- 文档大小:337.41 KB
- 文档格式:pdf
- 约 5页
- 2022-04-11 发布
- 举报
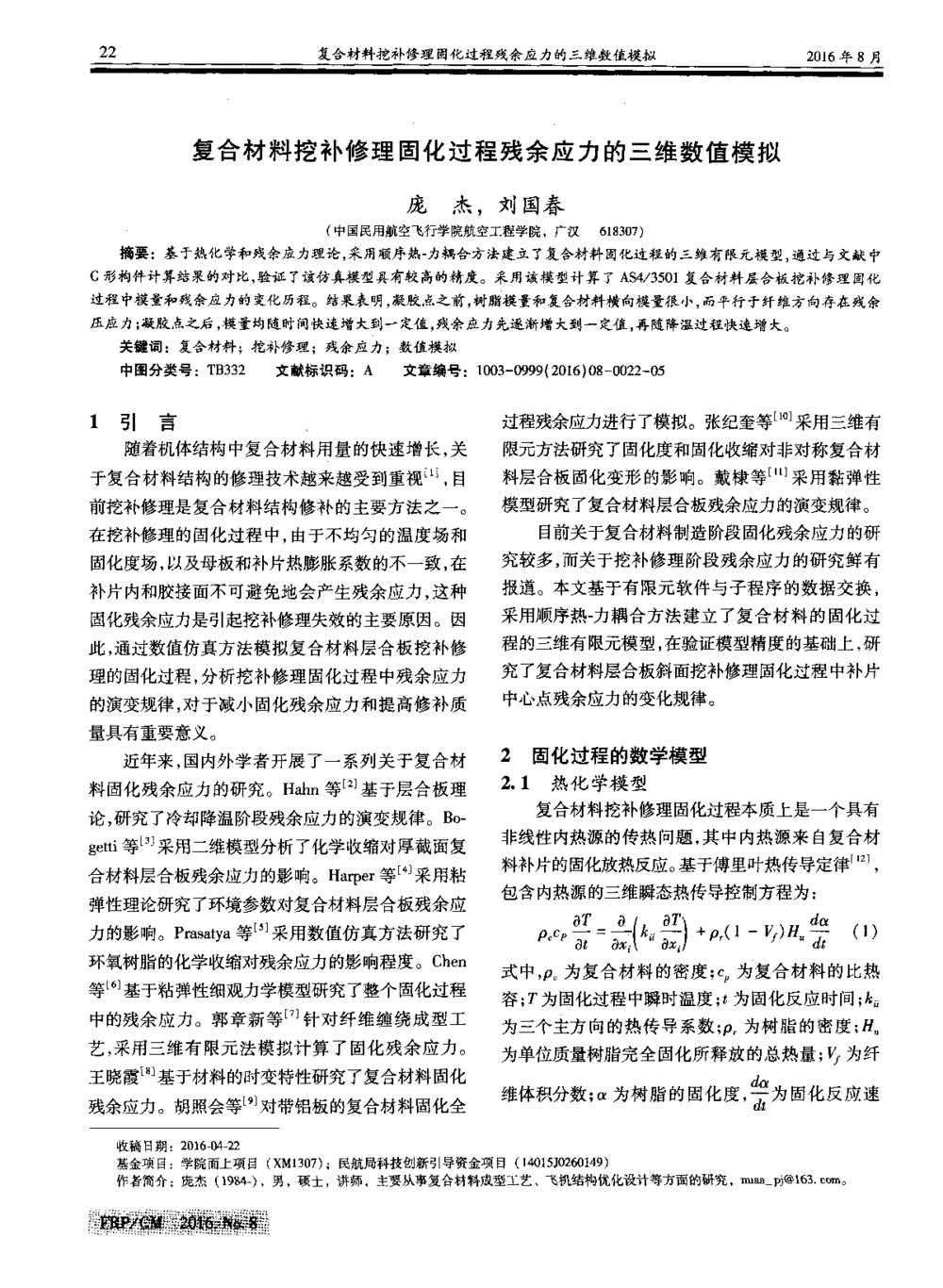
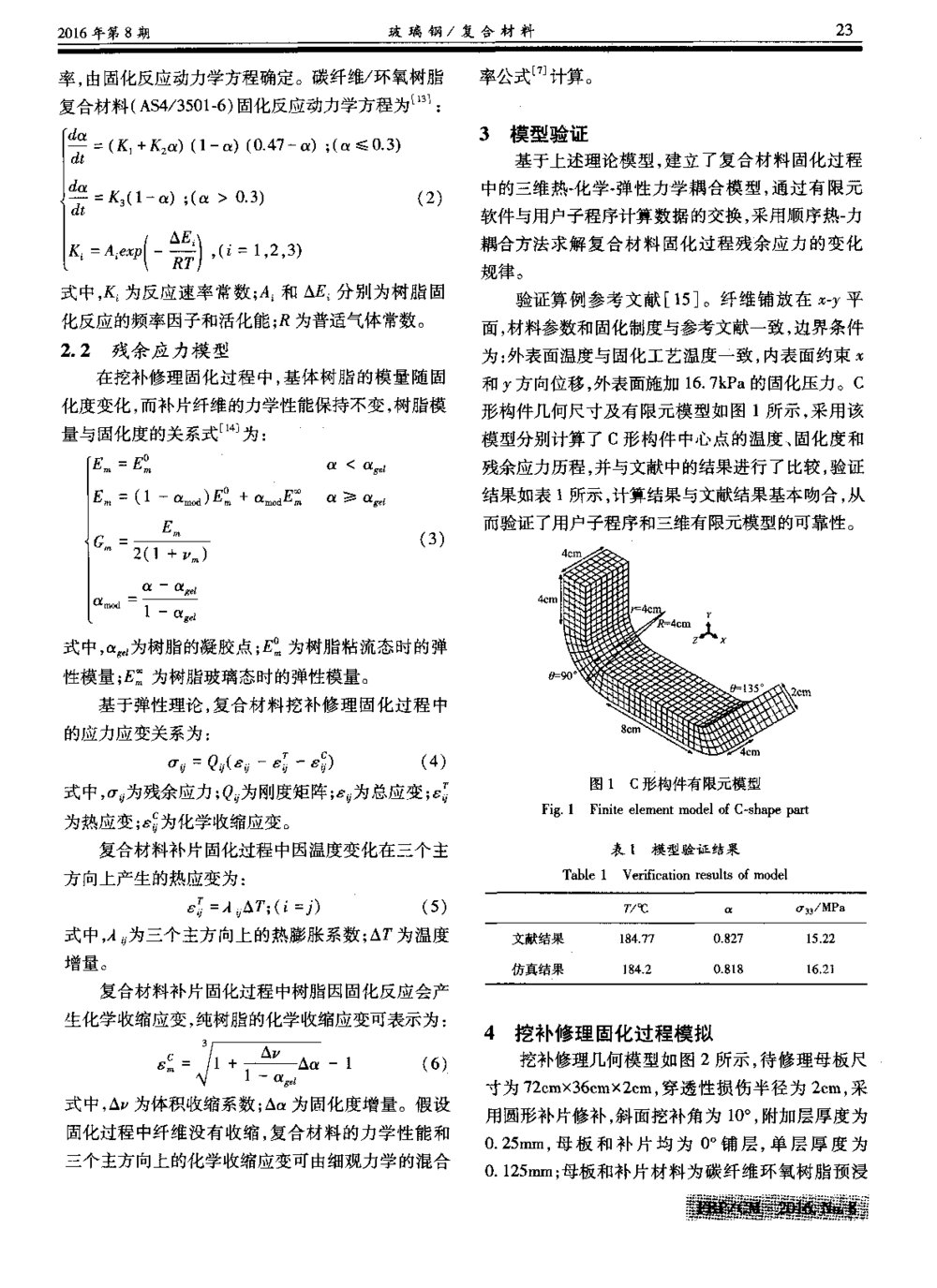
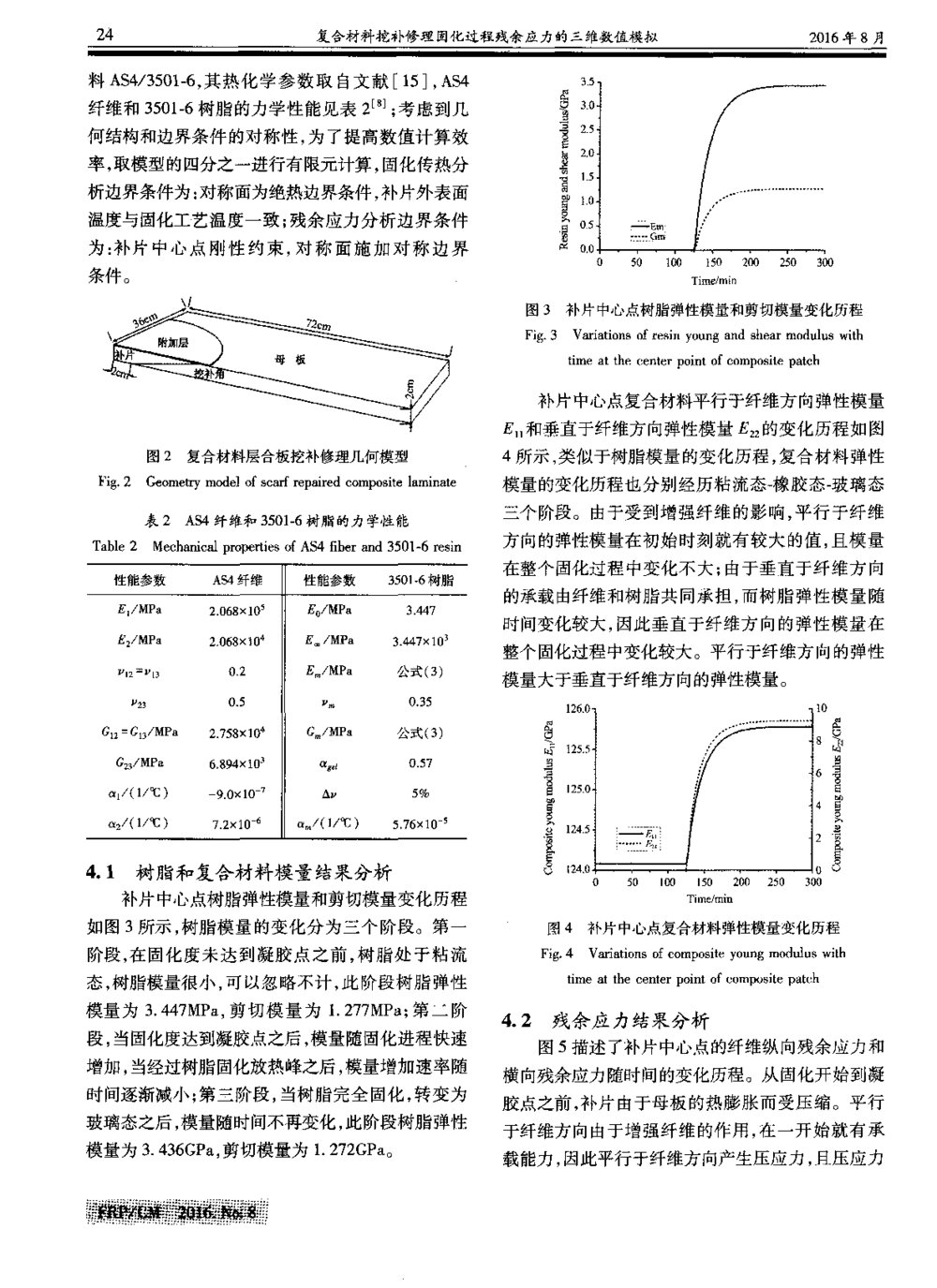
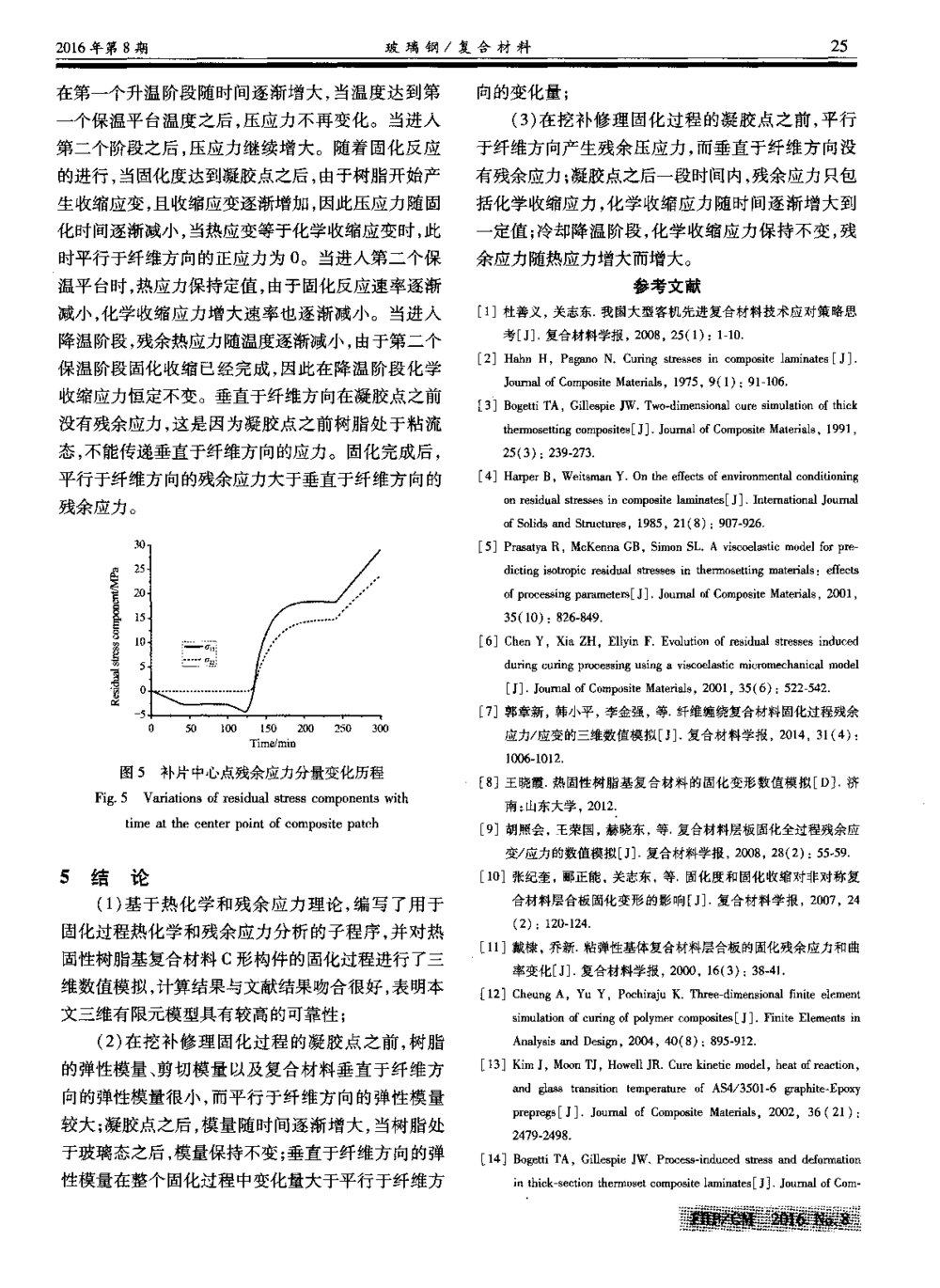
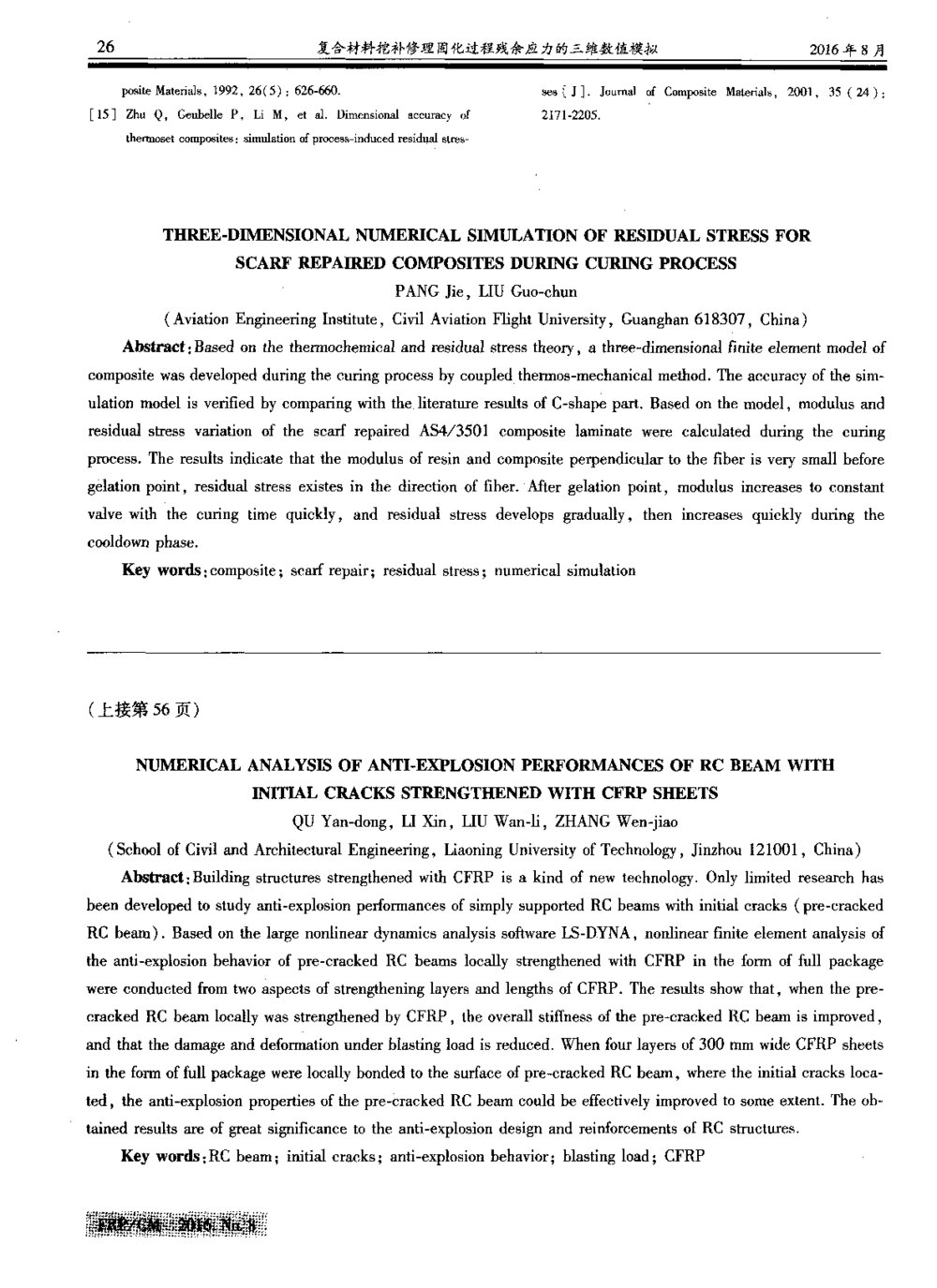
已阅读完毕,您还可以下载文档进行保存
- 1、本文档共5页,内容下载后可编辑。
- 2、本文档内容版权归属内容提供方,所产生的收益全部归内容提供方所有。如果您对本文有版权争议,可选择认领。
- 3、本文档由用户上传,本站不保证质量和数量令人满意,可能有诸多瑕疵,付费之前,请仔细先通过免费阅读内容等途径辨别内容交易风险。如存在严重挂羊头卖狗肉之情形,可联系本站下载客服投诉处理。
22 复合材料挖补修理固化过程残余应力的三维数值模拟 2016年8月 复合材料挖补修理固化过程残余应力的三维数值模拟 庞杰,刘国春 (中国民用航空飞行学院航空工程学院,广汉618307) 摘要:基于热化学和残余应力理论,采用顺序热一力耦合方法建立了复合材料固化过程的三维有限元模型,通过与文献中 c形构件计算结果的对比,验证了该仿真模型具有较高的精度。采用该模型计算了AS4/3501复合材料层合板挖补修理固化 过程中模量和残余应力的变化历程。结果表明,凝胶点之前,树脂模量和复合材料横向模量很小,而平行于纤维方向存在残余 压应力;凝胶点之后,模量均随时间快速增大到一定值,残余应力先逐渐增大到一定值,再随降温过程快速增大。 关键词:复合材料;挖补修理;残余应力;数值模拟 —— 中图分类号:TB332文献标识码:A文章编号:1003-0999(2016)08002205 1引言 随着机体结构中复合材料用量的快速增长,关 于复合材料结构的修理技术越来越受到重视【1J,目 前挖补修理是复合材料结构修补的主要方法之一。 在挖补修理的固化过程中,由于不均匀的温度场和 固化度场,以及母板和补片热膨胀系数的不一致,在 补片内和胶接面不可避免地会产生残余应力,这种 固化残余应力是引起挖补修理失效的主要原因。因 此,通过数值仿真方法模拟复合材料层合板挖补修 理的固化过程,分析挖补修理固化过程中残余应力 的演变规律,对于减小固化残余应力和提高修补质 量具有重要意义。 近年来,国内外学者开展了一系列关于复合材 料固化残余应力的研究。Hahn等_2基于层合板理— 论,研究了冷却降温阶段残余应力的演变规律。Bo getti等采用二维模型分析了化学收缩对厚截面复 合材料层合板残余应力的影响。Harper等采用粘 弹性理论研究了环境参数对复合材料层合板残余应 力的影响。Prasatya等采用数值仿真方法研究了 环氧树脂的化学收缩对残余应力的影响程度。Chen 等基于粘弹性细观力学模型研究了整个固化过程 中的残余应力。郭章新等【针对纤维缠绕成型工 艺,采用三维有限元法模拟计算了固化残余应力。 