- 文档大小:753.58 KB
- 文档格式:pdf
- 约 6页
- 2022-04-11 发布
- 举报
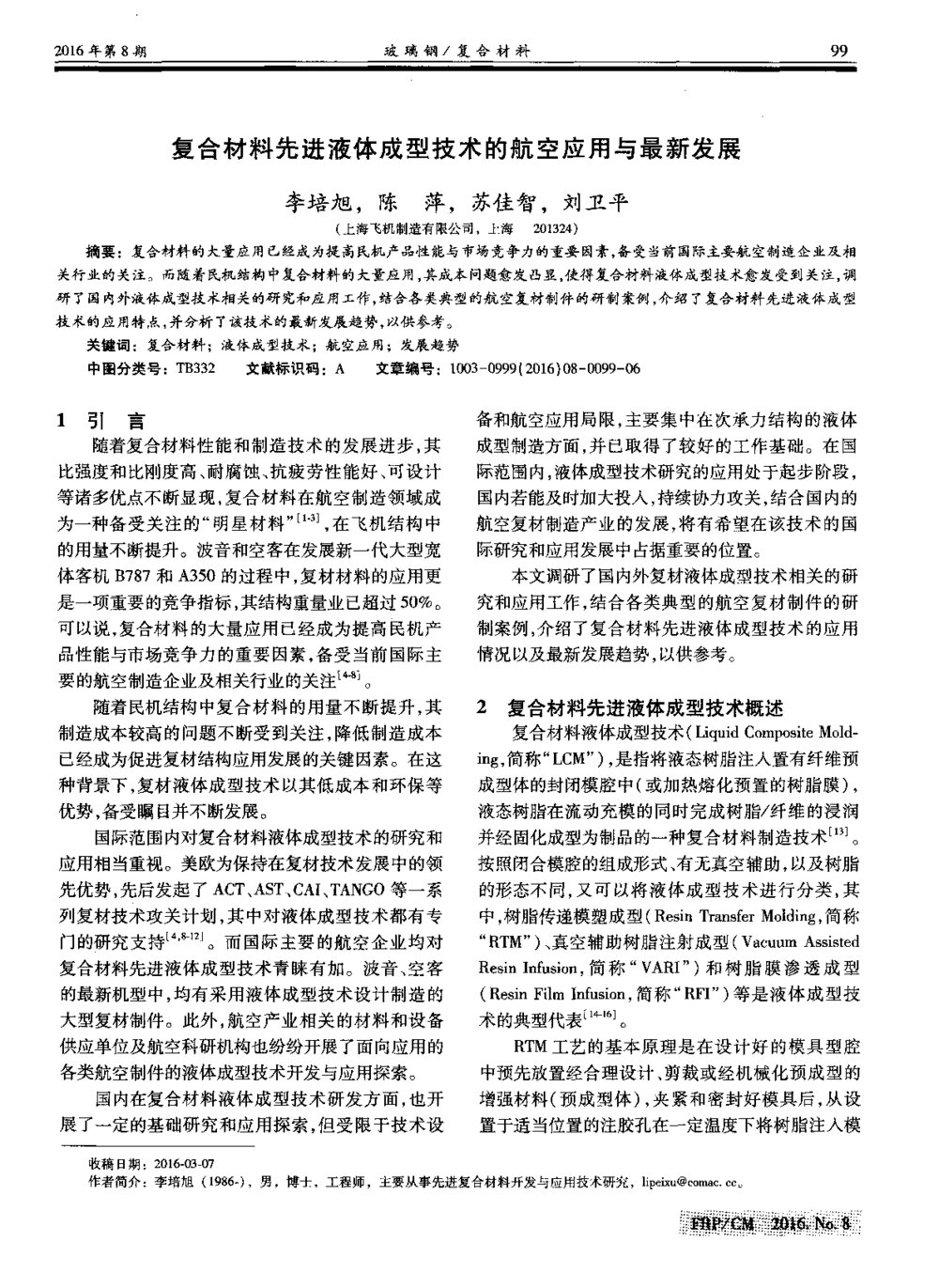
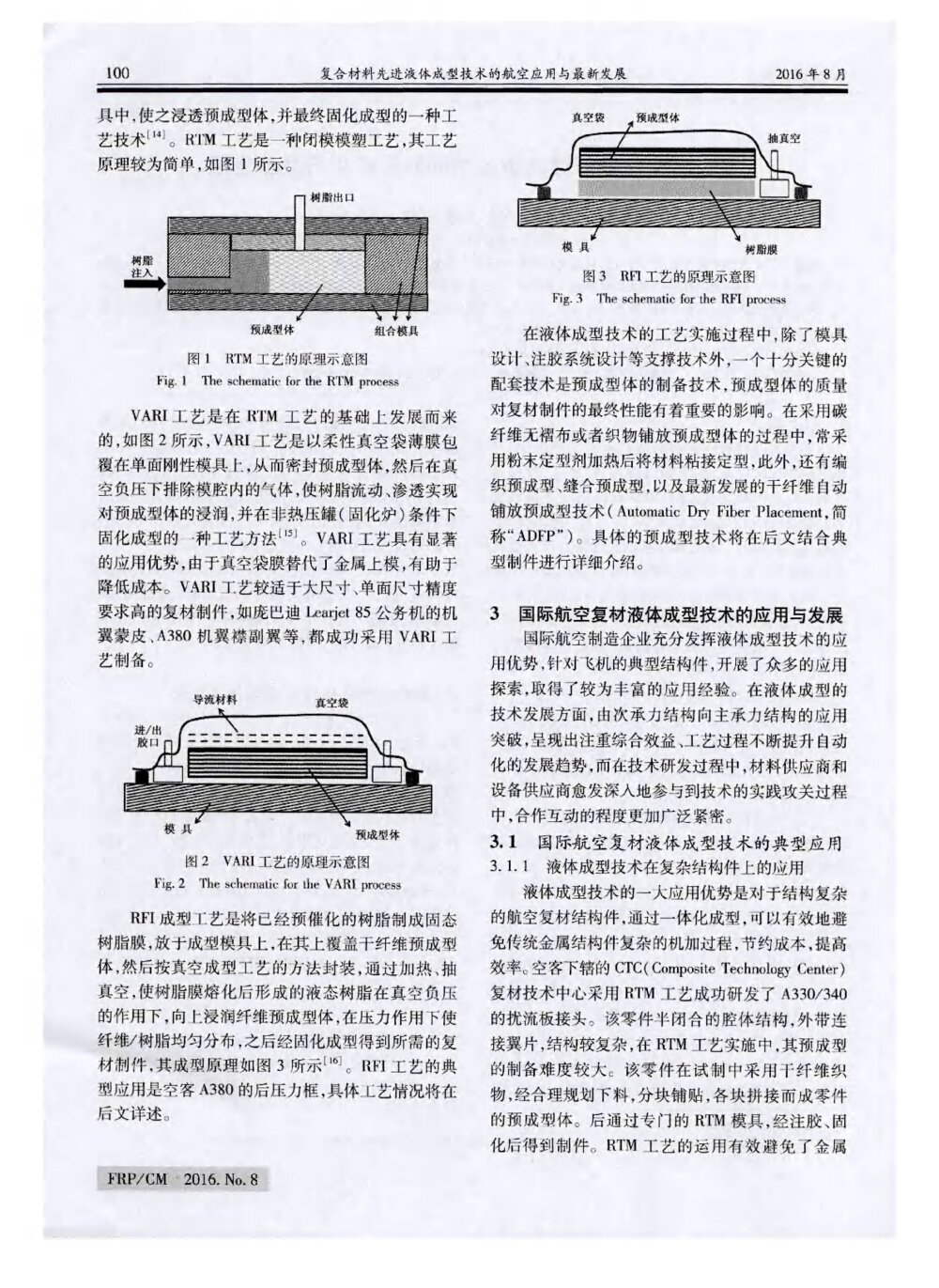
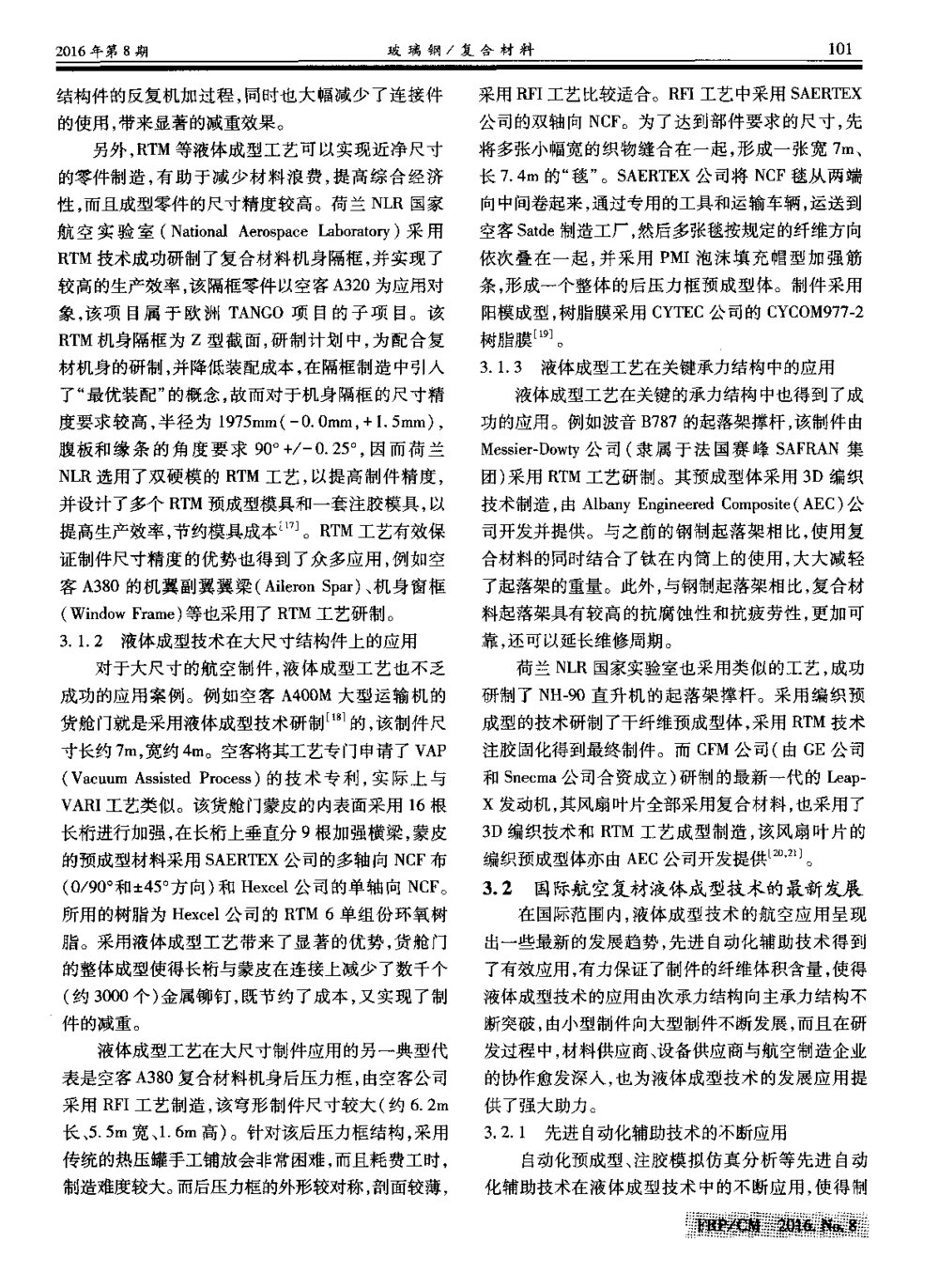
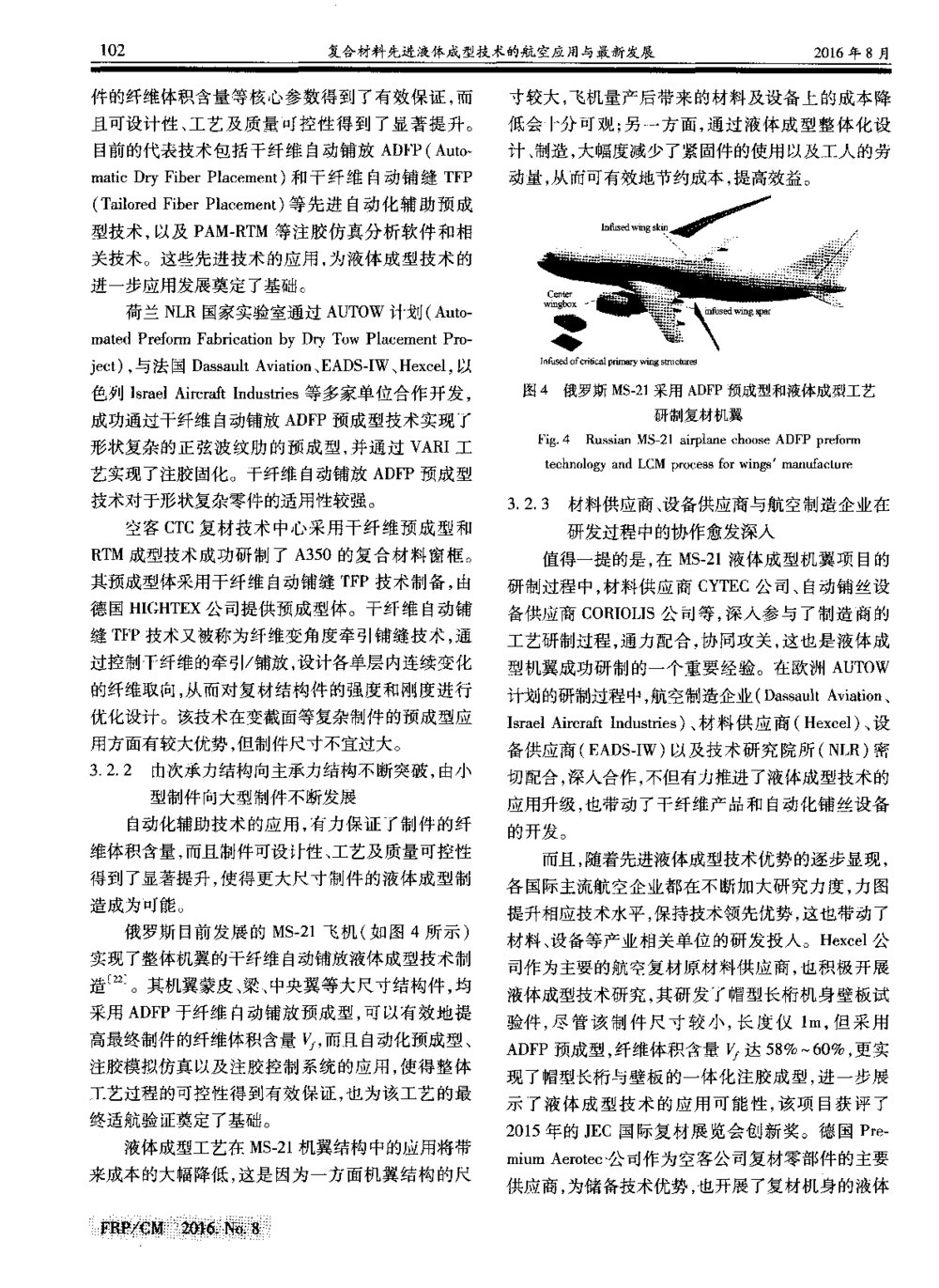
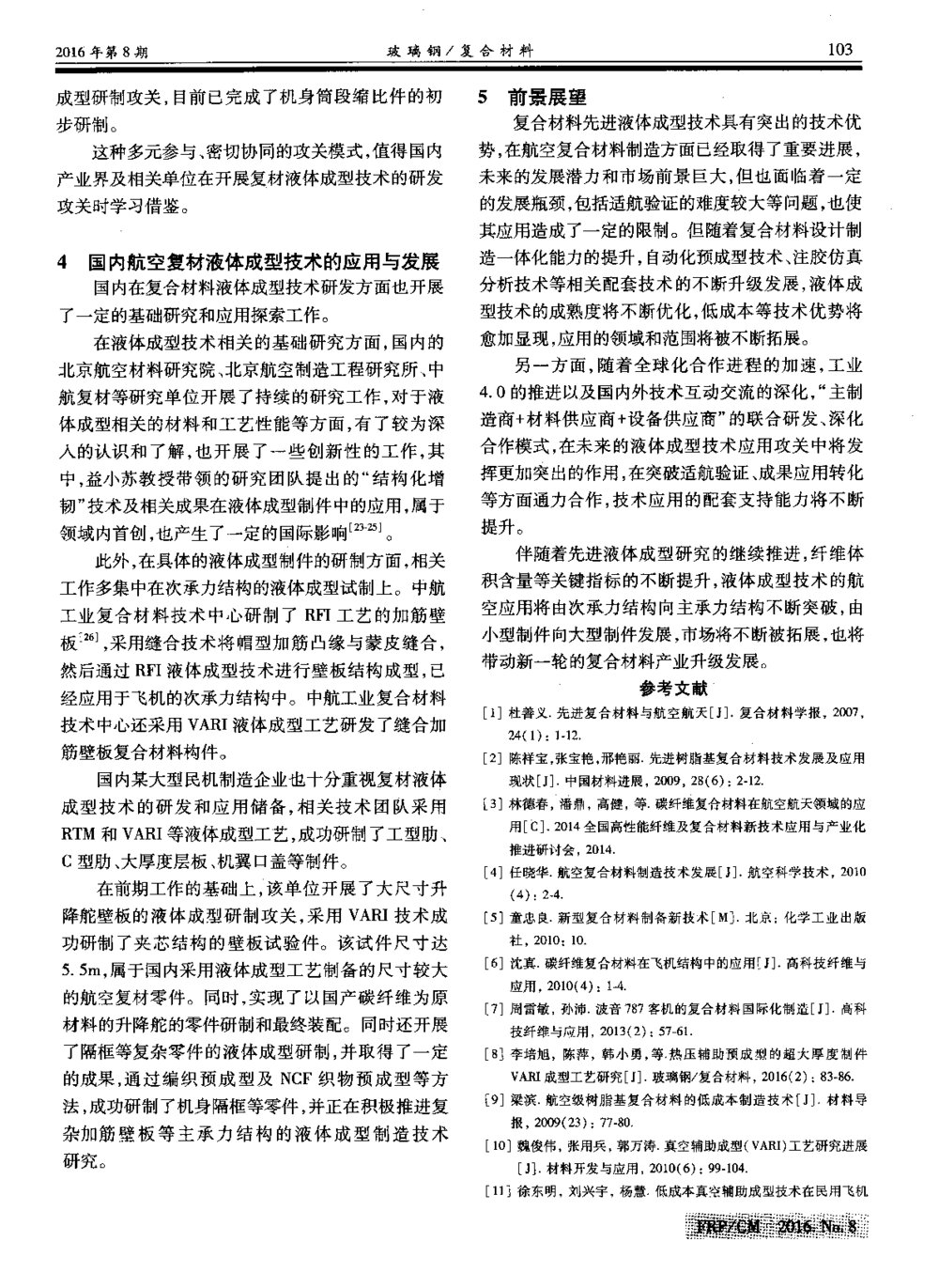
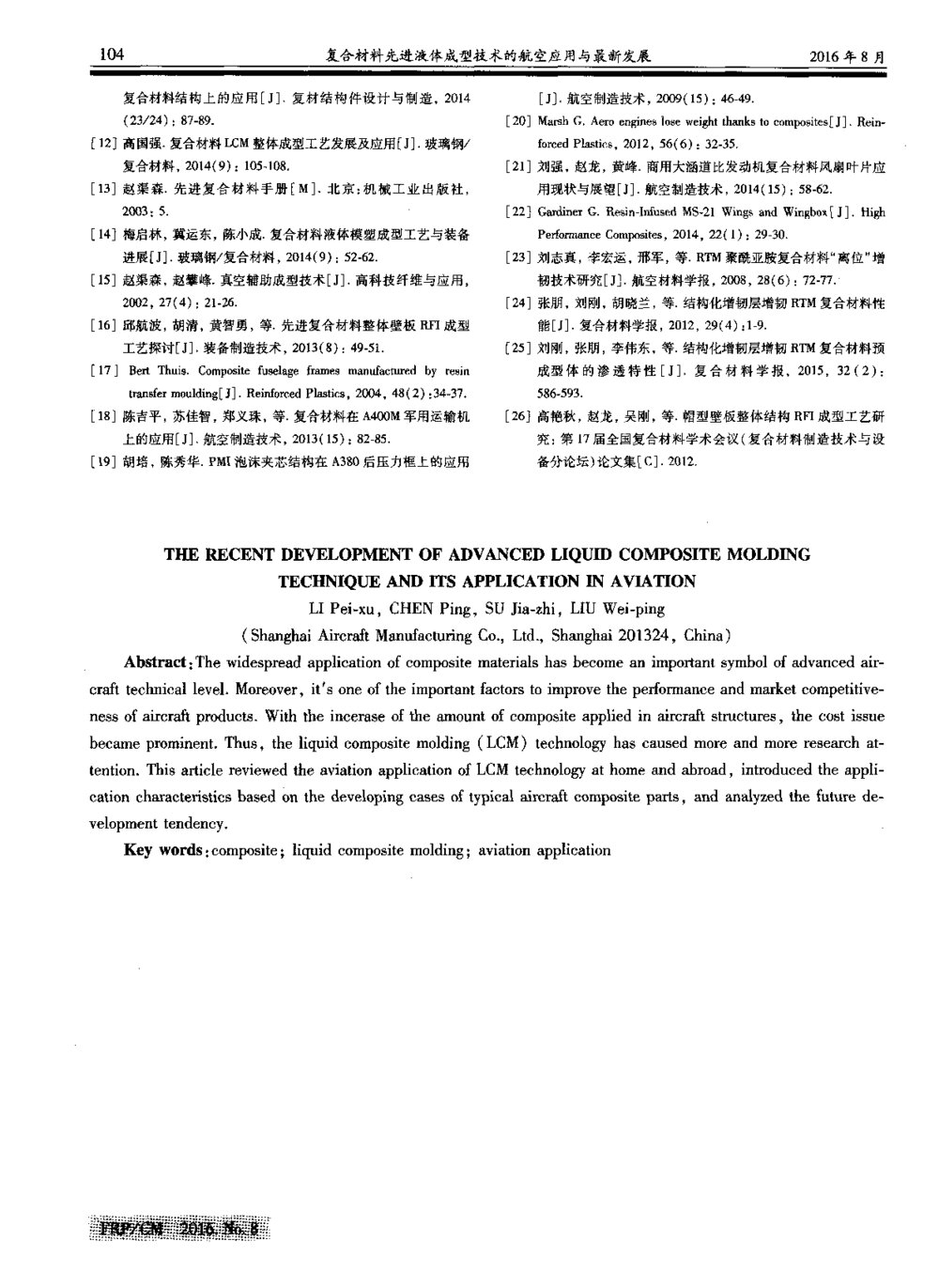
已阅读完毕,您还可以下载文档进行保存
- 1、本文档共6页,内容下载后可编辑。
- 2、本文档内容版权归属内容提供方,所产生的收益全部归内容提供方所有。如果您对本文有版权争议,可选择认领。
- 3、本文档由用户上传,本站不保证质量和数量令人满意,可能有诸多瑕疵,付费之前,请仔细先通过免费阅读内容等途径辨别内容交易风险。如存在严重挂羊头卖狗肉之情形,可联系本站下载客服投诉处理。
2016年第8期玻璃钢/复合材料复合材料先进液体成型技术的航空应用与最新发展李培旭,陈萍,苏佳智,刘卫平(上海飞机制造有限公司,上海201324)摘要:复合材料的大量应用已经成为提高民机产品性能与市场竞争力的重要因素,备受当前国际主要航空制造企业及相关行业的关注。而随着民机结构中复合材料的大量应用,其成本问题愈发凸显,使得复合材料液体成型技术愈发受到关注,调研了国内外液体成型技术相关的研究和应用工作,结合各类典型的航空复材制件的研制案例,介绍了复合材料先进液体成型技术的应用特点,并分析了该技术的最新发展趋势,以供参考。关键词:复合材料;液体成型技术;航空应用;发展趋势—中图分类号:TB332文献标识码:A文章编号:10030999(2016)08-0099-061引言随着复合材料性能和制造技术的发展进步,其比强度和比刚度高、耐腐蚀、抗疲劳性能好、可设计等诸多优点不断显现,复合材料在航空制造领域成“”为一种备受关注的明星材料_l。J,在飞机结构中的用量不断提升。波音和空客在发展新一代大型宽体客机B787和A350的过程中,复材材料的应用更是一项重要的竞争指标,其结构重量业已超过50%。可以说,复合材料的大量应用已经成为提高民机产品性能与市场竞争力的重要因素,备受当前国际主要的航空制造企业及相关行业的关注j。随着民机结构中复合材料的用量不断提升,其制造成本较高的问题不断受到关注,降低制造成本已经成为促进复材结构应用发展的关键因素。在这种背景下,复材液体成型技术以其低成本和环保等优势,备受瞩目并不断发展。国际范围内对复合材料液体成型技术的研究和应用相当重视。美欧为保持在复材技术发展中的领先优势,先后发起了ACT、AST、CAI、TANGO等一系列复材技术攻关计划,其中对液体成型技术都有专门的研究支持,J。而国际主要的航空企业均对复合材料先进液体成型技术青睐有ano波音、空客的最新机型中,均有采用液体成型技术设计制造的大型复材制件。