- 文档大小:731.99 KB
- 文档格式:pdf
- 约 10页
- 2022-04-11 发布
- 举报
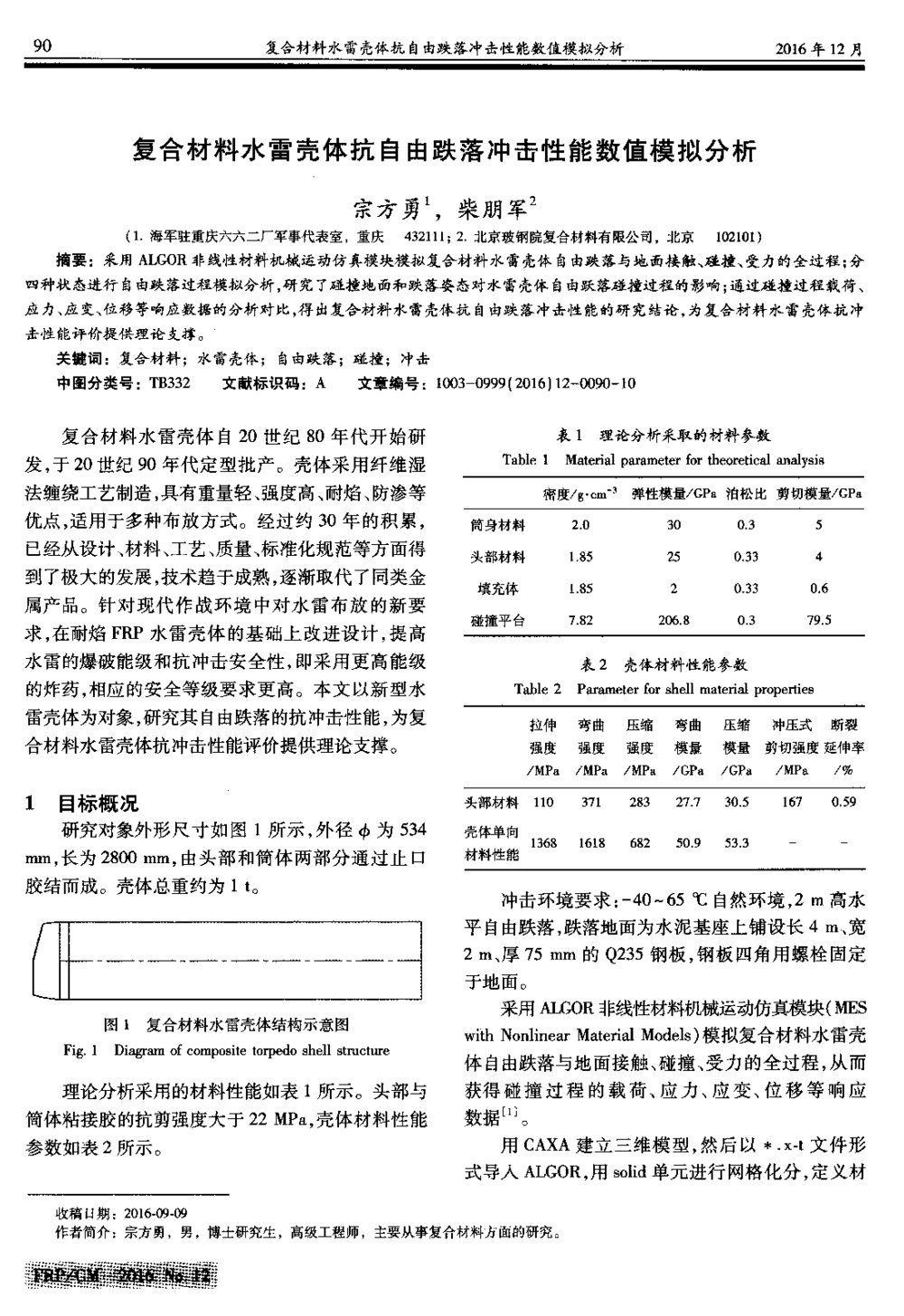
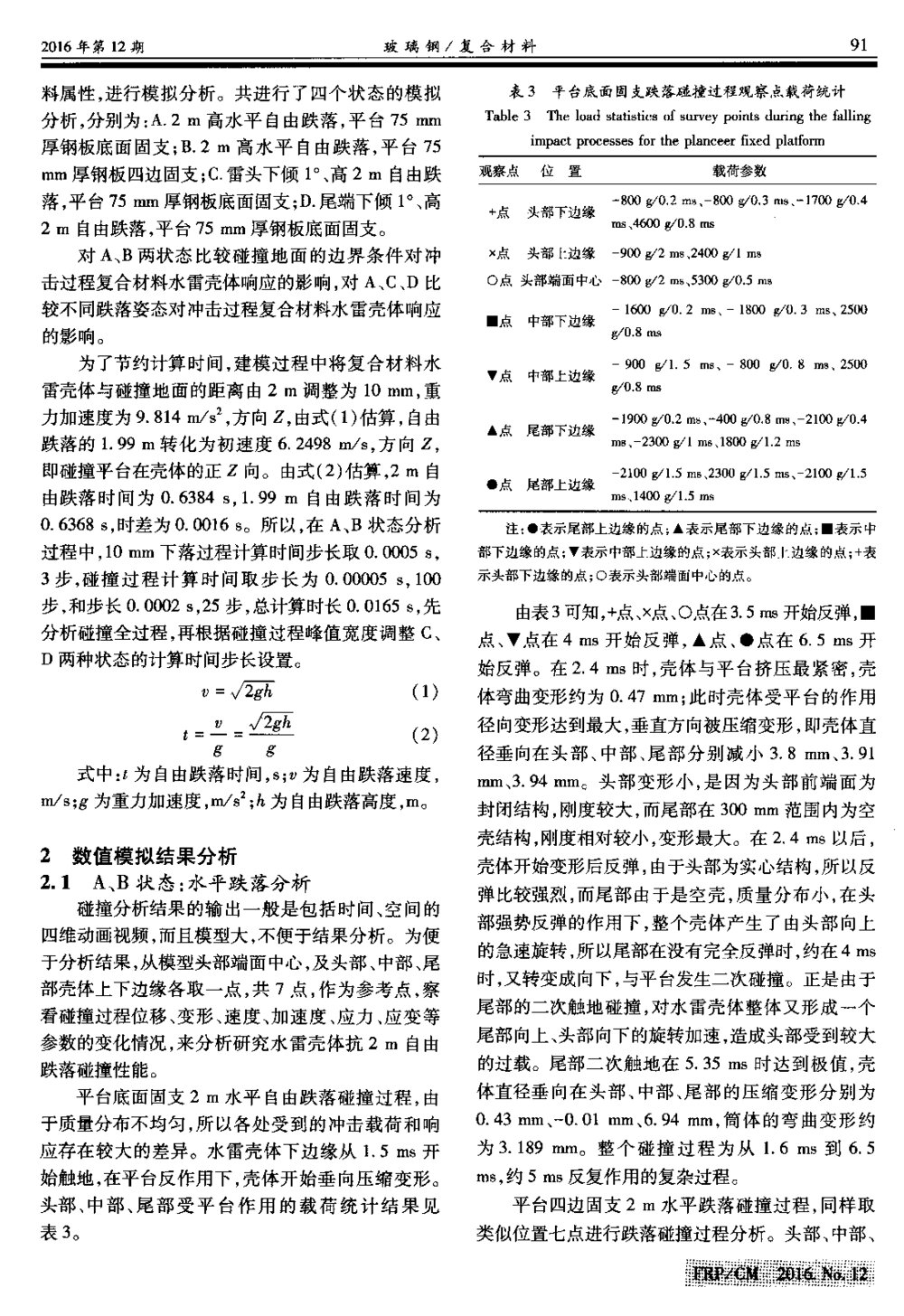
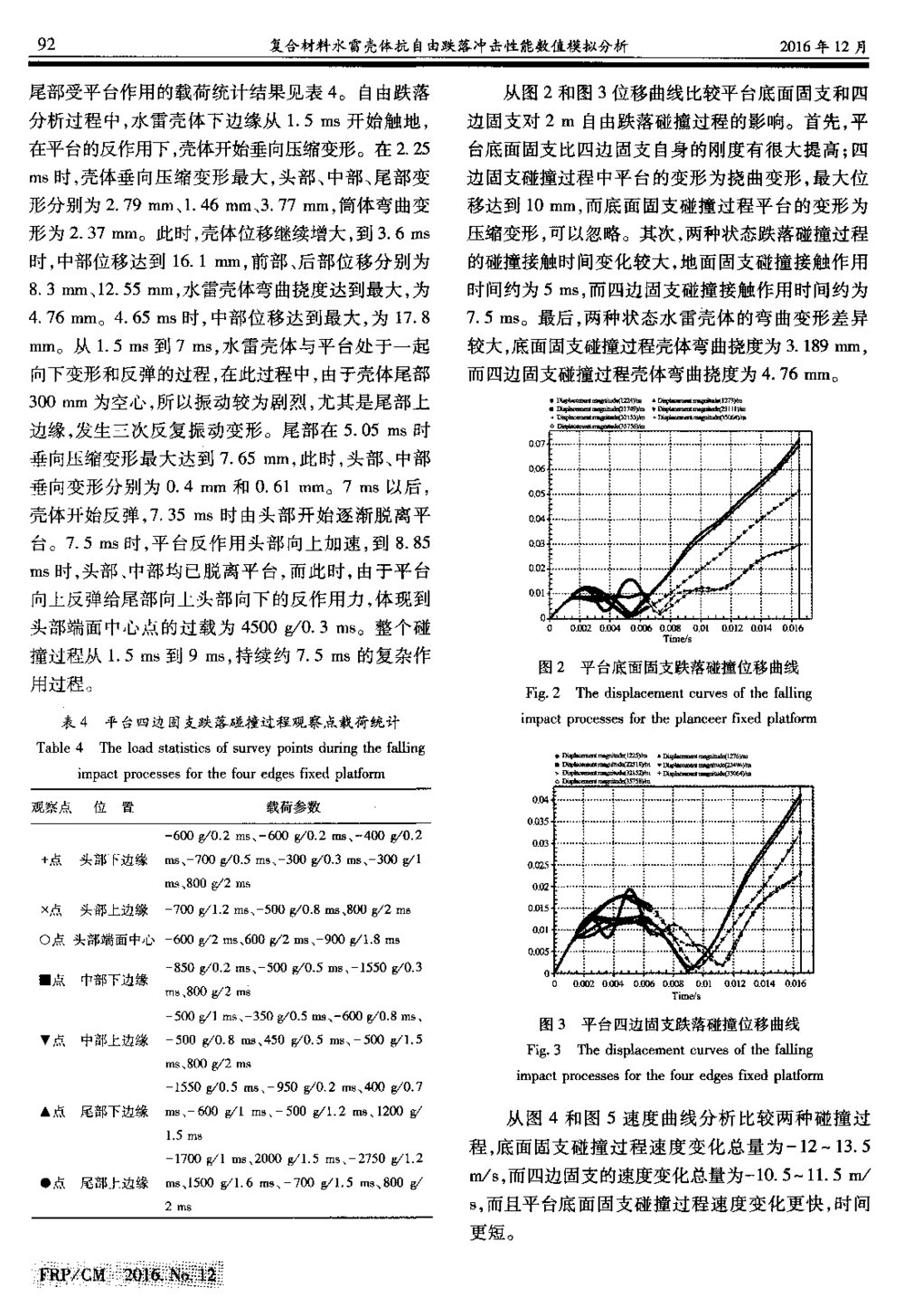
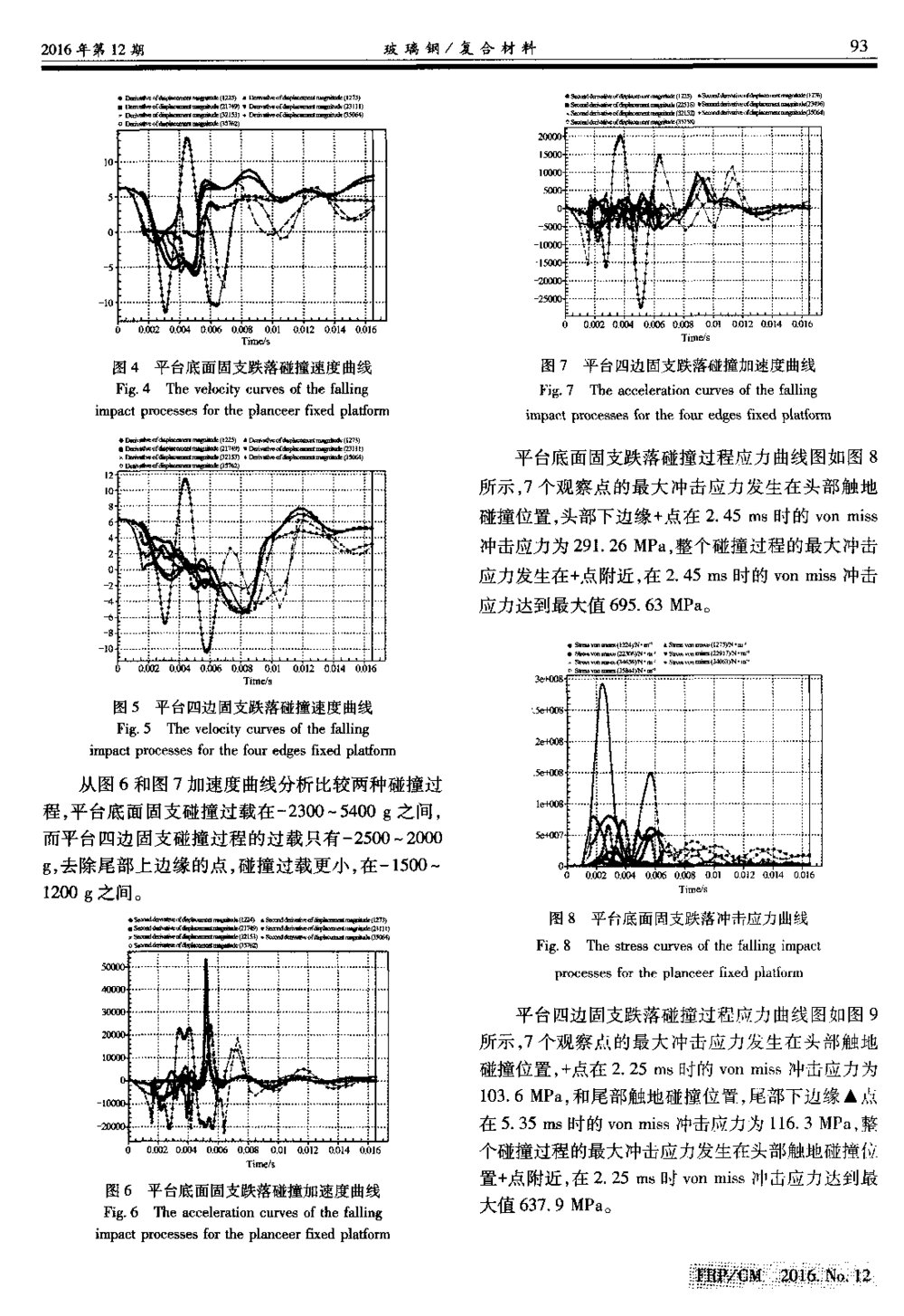
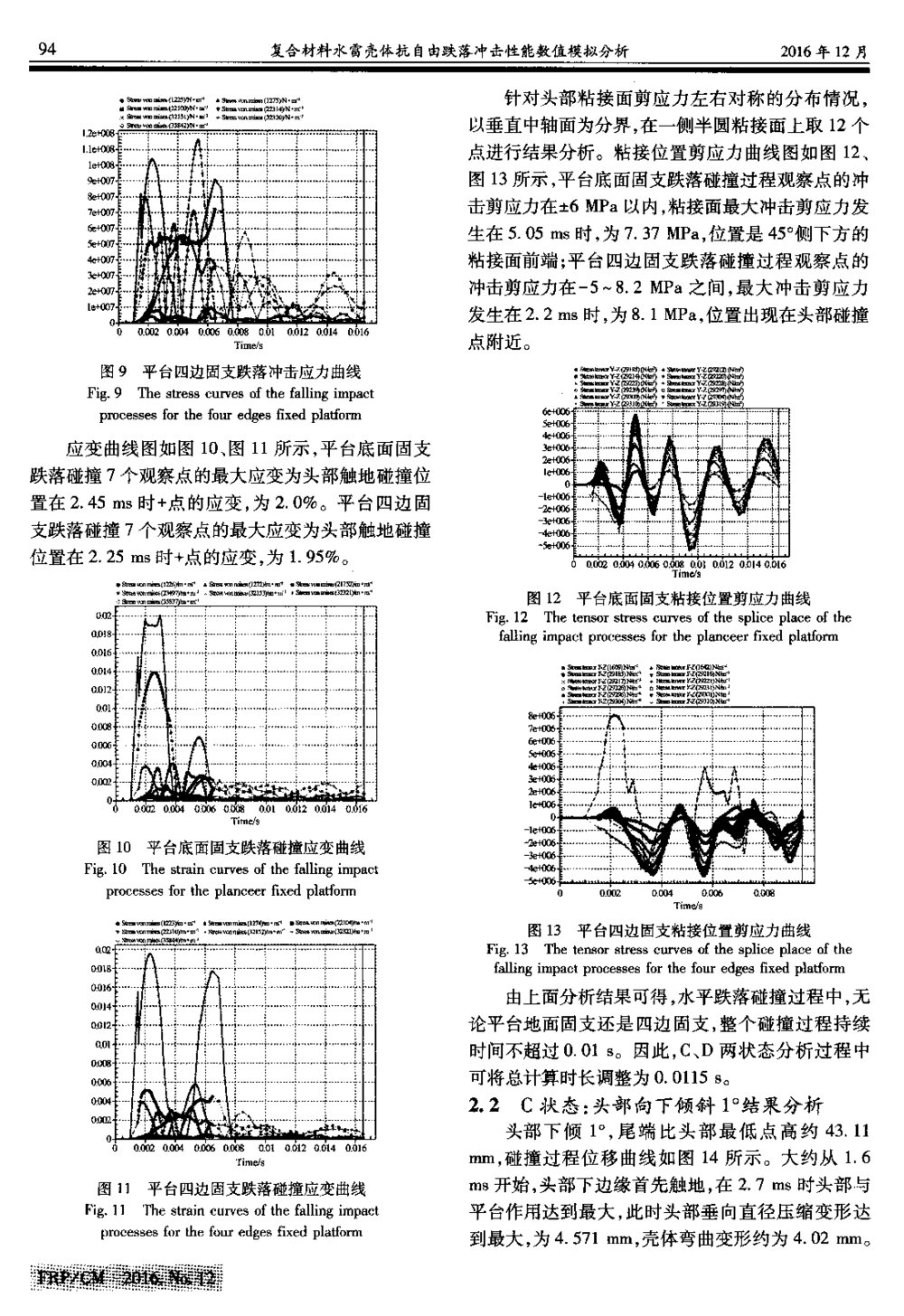
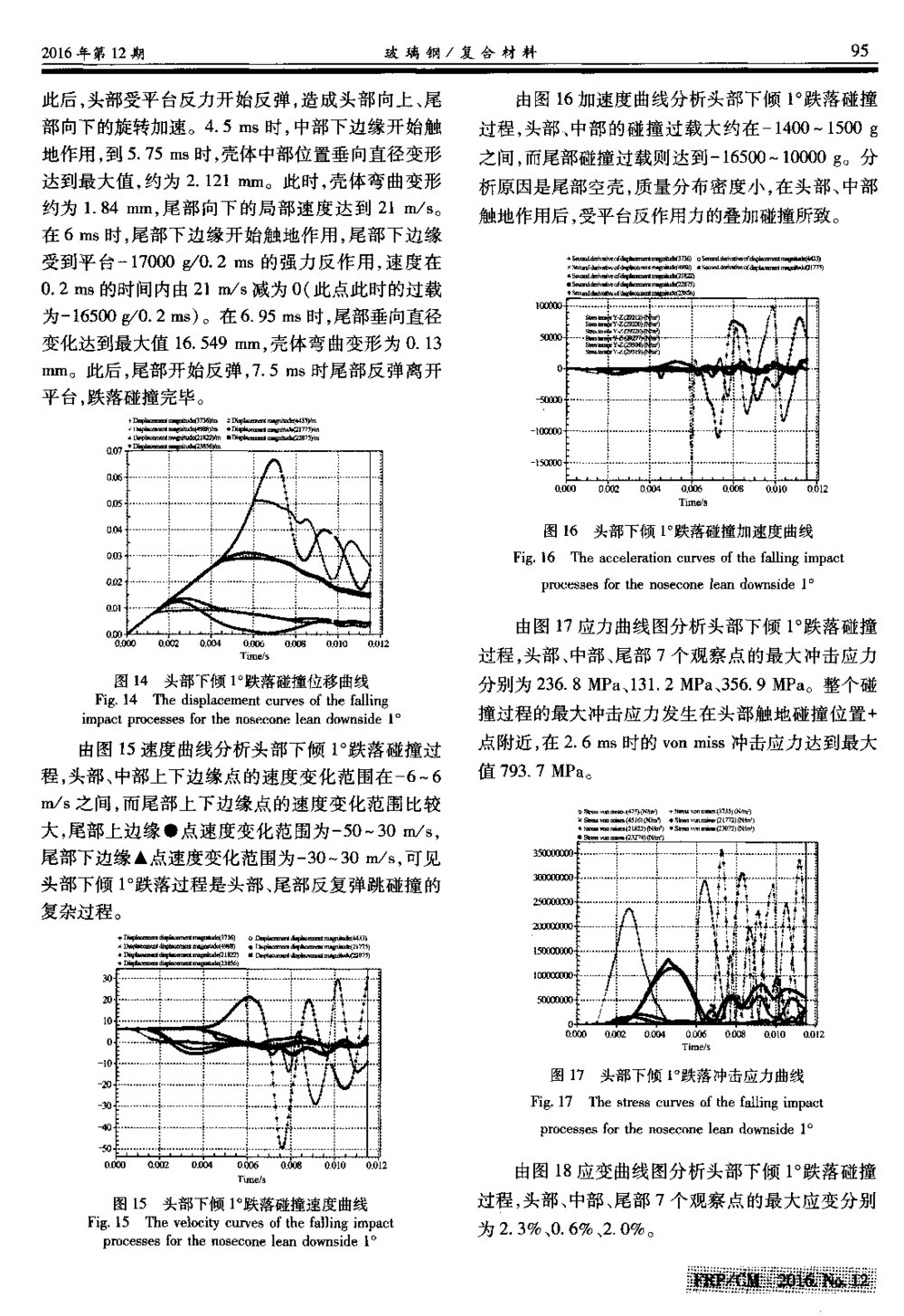
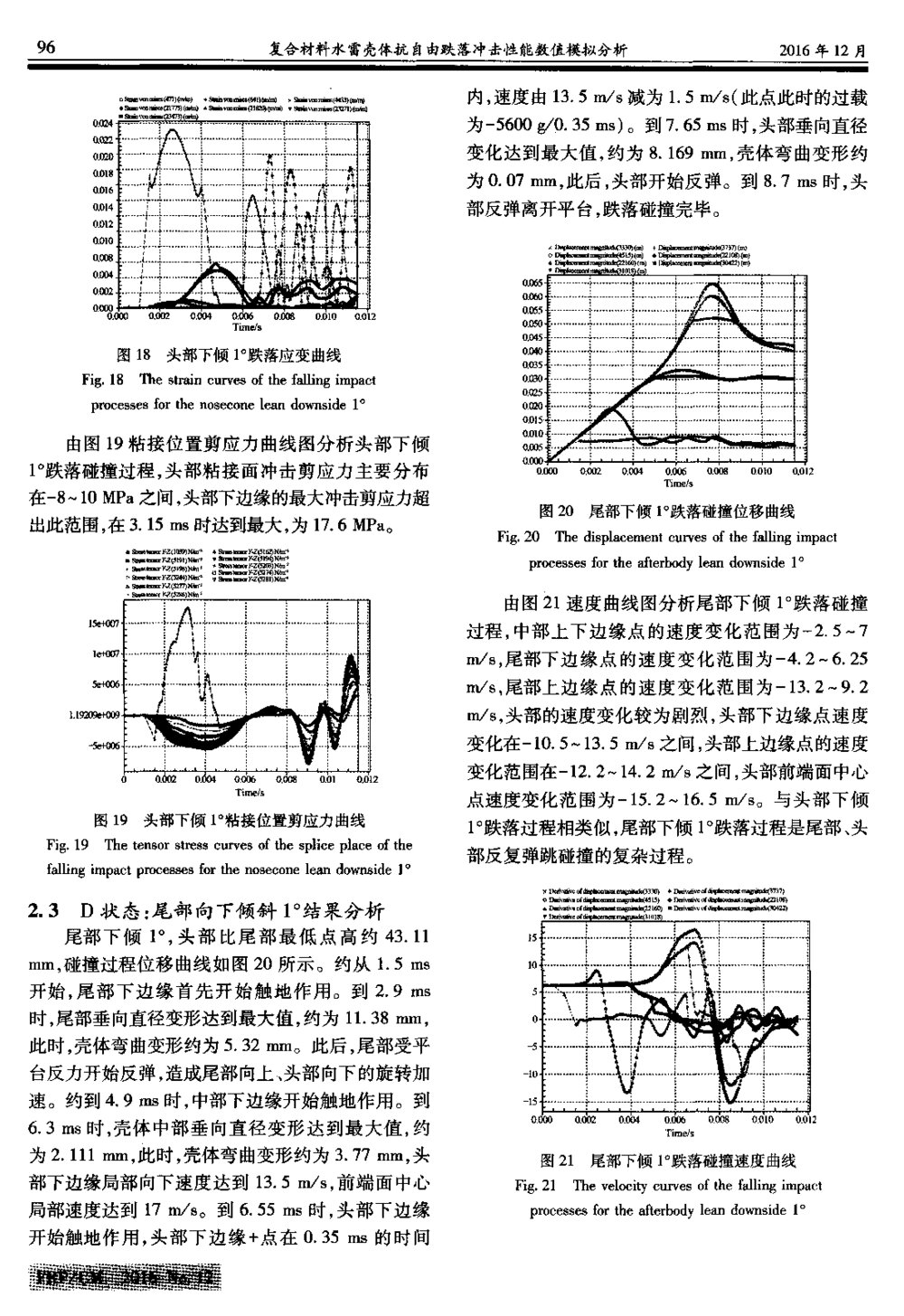
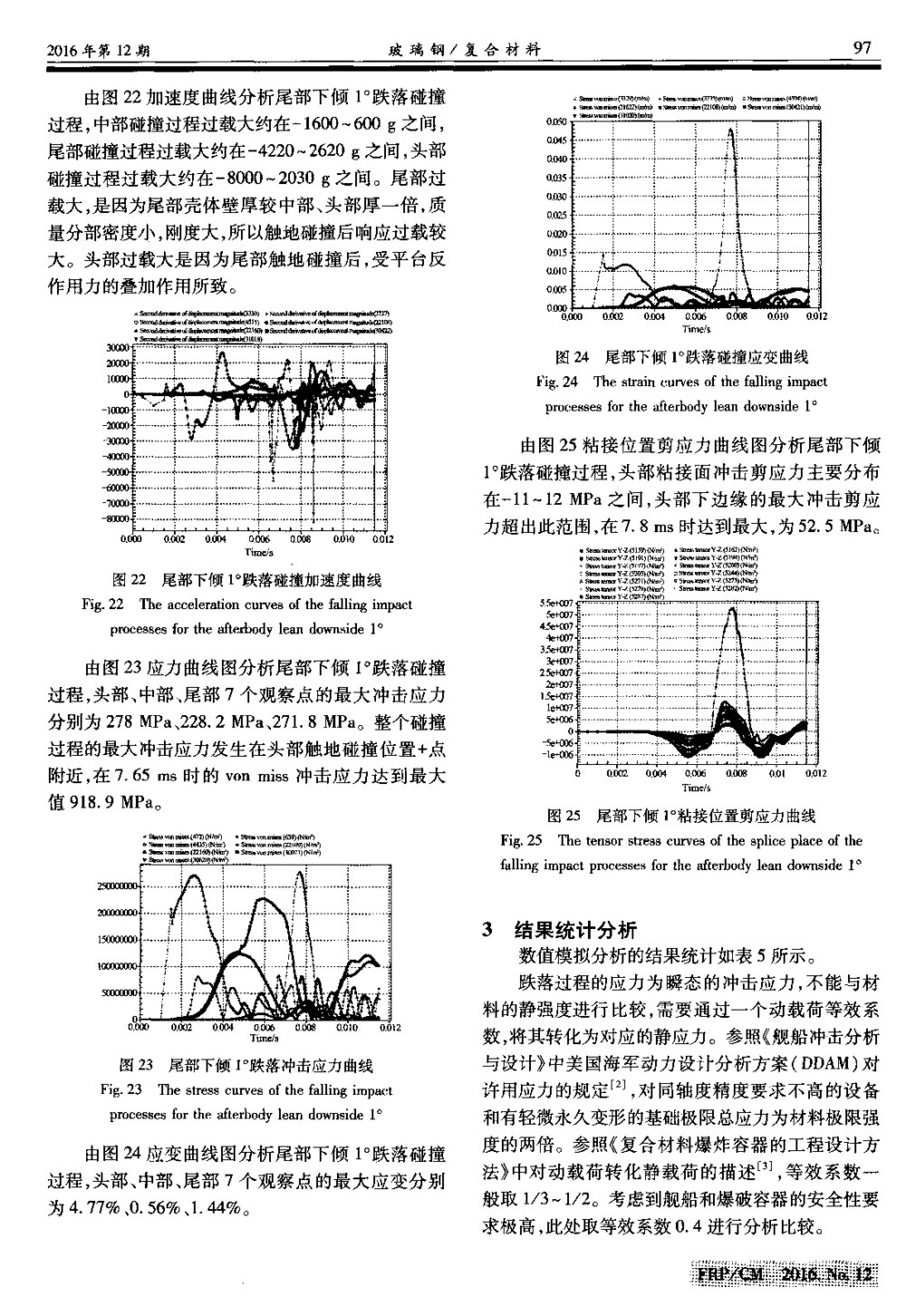
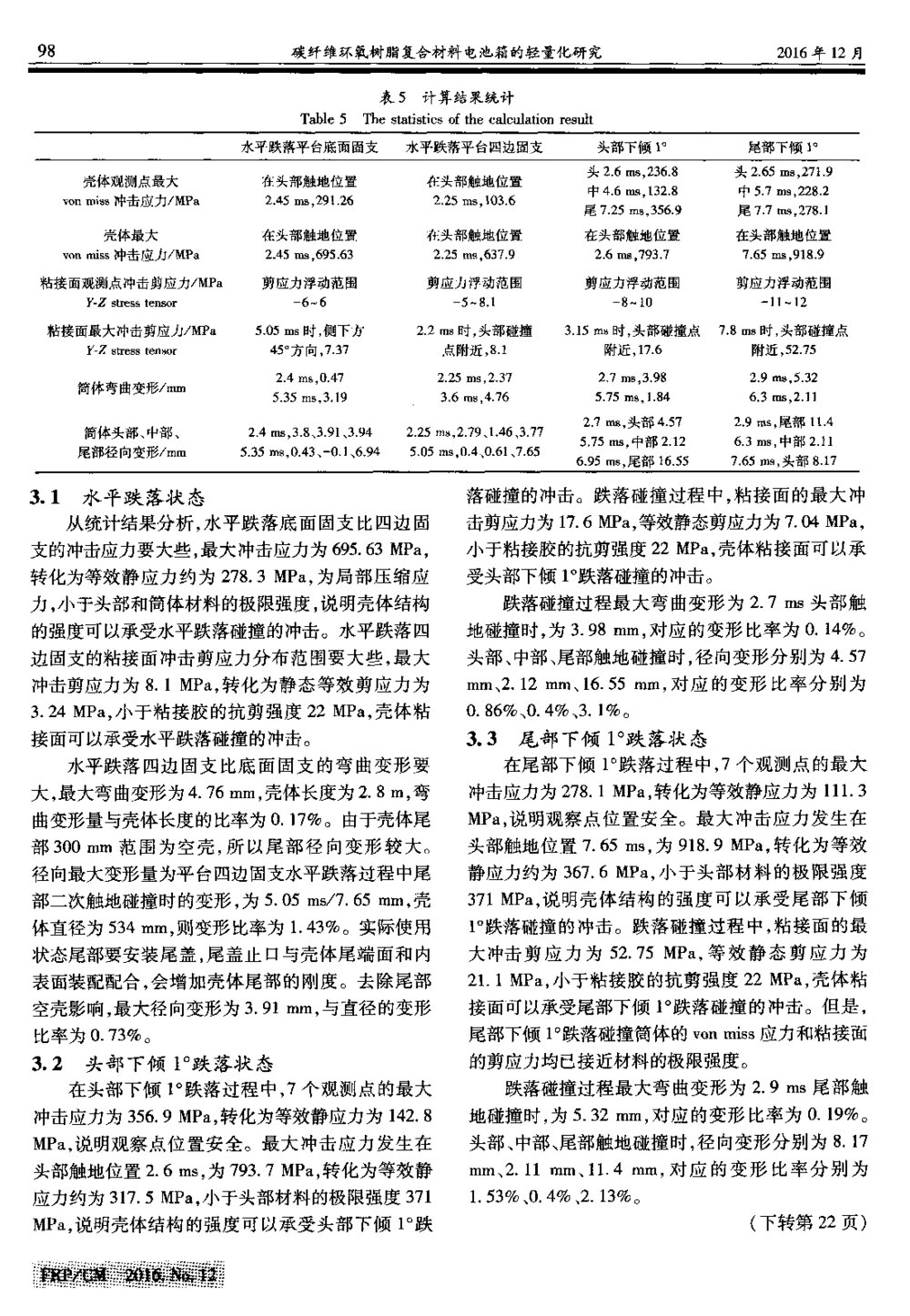
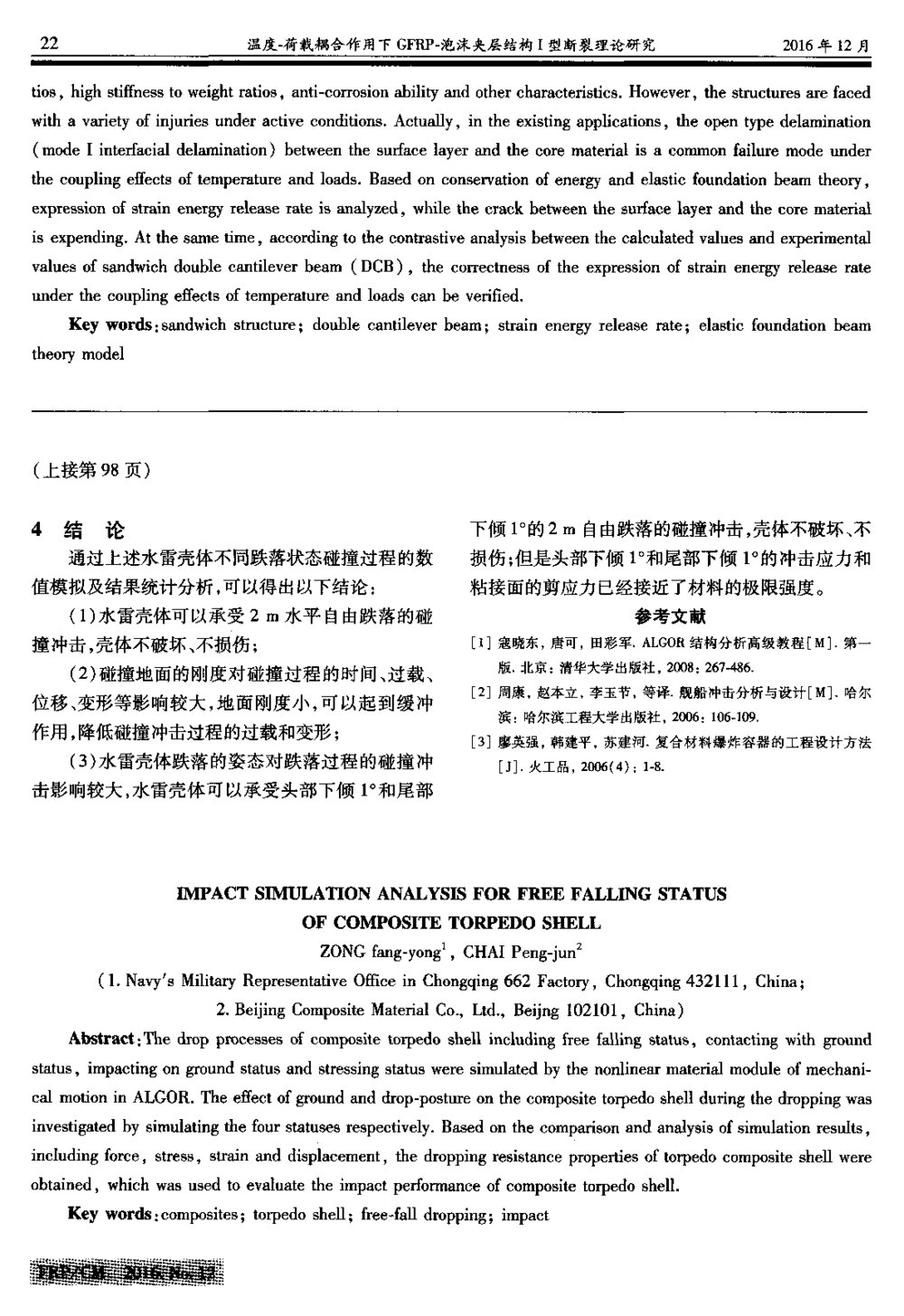
已阅读完毕,您还可以下载文档进行保存
- 1、本文档共10页,内容下载后可编辑。
- 2、本文档内容版权归属内容提供方,所产生的收益全部归内容提供方所有。如果您对本文有版权争议,可选择认领。
- 3、本文档由用户上传,本站不保证质量和数量令人满意,可能有诸多瑕疵,付费之前,请仔细先通过免费阅读内容等途径辨别内容交易风险。如存在严重挂羊头卖狗肉之情形,可联系本站下载客服投诉处理。
复合材料水雷壳体抗自由跌落冲击性能数值模拟分析2016年12月复合材料水雷壳体抗自由跌落冲击性能数值模拟分析宗方勇,柴朋军(1.海军驻重庆六六二厂军事代表室,重庆432111;2.北京玻钢院复合材料有限公司,北京102101)摘要:采用ALGOR非线性材料机械运动仿真模块模拟复合材料水雷壳体自由跌落与地面接触、碰撞、受力的全过程;分四种状态进行自由跌落过程模拟分析,研究了碰撞地面和跌落姿态对水雷壳体自由跃落碰撞过程的影响;通过碰撞过程载荷、应力、应变、位移等响应数据的分析对比,得出复合材料水雷壳体抗自由跌落冲击性能跌究结论,为复合材料水雷壳体抗冲击性能评价提供理论支撑。关键词:复合材料;水雷壳体;自由跌落;碰撞;冲击中图分类号:TB332文献标识码:A文章编号:1003-0999(2016)12-0090-10复合材料水雷壳体自20世纪80年代开始研发,于20世纪9O年代定型批产。壳体采用纤维湿法缠绕工艺制造,具有重量轻、强度高、耐焰、防渗等优点,适用于多种布放方式。经过约30年的积累,已经从设计、材料、工艺、质量、标准化规范等方面得到了极大的发展,技术趋于成熟,逐渐取代了同类金属产品。针对现代作战环境中对水雷布放的新要求,在耐焰FRP水雷壳体的基础上改进设计,提高水雷的爆破能级和抗冲击安全性,即采用更高能级的炸药,相应的安全等级要求更高。本文以新型水雷壳体为对象,研究其自由跌落的抗冲击性能,为复合材料水雷壳体抗冲击性能评价提供理论支撑。1目标概况研究对象外形尺寸如图l所示,外径西为534mm,长为2800mm,由头部和简体两部分通过止口胶结而成。壳体总重约为1t。图1复合材料水雷壳体结构示意图Fig.1Diagramofcompositetorpedoshellstructure理论分析采用的材料性能如表1所示。头部与筒体粘接胶的抗剪强度大于22MPa,壳体材料性能参数如表2所示。表1理论分析采取的材料参数Table1Materialparameterfortheoreticalanalysis表2壳体材料性能参数Table2Parameterforshellmaterialproperties—冲击环境要求:-4065oC自然环境,2m高水平自由跌落,跌落地面为水泥基座上铺设长4m、宽2m、厚75mm的Q235钢板,钢板四角用螺栓固定于地面。采用ALGOR非线性材料机械运动仿真模块(MESwithNonlinearMaterialModels)模拟复合材料水雷壳体自由跌落与地面接触、碰撞、受力的全过程,从而获得碰撞过程的载荷、应力、应变、位移等响应…数据。—用CAXA建立三维模型,然后以:Ic.xt文件形式导入ALGOR,用solid单元进行网格化分,定义材——收稿日期:20160909作者简介:宗方勇,男,博士研究生,高级工程师,主要从事复合材料方面跌究。2016年第l2期玻璃钢/复合材料9l料属性,进行模拟分析。共进行了四个状态的模拟分析,分别为:A.2m高水平自由跌落,平台75mm厚钢板底面固支;B.2m高水平自由跌落,平台75mm厚钢板四边固支;C.雷头下倾1。、高2m自由跌落,平台75mm厚钢板底面固支;D.尾端下倾1。、高2m自由跌落,平台75mm厚钢板底面固支。对A、B两状态比较碰撞地面的边界条件对冲击过程复合材料水雷壳体响应的影响,对A、c、D比较不同跌落姿态对冲击过程复合材料水雷壳体响应的影响。