静态压入损伤特性研究.pdf
- “神舟七号”飞船舱外航天服防护头盔组件的研制.pdf
- “十二五”复合材料发展重点和方向解读.pdf
- “珠串”堆叠超结构的介孔铁酸锌的制备与表征.pdf
- (001)应变对正交相Ca2 P0.25 Si0.75能带结构及光学性质的影响.pdf
- 0.8设计系数用X80管线钢在近中性pH溶液中的应力腐蚀开裂行为.pdf
- 0.20mm CGO硅钢高温退火Goss晶粒起源及异常长大行为研究.pdf
- 0Cr16Ni5Mo低碳马氏体不锈钢的热变形行为及其热加工图.pdf
- 0Cr17Ni4Cu4Nb钢制螺钉断裂原因分析.pdf
- 1.5MW风机叶片模具加热工艺研究与技术创新.pdf
- 1.5MW风机叶片VARI工艺模拟分析及验证.pdf
- 2.5维机织复合材料低速冲击性能研究.pdf
- 2.25Cr-1Mo钢后续热处理中的磷偏聚行为.pdf
- 2A50锻铝三点弯曲试验与高分辨率CT成像分析.pdf
- 2A12与2A11铝合金超声波焊接工艺与组织研究.pdf
- 2MW风机复合材料叶片材料及工艺研究.pdf
- 3Cr2W8V模具钢激光表面相变硬化层性能的研究.pdf
- 3D打印技术及先进应用研究进展.pdf
- 3D打印技术研究现状和关键技术.pdf
- 5%鱼藤酮悬浮剂的研制.pdf

- 周大爷
- 该用户很懒,什么也没介绍
相关文档
- “离位”增韧复合材料准静态压入损伤特性研究.pdf2021-11-235页
- “神舟七号”飞船舱外航天服防护头盔组件的研制.pdf2021-11-233页
- “十二五”复合材料发展重点和方向解读.pdf2021-11-232页
- “珠串”堆叠超结构的介孔铁酸锌的制备与表征.pdf2021-11-235页
- (001)应变对正交相Ca2 P0.25 Si0.75能带结构及光学性质的影响.pdf2021-11-236页
- 0.8设计系数用X80管线钢在近中性pH溶液中的应力腐蚀开裂行为.pdf2021-11-237页
- 0.20mm CGO硅钢高温退火Goss晶粒起源及异常长大行为研究.pdf2021-11-237页