此外,航空产业相关的材料和设备供应单位及航空科研机构也纷纷开展了面向应用的各类航空制件的液体成型技术开发与应用探索。国内在复合材料液体成型技术研发方面,也开展了一定的基础研究和应用探索,但受限于技术设备和航空应用局限,主要集中在次承力结构的液体成型制造方面,并已取得了较好的工作基础。在国际范围内,液体成型技术研究的应用处于起步阶段,国内若能及时加大投入,持续协力攻关,结合国内的航空复材制造产业的发展,将有希望在该技术的国际研究和应用发展中占据重要的位置。本文调研了国内外复材液体成型技术相关的研究和应用工作,结合各类典型的航空复材制件的研制案例,介绍了复合材料先进液体成型技术的应用情况以及最新发展趋势,以供参考。2复合材料先进液体成型技术概述复合材料液体成型技术(LiquidCompositeMold.“”ing,简称LCM),是指将液态树脂注入置有纤维预成型体的封闭模腔中(或加热熔化预置的树脂膜),液态树脂在流动充模的同时完成树脂/纤维的浸润并经固化成型为制品的一种复合材料制造技术引。按照闭合模腔的组成形式、有无真空辅助,以及树脂的形态不同,又可以将液体成型技术进行分类,其中,树脂传递模塑成型(ResinTransferMolding,简称“”RTM)、真空辅助树脂注射成型(VacuumAssisted“”ResinInfusion,简称VARI)和树脂膜渗透成型“”(ResinFilmInfusion,简称RFI)等是液体成型技术的典型代表¨。RTM工艺的基本原理是在设计好的模具型腔中预先放置经合理设计、剪裁或经机械化预成型的增强材料(预成型体),夹紧和密封好模具后,从设置于适当位置的注胶孔在一定温度下将树脂注入模——收稿日期:20160307作者简介:李培旭(1986一),男,博士,工程师,主要从事先进复合材料开发与应用技术研究,lipeixu@comac.cc。0|82016年第8期玻璃钢/复合材料101结构件的反复机加过程,同时也大幅减少了连接件的使用,带来显著的减重效果。另外,RTM等液体成型工艺可以实现近净尺寸的零件制造,有助于减少材料浪费,提高综合经济性,而且成型零件的尺寸精度较高。荷兰NLR国家航空实验室(NationalAerospaceLaboratory)采用RTM技术成功研制了复合材料机身隔框,并实现了较高的生产效率,该隔框零件以空客A320为应用对象,该项目属于欧洲TANGO项目的子项目。该RTM机身隔框为z型截面,研制计划中,为配合复材机身的研制,并降低装配成本,在隔框制造中引入“”了最优装配的概念,故而对于机身隔框的尺寸精度要求较高,半径为1975mm(一0.0mm,+1.5mm),腹板和缘条的角度要求90。+/一0.25。,因而荷兰NLR选用了双硬模的RTM工艺,以提高制件精度,并设计了多个RTM预成型模具和一套注胶模具,以提高生产效率,节约模具成本17]。RTM工艺有效保证制件尺寸精度的优势也得到了众多应用,例如空客A380的机翼副翼翼梁(AileronSpar)、机身窗框(WindowFrame)等也采用了RTM工艺研制。