王晓霞基于材料的时变特性研究了复合材料固化 残余应力。胡照会等对带铝板的复合材料固化全过程残余应力进行了模拟。张纪奎等¨ 。。采用三维有 限元方法研究了固化度和固化收缩对非对称复合材 料层合板固化变形的影响。戴棣等¨ u采用黏弹性 模型研究了复合材料层合板残余应力的演变规律。 目前关于复合材料制造阶段固化残余应力的研 究较多,而关于挖补修理阶段残余应力的研究鲜有 报道。本文基于有限元软件与子程序的数据交换, 采用顺序热一力耦合方法建立了复合材料的固化过 程的三维有限元模型,在验证模型精度的基础上,研 究了复合材料层合板斜面挖补修理固化过程中补片 中心点残余应力的变化规律。 2固化过程的数学模型 2.1热化学模型 复合材料挖补修理固化过程本质上是一个具有 非线性内热源的传热问题,其中内热源来自复合材 料补片的固化放热反应。基于傅里叶热传导定律, 包含内热源的三维瞬态热传导控制方程为:: 去差)+・一)dot(1) 式中,P为复合材料的密度;Cp为复合材料的比热 容;T为固化过程中瞬时温度;t为固化反应时间;k 为三个主方向的热传导系数;p为树脂的密度; 为单位质量树脂完全固化所释放的总热量;为纤 维体积分数;为树脂的固化度,为固化反应速 — 收稿日期:2016-0422 基金项目:学院面上项目(XM1307);民航局科技创新引导资金项目(14015J0260149) 作者简介:庞杰(1984一),男,硕士,讲师,主要从事复合材料成型工艺、飞机结构优化设计等方面的研究,Yftl ̄一pj@63.com。 嘶嘲潮蛹麓 2016年第8期 玻璃钢/复合材料 23 率,由固化反应动力学方程确定。碳纤维/环氧树脂率公式计算。 — 复合材料(As4/35016)固化反应动力学方程为: — ≤ Idot=(K+Kz0[)(1-ot)(0.470c).(o.3) {dot=g3(1一).(>0.3) (2) =Ai叫一面AEi)=・,2,3 式中,Ki为反应速率常数;A和AE分别为树脂固 化反应的频率因子和活化能;R为普适气体常数。 2.2残余应力模型 在挖补修理固化过程中,基体树脂的模量随固 化度变化,而补片纤维的力学性能保持不变,树脂模 量与固化度的关系式H为: E=Eo < E=(1一otmod)E+otmodE ̄≥ 0cf ㈩— ‰ od 式中,为树脂的凝胶点;E为树脂粘流态时的弹 性模量;为树脂玻璃态时的弹性模量。 基于弹性理论,复合材料挖补修理固化过程中 的应力应变关系为: =Q(一一;) (4) 式中,残余应力;Q刚度矩阵;为总应变;占; 为热应变;占为化学收缩应变。 复合材料补片固化过程中因温度变化在三个主 方向上产生的热应变为: s:=AAT;(i=) (5) △ 式中,/i为三个主方向上的热膨胀系数;为温度 增量。 复合材料补片固化过程中树脂因固化反应会产 生化学收缩应变,纯树脂的化学收缩应变可表示为: —————— ———— 3r_一C= /1+ 一1 (6)√ ^l— otgel△ 式中,为体积收缩系数;Aot为固化度增量。假设 固化过程中纤维没有收缩,复合材料的力学性能和 三个主方向上的化学收缩应变可由细观力学的混合 3模型验证 基于上述理论模型,建立了复合材料固化过程 中的三维热化学.