为了节约计算时间,建模过程中将复合材料水雷壳体与碰撞地面的距离由2m调整为10mm,重力加速度为9.814m/s,方向z,由式(1)估算,自由跌落的1.99m转化为初速度6.2498m/s,方向z,即碰撞平台在壳体的正z向。由式(2)估算,2m自由跌落时间为0.6384S,1.99m自由跌落时间为0.6368S,时差为0.0016s。所以,在A、B状态分析过程中,10mm下落过程计算时间步长取0.0005S,3步,碰撞过程计算时间取步长为0.00005s,100步,和步长0.0002s,25步,总计算时长0.0165s,先分析碰撞全过程,再根据碰撞过程峰值宽度调整C、D两种状态的计算时间步长设置。——= ̄/2gh一一v/2gh———t==—gg(1)(2)式中:t为自由跌落时间,s;v为自由跌落速度,m/s;g为重力加速度,m/s;为自由跌落高度,m。2数值模拟结果分析2.1A、B状态:水平跌落分析碰撞分析结果的输出一般是包括时间、空间的四维动画视频,而且模型大,不便于结果分析。为便于分析结果,从模型头部端面中心,及头部、中部、尾部壳体上下边缘各取一点,共7点,作为参考点,察看碰撞过程位移、变形、速度、加速度、应力、应变等参数的变化情况,来分析研究水雷壳体抗2m自由跌落碰撞性能。平台底面固支2m水平自由跌落碰撞过程,由于质量分布不均匀,所以各处受到的冲击载荷和响应存在较大的差异。水雷壳体下边缘从1.5ms开始触地,在平台反作用下,壳体开始垂向压缩变形。头部、中部、尾部受平台作用的载荷统计结果见表3。表3平台底面固支跌落碰撞过程观察点载荷统计Table3Theloadstatisticsofsurveypointsduringthefallingimpactprocessesfortheplanceerfixedplatform观察点位置载荷参数一……一800g/O.2ms、一800g/O.3ms、一1700g/O.4点头部下边缘ms、460o0.8.ms‘×点头部上边缘一900g/2ms、2400g/1ms0点头部端面中心一800s/2ms、5300s/o.5ms一点中部下边缘V点中部上边缘▲点尾部下边缘●点尾部上边缘一1600g/o.2ms、一1800g/O.3ms、2500g/O_8ms一900s/1.5ms、一800g/O.8ms、2500g/O.8ms一1900g/O.2ms、一400s/o.8ms、一2100g/o.4ms、一2300g,/1ms、1800g/1.2ms一2100g/1.5ms、2300g/1.5ms、一2100g/1.5ms、1400s/1.5ms●▲注:表不尾部上边缘的点;表不尾部下边缘的点;一表示中部下边缘的点;V表示中部上边缘的点;×表示头部上边缘的点;+表示头部下边缘的点;0表示头部端面中心的点。由表3可知,+点、×点、o点在3.511"i8开始反弹,一▲●点、V点在4ms开始反弹,点、点在6.5ms开始反弹。在2.4ms时,壳体与平台挤压最紧密,壳体弯曲变形约为0.47mm;此时壳体受平台的作用径向变形达到最大,垂直方向被压缩变形,即壳体直径垂向在头部、中部、尾部分别减小3.8mm、3.91mm、3.94mm。头部变形小,是因为头部前端面为封闭结构,刚度较大,而尾部在300mm范围内为空壳结构,刚度相对较小,变形最大。在2.4ms以后,壳体开始变形后反弹,由于头部为实心结构,所以反弹比较强烈,而尾部由于是空壳,质量分布小,在头部强势反弹的作用下,整个壳体产生了由头部向上的急速旋转,所以尾部在没有完全反弹时,约在4ms时,又转变成向下,与平台发生二次碰撞。正是由于尾部的二次触地碰撞,对水雷壳体整体又形成一个尾部向上、头部向下的旋转加速,造成头部受到较大的过载。尾部二次触地在5.35ms时达到极值,壳体直径垂向在头部、中部、尾部的压缩变形分别为0.43mm、一0.O1mm、6.94mm,简体的弯曲变形约为3.189mm。整个碰撞过程为从1.6ms到6.5ms,约5ms反复作用的复杂过程。平台四边固支2m水平跌落碰撞过程,同样取类似位置七点进行跌落碰撞过程分析。头部、中部、复合材料水雷壳体抗自由跌落冲击性能数值模拟分析2016年12月尾部受平台作用的载荷统计结果见表4。自由跌落分析过程中,水雷壳体下边缘从1.5ms开始触地,在平台的反作用下,壳体开始垂向压缩变形。在2.25ms时,壳体垂向压缩变形最大,头部、中部、尾部变形分别为2.79mm、1.46mm、3.77mm,简体弯曲变形为2.37mm。此时,壳体位移继续增大,到3.6ms时,中部位移达到16.1mm,前部、后部位移分别为8.3mm、12.55mm,水雷壳体弯曲挠度达到最大,为4.76mm。4.65ms时,中部位移达到最大,为l7.8mm。从1.5ms到7ms,水雷壳体与平台处于一起向下变形和反弹的过程,在此过程中,由于壳体尾部300mm为空心,所以振动较为剧烈,尤其是尾部上边缘,发生三次反复振动变形。