3.1.2液体成型技术在大尺寸结构件上的应用对于大尺寸的航空制件,液体成型工艺也不乏成功的应用案例。例如空客A400M大型运输机的货舱门就是采用液体成型技术研制¨副的,该制件尺寸长约7m,宽约4m。空客将其工艺专门申请了VAP(VacuumAssistedProcess)的技术专利,实际上与VARI工艺类似。该货舱门蒙皮的内表面采用16根长桁进行加强,在长桁上垂直分9根加强横梁,蒙皮的预成型材料采用SAERTEX公司的多轴向NCF布(0/90。和 ̄45。方向)和Hexcel公司的单轴向NCF。所用的树脂为Hexcel公司的RTM6单组份环氧树脂。采用液体成型工艺带来了显著的优势,货舱门的整体成型使得长桁与蒙皮在连接上减少了数千个(约3000个)金属铆钉,既节约了成本,又实现了制件的减重。液体成型工艺在大尺寸制件应用的另一典型代表是空客A380复合材料机身后压力框,由空客公司采用RFI工艺制造,该穹形制件尺寸较大(约6.2m长、5.5m宽、1.6m高)。针对该后压力框结构,采用传统的热压罐手工铺放会非常困难,而且耗费工时,制造难度较大。而后压力框的外形较对称,剖面较薄,采用RFI工艺比较适合。RFI工艺中采用SAERTEX公司的双轴向NCF。为了达到部件要求的尺寸,先将多张小幅宽的织物缝合在一起,形成一张宽7m、“”长7.4m的毯。SAERTEX公司将NCF毯从两端向中间卷起来,通过专用的工具和运输车辆,运送到空客Satde制造工厂,然后多张毯按规定的纤维方向依次叠在一起,并采用PMI泡沫填充帽型加强筋条,形成一个整体的后压力框预成型体。制件采用阳模成型,树脂膜采用CYTEC公司的CYCOM977.2树脂膜。3.1.3液体成型工艺在关键承力结构中的应用液体成型工艺在关键的承力结构中也得到了成功的应用。例如波音B787的起落架撑杆,该制件由—MessierDowry公司(隶属于法国赛峰SAFRAN集团)采用RTM工艺研制。其预成型体采用3D编织技术制造,由AlbanyEngineeredComposite(AEC)公司开发并提供。与之前的钢制起落架相比,使用复合材料的同时结合了钛在内筒上的使用,大大减轻了起落架的重量。此外,与钢制起落架相比,复合材料起落架具有较高的抗腐蚀性和抗疲劳性,更加可靠,还可以延长维修周期。荷兰NLR国家实验室也采用类似的工艺,成功研制了NH.90直升机的起落架撑杆。采用编织预成型的技术研制了干纤维预成型体,采用RTM技术注胶固化得到最终制件。而CFM公司(由GE公司—和Snecma公司合资成立)研制的最新一代的Leapx发动机,其风扇叶片全部采用复合材料,也采用了3D编织技术和RTM工艺成型制造,该风扇叶片的编织预成型体亦由AEC公司开发提供_20工。3.2国际航空复材液体成型技术的最新发展在国际范围内,液体成型技术的航空应用呈现出一些最新的发展趋势,先进自动化辅助技术得到了有效应用,有力保证了制件的纤维体积含量,使得液体成型技术的应用由次承力结构向主承力结构不断突破,由小型制件向大型制件不断发展,而且在研发过程中,材料供应商、设备供应商与航空制造企业的协作愈发深入,也为液体成型技术的发展应用提供了强大助力。