弹性力学耦合模型,通过有限元 软件与用户子程序计算数据的交换,采用顺序热-力 耦合方法求解复合材料固化过程残余应力的变化 规律。 验证算例参考文献[15]。纤维铺放在-Y平 面,材料参数和固化制度与参考文献一致,边界条件 为:外表面温度与固化工艺温度一致,内表面约束 和Y方向位移,外表面施加16.7kPa的固化压力。c 形构件几何尺寸及有限元模型如图1所示,采用该 模型分别计算了c形构件中心点的温度、固化度和 残余应力历程,并与文献中的结果进行了比较,验证 结果如表1所示,计算结果与文献结果基本吻合,从 而验证了用户子程序和三维有限元模型的可靠性。 图1C形构件有限元模型 — Fig.1FiniteelementmodelofCshapepart 表1模型验证结果 TablelVerificationresultsofmodel 4挖补修理固化过程模拟 挖补修理几何模型如图2所示,待修理母板尺寸为72cm ̄36cmx2er a,穿透性损伤半径为2cm,采 用圆形补片修补,斜面挖补角为10。,附加层厚度为 0.25mm,母板和补片均为0。铺层,单层厚度为 0.125mm;母板和补片材料为碳纤维环氧树脂预浸 复合材料挖补修理固化过程残余应力的三维数值模拟 2016年8月 料AS4/3501-6,其热化学参数取自文献[15],AS4 — 纤维和35016树脂的力学性能见表2_8;考虑到几 何结构和边界条件的对称性,为了提高数值计算效 率,取模型的四分之一进行有限元计算,固化传热分 析边界条件为:对称面为绝热边界条件,补片外表面 温度与固化工艺温度一致;残余应力分析边界条件 为:补片中心点刚性约束,对称面施加对称边界 条件。 图2复合材料层合板挖补修理几何模型 Fig.2Geometrymodelofscarfrepairedcompositelaminate 表2AS4纤维和3501.6树脂的力学性能 Table2MechanicalpropertiesofAS4f iberand3501-6resin 性能参数 AS4纤维 性能参数 3501.6树脂 El/MPa2. 068x105 E0/MPa 3.447 E2/MPa2. 068 ̄10 E/MPa 3.447 ̄103 /J121-'13 0.2 E/MPa 公式(3) 1)23 0.5 0.35 Gl2=Gl3/MPa2. 758x10 G/MPa 公式(3) G23/MPa6. 894 ̄103 l O.571 /(1/ ̄C)一9.0× 10一 Av 5% 2/(1/ ̄C)7.2× 10一 /(1/ ̄C) 5.76x10一 4.1树脂和复合材料模量结果分析 补片中心点树脂弹性模量和剪切模量变化历程 如图3所示,树脂模量的变化分为三个阶段。第一 阶段,在固化度未达到凝胶点之前,树脂处于粘流 态,树脂模量很小,可以忽略不计,此阶段树脂弹性 模量为3.447MPa,剪切模量为1.277MPa;第二阶 段,当固化度达到凝胶点之后,模量随固化进程快速 增加,当经过树脂固化放热峰之后,模量增加速率随 时间逐渐减小;第三阶段,当树脂完全固化,转变为 玻璃态之后,模量随时间不再变化,此阶段树脂弹性 模量为3.436GPa,剪切模量为1.272GPa。 