尾部在5.05ms时垂向压缩变形最大达到7.65mm,此时,头部、中部垂向变形分别为0.4mm和0.61mm。7ms以后,壳体开始反弹,7.35ms时由头部开始逐渐脱离平台。7.5ms时,平台反作用头部向上加速,到8.85ms时,头部、中部均已脱离平台,而此时,由于平台向上反弹给尾部向上头部向下的反作用力,体现到头部端面中心点的过载为4500g/o.3ms。整个碰撞过程从1.5ms到9ms,持续约7.5ms的复杂作用过程。表4平台四边固支跌落碰撞过程观察点栽荷统计Table4Theloadstatisticsofsurveypointsduringthefallingimpactprocessesforthefouredgesfixedplatform观察点位置载荷参数一600g/O.2ms、一600s/o.2m8、一400s/o.2+点头部下边缘ms、一700g/0.5ms、一300s/0.3ms、一300g/1ms、800g/2ms×点头部上边缘一700g/1.2rtl8、一500s/o.8rtl8、800g/2m8o点头部端面中心一600g/2ms、600s/2I118、一900g/1.8Ins一。.一…一850g/o.2ms、一500g/o.5ms、一1550g/o.3一点中部下边缘丫点中部上边缘▲点尾部下边缘●点尾部上边缘一500g/1ms、一350g/O.5ms、一600r/o.8ms、一500r/0.8m8、450go.5m8、一500g/1.5ms、800g/2ms一1550g/o.5ms、一950r/O.2ms、400g/o.7m8、一600g/1ms、一500g/1.2m8、1200g/1.5ms一1700g/lms、2000g/1.5ms、一2750r/1.2ms、1500g/1.6ms、一700r/1.5ms、8002ms/cllll碡从图2和图3位移曲线比较平台底面固支和四边固支对2m自由跌落碰撞过程的影响。首先,平台底面固支比四边固支自身的刚度有很大提高;四边固支碰撞过程中平台的变形为挠曲变形,最大位移达到10mm,而底面固支碰撞过程平台的变形为压缩变形,可以忽略。其次,两种状态跌落碰撞过程的碰撞接触时间变化较大,地面固支碰撞接触作用时间约为5ms,而四边固支碰撞接触作用时间约为7.5ms。最后,两种状态水雷壳体的弯曲变形差异较大,底面固支碰撞过程壳体弯曲挠度为3.189mm,而四边固支碰撞过程壳体弯曲挠度为4.76mm。●ⅡDm啪-耐目,l・l捌・D妇删口q口岫l,●D∞删m《・Cl7帮啪●Dfnm∞嘲l1Ivm■■■Ihc删rmmlaL't021f,YCmDd__n吐日口I・::::::::……:,,:一l…_/,一…...……l....………0O_加20.0040.∞006080OlOD12n014n016Time/s图2平台底面固支跌落碰撞位移曲线Fig.2Thedisplacementcurvesofthefallingimpactprocessesfortheplanceerfixedplatform图3平台四边固支跌落碰撞位移曲线Fig.3Thedisplacementcurvesofthefallingimpactprocessesforthefouredgesfixedplatform从图4和图5速度曲线分析比较两种碰撞过程,底面固支碰撞过程速度变化总量为一12~13.5—m/s,而四边固支的速度变化总量为一10.511.5m/s,而且平台底面固支碰撞过程速度变化更快,时间更短。2016年第12期玻璃钢/复合材料93图4平台底面固支跌落碰撞速度曲线Fig.4Thevelocitycurvesofthefallingimpactprocessesfortheplanceerfixedplatform图5平台四边固支跌落碰撞速度曲线Fig.5Thevelocitycurvesofthefallingimpactprocessesforthefouredgesfixedplatform从图6和图7加速度曲线分析比较两种碰撞过—程,平台底面固支碰撞过载在一23005400g之间,—而平台四边固支碰撞过程的过载只有-25002000—g,去除尾部上边缘的点,碰撞过载更小,在一15001200g之间。●删m帆■Ⅱ■■●●md口删啦(1}●■∞■■’&由hddh删止017 ̄9)■■∞■∞∞^d叫*150■口训d日dh删mhkt35:▲Jli■-●.一}_:一一.