3.2.1先进自动化辅助技术的不断应用自动化预成型、注胶模拟仿真分析等先进自动化辅助技术在液体成型技术中的不断应用,使得制濑嘶l02复合材料先进液体成型技术的航空应用与最新发展2016年8月件的纤维体积含量等核心参数得到了有效保证,而且可设计性、工艺及质量可控性得到了显著提升。目前的代表技术包括干纤维自动铺放ADFP(Auto.maticDryFiberPlacement)和干纤维自动铺缝rrFP(TailoredFiberPlacement)等先进自动化辅助预成型技术,以及PAM.RTM等注胶仿真分析软件和相关技术。这些先进技术的应用,为液体成型技术的进一步应用发展奠定了基础。—荷兰NLR国家实验室通过AUTOW计划(Auto—matedPreformFabricationbyDryTowPlacementProject),与法国DassauhAviation、EADS-IW、Hexcel,以色列IsraelAircraftIndustries等多家单位合作开发,成功通过干纤维自动铺放ADFP预成型技术实现了形状复杂的正弦波纹肋的预成型,并通过VARI工艺实现了注胶固化。干纤维自动铺放ADFP预成型技术对于形状复杂零件的适用性较强。空客CTC复材技术中心采用干纤维预成型和RTM成型技术成功研制了A350的复合材料窗框。其预成型体采用于纤维自动铺缝TFP技术制备,由德国HIGHTEX公司提供预成型体。干纤维自动铺缝TFP技术又被称为纤维变角度牵引铺缝技术,通过控制干纤维的牵引/铺放,设计各单层内连续变化的纤维取向,从而对复材结构件的强度和刚度进行优化设计。该技术在变截面等复杂制件的预成型应用方面有较大优势,但制件尺寸不宜过大。3.2.2由次承力结构向主承力结构不断突破,由小型制件向大型制件不断发展自动化辅助技术的应用,有力保证了制件的纤维体积含量,而且制件可设计性、工艺及质量可控性得到了显著提升,使得更大尺寸制件的液体成型制造成为可能。俄罗斯目前发展的MS一21飞机(如图4所示)实现了整体机翼的干纤维自动铺放液体成型技术制造引。其机翼蒙皮、梁、中央翼等大尺寸结构件,均采用ADFP干纤维自动铺放预成型,可以有效地提高最终制件的纤维体积含量,而且自动化预成型、注胶模拟仿真以及注胶控制系统的应用,使得整体工艺过程的可控性得到有效保证,也为该工艺的最终适航验证奠定了基础。液体成型工艺在MS一21机翼结构中的应用将带来成本的大幅降低,这是因为一方面机翼结构的尺FRP/CM:No.8寸较大,飞机量产后带来的材料及设备上的成本降低会十分可观;另一方面,通过液体成型整体化设计、制造,大幅度减少了紧固件的使用以及工人的劳动量,从而可有效地节约成本,提高效益。Infusedofcriticalprunmywingstructur ̄ ̄图4俄罗斯MS.21采用ADFP预成型和液体成型工艺研制复材机翼Fig.4RussianMS一21airplanechooseADFPpreformtechnologyandLCMprocessforwingsmanufacture3.2.3材料供应商、设备供应商与航空制造企业在研发过程中的协作愈发深入值得一提的是,在MS一21液体成型机翼项目的研制过程中,材料供应商CYTEC公司、自动铺丝设备供应商CORIOLIS公司等,深入参与了制造商的工艺研制过程,通力配合,协同攻关,这也是液体成型机翼成功研制的一个重要经验。