0 5O 10o l50200 250 300 Time/min 图3补片中心点树脂弹性模量和剪切模量变化历程 Fig.3Variationsofresinyoungandshearmoduluswith timeatthecenterpointofcompositepatch 补片中心点复合材料平行于纤维方向弹性模量 E。。和垂直于纤维方向弹性模量E的变化历程如图 4所示,类似于树脂模量的变化历程,复合材料弹性 模量的变化历程也分别经历粘流态橡胶态.玻璃态 三个阶段。由于受到增强纤维的影响,平行于纤维 方向的弹性模量在初始时刻就有较大的值,且模量 在整个固化过程中变化不大;由于垂直于纤维方向 的承载由纤维和树脂共同承担,而树脂弹性模量随 时间变化较大,因此垂直于纤维方向的弹性模量在 整个固化过程中变化较大。平行于纤维方向的弹性 模量大于垂直于纤维方向的弹性模量。 125.5 125.0 124.5 l240 0 5O 10o l50 200250 300 Time/min 图4补片中心点复合材料弹性模量变化历程 Fig.4Variationsofcompositeyoungmoduluswith timeatthecenterpointofcompositepatch 4.2残余应力结果分析 图5描述了补片中心点的纤维纵向残余应力和 横向残余应力随时间的变化历程。从固化开始到凝 胶点之前,补片由于母板的热膨胀而受压缩。平行 于纤维方向由于增强纤维的作用,在一开始就有承 载能力,因此平行于纤维方向产生压应力,且压应力 5 O 5 O 5 O 5 O 3 3 2 2 1 l 0 O 叠0藿 ∞ 口gg0,( 耐d[ 兰jp0暑锄量o 金异嚣u 2016年第8期 玻璃钢/复合材料 25 在第一个升温阶段随时间逐渐增大,当温度达到第一 个保温平台温度之后,压应力不再变化。当进入 第二个阶段之后,压应力继续增大。随着固化反应 的进行,当固化度达到凝胶点之后,由于树脂开始产 生收缩应变,且收缩应变逐渐增加,因此压应力随固 化时间逐渐减小,当热应变等于化学收缩应变时,此 时平行于纤维方向的正应力为0。当进入第二个保 温平台时,热应力保持定值,由于固化反应速率逐渐 减小,化学收缩应力增大速率也逐渐减小。当进入 降温阶段,残余热应力随温度逐渐减小,由于第二个 保温阶段固化收缩已经完成,因此在降温阶段化学 收缩应力恒定不变。垂直于纤维方向在凝胶点之前 没有残余应力,这是因为凝胶点之前树脂处于粘流 态,不能传递垂直于纤维方向的应力。固化完成后, 平行于纤维方向的残余应力大于垂直于纤维方向的 残余应力。 0 50 100 150 200 250 300 Time/min 图5补片中心点残余应力分量变化历程 Fig.5Variationsofresidualstresscomponentswith timeatthecenterpointofcompositepatch 5结论 (1)基于热化学和残余应力理论,编写了用于 固化过程热化学和残余应力分析的子程序,并对热 固性树脂基复合材料C形构件的固化过程进行了三 维数值模拟,计算结果与文献结果吻合很好,表明本 