‘●弋i0…l}¥一T:t00.0020.0040O060_嘲0Oln012n014n016Time/s图6平台底面固支跌落碰撞加速度曲线Fig.6Theaccelerationcurvesofthefallingimpactprocessesfortheplanceerfixedplatform图7平台四边固支跌落碰撞加速度曲线Fig.7Theaccelerationcurvesofthefallingimpactprocessesforthefouredgesfixedplatform平台底面固支跌落碰撞过程应力曲线图如图8所示,7个观察点的最大冲击应力发生在头部触地碰撞位置,头部下边缘+点在2.45ms时的yonmiss冲击应力为291.26MPa,整个碰撞过程的最大冲击应力发生在+点附近,在2.45ms时的yonmiss冲击应力达到最大值695.63MPa。・s啉啪 ̄(1224yN・^S'tmn(1275 ̄/Nm●轴锄呻Tm秭fzyN・。-Stl ̄m珊 ̄Ⅷ‘(22917yN・Ⅷx日一ON.Ⅷ+s一‘‘340yN・m:I…_lI:u000020.0040.00600080.010.0120.0140.016Time/s图8平台底面固支跌落冲击应力曲线Fig.8Thestresscurvesofthefallingimpactprocessesfortheplanceerfixedplatform平台四边固支跌落碰撞过程应力曲线图如图9所示,7个观察点的最大冲击应力发生在头部触地碰撞位置,+点在2.25ms时的vonmiss冲击应力为▲103.6MPa,和尾部触地碰撞位置,尾部下边缘点在5.35ms时的vonmiss冲击应力为116.3MPa,整个碰撞过程的最大冲击应力发生在头部触地碰撞位置+点附近,在2.25ms时vonmiss冲击应力达到最大值637.9MPa。辖…P_/1GM;20l6-No-l2☆m*#复合材料水雷壳体抗自由跌落冲击性能数值模拟分析2016年12月●Ⅱr嘲啪珊嘲(1五,yN-…・9r瞄(1275'/N●…r鼬(22100 ̄r’∞&r嚆咖m婚l・nⅡ一—02l51。m+s-啊wn∞OO・nr图9平台四边固支跌落冲击应力曲线Fig.9Thestresscurvesofthefallingimpactprocessesforthefouredgesfixedplatform应变曲线图如图l0、图11所示,平台底面固支跌落碰撞7个观察点的最大应变为头部触地碰撞位置在2.45ms时+点的应变,为2.0%。平台四边固支跌落碰撞7个观察点的最大应变为头部触地碰撞位置在2.25ms时+点的应变,为1.95%。●Ⅱ∞轴哪啪mEsf1帅・^轴日珊fr目(1●・r轴嘟、硼口船017s2 ̄・I-啭m晦0帅・T…sⅡⅡ(32153) ̄nr+嘲m雌(n1)b・rI;f;…l●…:………::…’…:ff鼹土一:}蜢船‘:}t-'0、h图lO平台底面固支跌落碰撞应变曲线Fig.10Thestraincurvesofthefallingimpactprocessesfortheplanceerfixedplatform:=:‘‘i+Sltmsm-(3202321},)m:Ⅵ∞'&r瞄mI珊%l(恂・&、ml恤・÷…R隅ⅡII^。r/、、…1…●●:l_’●●●●0_:….‘’●●……:・IA婚、^…:j≯0,狮,JS:图l1平台四边固支跌落碰撞应变曲线Fig.11Thestraincurvesofthefallingimpactprocessesforthefouredgesfixedplatform针对头部粘接面剪应力左右对称的分布情况,以垂直中轴面为分界,在一侧半圆粘接面上取12个点进行结果分析。粘接位置剪应力曲线图如图12、图l3所示,平台底面固支跌落碰撞过程观察点的冲击剪应力在±6MPa以内,粘接面最大冲击剪应力发生在5.05ms时,为7.37MPa,位置是45。侧下方的粘接面前端;平台四边固支跌落碰撞过程观察点的—冲击剪应力在一58.2MPa之间,最大冲击剪应力发生在2.2ms时,为8.1MPa,位置出现在头部碰撞点附近。图12平台底面固支粘接位置剪应力曲线Fig.12Thetensorstresscurvesofthespliceplaceofthefallingimpactprocessesfortheplanceerfixedplatform0垃勉nOO4nO060.008Timc/s图13平台四边固支粘接位置剪应力曲线Fig.13Thetensorstresscurvesofthespliceplaceofthefallingimpactprocessesforthefouredgesfixedplatform由上面分析结果可得,水平跌落碰撞过程中,无论平台地面固支还是四边固支,整个碰撞过程持续时间不超过0.01S。因此,C、D两状态分析过程中可将总计算时长调整为0.0115S。2.2C状态:头部向下倾斜1。结果分析头部下倾1。,尾端比头部最低点高约43.11mm,碰撞过程位移曲线如图14所示。大约从1.6ms开始,头部下边缘首先触地,在2.7ms时头部与平台作用达到最大,此时头部垂向直径压缩变形达到最大,为4.571mm,壳体弯曲变形约为4.02mm。。舢甜静船I}{2016年第12期玻璃钢/复合材料95此后,头部受平台反力开始反弹,造成头部向上、尾部向下的旋转加速。