在欧洲AUTOW计划的研制过程中,航空制造企业(DassauhAviation、IsraelAircraftIndustries)、材料供应商(Hexce1)、设备供应商(EADS.IW)以及技术研究院所(NLR)密切配合,深入合作,不但有力推进了液体成型技术的应用升级,也带动了干纤维产品和自动化铺丝设备的开发。而且,随着先进液体成型技术优势的逐步显现,各国际主流航空企业都在不断加大研究力度,力图提升相应技术水平,保持技术领先优势,这也带动了材料、设备等产业相关单位的研发投入。Hexcel公司作为主要的航空复材原材料供应商,也积极开展液体成型技术研究,其研发了帽型长桁机身壁板试验件,尽管该制件尺寸较小,长度仅lm,但采用ADFP预成型,纤维体积含量达58%一60%,更实现了帽型长桁与壁板的一体化注胶成型,进一步展示了液体成型技术的应用可能性,该项目获评了—2015年的JEC国际复材展览会创新奖。德国PremiumAerotec公司作为空客公司复材零部件的主要供应商,为储备技术优势,也开展了复材机身的液体2016年第8期玻璃钢/复合材料103成型研制攻关,目前已完成了机身筒段缩比件的初步研制。这种多元参与、密切协同的攻关模式,值得国内产业界及相关单位在开展复材液体成型技术的研发攻关时学习借鉴。4国内航空复材液体成型技术的应用与发展国内在复合材料液体成型技术研发方面也开展了一定的基础研究和应用探索工作。在液体成型技术相关的基础研究方面,国内的北京航空材料研究院、北京航空制造工程研究所、中航复材等研究单位开展了持续的研究工作,对于液体成型相关的材料和工艺性能等方面,有了较为深入的认识和了解,也开展了一些创新性的工作,其“中,益小苏教授带领的研究团队提出的结构化增”韧技术及相关成果在液体成型制件中的应用,属于领域内首创,也产生了一定的国际影响。此外,在具体的液体成型制件的研制方面,相关工作多集中在次承力结构的液体成型试制上。中航工业复合材料技术中心研制了RFI工艺的加筋壁板J,采用缝合技术将帽型加筋凸缘与蒙皮缝合,然后通过RFI液体成型技术进行壁板结构成型,已经应用于飞机的次承力结构中。中航工业复合材料技术中心还采用VARI液体成型工艺研发了缝合加筋壁板复合材料构件。国内某大型民机制造企业也十分重视复材液体成型技术的研发和应用储备,相关技术团队采用RTM和VARI等液体成型工艺,成功研制了工型肋、C型肋、大厚度层板、机翼口盖等制件。在前期工作的基础上,该单位开展了大尺寸升降舵壁板的液体成型研制攻关,采用VARI技术成功研制了夹芯结构的壁板试验件。该试件尺寸达5.5m,属于国内采用液体成型工艺制备的尺寸较大的航空复材零件。同时,实现了以国产碳纤维为原材料的升降舵的零件研制和最终装配。