文三维有限元模型具有较高的可靠性; (2)在挖补修理固化过程的凝胶点之前,树脂 的弹性模量、剪切模量以及复合材料垂直于纤维方 向的弹性模量很小,而平行于纤维方向的弹性模量 较大;凝胶点之后,模量随时间逐渐增大,当树脂处 于玻璃态之后,模量保持不变;垂直于纤维方向的弹 性模量在整个固化过程中变化量大于平行于纤维方 向的变化量; (3)在挖补修理固化过程的凝胶点之前,平行 于纤维方向产生残余压应力,而垂直于纤维方向没 有残余应力;凝胶点之后一段时间内,残余应力只包 括化学收缩应力,化学收缩应力随时间逐渐增大到一 定值;冷却降温阶段,化学收缩应力保持不变,残 余应力随热应力增大而增大。 参考文献 [1]杜善义,关志东.我国大型客机先进复合材料技术应对策略思 考[J].复合材料学报,2008,25(1):1-10. [2]HahnH,PaganoN.Curingstressesincompositelaminates[J]. — JournalofCompositeMaterials,1975,9(1):91106. [3]BogettiTA,GiUespieJW.Two-dimensionalcuresimulationofthick thermoseRingcomposites[J].Jour nalofComp ositeMater ials,1991, 25(3):239・273. [4]HarperB,WeitsmanY.Ontheeffectsofenvironmentalconditioning onresidualstr essesincompositelaminates[J].InternationalJournal ofSolidsandStructures,1985,21(8):907-926. — [5]PrasatyaR,McKennaGB,SimonSL.Aviscoelasticmodelforpre dictingisotropieresidualsti ̄ssesinthermosettingmaterials:effects ofprocessingparametem[J].JournalofCompositeMaterials,2001,— 35(10):826849. [6]ChenY,XiaZH,EUyinF.Evolutionofresidualstressesinduced duringcuringprocessingusingaviscoelasticmicromechanica lmodel [J].JournalofCompositeMaterials,2001,35(6):522-542. [7]郭章新,韩小平,李金强,等.纤维缠绕复合材料固化过程残余 应力/应变的三维数值模拟[J].复合材料学报,2014,31(4):— 10061012. [8]王晓霞.热固性树脂基复合材料的固化变形数值模拟[D].济 南:山东大学,2012. [9]胡照会,王荣国,赫晓东,等.复合材料层板固化全过程残余应 变/应力的数值模拟[J].复合材料学报,2008,28(2):55-59. [1O]张纪奎,郦正能,关志东,等.