4.5ms时,中部下边缘开始触地作用,到5.75ms时,壳体中部位置垂向直径变形达到最大值,约为2.121mm。此时,壳体弯曲变形约为1.84mm,尾部向下的局部速度达到21m/s。在6ms时,尾部下边缘开始触地作用,尾部下边缘受到平台一17000g/0.2ms的强力反作用,速度在0.2ms的时间内由21m/s减为0(此点此时的过载为一16500g/O.2ms)。在6.95ms时,尾部垂向直径变化达到最大值16.549mm,壳体弯曲变形为0.13mm。此后,尾部开始反弹,7.5ms时尾部反弹离开平台,跌落碰撞完毕。■+Dq^q删m"l07360D■目口d■■x【目o删W4988"● ̄aEH日h0Er曩lmm ̄vdeC2177YCm图14头部下倾1。跌落碰撞位移曲线Fig.14Thedisplacementcurvesofthefallingimpactprocessesforthenoseconeleandownside1。由图l5速度曲线分析头部下倾1。跌落碰撞过程,头部、中部上下边缘点的速度变化范围在一6~6m/s之间,而尾部上下边缘点的速度变化范围比较●大,尾部上边缘点速度变化范围为-50~30m/s,▲尾部下边缘点速度变化范围为-30~30m/s,可见头部下倾1。跌落过程是头部、尾部反复弹跳碰撞的复杂过程。+D妇嘣hln缸∞■u0736)0Dqtl-mh%m耐mqm^3)∞D唧删m州m●●畸9嘞Dh嘣n∞∞'哪m掣血-l啦l・D唧Ht^K一■d啦l啦—-叫l弧-8)n}嚣。。:、7一警.__二乞;‘。…………一……………………j.}V…………………_l……………………j..’……。。:一t。。。。:。。Time/s图l5头部下倾1。跌落碰撞速度曲线Fig.15Thevelocitycui'vesofthefallingimpactprocessesforthenoseconeleandownside1。由图16加速度曲线分析头部下倾l。跌落碰撞—过程,头部、中部的碰撞过载大约在一14001500g之间,而尾部碰撞过载则达到一16500~10000g。分析原因是尾部空壳,质量分布密度小,在头部、中部触地作用后,受平台反作用力的叠加碰撞所致。∞0—■&曲tm睁∞-‘:一.一艘≈.hK(1・Yz01・S ̄tmebty-Z0嘲岫…“………‘呻¥∞s崎Y州■Ⅱ■∞Ⅱ。YzCl(H^—‘-j、鞋毅‘曩V-一………………卜专Tj图l6头部下倾l。跌落碰撞加速度曲线●。由图17应力曲线图分析头部下倾1。跌落碰撞过程,头部、中部、尾部7个观察点的最大冲击应力分别为.8、.、.。整个碰撞过程的最大冲击应力发生在头部触地碰撞位置+点附近,在.时的冲击应力达到最大值.。々st瞄“9I懈啪-髑0岫’●s嘛恤nh瞄6jINIns蛔n但口'・Ⅷ一0I'㈣∞・一)图17头部下倾1。跌落冲击应力曲线●1。由图18应变曲线图分析头部下倾1。跌落碰撞过程,头部、中部、尾部7个观察点的最大应变分别为.3%、.6%、.0%。复合材料水雷壳体抗自由跌落冲击性能数值模拟分析2016年12月图18头部下倾1。跌落应变曲线Fig.18Thestraincurvesofthefallingimpactprocessesforthenoseconeleandownside1。由图l9粘接位置剪应力曲线图分析头部下倾1。跌落碰撞过程,头部粘接面冲击剪应力主要分布在-8 ̄10MPa之间,头部下边缘的最大冲击剪应力超出此范围,在3.15ms时达到最大,为17.6MPa。●∞-Ir(19INh●-,_:=篓冀:曼0_-一㈣M口9瞄-w№^_㈣N图19头部下倾1。粘接位置剪应力曲线Fig.19Thetensorstresscurvesofthespliceplaceofthefallingimpactprocessesforthenoseconeleandownside1。2.3D状态:尾部向下倾斜1。结果分析尾部下倾1。,头部比尾部最低点高约43.11mm,碰撞过程位移曲线如图20所示。约从1.5ms开始,尾部下边缘首先开始触地作用。到2.9Ills时,尾部垂向直径变形达到最大值,约为l1.38mill,此时,壳体弯曲变形约为5.32mm。此后,尾部受平台反力开始反弹,造成尾部向上、头部向下的旋转加速。约到4.9ms时,中部下边缘开始触地作用。到6.3ms时,壳体中部垂向直径变形达到最大值,约为2.111mm,此时,壳体弯曲变形约为3.77am,头部下边缘局部向下速度达到13.5m/s,前端面中心局部速度达到17m/s。到6.55ms时,头部下边缘开始触地作用,头部下边缘+点在0.35ms的时间内,速度由13.5m/s减为1.5m/s(此点此时的过载为一5600g/0.35ms)。到7.65ms时,头部垂向直径变化达到最大值,约为8.169mm,壳体弯曲变形约为0.07mm,此后,头部开始反弹。