同时还开展了隔框等复杂零件的液体成型研制,并取得了一定的成果,通过编织预成型及NCF织物预成型等方法,成功研制了机身隔框等零件,并正在积极推进复杂加筋壁板等主承力结构的液体成型制造技术研究。5前景展望复合材料先进液体成型技术具有突出的技术优势,在航空复合材料制造方面已经取得了重要进展,未来的发展潜力和市场前景巨大,但也面临着一定的发展瓶颈,包括适航验证的难度较大等问题,也使其应用造成了一定的限制。但随着复合材料设计制造一体化能力的提升,自动化预成型技术、注胶仿真分析技术等相关配套技术的不断升级发展,液体成型技术的成熟度将不断优化,低成本等技术优势将愈加显现,应用的领域和范围将被不断拓展。另一方面,随着全球化合作进程的加速,工业“4.0的推进以及国内外技术互动交流的深化,主制”造商+材料供应商+设备供应商的联合研发、深化合作模式,在未来的液体成型技术应用攻关中将发挥更加突出的作用,在突破适航验证、成果应用转化等方面通力合作,技术应用的配套支持能力将不断提升。伴随着先进液体成型研究的继续推进,纤维体积含量等关键指标的不断提升,液体成型技术的航空应用将由次承力结构向主承力结构不断突破,由小型制件向大型制件发展,市场将不断被拓展,也将带动新一轮的复合材料产业升级发展。参考文献[1]杜善义.先进复合材料与航空航天[J].复合材料学报,2007,24(1):1-12.[2]陈祥宝,张宝艳,邢艳丽.先进树脂基复合材料技术发展及应用现状[J].中国材料进展,2009,28(6):2-12.[3]林德春,潘鼎,高健,等.碳纤维复合材料在航空航天领域的应用[c].2o14全国高性能纤维及复合材料新技术应用与产业化推进研讨会,2o14.[4]任晓华.航空复合材料制造技术发展[J].航空科学技术,2OlO(4):2-4.[5]童忠良.新型复合材料制备新技术[M].北京:化学工业出版社,2010:10.[6]沈真.碳纤维复合材料在飞机结构中的应用[J].高科技纤维与应用,2010(4):1-4.[7]周雷敏,孙沛.波音787客机的复合材料国际化制造[J].高科—技纤维与应用,2013(2):5761.[8]李培旭,陈萍,韩小勇,等.热压辅助预成型的超大厚度制件VARI成型工艺研究[J].玻璃钢/复合材料,2016(2):83-86.[9]梁滨.航空级树脂基复合材料的低成本制造技术[J].材料导—报,2009(23):778O.[10]魏俊伟,张用兵,郭万涛.真空辅助成型(VARI)工艺研究进展—[J].材料开发与应用,2010(6):99104.『111徐东明,刘兴字。杨慧.低成本真空辅助成型技术在民用飞机104复合材料先进液体成型技术的航空应用与最新发展2016年8月复合材料结构上的应用[J].复材结构件设计与制造,2014—(23/24):8789.[12]高国强.复合材料LCM整体成型工艺发展及应用[J].玻璃钢/—复合材料,2014(9):105108.[13]赵渠森.先进复合材料手册[M].北京:机械工业出版社,2003:5.[14]梅启林,冀运东,陈小成.复合材料液体模塑成型工艺与装备进展[J].玻璃钢/复合材料,2014(9):52-62.[15]赵渠森,赵攀峰.真空辅助成型技术[J].