固化度和固化收缩对非对称复 合材料层合板固化变形的影响[J].复合材料学报,2007,24 (2):120・124. [11]戴棣,乔新.粘弹性基体复合材料层合板的固化残余应力和曲 率变化[J].复合材料学报,2000,16(3):38.41. — [12]CheungA,YuY,PochirajuK.Threedimensionalf initeelement simulationofcuringofpolymercomposites[J].FiniteElementsin AnalysisandDesign,2004,40(8):895-912. [13]KimJ,MoonTJ,HowellJR.Curekineticmodel,heatofreaction, andasstransitiontemperatureofAS4/3501・6graphite・Epoxy prepregs[J].JournalofCompositeMater ials,2002,36(21): 2479.2498. — [14]BogettiTA,GillespieJW,Processinducedstressanddeformation — inthicksectiont hermosetcompositelaminates[J].JournalofCom一∞ 加∞ 0 Bd ∞∞ ∞gg8尝一§ p18 26 复合材料挖补修理固化过程残余应力的三维数值模拟 2016年8月 — positeMaterials,1992,26(5):626660. [15]ZhuQ,GeubelleP,LiM,eta1.Dimensionalaccuracyof — — thermosetcomposites:simulationofprocessinducedresidualstres ses[J].JournalofCompositeMaterials,2001,35(24)— 21712205. THREE-DIMENSIONALNUMERICALSIMULATIoNoFRESIDUALSTRESSFoR SCARFREPAIREDCoMPoSITESDURINGCURINGPRoCESS — PANGJie,LIUGuochun (AviationEngineeringInstitute,CivilAviationFlightUniversity,Guanghan618307,China) — Abstract:Basedonthethermochemicalandresidualstresstheory,athreedimensionalf initeelementmodelof compositewasdevelopeddur — — ingthecuringprocessbycoupledthermosmechanicalmethod.Theaccuracyofthesim — ulationmodelisverifiedbycomparingwiththeliteratureresultsofCshapepart.Basedonthemodel,modulusandresidua