到8.7ms时,头部反弹离开平台,跌落碰撞完毕。图20尾部下倾1。跌落碰撞位移曲线Fig.20Thedisplacementcurvesofthefallingimpactprocessesfortheafterbodyleandownside1。由图21速度曲线图分析尾部下倾1。跌落碰撞过程,中部上下边缘点的速度变化范围为一2.5~7m/s,尾部下边缘点的速度变化范围为-4.2~6.25m/s,尾部上边缘点的速度变化范围为一13.2~9.2m/s,头部的速度变化较为剧烈,头部下边缘点速度变化在一lO.5~13.5m/s之间,头部上边缘点的速度—变化范围在一12.214.2m/s之间,头部前端面中心点速度变化范围为一15.2~16.5m/s。与头部下倾1。跌落过程相类似,尾部下倾1。跌落过程是尾部、头部反复弹跳碰撞的复杂过程。“Ikqedi ̄330)+IkIofot目■—l ̄●■4515)Eknvof^■—嘶l删砷I60)・一厂\△.:;:j!旦’j『V\f…1VTime/s图21尾部下倾1。跌落碰撞速度曲线Fig.21Thevelocitycurvesofthefallingimpactprocessesfortheafterbodyleandownside1。呈差㈣2016年第12期玻璃钢/复合材料97由图22加速度曲线分析尾部下倾1。跌落碰撞—过程,中部碰撞过程过载大约在一1600600g之间,—尾部碰撞过程过载大约在-42202620g之间,头部碰撞过程过载大约在一8000~2030g之间。尾部过载大,是因为尾部壳体壁厚较中部、头部厚一倍,质量分部密度小,刚度大,所以触地碰撞后响应过载较大。头部过载大是因为尾部触地碰撞后,受平台反作用力的叠加作用所致。_^.i..iff、,^.-暑■1.B.i;:iViUIri;i………………rrr}¨¨…Ilme/s图22尾部下倾1。跌落碰撞加速度曲线Fig.22Theaccelerationcurvesofthefallingimpactprocessesfortheafterbodyleandownside1。由图23应力曲线图分析尾部下倾1。跌落碰撞过程,头部、中部、尾部7个观察点的最大冲击应力分别为278MPa、228.2MPa、271.8MPa。整个碰撞过程的最大冲击应力发生在头部触地碰撞位置+点附近,在7.65ms时的vonmiss冲击应力达到最大值918.9MPa。:墨;晶:・§∞∞瑚越1卿-s嗡嘲0【埘1)呻图23尾部下倾l。跌落冲击应力曲线Fig.23Thestresscurvesofthefallingimpactprocessesfortheafterbodyleandownside1。由图24应变曲线图分析尾部下倾l。跌落碰撞过程,头部、中部、尾部7个观察点的最大应变分别为4.77%、0.56%、1.44%。^7f}^-,一、;/|—,::・天毒::_Time/s图24尾部下倾1。跌落碰撞应变曲线Fig.24Thestraincurvesofthefallingimpactprocessesfortheafterbodyleandownside1。由图25粘接位置剪应力曲线图分析尾部下倾l。跌落碰撞过程,头部粘接面冲击剪应力主要分布在-11~12MPa之间,头部下边缘的最大冲击剪应力超出此范围,在7.8ms时达到最大,为52.5MPa。图25尾部下倾1。粘接位置剪应力曲线Fig.25Thetensorstresscurvesofthespliceplaceofthefailingimpactprocessesfortheafterbodyleandownside1。3结果统计分析数值模拟分析的结果统计如表5所示。跌落过程落力为瞬态的冲击应力,不能与材料的静强度进行比较,需要通过一个动载荷等效系数,将其转化为对应的静应力。参照《舰船冲击分析与设计》中美国海军动力设计分析方案(DDAM)对许用应力的规定J,对同轴度精度要求不高的设备和有轻微永久变形的基础极限总应力为材料极限强度的两倍。参照《复合材料爆炸容器的工程设计方法》中对动载荷转化静载荷的描述J,等效系数一般取1/3~1/2。考虑到舰船和爆破容器的安全性要求极高,此处取等效系数0.4进行分析比较。啦llllllllli2l一一98碳纤维环氧树脂复合材料电池箱的轻量化研究2016年12月3.1水平跌落状态从统计结果分析,水平跌落底面固支比四边固支的冲击应力要大些,最大冲击应力为695.63MPa,转化为等效静应力约为278.3MPa,为局部压缩应力,小于头部和筒体材料的极限强度,说明壳体结构的强度可以承受水平跌落碰撞的冲击。水平跌落四边固支的粘接面冲击剪应力分布范围要大些,最大冲击剪应力为8.1MPa,转化为静态等效剪应力为3.24MPa,小于粘接胶的抗剪强度22MPa,壳体粘接面可以承受水平跌落碰撞的冲击。