高科技纤维与应用,—2002,27(4):2126.[16]邱航波,胡清,黄智勇,等.先进复合材料整体壁板RFI成型工艺探讨[J].装备制造技术,2013(8):49.51.[17]BertThuis.Compositefuselageframesmanufacturedbyresin—transfermoulding[J].ReinforcedPlastics,2004,48(2):3437.[18]陈吉平,苏佳智,郑义珠,等.复合材料在A400M军用运输机上的应用[J].航空制造技术,2013(15):82_85.[19]胡培,陈秀华.PMI泡沫夹芯结构在A380后压力框上的应用—[J].航空制造技术,2009(15):4649.—[20]MarshG.Aemenginesloseweisatthankstocomposites[J].Rein—forcedPlastics,2012,56(6):3235.[21]刘强,赵龙,黄峰.商用大涵道比发动机复合材料风扇叶片应—用现状与展望[J].航空制造技术,2014(15):5862.[22]GardinerG.Resin-InfusedMS一21WingsandWingbOX[J].Hi—PerformanceComposites,2014,22(1):2930.“”[23]刘志真,李宏运,邢军,等.RTM聚酰亚胺复合材料离位增韧技术研究[J].航空材料学报,2008,28(6):72-77.[24]张朋,刘刚,胡晓兰,等.结构化增韧层增韧RTM复合材料性能[J].复合材料学报,2012,29(4):1-9.[25]刘刚,张朋,李伟东,等.结构化增韧层增韧RTM复合材料预成型体的渗透特性[J].复合材料学报,2015,32(2):586.593.[26]高艳秋,赵龙,吴刚,等.帽型壁板整体结构RFI成型工艺研究:第17届全国复合材料学术会议(复合材料制造技术与设备分论坛)论文集[C].2012.TIlERECENTDEVELOPMENTOFADVANCEDLIQUIDCOMPOSITEMOLDINGTECHNIQUEANDITSAPPLICATIONINAVIATION———LIPeiXU,CHENPing,SUJiazhi,LIUWeiping(ShanghaiAircraftManufacturingCo.,Ltd.,Shanghai201324,China)Abstract:Thewidespreadapplicationofcompositemater—ialshasbecomeanimportantsymbolofadvancedair—crafttechnicalleve1.Moreover,itSoneoftheimportantfactorstoimprovetheperformanceandmarketcompetitivenessofaircraftproducts.Withtheinceraseoftheamountofcompositeappliedinaircraftstructures,thecostissuebecameprominent.Thus,theliquidcompositemolding(LCM)technologyhascausedmoreandmoreresearchat-—tention.ThisarticlereviewedtheaviationapplicationofLCMtechnologyathomeandabroad,introducedtheapplicationcharacteristicsbasedonthedevelopingcasesoftypicalaircraftcompositeparts,andana—lyzedthefuturedevelopmenttendency.Keywords:composite;liquidcompositemolding;aviationapplication
您可能关注的文档
- “离位”增韧复合材料准静态压入损伤特性研究.pdf
- “神舟七号”飞船舱外航天服防护头盔组件的研制.pdf
- “十二五”复合材料发展重点和方向解读.pdf
- “珠串”堆叠超结构的介孔铁酸锌的制备与表征.pdf
- (001)应变对正交相Ca2 P0.25 Si0.75能带结构及光学性质的影响.pdf
- 0.8设计系数用X80管线钢在近中性pH溶液中的应力腐蚀开裂行为.pdf
- 0.20mm CGO硅钢高温退火Goss晶粒起源及异常长大行为研究.pdf
- 0Cr16Ni5Mo低碳马氏体不锈钢的热变形行为及其热加工图.pdf
- 0Cr17Ni4Cu4Nb钢制螺钉断裂原因分析.pdf
- 1.5MW风机叶片模具加热工艺研究与技术创新.pdf
- 1.5MW风机叶片VARI工艺模拟分析及验证.pdf
- 2.5维机织复合材料低速冲击性能研究.pdf
- 2.25Cr-1Mo钢后续热处理中的磷偏聚行为.pdf
- 2A50锻铝三点弯曲试验与高分辨率CT成像分析.pdf
- 2A12与2A11铝合金超声波焊接工艺与组织研究.pdf
- 2MW风机复合材料叶片材料及工艺研究.pdf
- 3Cr2W8V模具钢激光表面相变硬化层性能的研究.pdf
- 3D打印技术及先进应用研究进展.pdf
- 3D打印技术研究现状和关键技术.pdf
- 5%鱼藤酮悬浮剂的研制.pdf

- 周大爷
- 该用户很懒,什么也没介绍
相关文档
- “离位”增韧复合材料准静态压入损伤特性研究.pdf2021-11-235页
- “神舟七号”飞船舱外航天服防护头盔组件的研制.pdf2021-11-233页
- “十二五”复合材料发展重点和方向解读.pdf2021-11-232页
- “珠串”堆叠超结构的介孔铁酸锌的制备与表征.pdf2021-11-235页
- (001)应变对正交相Ca2 P0.25 Si0.75能带结构及光学性质的影响.pdf2021-11-236页
- 0.8设计系数用X80管线钢在近中性pH溶液中的应力腐蚀开裂行为.pdf2021-11-237页
- 0.20mm CGO硅钢高温退火Goss晶粒起源及异常长大行为研究.pdf2021-11-237页