lstressvariationofthescar frepairedAS4/3501compositelaminatewerecalculatedduringthecur ing process.Theresultsindicatethatthemodulusofresinandcompositeperpendiculartothef iberisverysmallbefore gelationpoint,residualstressexistesinthedirectionoffiber.Aftergelationpoint,modulusincreasestoconstant valvewiththecuringtimequickly,andresidualstressdevelopsgradually,thenincreasesquicklydur ingthe cooldownphase. Keywords:composite;scarfrepair;residualstress;numer icalsimulation (上接第56页) UM【ERICALANALYSISOFANTI-EXPLoS10PERFOI僵ACESoFRCBEAMWITH INITIALCRACKSSTRENGTHENEDWITHCFRPSHEETS — QUYahdong,LIXin,LIUWan・li,ZHANGWen-jiao (SchoolofCivilandArchitecturalEngineering,LiaoningUniversityofTechnology,Jinzhou121001,China) Abstract:BuildingstructuresstrengthenedwithCFRPisakindofnewtechnolog y.Onlylimitedresearchhas beendevelopedtostudyanti-explosionperformancesofsimplysupportedRCbeamswithinitialcracks(pre-cracked — RCbeam).BasedonthelargenonlineardynamicsanalysissoftwareLSDYNA。nonlinearfiniteelementanalysisof theanti・・explosionbehaviorofpre--crackedRCbeamslocallystrengthenedwithCFRPintheformoffullpackage — wereconductedfromtwoaspectsofstrengtheninglayersandlengthsofCFRP.Theresultsshowthat,whenthepre — crackedRCbeamlocallywasstrengthenedbyCFRP,theoverallstiffnessoftheprecrackedRCbeamisimproved, andthatthedamageanddeformationunderblastingloadisreduced.Whenfourlayersof300mmwideCFRPsheets — — intheformoffullpackagewerelocallybondedtothesurfaceofprecrackedRCbeam,wheretheinitialcracksloca — — ted,theanti-explosionpropertiesofthepreCrackedRCbeamcouldbeeffectivelyimprovedtosomeextent.Theob — tainedresultsareofgreatsignificancetotheantiexplosiondesignandreinforcementsofRCstructures. — Keywords:RCbeam;initialcracks;antiexplosionbehavior;blastingload;CFRP
您可能关注的文档
- “离位”增韧复合材料准静态压入损伤特性研究.pdf
- “神舟七号”飞船舱外航天服防护头盔组件的研制.pdf
- “十二五”复合材料发展重点和方向解读.pdf
- “珠串”堆叠超结构的介孔铁酸锌的制备与表征.pdf
- (001)应变对正交相Ca2 P0.25 Si0.75能带结构及光学性质的影响.pdf
- 0.8设计系数用X80管线钢在近中性pH溶液中的应力腐蚀开裂行为.pdf
- 0.20mm CGO硅钢高温退火Goss晶粒起源及异常长大行为研究.pdf
- 0Cr16Ni5Mo低碳马氏体不锈钢的热变形行为及其热加工图.pdf
- 0Cr17Ni4Cu4Nb钢制螺钉断裂原因分析.pdf
- 1.5MW风机叶片模具加热工艺研究与技术创新.pdf
- 1.5MW风机叶片VARI工艺模拟分析及验证.pdf
- 2.5维机织复合材料低速冲击性能研究.pdf
- 2.25Cr-1Mo钢后续热处理中的磷偏聚行为.pdf
- 2A50锻铝三点弯曲试验与高分辨率CT成像分析.pdf
- 2A12与2A11铝合金超声波焊接工艺与组织研究.pdf
- 2MW风机复合材料叶片材料及工艺研究.pdf
- 3Cr2W8V模具钢激光表面相变硬化层性能的研究.pdf
- 3D打印技术及先进应用研究进展.pdf
- 3D打印技术研究现状和关键技术.pdf
- 5%鱼藤酮悬浮剂的研制.pdf

- 分享达人
- 该用户很懒,什么也没介绍
相关文档
- “离位”增韧复合材料准静态压入损伤特性研究.pdf2021-11-235页
- “神舟七号”飞船舱外航天服防护头盔组件的研制.pdf2021-11-233页
- “十二五”复合材料发展重点和方向解读.pdf2021-11-232页
- “珠串”堆叠超结构的介孔铁酸锌的制备与表征.pdf2021-11-235页
- (001)应变对正交相Ca2 P0.25 Si0.75能带结构及光学性质的影响.pdf2021-11-236页
- 0.8设计系数用X80管线钢在近中性pH溶液中的应力腐蚀开裂行为.pdf2021-11-237页
- 0.20mm CGO硅钢高温退火Goss晶粒起源及异常长大行为研究.pdf2021-11-237页