水平跌落四边固支比底面固支的弯曲变形要大,最大弯曲变形为4.76mm,壳体长度为2.8m,弯曲变形量与壳体长度的比率为0.17%。由于壳体尾部300mm范围为空壳,所以尾部径向变形较大。径向最大变形量为平台四边固支水平跌落过程中尾部二次触地碰撞时的变形,为5.05ms/7.65mm,壳体直径为534mm,则变形比率为1.43%。实际使用状态尾部要安装尾盖,尾盖止口与壳体尾端面和内表面装配配合,会增加壳体尾部的刚度。去除尾部空壳影响,最大径向变形为3.91mm,与直径的变形比率为0.73%。3.2头部下倾l。跌落状态在头部下倾l。跌落过程中,7个观测点的最大冲击应力为356.9MPa,转化为等效静应力为142.8MPa,说明观察点位置安全。最大冲击应力发生在头部触地位置2.6ms,为793.7MPa,转化为等效静应力约为317.5MPa,小于头部材料的极限强度371MPa,说明壳体结构的强度可以承受头部下倾1。跌嘲酾落碰撞的冲击。跌落碰撞过程中,粘接面的最大冲击剪应力为17.6MPa,等效静态剪应力为7.04MPa,小于粘接胶的抗剪强度22MPa,壳体粘接面可以承受头部下倾1。跌落碰撞的冲击。跌落碰撞过程最大弯曲变形为2.7ms头部触地碰撞时,为3.98mm,对应的变形比率为0.14%。头部、中部、尾部触地碰撞时,径向变形分别为4.57mm、2.12mm、16.55mm,对应的变形比率分别为0.86%、0.4%、3.1%。3.3尾部下倾1。跌落状态在尾部下倾1。跌落过程中,7个观测点的最大冲击应力为278.1MPa,转化为等效静应力为111.3MPa,说明观察点位置安全。最大冲击应力发生在头部触地位置7.65ms,为918.9MPa,转化为等效静应力约为367.6MPa,小于头部材料的极限强度371MPa,说明壳体结构的强度可以承受尾部下倾l。跌落碰撞的冲击。跌落碰撞过程中,粘接面的最大冲击剪应力为52.75MPa,等效静态剪应力为21.1MPa,小于粘接胶的抗剪强度22MPa,壳体粘接面可以承受尾部下倾1。跌落碰撞的冲击。但是,尾部下倾1。跌落碰撞筒体的VOIltmiss应力和粘接面的剪应力均已接近材料的极限强度。跌落碰撞过程最大弯曲变形为2.9ms尾部触地碰撞时,为5.32mm,对应的变形比率为0.19%。头部、中部、尾部触地碰撞时,径向变形分别为8.17mm、2.11mm、11.4mm,对应的变形比率分别为1.53%、0.4%、2.13%。(下转第22页)22温度-荷载耦合作用下GFRP-泡沫夹层结构I型断裂理论研究2016年l2月—tios,highstiffnesstoweightratios,anticorrosionabilityandothercharacteristics.However,thestructuresarefacedwithavarietyofinjuriesunderactiveconditions.Actually,intheexistingapplications,theopentypedelamination(modeIinterfacialdelamination)betweenthesurfacelayerandthecorematerialisacommonfailuremodeunderthecouplingeffectsoftemperatureandloads.Basedonconservationofenergyandelasticfoundationbeamtheory,expressionofstrainenergyreleaserateisanalyzed,whilethecrackbetweenthesurfacelayerandthecorematerialisexpending.Atthesanletime,accordingtothecontrastiveanalysisbetweenthecalculatedvaluesandexperimentalvaluesofsandwichdoublecantileverbeam(DCB),thecorrectnessoftheexpressionofstrainenergyreleaserateunderthecouplingeffectsoftemperatureandloadscanbeverified.Keywords:sandwichstructure;doublecantileverbeam;strainenergyreleaserate;elasticfoundationbeamtheorymodel(上接第98页)4结论通过上述水雷壳体不同跌落状态碰撞过程的数值模拟及结果统计分析,可以得出以下结论:(1)水雷壳体可以承受2m水平自由跌落的碰撞冲击,壳体不破坏、不损伤;(2)碰撞地面的刚度对碰撞过程的时间、过载、位移、变形等影响较大,地面刚度小,可以起到缓冲作用,降低碰撞冲击过程的过载和变形;(3)水雷壳体跌落的姿态对跌落过程的碰撞冲击影响较大,水雷壳体可以承受头部下倾1。和尾部下倾1。的2m自由跌落的碰撞冲击,壳体不破坏、不损伤;但是头部下倾l。和尾部下倾1。的冲击应力和粘接面的剪应力已经接近了材料的极限强度。参考文献[1]寇晓东,唐可,田彩军.ALGOR结构分析高级教程[M].第一—版.北京:清华大学出版社,2008:267486.[2]周康,赵本立,李玉节,等译.舰船冲击分析与设计[M].哈尔—滨:哈尔滨工程大学出版社,2006:106109.[3]廖英强,韩建平,苏建河.复合材料爆炸容器的工程设计方法[J].火工品,2006(4):1-8.IMPACTSIMULATl0NANALYSISFORFREEFALLGSTATUSoFCoMPOSIIETORPEDOSHELL—ZONGfangyong,CHAIPeng-jun(1.NavySMilitaryRepresentativeOfficeinChongqing662Factory,Chongqing432111,China;2.BeijingCompositeMaterialCo.,Ltd.,Beijng102101,China)Abstract:Thedropprocessesofcompositetorpedoshellincludingfreefallingstatus,contactingwithground—status,impactingongroundstatusandstressingstatusweresimulatedbythenonlinearmaterialmoduleofmechani—calmotioninALGOR.Theeffectofgroundanddroppostureonthecompositetorpedoshellduringthedroppingwasinvestigatedbysimulatingthefourstatusesrespectively.Basedonthecomparisonandanalysisofsimulationresults,includingforce,stress,strainanddisplacement,thedroppingresistancepropertiesoftorpedocompositeshellwereobtained,whichwasusedtoevaluatetheimpactperformanceofcompositetorpedoshel1.—Keywords:composites;torpedoshell;freefalldropping;impact
您可能关注的文档
- “离位”增韧复合材料准静态压入损伤特性研究.pdf
- “神舟七号”飞船舱外航天服防护头盔组件的研制.pdf
- “十二五”复合材料发展重点和方向解读.pdf
- “珠串”堆叠超结构的介孔铁酸锌的制备与表征.pdf
- (001)应变对正交相Ca2 P0.25 Si0.75能带结构及光学性质的影响.pdf
- 0.8设计系数用X80管线钢在近中性pH溶液中的应力腐蚀开裂行为.pdf
- 0.20mm CGO硅钢高温退火Goss晶粒起源及异常长大行为研究.pdf
- 0Cr16Ni5Mo低碳马氏体不锈钢的热变形行为及其热加工图.pdf
- 0Cr17Ni4Cu4Nb钢制螺钉断裂原因分析.pdf
- 1.5MW风机叶片模具加热工艺研究与技术创新.pdf
- 1.5MW风机叶片VARI工艺模拟分析及验证.pdf
- 2.5维机织复合材料低速冲击性能研究.pdf
- 2.25Cr-1Mo钢后续热处理中的磷偏聚行为.pdf
- 2A50锻铝三点弯曲试验与高分辨率CT成像分析.pdf
- 2A12与2A11铝合金超声波焊接工艺与组织研究.pdf
- 2MW风机复合材料叶片材料及工艺研究.pdf
- 3Cr2W8V模具钢激光表面相变硬化层性能的研究.pdf
- 3D打印技术及先进应用研究进展.pdf
- 3D打印技术研究现状和关键技术.pdf
- 5%鱼藤酮悬浮剂的研制.pdf

- 富富资料
- 该用户很懒,什么也没介绍
相关文档
- “离位”增韧复合材料准静态压入损伤特性研究.pdf2021-11-235页
- “神舟七号”飞船舱外航天服防护头盔组件的研制.pdf2021-11-233页
- “十二五”复合材料发展重点和方向解读.pdf2021-11-232页
- “珠串”堆叠超结构的介孔铁酸锌的制备与表征.pdf2021-11-235页
- (001)应变对正交相Ca2 P0.25 Si0.75能带结构及光学性质的影响.pdf2021-11-236页
- 0.8设计系数用X80管线钢在近中性pH溶液中的应力腐蚀开裂行为.pdf2021-11-237页
- 0.20mm CGO硅钢高温退火Goss晶粒起源及异常长大行为研究.pdf2021-11-237页